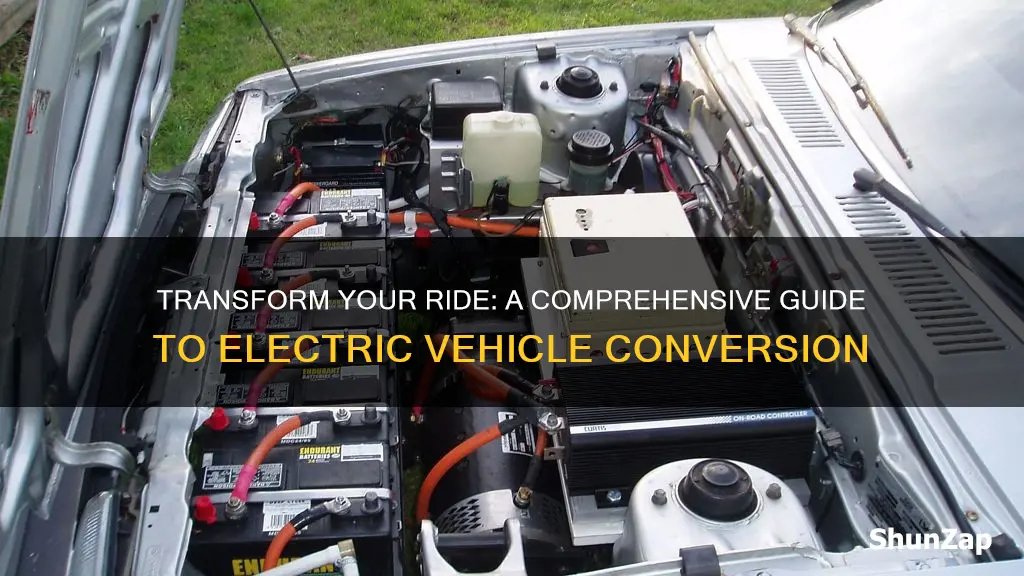
Converting a vehicle to electric power is a complex but rewarding process that can significantly reduce environmental impact and enhance performance. This guide will take you through the step-by-step process of transforming your vehicle into an electric-powered marvel. From selecting the right electric motor and battery to wiring and programming, each phase requires careful planning and execution. We'll explore the essential components, such as the inverter, charger, and controller, and provide practical tips for installation, ensuring your electric vehicle is not only efficient but also safe and reliable. Get ready to embark on a journey towards a greener and more sustainable mode of transportation!
What You'll Learn
- Battery Selection: Choose the right battery for your vehicle's needs and size
- Motor Installation: Mount the electric motor and ensure proper wiring
- Controller Setup: Configure the electronic speed controller for optimal performance
- Charging System: Design and integrate a charging port and system
- Testing and Calibration: Thoroughly test and calibrate the electric vehicle for safe operation
Battery Selection: Choose the right battery for your vehicle's needs and size
When converting a vehicle to electric, one of the most critical components is the battery. The right battery choice is essential to ensure optimal performance, efficiency, and longevity of your electric vehicle (EV). Here's a detailed guide on how to select the appropriate battery for your EV conversion:
Understand Your Vehicle's Requirements: Begin by assessing your vehicle's specific needs. Consider factors such as the desired range, the power output required for acceleration, and the overall weight of the vehicle. Heavier vehicles or those intended for frequent high-speed driving will typically require larger and more powerful batteries. Understanding your vehicle's characteristics will help you determine the battery capacity and voltage needed.
Battery Capacity and Voltage: Battery capacity is measured in ampere-hours (Ah) or kilowatt-hours (kWh). It indicates the amount of energy the battery can store. For EV conversions, you'll need a high-capacity battery to achieve the desired range. Calculate the required battery capacity based on your vehicle's estimated energy consumption and the desired range. Higher voltage batteries are often preferred for EV conversions as they provide more power to the electric motor. Common voltages for EV batteries range from 12V to 400V, with 120V to 240V being a popular choice for many conversions.
Consider Battery Chemistry: Different battery chemistries offer varying advantages and trade-offs. The most common types for EV conversions include Lead-Acid, Nickel-Cadmium (NiCd), Nickel-Metal Hydride (NiMH), and Lithium-Ion (Li-ion) batteries. Lithium-ion batteries are highly favored due to their high energy density, lightweight, and long cycle life. They provide excellent performance and efficiency, making them ideal for electric vehicles. However, Li-ion batteries can be more expensive, so consider your budget and the specific requirements of your project.
Size and Physical Constraints: Evaluate the physical space available in your vehicle for the battery pack. EV batteries come in various sizes and forms, including rectangular, cylindrical, and prismatic cells. Ensure that the chosen battery fits within the designated space, considering factors like mounting options and cooling systems. Proper ventilation and heat management are crucial to maintain battery performance and safety.
Safety and Maintenance: Safety should always be a top priority when selecting a battery. Look for batteries with built-in safety mechanisms, such as overcharge and over-discharge protection, temperature monitoring, and short-circuit prevention. Additionally, consider the maintenance requirements of the battery. Some batteries, like Li-ion, are maintenance-free, while others may require periodic checks and potential cell replacements.
By carefully considering these factors, you can make an informed decision when choosing the right battery for your electric vehicle conversion, ensuring a successful and efficient EV project. Remember, the battery is the heart of your electric vehicle, so selecting the appropriate one is crucial for a smooth and reliable driving experience.
Mastering EV Battery Care: Tips for Optimal Performance and Longevity
You may want to see also
Motor Installation: Mount the electric motor and ensure proper wiring
When it comes to converting a vehicle to electric, one of the most crucial steps is the installation of the electric motor. This process requires careful planning and execution to ensure optimal performance and safety. Here's a detailed guide on how to mount the electric motor and establish the necessary wiring:
Motor Selection and Preparation: Begin by choosing an electric motor suitable for your vehicle's requirements. Consider factors such as power output, size, and weight. Ensure the motor is designed for the specific application and meets the necessary specifications. Once you have the motor, inspect it for any damage or defects. Check the wiring connections and ensure all components are in good working order.
Mounting the Motor: Locate the desired position for the electric motor, typically in the vehicle's engine bay or a designated space for electric powertrains. Ensure the area is spacious enough to accommodate the motor and its cooling system. Mount the motor securely using appropriate brackets and fasteners. It should be firmly attached to the vehicle's frame or chassis to withstand the stresses of driving. Pay attention to the motor's orientation, ensuring it aligns with the vehicle's intended direction of travel.
Wiring and Connections: Proper wiring is essential for the motor's functionality and safety. Start by identifying the motor's power and ground connections. Connect the positive terminal of the battery to the motor's power input, ensuring a secure and tight connection. Use appropriate gauge wiring to handle the expected current draw. Route the wires through the vehicle's frame or designated channels, ensuring they are protected from damage. Connect the motor's control wiring, which may include signals for speed control, braking, and other vehicle systems.
Cooling and Ventilation: Electric motors generate heat, so proper cooling is vital. Install a cooling system such as a radiator or liquid cooling jacket to dissipate excess heat. Ensure the motor's ventilation is unobstructed, allowing for efficient airflow. Check that the cooling system is integrated with the vehicle's overall ventilation design to maintain optimal operating temperatures.
Testing and Final Adjustments: After the motor is mounted and wired, conduct thorough testing. Check all connections for tightness and integrity. Start the motor and verify its operation, ensuring it responds as expected. Adjust the motor's settings, such as speed and torque, to match the vehicle's performance requirements. Fine-tune the wiring connections and control systems to optimize performance and ensure a smooth driving experience.
Unlocking Federal EV Tax Credit: A Step-by-Step Guide
You may want to see also
Controller Setup: Configure the electronic speed controller for optimal performance
The electronic speed controller (ESC) is a critical component in an electric vehicle conversion, as it regulates the flow of power to the motor, controlling speed and torque. Proper setup and configuration of the ESC are essential to ensure optimal performance, efficiency, and safety. Here's a detailed guide on how to configure the ESC for your electric vehicle conversion:
- Understanding the ESC: Begin by familiarizing yourself with the specific ESC you've chosen for your conversion. Different ESCs may have varying settings and features, so it's crucial to consult the manufacturer's documentation or user manual. This resource will provide valuable information about the ESC's capabilities, input/output requirements, and any unique settings or adjustments it offers.
- Calibration and Tuning: Calibration is a critical step to ensure the ESC responds accurately to your input. This process involves adjusting various parameters to match your vehicle's characteristics and your driving preferences. Here's a general overview:
- Speed Sensor Calibration: Most ESCs require calibration with a speed sensor, often a Hall effect sensor or a magnetometer. This sensor provides speed feedback to the ESC. Calibrate it by setting the sensor's position and adjusting the ESC's internal speed sensor offset.
- Current Limit: Set the current limit to a safe value, ensuring it can handle the motor's peak current. This prevents damage to the ESC and motor.
- Brake Sensitivity: Adjust the brake sensitivity to control the motor's response during braking. A higher sensitivity will make the motor act more like a traditional brake, slowing the vehicle down more aggressively.
- Throttle Response: Fine-tune the throttle response to match your driving style. This includes adjusting the throttle deadband (the area where the ESC doesn't respond) and the throttle sensitivity.
- Motor Connection and Configuration: Properly connecting the motor to the ESC is essential. Ensure the motor's phase configuration matches the ESC's input requirements. This is typically done by connecting the motor's terminals to the corresponding terminals on the ESC, following the manufacturer's instructions. Additionally, configure the ESC to match the motor's characteristics, such as its no-load speed, voltage constant, and inertia.
- Testing and Validation: After the initial setup, it's crucial to test the ESC's performance. This can be done on a dyno (dynamic tester) or through test drives. Monitor the ESC's behavior, ensuring it responds correctly to throttle inputs and provides smooth power delivery. Use diagnostic tools to check for any error codes and verify that the ESC is functioning as expected.
- Fine-Tuning and Optimization: Based on your testing results, make any necessary adjustments to fine-tune the ESC's performance. This may involve recalibrating the speed sensor, adjusting current limits, or refining throttle response settings. The goal is to achieve a smooth, responsive, and safe driving experience.
Remember, the ESC's configuration can significantly impact the overall performance and driving experience of your electric vehicle. Take the time to understand the ESC's capabilities and make adjustments carefully to ensure a successful conversion.
The Ultimate Guide to Choosing the Best EV: A Comprehensive Comparison
You may want to see also
Charging System: Design and integrate a charging port and system
When designing and integrating a charging system for an electric vehicle conversion, several key considerations must be made to ensure a safe, efficient, and user-friendly setup. The charging port is a critical component, as it serves as the interface between the vehicle and the external power source. Here's a step-by-step guide to designing and integrating this essential system:
- Choose the Right Charging Port: Select a charging port that is compatible with the vehicle's electrical system and the desired charging speed. Common types include AC (Alternating Current) and DC (Direct Current) ports. AC ports are typically used for home charging and are more common in standard vehicle conversions. DC ports, on the other hand, are faster and are often used for public charging stations. Consider the vehicle's battery capacity and the charging infrastructure available to make an informed decision.
- Electrical Wiring and Connections: Design a wiring harness that connects the charging port to the vehicle's battery and power electronics. This wiring should be carefully planned to ensure proper voltage and current handling. Use high-quality, insulated wires to prevent electrical hazards. Connect the charging port's output to the vehicle's battery management system (BMS) to monitor charging levels and protect the battery from overcharging or over-discharging.
- Charging System Integration: The charging system consists of several components. Firstly, a charging controller is essential to regulate the charging process, ensuring the battery is charged safely and efficiently. This controller should be compatible with the chosen charging port and power source. Additionally, consider integrating a battery gauge or display to provide real-time charging status to the driver. This can be a simple LED indicator or a more advanced digital display.
- Safety Measures: Electric vehicle conversions require stringent safety measures. Install a circuit breaker or fuse system to protect against overcurrent and short-circuit situations. Implement a ground-fault circuit interrupter (GFCI) to prevent electrical shocks. Ensure that the charging system is designed to handle the expected current draw and that all connections are secure to avoid overheating or electrical faults.
- Mounting and Accessibility: Design the charging port's mounting system to ensure it is securely attached to the vehicle's body or a suitable mounting surface. Consider the driver's convenience and accessibility when placing the charging port. It should be easily accessible from outside the vehicle and positioned to avoid interference with other vehicle components.
- Testing and Validation: After integration, thoroughly test the charging system. Conduct voltage and current measurements to ensure it meets the required specifications. Perform charging cycles under various conditions to validate the system's performance and safety. This step is crucial to identify and rectify any potential issues before final installation.
Unlocking EV Savings: A Guide to Claiming Your Subsidy
You may want to see also
Testing and Calibration: Thoroughly test and calibrate the electric vehicle for safe operation
Before putting your newly converted electric vehicle on the road, it is crucial to conduct a series of tests and calibrations to ensure its safe and efficient operation. This process involves a comprehensive evaluation of various systems and components to identify and rectify any potential issues. Here's a step-by-step guide to the testing and calibration process:
Battery Performance Testing: Begin by assessing the battery's performance. This includes measuring its voltage, current, and capacity to ensure it meets the required specifications. Use specialized equipment to test the battery's health, including its ability to charge and discharge efficiently. Check for any anomalies in the battery's behavior, such as excessive temperature fluctuations or irregular voltage drops, which could indicate potential issues. Calibrate the battery management system to optimize its performance and ensure it operates within safe parameters.
Motor and Inverter Calibration: The electric motor and inverter are critical components that require precise calibration. Test the motor's torque and power output to ensure it delivers the expected performance. Adjust the inverter settings to match the motor's characteristics, ensuring efficient power distribution. Calibration should focus on optimizing the motor's response, including acceleration and deceleration, to match the vehicle's intended driving characteristics.
Charging System Evaluation: Thoroughly test the charging system to ensure it functions correctly. Connect the vehicle to various charging stations and monitor the charging process. Check for any errors or abnormalities during charging, such as incorrect voltage or current levels. Calibrate the charging system to accept and manage the appropriate charging rates, ensuring the battery's longevity and safety.
Brake and Safety Systems: Electric vehicles often have regenerative braking systems, so test and calibrate these to ensure smooth and safe braking. Evaluate the braking distance and adjust the system if needed. Additionally, test all safety features, including sensors, airbags (if applicable), and the vehicle's overall stability control system. Ensure that all safety mechanisms respond appropriately to various driving conditions.
Performance and Handling Tests: Conduct performance tests to assess the vehicle's overall driving experience. This includes acceleration, top speed, and handling tests. Evaluate the vehicle's response to driver inputs and make any necessary adjustments to the control systems. Calibrate the throttle and steering to provide a smooth and responsive driving feel.
Emissions and Noise Testing: While electric vehicles produce zero tailpipe emissions, it's essential to test and ensure that the conversion process hasn't introduced any harmful emissions or excessive noise. Use specialized equipment to measure and analyze the vehicle's emissions and noise levels, ensuring they comply with regulations.
After completing these tests and calibrations, you should have a fully optimized electric vehicle ready for the road. This process is crucial to ensure the safety, efficiency, and reliability of your converted vehicle, providing a positive driving experience while promoting sustainable transportation.
Georgia EV Tax Credit: A Step-by-Step Guide to Maximizing Your Savings
You may want to see also
Frequently asked questions
The first step is to assess the vehicle's suitability for conversion. Consider factors like the vehicle's age, make, model, and existing mechanical condition. Research and choose an appropriate electric vehicle (EV) conversion kit that matches your vehicle's specifications. This kit should include an electric motor, controller, batteries, and associated wiring.
Selecting the right motor depends on various factors. Consider the vehicle's weight, desired performance, and range requirements. Research and choose a motor with the appropriate power output and torque to match your vehicle's needs. Ensure the motor is compatible with the vehicle's transmission and drivetrain. Consult with experts or EV conversion specialists to make an informed decision.
Installation typically involves removing the existing internal combustion engine and transmission. Mount the electric motor onto the vehicle's frame, ensuring proper alignment and secure fastening. Connect the motor to the controller, which regulates power flow. Route and install the wiring carefully, following the kit instructions. Test the system to ensure proper functionality and make any necessary adjustments.
Choose high-capacity lithium-ion batteries suitable for your conversion. Install the battery pack in a secure location, often beneath the floor or in the trunk, ensuring it is well-ventilated and protected from extreme temperatures. Connect the batteries to the controller and motor using the provided wiring. Implement a battery management system to monitor and control charging, discharging, and overall battery health.