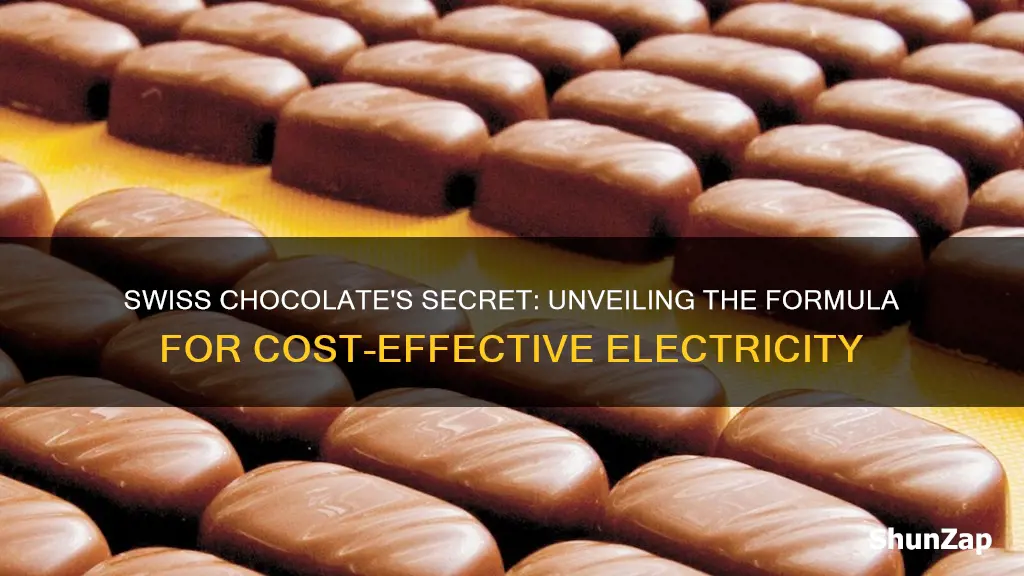
Swiss chocolate manufacturing companies have a unique challenge when it comes to managing electricity costs. The production process requires a significant amount of energy, especially for the complex machinery used to grind, melt, and temper chocolate. To optimize their operations, these companies have developed a sophisticated formula that takes into account various factors such as the type of chocolate, the size and efficiency of the equipment, and the local energy market. This formula helps them calculate the most cost-effective way to produce chocolate while ensuring the highest quality. By understanding and managing their electricity costs, these Swiss chocolate makers can maintain their reputation for excellence and sustainability in an energy-intensive industry.
What You'll Learn
- Ingredient Costs: Chocolate production relies on specific ingredients, each with unique price fluctuations
- Energy Consumption: Manufacturing chocolate requires significant energy, impacting electricity costs
- Process Optimization: Efficient processes can reduce electricity usage and associated costs
- Scale and Volume: Larger production volumes may offer economies of scale for electricity
- Market Dynamics: Global market trends influence raw material and energy prices, affecting Swiss chocolate costs
Ingredient Costs: Chocolate production relies on specific ingredients, each with unique price fluctuations
Chocolate production is an intricate process that demands a careful selection of ingredients, each contributing to the unique flavor and texture that defines this beloved treat. The cost of these ingredients is a critical factor in the overall production expenses, especially when considering the price volatility that can significantly impact the industry.
The primary ingredient, of course, is chocolate itself, derived from the beans of the cacao tree. The price of cocoa beans is subject to various market forces, including global supply and demand dynamics, weather conditions affecting crop yields, and economic factors in major producing countries. For instance, a sudden decrease in cocoa production due to adverse weather might lead to a surge in prices, impacting the overall cost structure for chocolate manufacturers.
Other essential ingredients include sugar, milk, and various flavorings and additives. Sugar, a fundamental component, is relatively stable in price, but its cost can still fluctuate based on agricultural factors and global sugar market trends. Milk, crucial for its creamy texture and flavor, is another variable. The price of milk is influenced by dairy farming practices, seasonal variations, and the overall health of the dairy industry.
Additionally, chocolate manufacturers often incorporate a range of flavorings and additives to create distinct tastes and textures. These ingredients can include vanilla, cinnamon, nuts, and various natural or artificial flavorings. The cost of these additives can vary widely, with some being more expensive due to their rarity or the complexity of their extraction processes. For instance, certain exotic spices or rare floral essences might be more costly, adding to the overall expense of production.
Understanding these ingredient costs is vital for chocolate manufacturers, as it directly impacts their profitability. Price volatility can lead to significant challenges in production planning and budgeting. To mitigate these risks, companies often employ various strategies, such as long-term supply contracts, inventory management, and cost-saving measures in production processes. By carefully monitoring these ingredient costs and adapting to market fluctuations, chocolate manufacturers can ensure the sustainability and competitiveness of their businesses.
Electricity Providers for Rancho Cucamonga's 10825 7th Street
You may want to see also
Energy Consumption: Manufacturing chocolate requires significant energy, impacting electricity costs
The process of chocolate manufacturing is an energy-intensive endeavor, with electricity costs playing a pivotal role in the overall production expenses for Swiss chocolate companies. The intricate steps involved in transforming cocoa beans into the delectable treat we know and love demand substantial energy input. From the initial stages of roasting and grinding to the complex processes of conching and tempering, each step requires careful management of energy resources.
One of the primary energy consumers in chocolate production is the roasting of cocoa beans. This process, essential for developing the beans' flavor and aroma, requires significant heat energy. The roasting process is typically carried out in large, industrial-scale roasters, which operate at high temperatures to ensure uniform roasting. The energy required for this step is substantial, and the cost of electricity directly influences the overall production cost.
Following roasting, the beans undergo a series of grinding and refining processes to create a smooth, consistent chocolate liquor. This stage involves heavy machinery and requires a considerable amount of electrical power. The energy consumption during this phase is particularly notable due to the need for continuous operation and the high-speed mixing and grinding of the chocolate mass.
The subsequent steps of conching and tempering further emphasize the energy demands of chocolate manufacturing. Conching, a process that involves mixing and aerating the chocolate to develop its texture and flavor, requires extensive energy input. The machines used for conching operate continuously, ensuring the chocolate's consistency and quality. Tempering, a process to stabilize the chocolate's crystal structure, also demands precise temperature control, contributing to the overall energy consumption.
Managing energy efficiency is crucial for Swiss chocolate manufacturers to optimize their electricity costs. Implementing energy-efficient technologies, such as advanced roasting and refining equipment, can significantly reduce energy usage. Additionally, adopting renewable energy sources and implementing energy-saving practices throughout the production process can help mitigate the environmental impact and financial burden of high electricity costs. By carefully monitoring and optimizing energy consumption, chocolate producers can ensure the sustainability and economic viability of their operations.
Unveiling the Electric Power Providers in 90021: A Comprehensive Guide
You may want to see also
Process Optimization: Efficient processes can reduce electricity usage and associated costs
The Swiss chocolate industry is renowned for its precision and attention to detail, and optimizing processes can significantly impact electricity costs, which are a substantial expense for these manufacturers. One key area for process optimization is energy-efficient machinery and equipment. Chocolate production involves various processes, from ingredient mixing to tempering and molding. Each step requires specific machinery, and older models can be energy-intensive, leading to higher electricity bills. Upgrading to energy-efficient machines can be a strategic move. For instance, modern mixing and refining equipment often incorporates advanced technologies that optimize mixing speeds and temperatures, reducing energy consumption without compromising product quality. Similarly, investing in energy-efficient tempering machines can help control the temperature and consistency of chocolate, ensuring a perfect finish while using less electricity.
Another aspect of process optimization is the implementation of automated systems and smart sensors. Automation can streamline production, reducing the need for constant human intervention, which often leads to increased electricity usage. Automated systems can monitor and control various parameters in real-time, ensuring that processes run efficiently. For example, sensors can detect the temperature and humidity levels in the chocolate storage area, adjusting ventilation and cooling systems accordingly. This not only saves electricity but also maintains the quality of the chocolate by preventing spoilage.
Process optimization also involves re-evaluating and redesigning production lines to minimize waste and maximize output. This could include rearranging machinery to create more efficient workflows, reducing the time and energy required for each production step. For instance, implementing a just-in-time inventory system can minimize the need for excessive storage, which often requires additional lighting and climate control, thus reducing electricity costs. Additionally, optimizing the cooling and freezing processes can ensure that chocolate products are stored at the optimal temperature, reducing energy usage for refrigeration.
Furthermore, the Swiss chocolate manufacturers can focus on employee training and awareness programs. Educating staff about energy-efficient practices and providing guidelines for energy conservation can lead to behavioral changes that directly impact electricity usage. Simple actions like turning off machines when not in use, reporting any equipment malfunctions promptly, and adopting energy-conscious habits can collectively result in significant cost savings.
In summary, process optimization in Swiss chocolate manufacturing involves a multi-faceted approach. It includes investing in modern, energy-efficient machinery, implementing automated systems, redesigning production lines for efficiency, and educating employees about sustainable practices. By adopting these strategies, chocolate producers can reduce their reliance on electricity, lower operational costs, and contribute to a more sustainable and environmentally friendly production process. This approach not only benefits the company's bottom line but also aligns with the industry's commitment to quality and innovation.
Electricity Coverage: Who Serves 300 Randell Drive, Clarksville, TN?
You may want to see also
Scale and Volume: Larger production volumes may offer economies of scale for electricity
The concept of economies of scale is particularly relevant in the context of electricity costs for chocolate manufacturing companies, especially those in Switzerland, renowned for their high-quality chocolate production. As the production volume increases, several factors come into play that can significantly impact the cost of electricity.
Firstly, larger-scale operations often benefit from more efficient machinery and processes. Modern chocolate production lines are designed to handle higher output, and this increased capacity can lead to improved energy efficiency. For instance, advanced cocoa bean roasting and grinding equipment can process more beans in a shorter time, reducing the overall energy consumption per unit of chocolate produced. This efficiency gain is a direct result of the economies of scale, where the fixed costs of setting up and maintaining the machinery are distributed over a larger production volume, leading to lower per-unit costs.
Secondly, utility companies often provide incentives for businesses to increase their energy consumption during off-peak hours. This strategy encourages companies to optimize their production schedules to take advantage of lower electricity rates at specific times. By increasing production volume, chocolate manufacturers can better manage their energy usage, ensuring that they operate during these off-peak periods, thus reducing their overall electricity costs.
Furthermore, the relationship between scale and electricity cost is also evident in the management of energy-intensive processes. Larger production facilities can implement more sophisticated energy management systems, allowing for precise control over energy usage. This includes optimizing the temperature and humidity in chocolate storage areas, ensuring that energy is not wasted on maintaining ideal conditions for extended periods. Such control and optimization are crucial in reducing electricity costs, especially in the chocolate industry, where temperature and moisture control are critical to product quality.
In summary, larger production volumes in the chocolate manufacturing industry can lead to significant economies of scale in electricity costs. This is achieved through more efficient machinery, strategic energy usage during off-peak hours, and the implementation of advanced energy management systems. Understanding and utilizing these scale-based advantages can be a key factor in the financial success of Swiss chocolate companies, allowing them to maintain their reputation for quality while remaining competitive in the global market.
Unraveling the Mystery: What Does APS Electric Company Stand For?
You may want to see also
Market Dynamics: Global market trends influence raw material and energy prices, affecting Swiss chocolate costs
The global market dynamics play a pivotal role in shaping the cost structures of Swiss chocolate manufacturers, particularly in terms of raw materials and energy prices. One of the primary factors influencing these costs is the global supply and demand for cocoa beans, the cornerstone of chocolate production. Fluctuations in the international cocoa market can significantly impact the prices Swiss chocolatiers pay for this essential ingredient. For instance, a global drought affecting major cocoa-producing regions could lead to a shortage, driving up prices and subsequently increasing production costs for Swiss chocolate makers.
In addition to cocoa, other raw materials such as sugar, milk, and vanilla also experience global market trends that can affect Swiss chocolate prices. The availability and cost of these ingredients are often influenced by weather conditions, crop yields, and global trade policies. For example, a poor harvest of vanilla beans in Madagascar, a major producer, could result in higher prices for this spice, impacting the overall cost of chocolate production.
Energy prices, another critical component of production costs, are also subject to global market dynamics. Switzerland, like many other countries, relies on imported energy sources, making it susceptible to international energy market fluctuations. A surge in global oil or gas prices can lead to increased electricity and heating costs, which are essential for the various stages of chocolate manufacturing, from melting to tempering and packaging. These energy-intensive processes contribute significantly to the overall production expenses.
The global market's influence on raw materials and energy prices can create a complex web of challenges for Swiss chocolate manufacturers. To mitigate these costs, companies may explore strategies such as long-term supply contracts for raw materials, energy efficiency improvements, or even vertical integration to secure a more stable supply chain. Understanding and adapting to these global market trends is crucial for Swiss chocolate producers to maintain competitiveness in a dynamic and ever-changing market environment.
In summary, the global market trends have a profound impact on the raw material and energy costs of Swiss chocolate production. Chocolate manufacturers must closely monitor international markets, weather patterns, and global trade policies to anticipate and manage these costs effectively. By staying agile and implementing strategic initiatives, Swiss chocolatiers can navigate the challenges posed by global market dynamics and ensure the sustainability of their industry.
Cape Cod's Electric Company: Powering the Peninsula with Green Energy
You may want to see also
Frequently asked questions
The company employs a sophisticated formula that considers various factors. It includes the total energy consumption in kilowatt-hours (kWh) for each production phase, the regional electricity tariff, and the specific efficiency of their machinery. By multiplying these variables, they can determine the precise cost of electricity for a given production cycle.
While there isn't a universal formula, many Swiss chocolate manufacturers adapt a similar approach. They often tailor the calculation to their unique production methods and energy sources. This customization ensures an accurate representation of their specific electricity costs, which can vary based on factors like production volume, machinery age, and energy supply agreements.
Regular updates are essential to maintain accuracy. Swiss chocolate manufacturers typically review and adjust their electricity cost formulas monthly or quarterly. This frequency ensures that the calculations reflect the most current energy prices, production rates, and any changes in machinery efficiency, providing a reliable basis for financial planning and budgeting.