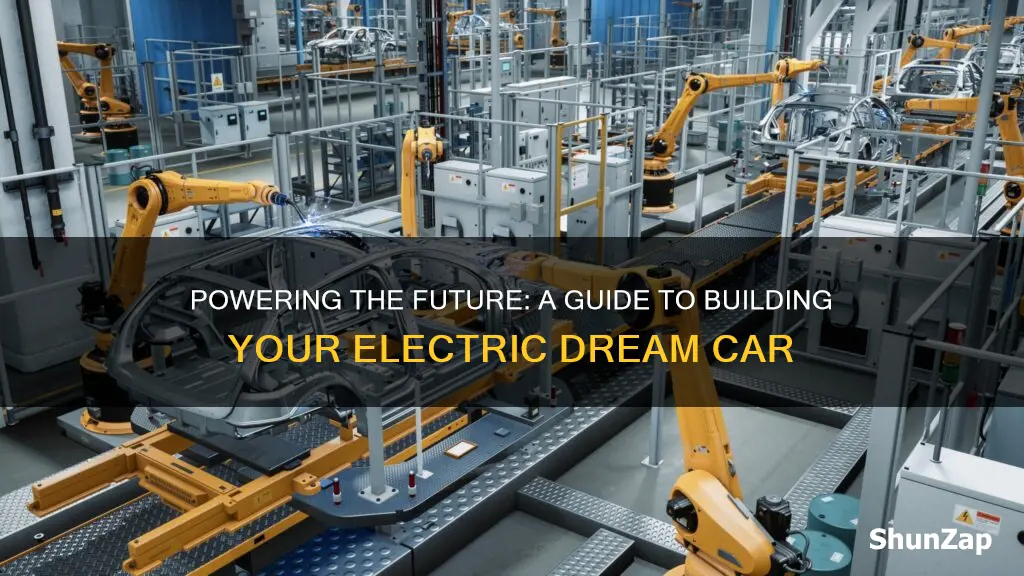
Building an electric vehicle (EV) is an exciting project that combines engineering, technology, and sustainability. It involves a series of intricate steps, from designing the vehicle's architecture to selecting the right components for the electric motor, battery, and charging system. The process requires a deep understanding of electrical engineering, as well as knowledge of materials science and manufacturing techniques. This guide will explore the key considerations and steps involved in constructing an electric vehicle, offering insights into the challenges and opportunities of this rapidly evolving field.
What You'll Learn
- Battery Technology: Choose efficient, high-capacity batteries for optimal range and performance
- Motor Selection: Opt for powerful, efficient motors suited to vehicle size and purpose
- Power Electronics: Design efficient power electronics for optimal energy conversion and control
- Charging Systems: Implement smart charging systems for safe and efficient battery charging
- Vehicle Structure: Utilize lightweight, strong materials to create a robust yet lightweight vehicle frame
Battery Technology: Choose efficient, high-capacity batteries for optimal range and performance
Battery technology is a critical component of electric vehicle (EV) design, as it directly impacts the vehicle's range, performance, and overall efficiency. When building an electric vehicle, choosing the right batteries is essential to ensure a successful and sustainable EV. Here's a detailed guide on selecting efficient and high-capacity batteries:
Battery Chemistry and Capacity: The first step is to understand the various battery chemistries available. Lithium-ion batteries are the most common choice for EVs due to their high energy density and relatively low self-discharge rate. Within lithium-ion technology, there are different types, such as nickel-cobalt-manganese (NMC) and lithium-iron-phosphate (LFP) batteries. NMC batteries offer higher energy density and better thermal stability, making them suitable for high-performance EVs. LFP batteries, on the other hand, provide a longer cycle life and are often used in vehicles requiring frequent deep discharges. When selecting batteries, consider the specific energy capacity (Wh/kg) and specific power (W/kg) to ensure they meet the vehicle's power and energy requirements.
High-Capacity Batteries for Range: To achieve optimal range, EV manufacturers should opt for high-capacity batteries. This involves choosing batteries with a higher energy density, allowing for more energy storage in a compact space. Modern lithium-ion batteries can provide energy densities of around 250-350 Wh/kg, but advancements in materials and cell design can push this even higher. For instance, solid-state batteries, which replace the liquid electrolyte with a solid conductive material, have the potential to offer significantly higher energy densities, thus extending the vehicle's range. It is crucial to match the battery capacity to the vehicle's estimated driving range requirements.
Efficiency and Performance: Battery efficiency is another critical factor. High-efficiency batteries can convert a larger percentage of stored energy into useful power, reducing energy waste and improving overall vehicle efficiency. This is particularly important for range anxiety, as efficient batteries can help extend the distance an EV can travel on a single charge. Additionally, consider the battery's power output and how it aligns with the vehicle's performance needs. High-performance EVs may require batteries with rapid charging capabilities and quick power delivery to accelerate efficiently.
Safety and Longevity: Safety is paramount in battery selection. Choose batteries with advanced safety features, such as thermal management systems to prevent overheating and overcharging protection circuits. The longevity of the battery pack is also essential. Look for batteries with a long cycle life, typically measured in thousands of charge-discharge cycles, ensuring the vehicle's battery will last for the vehicle's lifespan.
In summary, building an electric vehicle requires a careful selection of batteries that offer a balance between high capacity, efficiency, and performance. By choosing advanced battery technologies and considering the specific requirements of the EV, manufacturers can create sustainable and high-performing electric vehicles. This process involves a deep understanding of battery chemistry, energy density, and the integration of these components into the overall vehicle design.
Electric Vehicles: The Rapid Overtake in the Automotive Industry
You may want to see also
Motor Selection: Opt for powerful, efficient motors suited to vehicle size and purpose
When building an electric vehicle, motor selection is a critical aspect that significantly impacts performance, efficiency, and overall driving experience. The right motor choice will ensure your vehicle meets its intended purpose, whether it's for urban commuting, off-road adventures, or long-distance travel. Here's a detailed guide on how to approach motor selection:
Understand Your Vehicle's Requirements: Begin by evaluating the specific needs of your electric vehicle. Consider factors such as the desired top speed, acceleration capabilities, and the overall weight of the vehicle. For instance, a lightweight city car might require a different motor setup compared to a heavy-duty off-road vehicle. The size and type of your vehicle will influence the motor's power-to-weight ratio, which is crucial for performance and efficiency.
Motor Power and Efficiency: Electric motors come in various power outputs, typically measured in horsepower (hp) or kilowatts (kW). For optimal efficiency, aim for a motor that provides a balanced power-to-weight ratio. High-performance vehicles might require more powerful motors to achieve rapid acceleration, while efficiency-focused designs may prioritize motors with higher torque at lower RPMs. Modern electric vehicles often utilize advanced motor designs, such as permanent magnet synchronous motors, which offer excellent efficiency and power density.
Size and Space Constraints: The physical dimensions of your vehicle play a vital role in motor selection. Motors need to fit within the available space, often in the vehicle's underbody or within the wheel wells. Consider the motor's length, width, and height, ensuring it aligns with the vehicle's design. For instance, in-wheel motors are a popular choice as they provide a low-profile design and efficient power transmission to the wheels.
Purpose-Specific Motors: Different vehicle purposes may call for specialized motors. For instance, sports cars or high-performance EVs might benefit from high-output motors with advanced cooling systems to handle the extra heat. In contrast, electric scooters or urban mobility vehicles could utilize smaller, lightweight motors with good efficiency. Purpose-specific motors often feature unique designs and materials to optimize performance and durability.
Efficiency and Range: Efficient motors contribute to longer driving ranges, a critical factor for electric vehicles. Look for motors with advanced cooling systems and well-designed power electronics to minimize energy losses. Regenerative braking systems can also play a role in motor efficiency, capturing and reusing kinetic energy during braking. By selecting motors with high efficiency, you can ensure your vehicle provides an excellent driving range while minimizing energy consumption.
In summary, motor selection is a complex process that requires careful consideration of various factors. By understanding your vehicle's requirements, prioritizing power and efficiency, and accounting for size and purpose, you can make an informed decision when choosing the right motors for your electric vehicle. This approach ensures optimal performance, efficiency, and a satisfying driving experience.
Demystifying the Scrap Process: A Guide to Recycling Electric Vehicles
You may want to see also
Power Electronics: Design efficient power electronics for optimal energy conversion and control
Power electronics play a critical role in the efficiency and performance of electric vehicles (EVs). The primary goal in designing power electronics for EVs is to optimize energy conversion and control, ensuring that the vehicle's battery is utilized effectively while maintaining high efficiency. Here's a detailed guide on how to approach this design process:
- System Architecture and Component Selection: Begin by defining the overall architecture of the power electronics system. This includes deciding on the type of inverter (for AC-DC conversion) or converter (for DC-DC conversion) that will be used. For EVs, three-phase inverters are commonly employed to drive the electric motor. Select components such as power semiconductors (MOSFETs or IGBTs), capacitors, and diodes carefully. High-quality, efficient components are essential to minimize power losses. Consider factors like voltage ratings, switching speeds, and thermal management capabilities when choosing these parts.
- Efficient Power Conversion: The power electronics system is responsible for converting the DC battery voltage to the required AC voltage for the motor and managing the power flow. Design the converter/inverter to have a high power factor and low harmonic distortion. This can be achieved through proper circuit topology selection and control strategies. For instance, using a three-level inverter can reduce the number of power devices and improve efficiency. Implement advanced control techniques like pulse-width modulation (PWM) to regulate the voltage and current, ensuring optimal power transfer.
- Thermal Management and Efficiency Optimization: Efficient cooling is vital to maintain the performance and longevity of power electronics. Design a thermal management system that can handle the heat generated during operation. This might involve using heat sinks, liquid cooling, or advanced materials for thermal dissipation. Ensure that the system operates within the optimal temperature range to maximize efficiency. Regularly test and analyze the system's efficiency under various driving conditions to identify areas for improvement.
- Voltage and Current Control: Precise control of voltage and current is essential for efficient energy management. Implement feedback control systems using sensors to monitor the motor's speed, torque, and battery voltage. Adjust the inverter's output to match the motor's requirements and maintain a constant battery voltage. This control strategy ensures that the EV's performance is optimized while minimizing energy wastage.
- Protection and Fault Handling: Power electronics must be designed with robust protection mechanisms. Implement over-voltage, over-current, and short-circuit protection to safeguard the system and the battery. Develop fault-handling strategies to manage unexpected failures or malfunctions. This includes isolating faulty components and safely shutting down the system to prevent further damage.
- Testing and Simulation: Utilize advanced simulation tools to test and validate the power electronics design before physical implementation. Simulate different driving scenarios and load conditions to analyze the system's performance. This allows for the identification of potential issues and the optimization of control algorithms. Physical testing should also be conducted to verify the system's efficiency, reliability, and compliance with safety standards.
Vehicle Electrical Drain: Tips for Isolating Power to Prevent Drain
You may want to see also
Charging Systems: Implement smart charging systems for safe and efficient battery charging
Implementing smart charging systems is a critical aspect of building an electric vehicle (EV) that ensures safe and efficient battery charging. These systems are designed to optimize the charging process, protect the battery, and enhance the overall performance of the EV. Here's a detailed guide on how to approach this:
Understanding Smart Charging:
Smart charging technology is an intelligent process that goes beyond simply plugging in the vehicle. It involves a network of communication and control systems that work together to manage the charging process. The primary goal is to ensure that the EV's battery is charged optimally while considering various factors such as power availability, battery health, and user preferences. This technology is essential for maximizing the lifespan of the battery and providing a seamless charging experience.
Key Components of Smart Charging Systems:
- Charging Station Communication: Install advanced charging stations equipped with communication modules. These stations should support wireless communication protocols like Bluetooth, Wi-Fi, or cellular networks (4G/5G) to enable data exchange between the vehicle and the charging infrastructure. This communication allows for real-time monitoring and control.
- Battery Management System (BMS): Integrate a sophisticated BMS into the EV's battery pack. The BMS monitors individual cell voltages, temperatures, and overall battery health. It ensures that the charging process is tailored to the specific needs of the battery, preventing overcharging, overheating, and potential damage. The BMS also provides valuable data for smart charging algorithms.
- Power Electronics: Utilize high-efficiency power electronics to regulate the charging process. These components include inverters and converters that adjust the voltage and current to match the battery's requirements. Smart power electronics can optimize charging rates and ensure a stable and controlled environment for the battery.
Smart Charging Process:
- Charging Initiation: When the EV owner plugs in the vehicle, the smart charging system activates. It communicates with the BMS to initiate the charging process, ensuring it starts at the optimal voltage and current levels.
- Real-Time Monitoring: During charging, the system continuously monitors the battery's performance. It adjusts the charging rate based on factors like ambient temperature, battery temperature, and available power supply. This dynamic adjustment ensures efficient charging without compromising safety.
- Predictive Maintenance: Smart charging systems can predict potential issues and schedule maintenance proactively. For instance, if the battery temperature exceeds safe limits, the system can notify the user and suggest a charging pause or station relocation.
- User Preferences and Scheduling: Allow users to set preferences for charging, such as preferred charging times or specific power levels. The system can then schedule charging sessions accordingly, ensuring convenience and optimizing energy usage.
Safety Measures:
- Implement over-voltage and over-current protection to safeguard the battery and charging infrastructure.
- Use advanced algorithms to detect and prevent short circuits, ensuring the safety of the EV and the charging station.
- Regularly update the charging system's software to incorporate the latest safety features and improvements.
By integrating smart charging systems, electric vehicle manufacturers can provide a safer, more efficient, and user-friendly charging experience, contributing to the widespread adoption of electric mobility. This technology is a key enabler in the transition to sustainable transportation.
Exploring the Electric Revolution: Features and Benefits of EV Technology
You may want to see also
Vehicle Structure: Utilize lightweight, strong materials to create a robust yet lightweight vehicle frame
When designing the structure of an electric vehicle, the primary goal is to achieve a balance between strength, durability, and lightweight efficiency. This is a critical aspect of EV construction, as it directly impacts the vehicle's performance, range, and overall driving experience. The frame forms the backbone of the vehicle, providing structural integrity and ensuring the safety of the occupants.
Lightweight materials are essential to achieving the desired weight reduction without compromising strength. One of the most popular choices for EV frames is advanced composites, such as carbon fiber-reinforced polymers (CFRP). Carbon fiber is renowned for its exceptional strength-to-weight ratio, making it an ideal candidate for load-bearing components. These composites can be molded into complex shapes, allowing for innovative design possibilities and efficient use of space. For instance, the vehicle's body panels, roof, and even the floor can be constructed using these materials, reducing overall weight while maintaining structural rigidity.
Another innovative approach is the use of aluminum alloys, which have been a staple in the automotive industry for decades. Modern aluminum alloys offer excellent strength and corrosion resistance, making them suitable for both structural and aesthetic components. By utilizing aluminum for the vehicle's frame and body, engineers can achieve a lightweight yet robust structure. This material is also highly recyclable, contributing to the sustainability of the EV manufacturing process.
To further optimize the vehicle's structure, engineers can employ a technique called 'monocoque' or 'unibody' construction. This design philosophy integrates the body and chassis into a single, lightweight structure. In this approach, the body panels themselves contribute to the overall strength, reducing the need for a separate, heavy frame. Monocoque designs are prevalent in high-performance vehicles and offer excellent weight distribution and handling characteristics.
In addition to material selection, the design and layout of the vehicle's structure play a crucial role. Engineers must carefully consider the placement of batteries, motors, and other components to ensure optimal weight distribution. A well-designed structure will have a low center of gravity, enhancing stability and handling. Furthermore, the use of advanced manufacturing techniques, such as 3D printing and automated welding, allows for precise and efficient assembly, ensuring the structural integrity of the vehicle.
The Green Revolution: Why Electric Vehicles Are the Future
You may want to see also
Frequently asked questions
Building an electric vehicle (EV) involves several essential components. Firstly, you need a powerful electric motor, typically an AC or DC motor, which converts electrical energy into mechanical motion. This is coupled with a transmission system to control the speed and torque. The battery pack is a critical element, storing the energy required to power the vehicle. Lithium-ion batteries are commonly used due to their high energy density and efficiency. Additionally, an inverter is necessary to convert the direct current (DC) from the battery to alternating current (AC) for the motor. Other components include a charging system, power electronics, a cooling system, and a sophisticated control unit to manage the vehicle's performance and safety.
Selecting the appropriate electric motor depends on various factors. Consider the desired vehicle specifications, such as the desired range, top speed, and overall performance. Motors can be categorized into two main types: brushed and brushless. Brushless DC motors are more efficient and offer better performance, making them a popular choice for EVs. The power output, size, and weight of the motor should align with your vehicle's requirements. It's crucial to consider the motor's efficiency, torque, and power-to-weight ratio. Consulting with motor manufacturers and experts can provide valuable insights to ensure you choose a motor that meets your specific EV project needs.
Designing the battery pack for an EV presents several challenges. One significant concern is energy density, as high-density batteries are desirable for longer ranges. However, this can lead to safety issues, such as overheating and fire risks. Balancing energy density with safety is crucial. Another challenge is managing state-of-charge (SoC) and state-of-health (SoH) to ensure optimal performance and longevity. Battery packs require efficient cooling systems to maintain optimal temperatures, especially during charging and discharging. Additionally, designing a pack that is lightweight, compact, and cost-effective while adhering to regulatory standards is a complex task. Advanced battery management systems and careful pack design are essential to address these challenges.