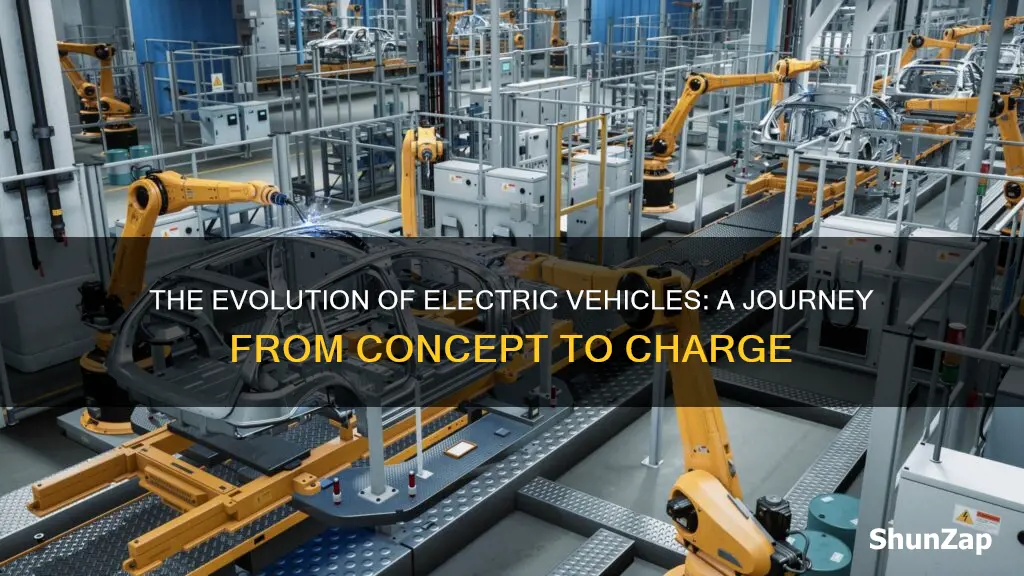
Electric vehicles (EVs) are a rapidly growing segment in the automotive industry, and their production process is quite different from traditional internal combustion engine (ICE) vehicles. The manufacturing of EVs involves several key steps, starting with the design and engineering phase, where engineers and designers create the vehicle's architecture, focusing on efficiency, performance, and sustainability. The next stage involves the selection of materials, with a strong emphasis on lightweight, high-strength components to improve energy efficiency. The assembly process is highly automated, utilizing advanced robotics and assembly lines to ensure precision and speed. EVs are often equipped with advanced technologies like lithium-ion batteries, electric motors, and sophisticated control systems, which are carefully integrated into the vehicle's structure. Finally, rigorous testing and quality control measures are implemented to ensure the vehicle's reliability and performance, marking the culmination of a complex manufacturing process that has revolutionized the automotive industry.
What You'll Learn
- Battery Technology: Advanced lithium-ion batteries power electric vehicles
- Motor Design: Electric motors convert energy into motion efficiently
- Charging Systems: Fast and wireless charging methods are integrated into EVs
- Body Construction: Lightweight materials reduce weight and improve performance
- Software Integration: Advanced software controls vehicle performance and driver experience
Battery Technology: Advanced lithium-ion batteries power electric vehicles
The heart of an electric vehicle's power lies in its advanced lithium-ion battery technology. These batteries are a crucial component, providing the energy needed to propel the vehicle and offering a sustainable alternative to traditional internal combustion engines. Lithium-ion batteries have revolutionized the automotive industry due to their high energy density, lightweight design, and long-lasting performance.
These batteries consist of multiple cells, each containing a positive electrode (cathode), a negative electrode (anode), and an electrolyte. The cathode is typically made of a lithium-based material, such as lithium cobalt oxide (LiCoO2), while the anode is often composed of graphite. The electrolyte facilitates the movement of lithium ions between the electrodes during charging and discharging. One of the key advantages of lithium-ion batteries is their ability to store and release energy efficiently. This is achieved through a process called electrochemical conversion, where lithium ions move from the anode to the cathode during charging and reverse the path during discharge, generating electricity.
The development of advanced lithium-ion batteries has focused on improving energy density, charging speed, and overall lifespan. Researchers and engineers have been working on enhancing the materials used in the electrodes to increase the battery's capacity and reduce weight. For instance, developing new cathode materials, such as lithium nickel manganese cobalt oxide (NMC), offers improved thermal stability and higher energy density compared to traditional LiCoO2. Similarly, anode materials like silicon and lithium metal have shown potential for increased energy storage capacity.
Battery management systems play a critical role in optimizing the performance and longevity of lithium-ion batteries. These systems monitor and control various parameters, including voltage, temperature, and current, to ensure safe and efficient operation. They also manage the charging and discharging cycles, preventing overcharging or over-discharging, which can significantly impact battery life.
In recent years, there has been a push towards solid-state batteries, which replace the liquid electrolyte with a solid conductive material. This innovation promises higher energy density, faster charging, and improved safety. Solid-state batteries have the potential to revolutionize electric vehicles, enabling longer ranges and faster charging times, making them more appealing to consumers.
The evolution of battery technology is an ongoing process, with continuous research and development aimed at creating more efficient, sustainable, and powerful energy storage solutions for electric vehicles. As the demand for cleaner and more sustainable transportation grows, advancements in battery technology will play a pivotal role in shaping the future of the automotive industry.
Electric Revolution: Soaring Demand for Green Cars
You may want to see also
Motor Design: Electric motors convert energy into motion efficiently
Electric motors are the heart of electric vehicles, and their design is a critical aspect of the overall efficiency and performance of these vehicles. The primary function of an electric motor in an EV is to convert electrical energy into mechanical motion, which propels the vehicle forward. This process is achieved through a combination of carefully engineered components and precise control systems.
Motor design involves several key elements. Firstly, the choice of motor type is crucial. There are two main types: AC (Alternating Current) and DC (Direct Current) motors. AC motors are commonly used in electric vehicles due to their simplicity, reliability, and ability to provide high torque at low speeds. They operate on the principle of electromagnetic induction, where alternating current is supplied to the motor's windings, creating a rotating magnetic field that drives the rotor. DC motors, on the other hand, offer higher efficiency and are often used in high-performance EVs, but they require more complex control systems.
The motor's construction includes a stator, which is the stationary part of the motor, and a rotor, the rotating part. The stator is typically made of laminated iron or steel, with coils of wire wound around it to create the magnetic field. The rotor, often made of lightweight materials like aluminum or copper, contains permanent magnets or electromagnets that interact with the stator's magnetic field. The design of these components is optimized to ensure efficient energy conversion and minimal energy loss.
One of the critical aspects of motor design is achieving high power density. This means packing a large amount of power into a compact space, which is essential for electric vehicles to have a small footprint and efficient use of space. Engineers strive to minimize the size of the motor while maximizing its output, allowing for more efficient packaging in the vehicle's chassis. This involves intricate winding patterns, advanced cooling systems to dissipate heat, and the use of lightweight materials to reduce overall weight.
Additionally, motor design focuses on controlling the speed and torque of the vehicle. Electric motors can provide high torque from a standstill, which is beneficial for acceleration. The control system adjusts the motor's power output and speed based on the driver's input, ensuring a smooth and responsive driving experience. This control is achieved through sophisticated electronic controls and sensors that monitor the motor's performance in real time.
Electric Vehicles: Fire Risks and Safety Concerns Explored
You may want to see also
Charging Systems: Fast and wireless charging methods are integrated into EVs
The integration of fast and wireless charging systems into electric vehicles (EVs) is a significant advancement in the automotive industry, addressing the critical need for efficient and convenient charging solutions. This technology enables EVs to recharge rapidly, reducing the time required for charging compared to traditional methods, and offering a more seamless and user-friendly experience for drivers.
Fast charging systems are designed to replenish a substantial amount of an EV's battery in a relatively short time. These systems typically utilize advanced power electronics and high-voltage direct current (DC) to rapidly transfer energy from the charging station to the vehicle. The charging infrastructure often includes specialized connectors and communication protocols to ensure safe and efficient power transfer. Fast charging stations can provide power output ranging from 50 kW to several hundred kW, significantly reducing the charging time, especially for larger battery packs. For instance, a 100 kWh battery can be charged to 80% in as little as 30 minutes with a fast-charging station.
Wireless charging, also known as inductive charging, is another innovative feature that eliminates the need for physical connectors. This method involves a charging pad or station placed under the vehicle, which uses electromagnetic fields to transfer energy to the battery. The EV's battery is equipped with a receiver coil that induces a current when exposed to the electromagnetic field, generating power that charges the battery. Wireless charging offers convenience and a sleek design, as it removes the need for cables and connectors, making it aesthetically pleasing and reducing potential wear and tear on the vehicle's charging port.
The implementation of fast and wireless charging methods requires careful consideration of safety and efficiency. These systems must adhere to strict standards and regulations to ensure the protection of both the vehicle and the charging infrastructure. Advanced safety features, such as temperature monitoring and fault detection, are integrated to prevent overheating, short circuits, and other potential hazards. Additionally, efficient power management systems optimize energy transfer, minimizing energy losses and maximizing the charging speed.
In summary, the integration of fast and wireless charging systems into EVs is a crucial aspect of modern electric vehicle manufacturing. It addresses the challenge of providing efficient and convenient charging solutions, ensuring that EVs can be rapidly recharged and ready for the road. With these advancements, electric vehicles become more practical and appealing to a broader range of consumers, contributing to the widespread adoption of sustainable transportation.
Debunking the Electric Vehicle Myth: Unveiling the Truth
You may want to see also
Body Construction: Lightweight materials reduce weight and improve performance
The body construction of electric vehicles (EVs) is a critical aspect of their design, focusing on achieving a lightweight yet robust structure. This is a key factor in enhancing performance and efficiency, which are essential for the success of electric cars. The primary goal is to minimize weight while maintaining structural integrity, a challenge that engineers tackle through the strategic use of advanced materials.
One of the primary materials used in EV body construction is high-strength steel, which offers a balance between strength and weight. This steel is designed to be lightweight yet robust, capable of withstanding the stresses of everyday driving while keeping the overall weight of the vehicle low. The use of advanced steel alloys allows for the creation of a sturdy yet lightweight body, a crucial factor in the overall performance of the vehicle.
Carbon fiber-reinforced polymers (CFRP) are another key material in the EV industry. These composites are known for their exceptional strength-to-weight ratio, making them ideal for structural components. By incorporating carbon fiber into the polymer matrix, engineers can create a material that is both lightweight and incredibly strong. This is particularly useful in areas that require high structural integrity, such as the vehicle's floor, roof, and body panels.
The use of lightweight materials in EV body construction has a direct impact on performance. Lighter vehicles can accelerate more quickly, handle better, and offer improved energy efficiency. This is because less weight means less energy is required to move the vehicle, resulting in a more responsive and efficient driving experience. Additionally, the reduced weight can lead to better overall range, as the vehicle's battery can power the car for a longer distance without the extra burden of a heavy body.
In the pursuit of lightweight construction, engineers also consider the use of aluminum and advanced composites. These materials are often used for specific components, such as the vehicle's hood, trunk lid, or fenders, where weight reduction is crucial without compromising on structural integrity. The strategic placement of these materials ensures that the vehicle's body is both lightweight and strong, contributing to the overall performance and driving experience of electric cars.
Green Revolution: Unveiling the Environmental Impact of Electric Vehicles
You may want to see also
Software Integration: Advanced software controls vehicle performance and driver experience
The integration of advanced software is a critical aspect of modern electric vehicle (EV) manufacturing, revolutionizing how these vehicles perform and how drivers interact with them. This software plays a pivotal role in optimizing the driving experience, enhancing safety, and improving overall efficiency. At the heart of this technology is the vehicle's central control unit, often referred to as the Electronic Control Unit (ECU). This unit acts as the brain of the vehicle, processing data from various sensors and systems to make real-time decisions that affect the vehicle's performance.
One of the key functions of this software is in the management of the electric motor and battery. It controls the flow of energy, ensuring that the motor operates at the most efficient level for the given driving conditions. For instance, during acceleration, the software can adjust the power output to provide a smooth and responsive drive while also conserving energy. When the vehicle is stationary or during deceleration, the software can optimize the motor's operation to recharge the battery, maximizing the range and reducing the time needed for recharging.
Driver assistance systems are another area where software integration is transformative. These systems include features like adaptive cruise control, lane-keeping assist, and automatic emergency braking. Advanced algorithms enable these systems to interpret sensor data, such as radar and camera inputs, to make split-second decisions. For example, adaptive cruise control uses software to maintain a set speed while adjusting for the speed of the vehicle ahead, ensuring a safe and comfortable driving experience.
The software also contributes to the overall driving experience by offering personalized settings. Drivers can customize various parameters, such as steering feel, shift patterns, and even the sound of the electric motor, through the vehicle's infotainment system. This level of customization ensures that each driver can tailor the vehicle to their preferences, making the driving experience more enjoyable and satisfying.
Furthermore, over-the-air software updates have become a standard feature in modern EVs. This capability allows manufacturers to remotely update the vehicle's software, improving performance, fixing bugs, and adding new features without requiring a physical visit to a service center. This not only enhances the vehicle's longevity but also ensures that the EV remains up-to-date with the latest technological advancements, providing a consistent and improved driving experience over time.
Aerodynamic Design: The Secret to Electric Vehicle Efficiency
You may want to see also
Frequently asked questions
Electric vehicles (EVs) are primarily constructed using a variety of materials, including steel, aluminum, and high-strength plastics. The body structure often incorporates lightweight materials like carbon fiber composites to reduce weight and improve efficiency. Advanced high-strength steel (AHSS) is also used for its superior strength-to-weight ratio, ensuring structural integrity and safety.
The battery pack is a critical component of EVs, and its assembly involves several steps. It starts with the selection of individual cells, which are then arranged in modules. These modules are stacked and secured together to form the battery pack. Each cell is connected in series and parallel configurations to achieve the desired voltage and capacity. Advanced cooling systems are often integrated to maintain optimal temperatures during operation.
The electric motor is a key component that converts electrical energy into mechanical motion. Manufacturing involves precision engineering and involves several steps. The process typically includes designing and creating the motor's core, which is made of electrical steel laminations. Copper windings are then wound around the core, and the entire assembly is encased in a protective housing. Advanced manufacturing techniques like injection molding and 3D printing are used to produce the motor's components with high accuracy.
The electronics and control systems in EVs are complex and play a vital role in the vehicle's performance and safety. These systems include the battery management system (BMS), power electronics, and the central control unit. The BMS monitors and controls the battery pack's performance, ensuring optimal charging and discharging. Power electronics manage the flow of electricity between the battery and the motor. The central control unit processes data from various sensors and actuators, making real-time decisions to control the vehicle's operation. Integration involves precise wiring, advanced software development, and rigorous testing to ensure seamless functionality.