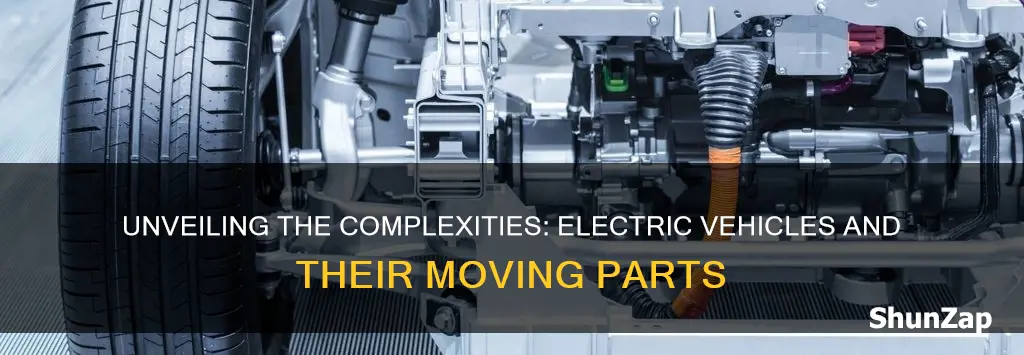
Electric vehicles (EVs) have revolutionized the automotive industry, offering a sustainable and efficient alternative to traditional internal combustion engine cars. One of the key aspects that set EVs apart is their unique mechanical design, which significantly differs from conventional vehicles. When it comes to the number of moving parts, EVs have fewer components compared to their gasoline counterparts. While traditional cars can have hundreds of moving parts, electric vehicles typically have fewer than half that number. This reduction in moving parts contributes to the overall efficiency and reliability of EVs, making them a popular choice for environmentally conscious drivers.
Characteristics | Values |
---|---|
Electric Motor | 1-3 (depending on the vehicle type and configuration) |
Transmission | 1 (typically a single-speed or two-speed transmission) |
Drivetrain | 1-2 (front-wheel drive or all-wheel drive) |
Differential | 1 (located in the drivetrain) |
Power Electronics | 1-2 (for inverter and DC-DC converter) |
Battery Pack | 1 (consists of multiple cells and modules) |
Charging System | 1-2 (for AC and DC charging) |
Cooling System | 1-2 (for motor and battery cooling) |
Steering Mechanism | 1 (power steering system) |
Suspension | 1-2 (dependent on the vehicle's suspension type) |
Braking System | 1-2 (disc or drum brakes) |
Total Moving Parts | 10-15 (estimated average for a typical electric vehicle) |
What You'll Learn
- Engine: Electric vehicle motors have fewer moving parts compared to internal combustion engines
- Transmission: Most EVs use single-speed transmissions, simplifying gear changes
- Drivetrain: The drivetrain connects the motor to the wheels, with fewer components
- Battery Pack: Batteries have numerous cells, but each cell has minimal moving parts
- Electronics: Advanced electronics control power distribution, with fewer mechanical components
Engine: Electric vehicle motors have fewer moving parts compared to internal combustion engines
Electric vehicle (EV) motors are a marvel of engineering, boasting a remarkable reduction in the number of moving parts compared to their internal combustion engine (ICE) counterparts. This design philosophy is a key advantage of electric powertrains, contributing to their efficiency, reliability, and overall performance.
At the heart of an electric motor lies a simple yet elegant design. It typically consists of a rotor and a stator. The rotor, often made of lightweight materials, is the moving component that rotates within the stator's magnetic field. This design is in stark contrast to the complex arrangements of valves, pistons, and cylinders found in ICEs. By eliminating these traditional engine components, EV motors significantly reduce the number of moving parts, leading to several benefits.
One of the primary advantages is the absence of the need for lubrication. ICEs require regular oil changes to keep their moving parts lubricated, which can be a maintenance hassle. In contrast, EV motors operate without the need for oil, as the rotor's rotation is facilitated by the magnetic field, eliminating the requirement for lubrication. This not only simplifies maintenance but also contributes to a cleaner and more environmentally friendly system.
The reduced number of moving parts in EV motors also translates to lower energy consumption. With fewer components to power and maintain, electric motors can be more efficient, converting a higher percentage of the energy from the battery into actual power. This efficiency is a crucial factor in extending the range of electric vehicles, addressing a significant concern among potential buyers.
Furthermore, the simplicity of EV motors contributes to their reliability. With fewer parts that can wear out or malfunction, the risk of breakdowns is significantly reduced. This reliability is essential for building consumer trust in electric vehicles, as it ensures a more dependable and hassle-free driving experience.
In summary, the engine of an electric vehicle is a testament to the ingenuity of modern automotive engineering. By minimizing the number of moving parts, EV motors offer a more efficient, reliable, and environmentally friendly alternative to traditional internal combustion engines. This design philosophy is a key factor in the growing popularity of electric vehicles, as it addresses many of the concerns associated with range, maintenance, and reliability.
Powering the Engine: The Secret to Vehicle Electricity
You may want to see also
Transmission: Most EVs use single-speed transmissions, simplifying gear changes
Electric vehicles (EVs) have revolutionized the automotive industry, offering an eco-friendly and efficient mode of transportation. One of the key factors contributing to their success is the design and functionality of their transmission systems. Unlike traditional internal combustion engine vehicles, EVs often employ a unique approach to gear management, which significantly reduces the number of moving parts and simplifies the overall transmission mechanism.
The transmission in most electric cars is a single-speed transmission, a departure from the multi-gear systems commonly found in conventional vehicles. This design choice is a direct result of the inherent characteristics of electric motors. Electric motors provide a high torque output from a standstill, allowing EVs to accelerate quickly and efficiently. A single-speed transmission is ideal for this purpose as it enables the vehicle to maintain optimal performance across various driving conditions. By eliminating the need for multiple gears, the transmission becomes more compact and lightweight, contributing to the overall efficiency of the EV.
The simplicity of a single-speed transmission is a game-changer in terms of reliability and maintenance. With fewer components, the risk of mechanical failure is reduced, leading to lower maintenance costs and increased vehicle longevity. This design philosophy aligns with the overall goal of EVs, which is to provide a cost-effective and environmentally friendly transportation solution. The absence of complex gear changes also enhances the driving experience, as it eliminates the need for the driver to manually shift gears, making the driving process smoother and more intuitive.
Furthermore, the single-speed transmission in EVs is designed to optimize power delivery. By maintaining a constant gear ratio, the transmission ensures that the electric motor delivers its full torque output at all times. This results in a consistent and powerful performance, making EVs capable of rapid acceleration and maintaining high speeds with ease. The efficiency gained from this design choice is a significant advantage over traditional vehicles, where gear changes can lead to temporary power loss and reduced performance.
In summary, the transmission system in electric vehicles is a testament to the innovative approach taken to optimize performance and efficiency. The use of single-speed transmissions simplifies gear changes, reduces mechanical complexity, and enhances the overall driving experience. This design choice is a key factor in the widespread adoption of EVs, contributing to their reputation as a modern, efficient, and environmentally conscious mode of transportation.
Unveiling the Power of EV: Electric Vehicles Explained
You may want to see also
Drivetrain: The drivetrain connects the motor to the wheels, with fewer components
The drivetrain of an electric vehicle (EV) is a crucial component that facilitates the transfer of power from the electric motor to the wheels, enabling the vehicle to move. Unlike traditional internal combustion engine (ICE) vehicles, EVs have a significantly simpler drivetrain design, which contributes to their overall efficiency and reliability. This reduction in complexity is primarily due to the absence of several components found in conventional drivetrains.
In a typical ICE vehicle, the drivetrain includes various components such as the transmission, driveshaft, and differential, each with multiple moving parts. These components are necessary to transmit power from the engine to the wheels, allowing for different speeds and torque requirements. However, in an EV, the drivetrain is streamlined, often consisting of just a few essential parts.
The simplified drivetrain in EVs typically includes a single-speed transmission or a fixed ratio gear set, which directly connects the motor to the differential. This design eliminates the need for complex gearboxes and multiple shifters, reducing the number of moving parts significantly. The motor itself, often a high-torque, high-efficiency electric motor, provides the necessary power to turn the wheels.
One of the key advantages of this simplified drivetrain is its reliability. With fewer components, there are fewer potential failure points, resulting in reduced maintenance requirements. Additionally, the absence of traditional transmission components means that EVs often have a more linear power delivery, providing a smooth and responsive driving experience.
Furthermore, the reduced complexity of the drivetrain contributes to the overall weight and size of the vehicle. EVs can be designed with more efficient packaging, allowing for a lower center of gravity and improved handling. This design philosophy is a significant factor in the popularity and appeal of electric vehicles, as it enhances their performance and driving dynamics.
In summary, the drivetrain of an electric vehicle is a critical yet relatively simple system that connects the motor to the wheels. Its streamlined design, with fewer moving parts, contributes to the overall efficiency, reliability, and performance of EVs, making them an attractive and modern alternative to traditional combustion engine vehicles.
Unveiling the Power: Hybrid Vehicles' Dual-Engine Drive
You may want to see also
Battery Pack: Batteries have numerous cells, but each cell has minimal moving parts
The battery pack is a critical component of an electric vehicle (EV), and it is designed to store and supply the electrical energy required to power the vehicle. While the overall battery pack consists of multiple cells, it is important to understand that each individual cell has a relatively simple design with minimal moving parts.
A typical battery cell comprises several key components, including an anode, a cathode, an electrolyte, and separators. The anode and cathode are the electrodes where chemical reactions occur during charging and discharging. These electrodes are often made of materials like lithium cobalt oxide (LCO) or lithium iron phosphate (LFP), which have a solid structure with no moving parts. The electrolyte, typically a liquid or gel, facilitates the movement of ions between the electrodes, but it does not involve any mechanical motion. Separators, usually made of polymer materials, prevent the electrodes from coming into direct contact while allowing the movement of ions.
The design of these cells is intentionally simplified to minimize the number of moving parts, which is a significant advantage over traditional internal combustion engines. In an internal combustion engine, there are numerous moving components, such as pistons, crankshafts, and valves, which are required to convert chemical energy into mechanical work. In contrast, the cells in a battery pack rely on electrochemical reactions, which are highly efficient and produce minimal mechanical stress.
The absence of complex moving parts in each cell contributes to the overall reliability and longevity of the battery pack. With fewer components prone to wear and tear, EV manufacturers can design batteries that are more durable and require less maintenance over time. This simplicity also allows for more efficient manufacturing processes, as the production of cells with minimal moving parts is generally less complex and more cost-effective.
Furthermore, the design of battery cells with minimal moving parts enables engineers to pack more cells into a given space, increasing the overall energy density of the battery pack. This is crucial for EVs, as higher energy density allows for longer driving ranges and shorter charging times, making electric vehicles more practical and appealing to consumers.
Electric Vehicles: CO2 Comparison with Diesel
You may want to see also
Electronics: Advanced electronics control power distribution, with fewer mechanical components
The evolution of electric vehicles (EVs) has been a remarkable journey, and at the heart of this transformation is the sophisticated use of electronics. One of the most significant advancements in EVs is the reduction of mechanical components and the increased reliance on advanced electronics to control power distribution. This shift has not only improved efficiency but has also contributed to the overall reliability and performance of electric vehicles.
In traditional internal combustion engine (ICE) vehicles, power distribution is primarily managed by a complex network of mechanical components. These include the engine itself, the transmission, and various actuators and sensors. Each of these parts has multiple moving components, such as gears, pistons, and valves, which work in harmony to deliver power to the wheels. However, this mechanical system is not without its drawbacks, including increased weight, complexity, and the need for frequent maintenance due to wear and tear.
In contrast, electric vehicles utilize advanced electronics to control power distribution, which significantly reduces the number of moving parts. The heart of an EV's power distribution system is the electric motor, which is a highly efficient and reliable component. Electric motors have far fewer moving parts compared to their internal combustion counterparts, often consisting of a rotor and stator assembly with minimal additional components. This simplicity in design translates to reduced weight, lower maintenance requirements, and improved overall efficiency.
The electronics in an EV play a crucial role in managing power flow. These systems include sophisticated controllers, inverters, and power electronics modules. These electronic components work together to regulate the flow of electricity from the battery to the motor, ensuring optimal performance and efficiency. For instance, the inverter converts direct current (DC) from the battery into alternating current (AC) that the motor can use, while the controller adjusts the motor's speed and torque based on driver input and road conditions. This level of control and precision is made possible by the advanced electronics, which can make split-second decisions to optimize performance and ensure a smooth driving experience.
Furthermore, the integration of advanced electronics has led to the development of regenerative braking systems in EVs. When the driver applies the brakes, the electric motor reverses its operation, acting as a generator to convert kinetic energy back into electrical energy, which is then stored in the battery. This process not only improves energy efficiency but also reduces wear on traditional braking components, further decreasing the number of moving parts in an EV.
In summary, the use of advanced electronics in electric vehicles has revolutionized power distribution, leading to a significant reduction in mechanical components and moving parts. This shift has contributed to improved efficiency, reliability, and performance, making EVs a more attractive and sustainable transportation option. As technology continues to advance, we can expect further innovations in electronics, potentially leading to even more efficient and environmentally friendly electric vehicles.
Electric Vehicles: The Missing Piece in Sustainable Transportation
You may want to see also
Frequently asked questions
Electric vehicles generally have fewer moving parts than their ICE counterparts. While traditional cars have numerous components like pistons, valves, camshafts, and transmissions, EVs rely on simpler mechanisms. The primary moving parts in an EV include the electric motor, inverter, and the reduction gear (if present). This simplicity often contributes to the reliability and lower maintenance requirements of electric vehicles.
The battery pack in an EV is designed to be a sealed unit with minimal moving parts. Each battery cell has a limited number of components, such as the anode, cathode, separator, and electrolyte. However, there might be some additional mechanisms for cooling and monitoring, but these are typically automated and require less maintenance compared to the complex systems in ICE vehicles.
The drivetrain of an EV is relatively straightforward. It usually consists of the electric motor, which drives the wheels via a simple gear system or a single-speed transmission. This design significantly reduces the number of moving parts compared to the complex transmissions found in traditional cars, leading to improved efficiency and durability.
The charging system of an EV is relatively simple and has fewer moving parts. It typically includes the charging port, connector, and the charging cable, which is connected to the onboard charger. The onboard charger converts the alternating current (AC) from the charging station to direct current (DC) to charge the battery, and it has fewer mechanical components than the fuel system in a conventional car.
The reduced number of moving parts in electric vehicles contributes to their overall efficiency and performance. With fewer components, there is less friction, less energy loss, and improved power transmission. This simplicity also makes EVs quieter, as there are no noisy engine components. Additionally, the lack of complex transmissions allows for quicker acceleration and better overall driving experience.