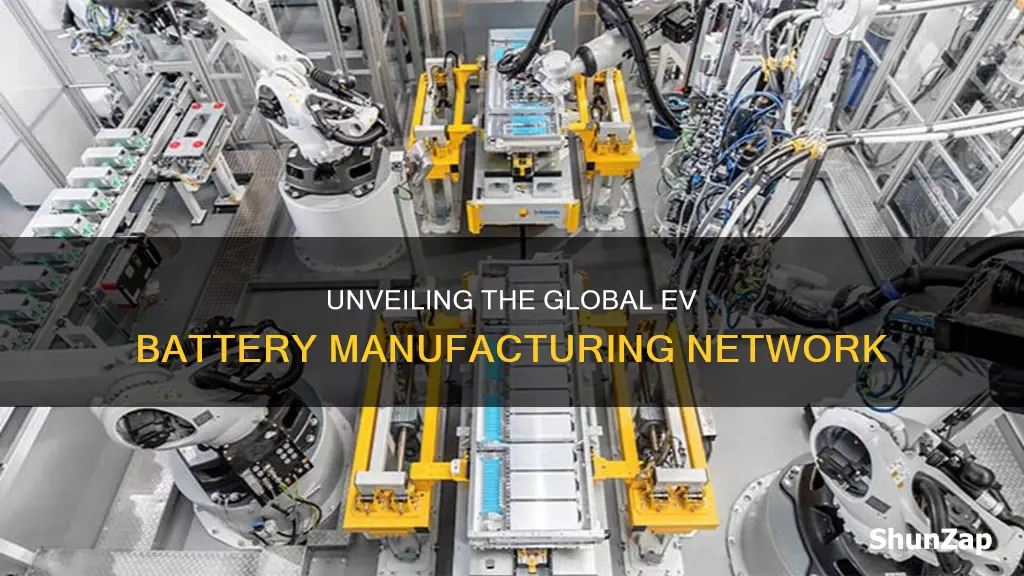
The production of electric vehicle (EV) batteries is a complex process that involves multiple stages and a global supply chain. These batteries, which power EVs, are typically made in specialized manufacturing facilities located in various regions around the world. The manufacturing process includes the extraction and processing of raw materials such as lithium, cobalt, and nickel, which are then assembled into battery cells and modules. Understanding the geographical distribution of these production sites is crucial as it influences the sustainability and efficiency of the EV industry, impacting factors like supply chain logistics and environmental considerations.
Characteristics | Values |
---|---|
Manufacturing Location | Electric vehicle batteries are primarily manufactured in Asia, with China being the largest producer. Other significant production hubs include South Korea, Japan, and India. |
Battery Chemistry | Common chemistries include Lithium-ion (Li-ion), Nickel-Metal Hydride (NiMH), and Sodium-ion (Na-ion). Li-ion batteries are the most prevalent due to their high energy density and performance. |
Production Process | The process involves multiple stages: electrode manufacturing, assembly, testing, and quality control. It requires specialized equipment and materials, including lithium, nickel, cobalt, and manganese. |
Supply Chain | The supply chain is complex, involving raw material extraction, processing, and assembly. Many companies have global supply chains to ensure a steady supply of materials and components. |
Market Leaders | Major battery manufacturers include Contemporary Amperex Technology (CATL) in China, Panasonic in Japan, and LG Energy Solution in South Korea. These companies dominate the market and supply batteries to various EV manufacturers. |
Regional Variations | Production varies by region due to factors like government incentives, market demand, and local manufacturing capabilities. For example, Europe and North America have seen increased investment in battery manufacturing facilities. |
Environmental Impact | Battery production can have environmental implications, including resource extraction, energy consumption, and waste management. Sustainable practices and recycling initiatives are being developed to address these concerns. |
What You'll Learn
- Manufacturing Process: From raw materials to finished cells, the intricate steps of battery production
- Supply Chain: Complex networks of suppliers and manufacturers across global regions
- Regional Specialization: Certain regions dominate battery production due to resource availability and expertise
- Environmental Impact: The ecological consequences of battery manufacturing, including resource extraction and waste management
- Labor Conditions: Ethical considerations and labor practices in the battery manufacturing industry
Manufacturing Process: From raw materials to finished cells, the intricate steps of battery production
The manufacturing of electric vehicle (EV) batteries is a complex process that involves multiple stages, from sourcing raw materials to assembling the final product. This intricate journey begins with the extraction and processing of essential elements, primarily lithium, cobalt, nickel, and manganese, which are the key components of lithium-ion batteries. These raw materials are sourced from various regions worldwide, with significant mining operations in countries like Australia, Chile, and the Democratic Republic of Congo for lithium, cobalt, and nickel, respectively. The extraction process is meticulous, ensuring the purity and quality of these materials, which are then transported to manufacturing facilities for further processing.
Once the raw materials are acquired, the manufacturing process commences with the preparation of the electrode materials. This involves a series of steps, starting with the mixing of the raw materials with binders and conductive additives to create a slurry. The slurry is then coated onto a metal current collector, typically made of aluminum or copper, to form the anode or cathode. This process is highly precise, requiring advanced coating techniques to ensure the uniform distribution of active materials. After coating, the electrodes undergo a drying and curing process to solidify the mixture and prepare it for the next stage.
The subsequent step is the assembly of the battery cells, which involves several intricate processes. The electrodes are carefully cut to size and shaped to fit the battery casing. This is followed by the formation of the battery cell, where the anode and cathode are stacked and separated by a porous separator, allowing ion movement while preventing electrical contact. The assembled cell is then wound or stacked to create the desired configuration, and the entire stack is inserted into the battery casing. This casing is typically made of a metal or polymer material and houses the cell, providing structural support and protection.
After the cell assembly, the battery undergoes a series of testing and quality control procedures. This includes electrical testing to ensure the cell's performance meets the required specifications. The batteries are also subjected to various environmental and safety tests to assess their behavior under different conditions. Once the batteries pass these rigorous tests, they are ready for the final packaging and integration into electric vehicles.
The journey from raw materials to finished EV batteries is a meticulous and intricate process, requiring advanced technologies and precise engineering. Each step, from material extraction to cell assembly, is crucial in ensuring the performance, safety, and reliability of the batteries that power electric vehicles. The manufacturing process is a testament to the complexity and innovation required in the development of sustainable energy storage solutions.
The Pioneers: Who Led the Charge for Electric Vehicles?
You may want to see also
Supply Chain: Complex networks of suppliers and manufacturers across global regions
The production of electric vehicle (EV) batteries is a complex and global supply chain process, involving a vast network of suppliers and manufacturers. This intricate web of connections ensures that the specialized components required for EV batteries can be sourced and assembled efficiently, meeting the growing demand for sustainable transportation. The supply chain for EV batteries is a critical aspect of the automotive industry, as it directly impacts the performance, cost, and environmental impact of these vehicles.
At the heart of this supply chain are the battery cell manufacturers, who produce the individual cells that form the core of EV batteries. These cells are typically made from a combination of lithium, cobalt, nickel, and manganese, among other materials. The manufacturing process involves multiple stages, starting with the extraction and purification of raw materials, followed by the creation of the battery's anode, cathode, and electrolyte. Each of these components is carefully designed and produced to meet specific performance and safety standards. For instance, the cathode material, often a lithium-based compound, is a critical element in determining the battery's energy density and overall efficiency.
Suppliers play a vital role in this process, providing the necessary materials, equipment, and expertise. These suppliers can be found across various regions, with some specializing in specific materials or technologies. For example, companies in Asia, such as Japan and South Korea, have a strong presence in the supply chain, offering advanced technologies for battery cell manufacturing and supplying high-quality raw materials. European and American companies also contribute significantly, focusing on research and development, as well as the production of specialized equipment for battery assembly.
The global nature of this supply chain is further emphasized by the presence of international companies and partnerships. Many EV battery manufacturers have established collaborations with suppliers worldwide to ensure a steady supply of materials and components. This global collaboration is essential to maintaining the high quality and consistency required for EV batteries, as well as to managing the complex logistics of transporting goods across borders. As a result, the supply chain for EV batteries is a dynamic and ever-evolving network, adapting to technological advancements, market demands, and environmental considerations.
In summary, the production of electric vehicle batteries involves a sophisticated global supply chain, with a network of suppliers and manufacturers working together to meet the increasing demand for sustainable transportation. This complex process ensures that the specialized components required for EV batteries are sourced, produced, and assembled efficiently, contributing to the overall success of the electric vehicle industry. Understanding this supply chain is crucial for investors, policymakers, and consumers alike, as it highlights the interconnectedness of the automotive, energy, and environmental sectors.
Electric Revolution: A Global Shift Towards Sustainable Driving?
You may want to see also
Regional Specialization: Certain regions dominate battery production due to resource availability and expertise
The global electric vehicle (EV) market has sparked a surge in demand for advanced battery technology, and as a result, specific regions have emerged as key players in the battery production landscape. This regional specialization is primarily driven by a combination of factors, including resource availability, skilled labor, and established supply chains.
One such region is Asia, particularly China, South Korea, and Japan. These countries have become powerhouses in the battery industry, with a strong focus on lithium-ion technology. China, in particular, has invested heavily in its battery manufacturing sector, benefiting from its vast reserves of lithium, cobalt, and other critical minerals. The country's rapid industrialization and the presence of large, state-owned battery manufacturers have contributed to its dominance. For instance, CATL (Contemporary Amperex Technology Limited), a Chinese company, is now one of the largest battery producers globally, supplying batteries to major EV manufacturers. South Korea and Japan also have a strong presence, with companies like LG Energy Solution and Panasonic leading the way, respectively. These Asian nations have a well-established supply chain, skilled workforce, and access to raw materials, making them ideal locations for battery production.
In Europe, Germany and its neighboring countries have also carved out a significant niche in the battery production market. The region benefits from a highly skilled workforce and a strong automotive industry. Germany, in particular, has a long history of automotive engineering and a robust research and development sector. The country's focus on sustainability and the push towards a carbon-neutral future have further fueled investments in battery technology. Additionally, the European Union's policies and incentives for EV adoption have encouraged the establishment of battery manufacturing facilities across the region.
The United States, while not as specialized as some regions, is also making strides in battery production. The country has a diverse range of battery manufacturers, with a focus on innovation and technology development. The US has a well-established energy sector, and its proximity to North American markets makes it an attractive location for EV battery production. States like Michigan and South Carolina have seen significant investments in battery manufacturing, often driven by partnerships with major EV manufacturers.
Furthermore, the Middle East and North Africa (MENA) region is another area with potential for battery production. Countries like Saudi Arabia and the United Arab Emirates have vast reserves of oil and natural gas, which can be utilized for the production of lithium-ion batteries. These regions are also exploring opportunities to diversify their economies and reduce reliance on fossil fuels. The MENA region's strategic location and access to global markets make it an attractive investment destination for battery manufacturers.
In summary, regional specialization in battery production is a result of a complex interplay of factors. Resource availability, skilled labor, and established supply chains are key determinants. Asia, with its strong focus on lithium-ion technology, leads the way, followed by Europe's automotive expertise and the US's innovation-driven approach. The MENA region also presents potential opportunities, driven by economic diversification and strategic advantages. As the EV market continues to grow, these regions are likely to play a pivotal role in meeting the increasing demand for advanced battery technology.
GM's Electric Future: Will Chevy Go All-In?
You may want to see also
Environmental Impact: The ecological consequences of battery manufacturing, including resource extraction and waste management
The manufacturing of electric vehicle (EV) batteries has significant environmental implications, primarily due to the resource-intensive nature of the process and the potential for hazardous waste generation. The ecological consequences of battery production can be far-reaching, impacting ecosystems, water resources, and air quality.
One of the critical environmental concerns is the extraction of raw materials. Lithium-ion batteries, commonly used in EVs, require the extraction of various metals and minerals, including lithium, cobalt, nickel, and manganese. These resources are often obtained through mining operations, which can have devastating effects on local ecosystems. For instance, lithium mining can lead to habitat destruction, soil erosion, and water pollution, especially if proper environmental regulations are not in place. The process of extracting these materials often involves energy-intensive methods, contributing to the carbon footprint of battery manufacturing.
The manufacturing process itself also poses challenges. Battery production facilities require substantial energy consumption, often relying on non-renewable sources, which further exacerbates the environmental impact. Additionally, the chemical processes involved can release pollutants into the air and water, posing risks to nearby communities and ecosystems. The handling and disposal of hazardous chemicals and waste materials are critical aspects that need careful management to prevent soil and water contamination.
Waste management is another critical issue in the lifecycle of EV batteries. As batteries age or become obsolete, they need to be recycled or disposed of properly. Improper disposal can lead to the release of toxic substances into the environment. Recycling processes must be efficient and environmentally friendly to minimize the ecological footprint. Current recycling methods often involve energy-intensive processes and can generate significant amounts of waste, highlighting the need for more sustainable recycling technologies.
Furthermore, the transportation of raw materials and finished batteries contributes to the overall environmental impact. The logistics involved in sourcing materials from various regions and transporting them to manufacturing sites can result in significant carbon emissions. Optimizing supply chains and adopting more sustainable transportation methods are essential steps towards reducing the ecological consequences of battery manufacturing.
In summary, the environmental impact of EV battery manufacturing is a complex issue. It encompasses the extraction of finite resources, energy-intensive production processes, waste management challenges, and the need for sustainable supply chain practices. Addressing these environmental concerns is crucial for the long-term viability of the EV industry and the transition to a more sustainable transportation ecosystem.
Electric Vehicle Sales Leaders: Who's Dominating the Market?
You may want to see also
Labor Conditions: Ethical considerations and labor practices in the battery manufacturing industry
The production of electric vehicle (EV) batteries is a complex process that involves multiple stages, from raw material extraction to assembly. While the focus on environmental sustainability is crucial, it is equally important to shed light on the labor conditions and ethical considerations within the battery manufacturing industry. This aspect often remains in the shadows, despite the growing demand for EVs and the increasing scrutiny on supply chains.
Labor practices in the battery manufacturing sector have been a subject of concern, particularly in regions where production facilities are located. The industry's rapid growth has led to a surge in manufacturing jobs, attracting workers from various backgrounds. However, the nature of battery production, which often involves hazardous chemicals and heavy machinery, raises significant safety and health issues. Workers in these facilities are exposed to potential risks, including chemical burns, respiratory problems, and even explosions, especially in the case of lithium-ion batteries. Ensuring the well-being of employees through stringent safety protocols and regular training is essential to mitigate these risks.
Ethical considerations come into play when examining the social impact of battery manufacturing. The industry's reliance on certain raw materials, such as lithium and cobalt, has led to environmental and social challenges in the regions where these materials are sourced. For instance, the extraction of cobalt in the Democratic Republic of Congo (DRC) has been associated with child labor and human rights abuses. As a result, companies are increasingly under pressure to implement responsible sourcing practices, ensuring that their supply chains are free from exploitation and unethical labor practices. This includes conducting thorough due diligence, verifying the origin of materials, and promoting fair trade practices.
Furthermore, the global nature of the EV battery supply chain highlights the importance of international cooperation and standards. As batteries are produced in various countries, it becomes crucial to establish labor standards and regulations that are consistent and enforceable across borders. This involves collaboration between governments, industry leaders, and international organizations to create a framework that promotes ethical labor practices while also supporting economic growth in the manufacturing sector.
In summary, the labor conditions and ethical considerations in the battery manufacturing industry are integral to the overall sustainability and success of the EV market. By addressing safety concerns, promoting responsible sourcing, and advocating for global labor standards, the industry can ensure that the benefits of electric vehicles are shared equitably while minimizing the potential negative impacts on workers and communities. It is through a comprehensive approach that the industry can move towards a more sustainable and socially responsible future.
Electric Road Trip: Tips for Planning Your EV Adventure
You may want to see also
Frequently asked questions
Electric vehicle batteries are predominantly produced in specialized factories, often referred to as "battery manufacturing facilities" or "battery plants." These facilities are strategically located near major markets to ensure efficient supply chains and reduce transportation costs. Countries like China, the United States, South Korea, and Japan have significant battery manufacturing capabilities, with many companies establishing production sites in these regions.
Yes, the market for electric vehicle batteries is highly concentrated in a few key regions. Asia, particularly China, South Korea, and Japan, is a major player in the battery manufacturing sector. Chinese companies, such as Contemporary Amperex Technology (CATL), have become global leaders in battery production, supplying batteries to numerous EV manufacturers worldwide. Additionally, South Korea's LG Energy Solution and Samsung SDI, and Japan's Panasonic and Toyota are also significant players in this industry.
Battery manufacturers are increasingly focusing on sustainable practices and reducing their environmental footprint. Many companies invest in research and development to improve recycling technologies, allowing for the recovery of materials from end-of-life batteries. They also aim to minimize waste generation and energy consumption during manufacturing. Some manufacturers have adopted green energy sources, such as solar or wind power, to power their production facilities. Furthermore, partnerships with raw material suppliers to ensure responsible sourcing and minimize environmental degradation are becoming more common in the industry.