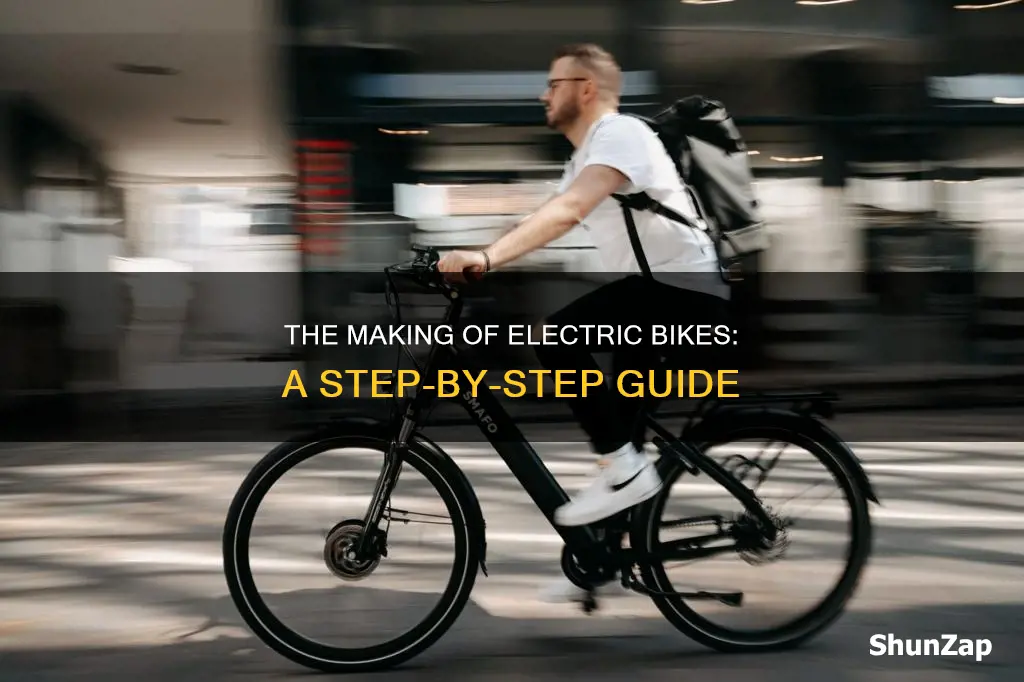
Electric bikes have witnessed a rapid surge in popularity, with an estimated 40 million units expected to be sold worldwide by 2023. The manufacturing process for these bikes involves several key steps, including the selection of frame materials, battery integration, and motor performance. Frames are typically made from lightweight aluminium alloy, with some companies also offering steel, titanium, or carbon fibre frames. The choice of material impacts the bike's performance, weight, longevity, and cost. The next crucial step is battery integration, where manufacturers decide between integrated and removable batteries, considering both performance and design aesthetics. Finally, the motor must provide optimal torque and speed without adding excessive weight or complexity to the frame design. While some companies design their own bikes, many outsource production to countries like China, Taiwan, and the United States, where labour and factory standards vary.
Characteristics | Values |
---|---|
Frame material | Aluminum, carbon fibre, steel, or titanium |
Frame production | Welding, painting, assembling |
Battery integration | Integrated or removable |
Battery models | Lithium-ion, lithium iron phosphate |
Motor | Hub motor, brushless motor |
Manufacturing countries | China, Italy, South Korea, Taiwan, India, Japan, Germany, Switzerland, Sweden, France, Australia, Canada, United Kingdom, Belgium, Denmark, Netherlands, Norway, Spain, Mexico, Austria, Brazil, US |
Top manufacturing countries | China, Taiwan, US, Germany |
Top companies | Giant, Merida, Trek, Riese & Muller, M1 Sporttechnik, Specialized, Cannondale |
What You'll Learn
Frame material selection: aluminium, carbon fibre, steel or titanium
Aluminium, carbon fibre, steel and titanium are the four main options for electric bike frames. Each has its pros and cons, and the right choice depends on the rider's priorities, including weight, budget, longevity, and performance.
Aluminium is relatively cheap and therefore perfect for mass production. It has a good strength-to-weight ratio, resulting in a light and stiff frame. It is a popular option for budget and mid-range electric bikes. However, aluminium frames can't absorb vibrations and are rigid, providing the worst riding quality out of all four materials. They are also prone to corrosion in humid environments and are difficult to repair.
Carbon fibre is a composite of carbon sheets bonded with resin. It is incredibly stiff, light, and adaptable, allowing designers to create unique shapes. It can absorb minor vibrations, contributing to a more comfortable ride. However, carbon fibre is labour-intensive and expensive. It is prone to dings and damage and can have a harsh feel on rough roads.
Steel was the traditional choice for bike frames and is still widely available. It is famed for its smooth ride, making it popular for touring and custom-built bikes. Steel is also relatively easy to repair and offers excellent durability. However, steel is generally heavier than the other three materials and can corrode over time in humid environments.
Titanium is an upgrade from steel, offering a lightweight, strong, corrosion-proof, and exceptionally durable frame. It provides a silky smooth ride quality and is resistant to the elements. However, titanium is more expensive than steel and less flexible than traditional steel.
Electric Bike Benefits: Are They Worth the Hype?
You may want to see also
Frame production: welding, painting, and assembly
Frame production is a crucial aspect of the electric bike manufacturing process. It involves several steps, including welding, painting, and assembly.
Welding is a challenging process, especially for aluminium frames, as it requires specialised techniques and equipment to ensure strong and precise joints. Some manufacturers in China use large factories with robots to weld frames, which can be more cost-effective than manual labour.
Painting is another important step in frame production. It not only enhances the visual appeal of the bike but also provides protection against corrosion. The painting process typically involves applying multiple coats of paint, including a primer, base colour, and potentially additional decorative layers.
Assembly is the final step in frame production, where all the components come together. This includes attaching the wheels, handlebars, seat, and other accessories. The assembly process can vary depending on the specific design and features of the electric bike.
The materials used for the frame significantly impact the overall weight of the electric bike. Aluminium alloy frames are popular due to their lightweight and stiffness, contributing to the range the bike can travel before requiring a recharge. Additionally, the frame design must accommodate the integration of the battery and motor, ensuring a sleek and functional design.
Electric bike frames are manufactured and assembled in various countries, including China, Taiwan, the United States, Germany, and the United Kingdom. The choice of manufacturing location can depend on factors such as cost, labour standards, and quality control.
The Evolution of Electric Derny Bikes: Are They Electric?
You may want to see also
Battery integration: removable or integrated
The decision between removable and integrated batteries is a crucial aspect of the electric bike manufacturing process. It significantly influences the e-bike's performance and visual appeal.
Removable batteries are very common in the market. They are widely accepted because of their many advantages. They are easy to recharge, as the rider can choose to recharge the battery on the e-bike or remove it and take it elsewhere. They are also usually lightweight, agile, and easy to replace. However, they can leave the e-bike at greater risk of damage due to the weather or other environmental factors if the electrical components are exposed when removing the battery.
Integrated batteries, on the other hand, are built directly into the e-bike's frame, often helping them to resemble a traditional non-electric bike. They offer superior protection from adverse elements and a sleeker bike design. Their inherent design provides resistance to environmental factors, and given they can't be easily removed, the theft risks are lower. Integrated batteries also have a reduced risk of damage when it comes to charging since there is always a secure connection. However, they often have a fixed or limited capacity, which affects how far one can travel with power assistance. The e-bike will always need to be parked near a power source for charging, which some owners may find inconvenient.
Ultimately, the choice between integrated and removable batteries depends on individual preferences and lifestyles, as well as how the rider plans to use their bike daily. Integrated batteries are great for those who want minimal fuss and maximum security, while removable batteries offer more flexibility when it comes to charging and range.
Electric Bikes in Ohio: What's the Law?
You may want to see also
Motor selection: hub motors, torque, speed, and weight
Motor selection is a critical aspect of electric bike manufacturing, with hub motors being the most common choice. Hub motors are versatile and can be placed on either the front or rear wheel of the bike, offering similar performance and customer satisfaction. They are also independent of the pedal transmission, so issues with the chain or derailleur will not affect the motor's operation.
When selecting a hub motor, there are two main types to choose from: geared hub motors and direct-drive hub motors. Geared hub motors are smaller and lighter, typically weighing between 2-4 kg, and can provide substantial torque thanks to their internal gearing. They are also quieter and more efficient for pedalling, but the nylon gears may wear out under hard use.
On the other hand, direct-drive hub motors are heavier, typically weighing between 4-9 kg, and have larger diameters, usually over 20 cm. They offer higher torque and are more durable, making them suitable for heavier riders or those carrying cargo. Direct-drive motors are also quieter and simpler, with no internal gearing, but they may make pedalling less efficient due to drag.
The motor's torque and speed are crucial factors in electric bike design. The motor must provide optimal torque and speed across various conditions without adding excessive weight or complicating the frame design. A higher-wattage motor, such as the eZee Kit with 500-1000 watts, will offer more power and torque, making it ideal for steep climbs or hauling cargo.
Additionally, the weight of the electric bike's frame and overall weight are important considerations. Lighter frames, such as those made with aluminium alloy, contribute to a lighter overall weight, allowing the bike to travel further on a single battery charge. However, the spokes on the wheels must be stronger than traditional bicycles to withstand the high torque generated by the hub motor.
Concealing Your Electric Bike: Creative Camouflage Techniques
You may want to see also
Market analysis: demand, pricing, and competition
The global electric bike market is experiencing significant growth, with an estimated size of USD 43.59 billion in 2023, projected to reach USD 148.70 billion by 2032. This growth is attributed to various factors, including the rising demand for eco-friendly transportation, government initiatives promoting green vehicles, and the increasing stringency of emission regulations for gasoline motorcycles.
Regionally, the Asia Pacific market, particularly China, dominates the global electric bike industry. This dominance is driven by comprehensive bicycle infrastructure in countries like South Korea, Taiwan, India, and Japan, as well as high vehicular and public transit congestion. The European market is also expected to show significant growth, with manufacturers actively innovating and developing advanced e-bike technology.
The demand for electric bikes is influenced by several factors. Firstly, the growing popularity of recreational and leisure bicycling, especially in the United States, contributes to the increasing demand for electric bikes. Additionally, the versatility of electric bikes, with various types such as city, commuter, cargo, family, and folding bikes, caters to a wide range of consumer needs. The integration of advanced features, such as front suspension, hydraulic disc brakes, and smart technology, further enhances the appeal of electric bikes.
Pricing of electric bikes varies depending on several factors, including frame material, battery type, and additional features. Frame materials like aluminum and carbon fiber are generally more expensive than traditional steel frames but offer advantages in weight and performance. Removable batteries, for example, offer convenience and influence the overall price of the electric bike. Competition in the electric bike market is intensifying, with companies adopting direct-to-consumer business models, offering flexible financing options, and providing enhanced customer support to cater to diverse consumer needs.
Best Electric Dirt Bikes: Affordable, Eco-Friendly Options
You may want to see also
Frequently asked questions
The first step in the manufacturing process is selecting the frame material. Historically, steel was the predominant material, but today, manufacturers tend to choose between aluminum and carbon fibre, with steel and titanium as alternative options.
The next step is battery integration, which involves deciding between integrated and removable batteries. This decision is tailored to specific design blueprints and anticipated user preferences.
Electric bikes are manufactured all over the world, including in China, Italy, South Korea, Taiwan, India, Japan, Germany, Switzerland, the United States, and many other countries. China is the largest manufacturer of cheaper, mass-produced electric bikes, while Taiwan is the biggest manufacturer of higher-quality frames for well-known brands.