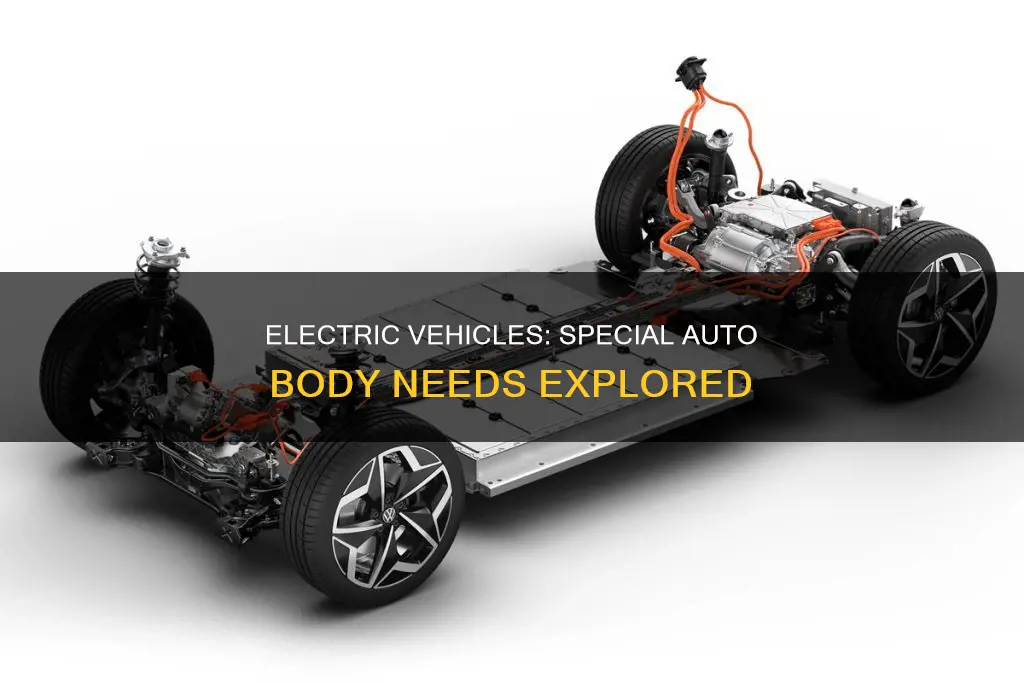
Electric vehicles (EVs) have gained significant popularity in recent years, and as the market for EVs continues to grow, so does the demand for specialized auto body shops that can cater to their unique needs. While traditional internal combustion engine (ICE) vehicles and EVs share many common components, there are distinct differences in their construction and maintenance requirements. This paragraph aims to explore whether electric vehicles necessitate specialized auto body shops and delve into the specific considerations and benefits of such specialized services.
Characteristics | Values |
---|---|
Specialized Body Panels | Electric vehicles often require custom-designed body panels to accommodate the unique placement of batteries and other components. These panels may be made from lightweight materials to reduce overall weight. |
Battery Integration | The placement and integration of batteries within the vehicle's body structure are critical. This may involve specialized mounting systems and cooling solutions to ensure optimal performance and safety. |
Weight Distribution | Due to the heavy batteries, electric vehicles might need a more robust and carefully designed body structure to maintain proper weight distribution and handling. |
Aerodynamics | Special attention is paid to aerodynamics, as efficient airflow can improve range. This can be achieved through unique body shapes and designs. |
Safety Considerations | The body structure of electric vehicles needs to meet strict safety regulations, especially regarding battery protection and pedestrian safety. |
Maintenance Access | Easy access to batteries and other components for maintenance and repairs may require specific body panels and designs. |
Charging Port Placement | The location of charging ports may influence the body design, ensuring convenient access during charging. |
Regulations and Standards | Compliance with various automotive regulations and standards specific to electric vehicles is essential. |
What You'll Learn
- Battery Placement: Special considerations for battery placement and cooling systems
- Frame Reinforcement: Reinforced frames to handle electric vehicle's weight and torque
- Collision Safety: Advanced materials and design for enhanced crash protection
- Charging Port Protection: Specialized body panels to safeguard charging ports
- Aerodynamics: Body shapes optimized for reduced drag and improved efficiency
Battery Placement: Special considerations for battery placement and cooling systems
Battery placement and cooling systems are critical components of electric vehicle (EV) design, requiring careful consideration to ensure optimal performance, safety, and longevity. The placement of batteries is a complex task, as it involves balancing various factors to maximize efficiency and minimize potential risks.
One key consideration is the location of the battery pack within the vehicle's structure. In traditional internal combustion engine (ICE) vehicles, the engine is typically mounted in the front or rear, with the transmission and other components positioned accordingly. In EVs, the battery pack often takes the place of the engine compartment, requiring a rethinking of the vehicle's architecture. Designers must ensure that the battery pack is securely mounted, providing structural integrity to the vehicle while also allowing for easy access during maintenance and repairs. The placement should also consider the center of gravity, as a well-balanced battery pack contributes to improved handling and stability.
The cooling system is another critical aspect of battery placement. Electric vehicle batteries generate heat during operation, and efficient cooling is essential to maintain optimal performance and prevent overheating. There are several cooling methods employed in EV designs. One common approach is liquid cooling, where a coolant circulates through the battery pack, absorbing heat and transferring it to a radiator or cooling system. This method is often used in larger battery packs and can be integrated into the vehicle's overall cooling architecture. Air cooling is another technique, utilizing fans and air ducts to draw cool air over the battery cells, which is particularly effective for smaller, more compact battery modules.
Special attention should be given to the design of the battery pack's cooling channels and passages. These channels should be strategically placed to ensure efficient heat dissipation, allowing for uniform cooling across the entire battery assembly. The cooling system's design must also consider the vehicle's aerodynamics, especially for high-performance EVs, where reducing drag is essential. Proper battery placement and cooling can significantly impact the vehicle's range, performance, and overall efficiency.
Furthermore, the integration of advanced cooling systems, such as thermoelectric cooling or phase-change materials, can provide more precise temperature control. These technologies can be particularly useful in high-performance EVs or in regions with extreme climate conditions. By optimizing battery placement and cooling, engineers can ensure that EV batteries operate within their optimal temperature range, maximizing energy efficiency and extending the lifespan of these critical components.
Electric Vehicles: The Truth About Exhaust Systems
You may want to see also
Frame Reinforcement: Reinforced frames to handle electric vehicle's weight and torque
The concept of frame reinforcement is crucial when considering the unique demands of electric vehicles (EVs) on automotive body and suspension (SHOP) design. EVs, despite their sleek and lightweight appearance, can generate substantial torque and weight, especially when equipped with powerful electric motors and advanced battery systems. This increased power output and the associated weight distribution require careful attention to ensure the vehicle's structural integrity and performance.
Reinforcing the vehicle's frame is a critical aspect of addressing these challenges. The frame serves as the backbone of the vehicle, providing structural support and distributing forces generated by the electric powertrain. In traditional internal combustion engine (ICE) vehicles, the frame's design often focuses on managing the weight of the engine and associated components. However, with EVs, the distribution of weight shifts significantly, with the battery pack often occupying a lower position, impacting the overall center of gravity.
To handle the unique weight and torque characteristics of EVs, frame reinforcement involves several key considerations. Firstly, the use of high-strength materials such as advanced steel alloys or lightweight composites can enhance the frame's structural integrity. These materials offer superior strength-to-weight ratios, enabling the frame to withstand the additional forces without compromising on overall vehicle weight. For instance, employing laser-welded steel joints can create robust connections, ensuring the frame's rigidity and ability to manage torque effectively.
Secondly, the design of the frame itself may require modifications to accommodate the unique layout of EV components. The placement of the battery pack, often positioned low and central, influences the frame's shape and structure. Reinforcement techniques could include adding additional cross-members or reinforcing existing ones to provide lateral stability and manage the increased weight distribution. This ensures that the frame can effectively support the vehicle's weight, especially during acceleration and high-torque operations.
Furthermore, the integration of advanced suspension systems is essential to complement the reinforced frame. The suspension plays a vital role in maintaining ride quality, handling, and overall safety. With EVs, the suspension design must consider the increased weight and torque, often requiring specialized components such as air springs or adjustable damping systems. These adaptations ensure that the vehicle can navigate various road conditions while providing a smooth and controlled ride, all while benefiting from the structural enhancements made to the frame.
Electric Revolution: Unlocking the Future of Sustainable Mobility
You may want to see also
Collision Safety: Advanced materials and design for enhanced crash protection
The evolution of electric vehicles (EVs) has brought about a paradigm shift in the automotive industry, with a focus on sustainability, efficiency, and innovative technologies. As the demand for EVs continues to rise, so does the need for advanced safety features, particularly in the realm of collision protection. The unique characteristics of electric powertrains and lightweight materials used in EVs necessitate specialized design considerations for auto body structures, ensuring optimal safety performance.
One of the key aspects of collision safety in EVs is the utilization of advanced materials. Traditional steel bodies, while robust, may not be the best choice for modern electric vehicles. Lightweight materials such as aluminum alloys, carbon fiber composites, and advanced high-strength steel (AHSS) are now being employed to reduce overall vehicle weight while maintaining structural integrity. These materials offer improved strength-to-weight ratios, allowing for more efficient energy absorption during collisions. For instance, carbon fiber composites provide exceptional strength and stiffness, making them ideal for reinforcing critical areas like the vehicle's front end and passenger compartment.
The design of the auto body plays a crucial role in managing crash forces and protecting occupants. Modern EVs often incorporate innovative design elements to enhance safety. One such feature is the use of energy-absorbing structures, such as crumple zones, which are strategically designed to deform and absorb impact energy during a collision. These zones are carefully engineered to manage the distribution of forces, ensuring that the vehicle's structure deforms in a controlled manner, reducing the risk of damage to critical components and providing better protection for passengers.
Additionally, the integration of advanced safety systems, such as autonomous braking and lane-keeping assist, further emphasizes the importance of collision safety in EVs. These systems rely on precise and robust vehicle structures to function effectively. The design of the auto body must accommodate the placement of sensors, cameras, and other electronic components while maintaining the overall structural integrity. This requires a meticulous approach to ensure that the vehicle's body provides the necessary protection without compromising the performance of these advanced safety features.
In summary, the development of collision safety in electric vehicles requires a careful consideration of materials and design. By utilizing advanced materials and innovative structural designs, EVs can achieve enhanced crash protection while maintaining the lightweight and efficient nature of these vehicles. The unique challenges posed by electric powertrains and the integration of advanced safety systems demand a specialized approach to auto body design, ensuring that EVs meet and exceed traditional safety standards. This focus on collision safety is essential to building consumer trust and fostering the widespread adoption of electric vehicles.
The Future of Driving: Are Electric Vehicles the Answer?
You may want to see also
Charging Port Protection: Specialized body panels to safeguard charging ports
The integration of charging ports in electric vehicles (EVs) has become a standard feature, offering convenience for EV owners. However, this convenience comes with a unique challenge: the need for specialized body panels to protect these ports. The charging port, often located at the front or side of the vehicle, is a vulnerable component that requires careful consideration in the design and construction process.
Specialized body panels are designed to provide an extra layer of defense against potential impacts and damage. These panels are typically made from high-strength materials, such as advanced composites or reinforced plastics, which offer superior impact resistance compared to traditional metal panels. The primary goal is to ensure that the charging port remains secure and functional, even in the event of a collision or accidental impact. By incorporating these specialized panels, manufacturers aim to minimize the risk of damage to the charging port, which could result in costly repairs or, in severe cases, render the port inoperable.
One of the key advantages of these protective panels is their ability to absorb and redistribute the force of an impact. When a vehicle is involved in a minor accident or collision, the specialized panels act as a buffer, reducing the direct force on the charging port. This design consideration is crucial, as it helps prevent structural damage to the port and the associated wiring, ensuring the longevity of the EV's charging system. Moreover, these panels can be designed to be easily replaceable, allowing for cost-effective repairs and minimizing the downtime of the vehicle.
In addition to impact protection, specialized body panels can also address other concerns related to charging port safety. For instance, they can be engineered to provide insulation and protection against environmental factors such as water and dust. This is particularly important for EVs, as charging ports are often exposed to the elements, and proper sealing can prevent potential water ingress or dust accumulation, which could lead to electrical issues or performance degradation.
Manufacturers are increasingly recognizing the importance of charging port protection and are incorporating these specialized body panels as standard features in their EV models. This not only ensures the reliability and longevity of the vehicle but also provides peace of mind to EV owners, knowing that their charging ports are well-guarded against potential hazards. As the popularity of electric vehicles continues to grow, the demand for such innovative solutions will likely drive further advancements in automotive design and safety.
Toyota Prius: Hybrid or Electric? Unveiling the Truth
You may want to see also
Aerodynamics: Body shapes optimized for reduced drag and improved efficiency
The design of an electric vehicle's body plays a crucial role in its overall performance and efficiency, especially when it comes to aerodynamics. Aerodynamic efficiency is a key factor in reducing drag, which directly impacts the vehicle's range and energy consumption. This is particularly important for electric cars, as they rely solely on their batteries for power, and any inefficiency can lead to reduced driving range.
Aerodynamic drag is the force that opposes the motion of an object as it moves through a fluid, in this case, air. For electric vehicles, minimizing drag is essential to optimize energy usage. The body shape of the car significantly influences the amount of drag experienced. A well-designed body can reduce drag by smoothly directing air around the vehicle, ensuring that it flows efficiently over and under the car's surface. This is achieved through careful consideration of the vehicle's frontal area, side profile, and rear shape.
One of the primary design considerations is the frontal area, which is the surface area of the vehicle that faces forward. A smaller frontal area reduces the amount of air that needs to be moved, resulting in lower drag. Designers often use sleek and streamlined front ends, incorporating features like air intakes and grilles that are strategically positioned to manage airflow efficiently. This approach not only improves aerodynamics but also contributes to a visually appealing design.
The side profile of the vehicle is another critical aspect. Designers aim to create a smooth, curved surface that follows the airflow from front to back. This can be achieved through the use of sloping roofs, gently curved doors, and carefully designed wheel arches. By reducing the turbulence around the vehicle, these design elements minimize drag and improve overall efficiency. Additionally, the side mirrors and door handles should be designed to avoid creating additional drag, often by incorporating small, streamlined shapes or by integrating them into the body seamlessly.
The rear of the vehicle is also crucial for aerodynamics. A well-designed rear end can help manage the airflow exiting the vehicle, reducing drag and turbulence. This can be accomplished through the use of spoilers, diffusers, and carefully positioned lights. For instance, a rear spoiler can help create downforce, which increases traction and stability at high speeds, while also reducing drag. The overall goal is to create a body shape that seamlessly integrates all these design elements to optimize airflow, ensuring that the electric vehicle glides through the air with minimal resistance.
Toyota's Electric Future: Rumors of EV Production Halt
You may want to see also
Frequently asked questions
While electric vehicles share many of the same auto body requirements as traditional gasoline-powered cars, there are some unique considerations. EVs often have different structural components, such as battery packs and electric motor mounts, which may require specialized knowledge and equipment for repairs. However, many auto body shops are equipped to handle these repairs, and some shops even specialize in EV-specific services.
One of the main challenges is the high voltage and potential electrical hazards associated with the vehicle's battery system. Technicians must be trained to safely disconnect the battery and handle the electrical connections during the repair process. Additionally, the lightweight materials used in some EVs, like carbon fiber, might require specialized techniques for body repairs and painting.
Start by researching local auto body shops that have experience with electric vehicles. Look for shops that are familiar with the unique aspects of EVs and have access to the necessary tools and equipment. You can also reach out to EV communities or forums for recommendations and reviews. Many EV manufacturers also provide resources and networks of authorized service centers that can assist with body repairs and maintenance.