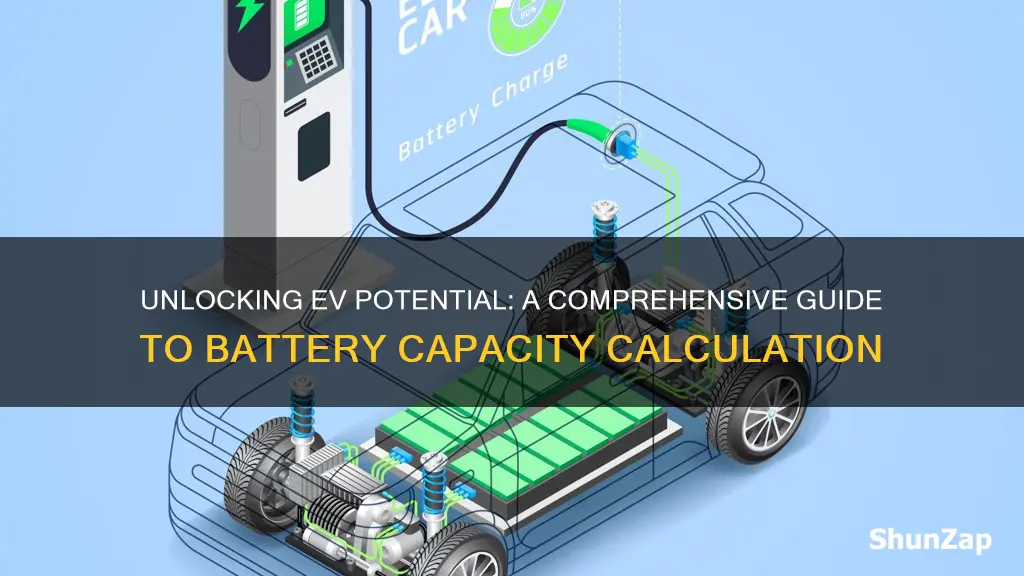
Calculating the battery capacity of an electric vehicle (EV) is a crucial step in understanding its performance and range. Battery capacity refers to the amount of energy an EV battery can store and deliver to power the vehicle's electric motor. This measurement is typically expressed in kilowatt-hours (kWh) and directly impacts the vehicle's driving range. To calculate battery capacity, engineers and technicians use various methods, including laboratory testing, where they subject the battery to controlled conditions to measure its energy output. Another approach involves analyzing the battery's performance during real-world driving cycles, providing a more accurate representation of its efficiency. Understanding battery capacity is essential for EV manufacturers and buyers alike, as it influences the vehicle's overall performance, charging requirements, and environmental impact.
What You'll Learn
- Energy Storage: Understand battery energy density and storage capacity
- Power Output: Calculate power output based on voltage and current
- Efficiency: Assess efficiency losses during charging and discharging
- Cycle Life: Determine battery lifespan through charge-discharge cycles
- Temperature Impact: Consider temperature effects on battery performance
Energy Storage: Understand battery energy density and storage capacity
Energy storage is a critical aspect of electric vehicles (EVs), as it directly impacts their range and performance. When it comes to EVs, battery energy density and storage capacity are two essential metrics that determine how efficiently a battery can store and deliver energy. Understanding these concepts is key to optimizing EV battery performance and designing efficient energy systems.
Battery energy density refers to the amount of energy that can be stored in a given volume or weight of the battery. It is typically measured in watt-hours per liter (Wh/L) or watt-hours per kilogram (Wh/kg). Higher energy density means the battery can store more energy in a smaller or lighter package, which is crucial for EVs as it directly influences their range. For instance, a battery with a higher energy density can provide more miles per charge, making it more practical for long-distance travel.
Storage capacity, on the other hand, is about the total amount of energy a battery can hold. It is often associated with the battery's voltage and the number of cells it contains. The storage capacity is measured in watt-hours (Wh) or kilowatt-hours (kWh). A larger storage capacity means the battery can store more energy, which is essential for longer driving ranges and for accommodating the varying energy demands of different EV models and driving conditions.
To calculate the battery capacity for an EV, you need to consider both energy density and storage capacity. Start by determining the battery's volume or weight, then multiply it by the energy density to get an estimate of the stored energy. For instance, if you have a battery with a volume of 0.5 liters and an energy density of 300 Wh/L, the stored energy is 150 Wh. This calculation provides a basic understanding of the battery's energy storage capability.
Additionally, the storage capacity can be calculated by multiplying the battery's voltage, current, and time. This method provides a more comprehensive view of the battery's energy storage potential. For example, if a battery has a voltage of 360V, a current of 50A, and is charged for 1 hour, the storage capacity would be 18 kWh. This calculation is particularly useful when designing EV battery systems and ensures that the battery can meet the energy demands of the vehicle.
Unlocking the Mystery: Are Hybrid Vehicles Electric?
You may want to see also
Power Output: Calculate power output based on voltage and current
To calculate the power output of an electric vehicle's battery, you need to understand the relationship between voltage, current, and power. Power output is essentially the rate at which energy is transferred or converted, and it's a crucial parameter for evaluating the performance of an EV's battery. This calculation is based on Ohm's Law and the formula for power, which is P = VI, where P is power, V is voltage, and I is current.
In the context of electric vehicles, voltage (V) is the electrical potential difference across the battery, and current (I) is the flow of electric charge through the battery. When you multiply these two values, you get the power output in watts (W). This is a fundamental concept in electrical engineering and is essential for understanding the capabilities of EV batteries.
The process begins with measuring or knowing the voltage of the battery. This can be done using a voltmeter or by referring to the manufacturer's specifications. Voltage is typically measured in volts (V). Once you have the voltage, you need to determine the current flowing through the battery. Current can be measured using an ammeter or calculated if you have the resistance of the circuit and the voltage. Current is measured in amperes (A).
After obtaining the voltage and current values, you can calculate the power output. Using the formula P = VI, you simply multiply the voltage by the current. For example, if your EV battery has a voltage of 300V and a current of 50A, the power output would be 15,000 watts or 15 kW. This calculation provides valuable insights into the battery's performance and can help in designing efficient power systems for electric vehicles.
Understanding power output is crucial for optimizing the performance of electric vehicle batteries. It allows engineers and enthusiasts to assess the efficiency of the battery-powered system and make informed decisions about power management, charging infrastructure, and overall vehicle design. By calculating power output, you can ensure that the EV's battery meets the required performance standards and provides the necessary power for the vehicle's operation.
Unveiling the Green Myth: Electric Vehicles' Environmental Impact
You may want to see also
Efficiency: Assess efficiency losses during charging and discharging
When evaluating the efficiency of an electric vehicle's battery system, it's crucial to consider the losses that occur during both charging and discharging processes. These losses can significantly impact the overall performance and range of the vehicle. Here's a detailed breakdown of how to assess these efficiency losses:
Charging Efficiency:
- During charging, several factors contribute to efficiency losses. Firstly, the charging process itself incurs power conversion losses, especially when using alternating current (AC) chargers. AC-to-direct current (DC) converters within the charger convert the AC power to the DC voltage required by the battery. These conversions can result in energy losses, typically around 5-10% depending on the charger's efficiency.
- Another critical aspect is the internal resistance of the battery. As current flows into the battery, some energy is dissipated as heat due to this resistance. Higher internal resistance leads to increased power losses during charging. This can be measured and quantified using specialized equipment that monitors current, voltage, and temperature during the charging process.
- Additionally, the temperature of the battery during charging plays a role. Charging at higher temperatures can reduce efficiency due to increased thermal expansion and internal resistance. Conversely, charging at lower temperatures might slow down the process but can be more efficient.
Discharging Efficiency:
- During discharging, the efficiency losses are primarily associated with the vehicle's electrical system and the battery's internal characteristics. As the battery powers the vehicle, electrical components like the motor, inverter, and accessories draw current. Inefficiencies in these systems can lead to power losses.
- Similar to charging, the internal resistance of the battery is a significant factor. Higher resistance results in increased power dissipation as heat during discharging. This can be measured by monitoring the voltage drop across the battery terminals and comparing it to the ideal voltage expected under load.
- Furthermore, the depth of discharge (DoD) is essential. Deep discharging the battery frequently can lead to increased internal resistance and reduced efficiency over time. It is recommended to maintain a healthy DoD range to minimize efficiency losses.
To assess overall efficiency, engineers and researchers often use specialized testing equipment that simulates real-world driving conditions. This includes varying load profiles, temperatures, and charging/discharging rates. By measuring the input power and comparing it to the actual output power, they can calculate efficiency losses and identify areas for improvement in the battery system design.
In summary, evaluating efficiency losses during charging and discharging is a complex process that requires a comprehensive understanding of the battery's internal characteristics, the vehicle's electrical system, and environmental factors. By quantifying these losses, engineers can optimize battery designs, improve charging infrastructure, and enhance the overall efficiency of electric vehicles.
Hyundai's Electric Revolution: Sales Figures Unveiled
You may want to see also
Cycle Life: Determine battery lifespan through charge-discharge cycles
The concept of cycle life is a fundamental aspect of evaluating the longevity and performance of batteries, especially in the context of electric vehicles (EVs). It refers to the number of times a battery can undergo a complete charge-discharge cycle while maintaining its capacity and performance. This metric is crucial for understanding the battery's durability and its ability to withstand repeated use over an extended period.
Cycle life testing involves subjecting a battery to multiple charge-discharge cycles, gradually reducing its capacity until it no longer meets the desired performance criteria. The process typically starts with a fully charged battery, which is then discharged to a specific level, recharged, and this cycle is repeated numerous times. Each cycle consists of two main stages: the charging phase and the discharging phase. During charging, the battery absorbs electrical energy, and during discharging, it releases this stored energy to power the vehicle.
The key to determining cycle life is to monitor and record the battery's performance at each cycle. This includes measuring the voltage, current, and temperature during both charging and discharging. By analyzing these parameters, engineers can identify any degradation in the battery's performance over time. The cycle life is then calculated by dividing the total number of successful cycles by the initial capacity of the battery. A successful cycle is one where the battery can retain a significant portion of its initial capacity after multiple iterations.
It's important to note that cycle life varies depending on various factors, including the type of battery chemistry, temperature conditions, charging rates, and the depth of discharge. For instance, lithium-ion batteries, commonly used in EVs, have a cycle life that can range from 500 to 1000 cycles or more, depending on the aforementioned factors. Manufacturers often provide cycle life estimates based on standardized testing conditions to give consumers an idea of the battery's expected lifespan.
In summary, cycle life testing is an essential method to assess the durability and performance of EV batteries. By subjecting batteries to controlled charge-discharge cycles and monitoring their behavior, engineers can predict and ensure the battery's longevity, providing valuable insights for both manufacturers and consumers in the EV market. This approach contributes to the overall reliability and sustainability of electric vehicles.
The Green Evolution: When EVs Outshine Fossil Fuels
You may want to see also
Temperature Impact: Consider temperature effects on battery performance
Temperature plays a critical role in the performance and longevity of batteries used in electric vehicles (EVs). The impact of temperature on battery capacity is a complex subject that requires careful consideration for accurate calculations. Here's an overview of how temperature affects battery performance and how to account for these effects in your calculations:
Understanding Temperature's Influence:
- Battery capacity is not constant and varies with temperature. As temperature decreases, the chemical reactions within the battery slow down, leading to a decrease in capacity. Conversely, higher temperatures can enhance reaction rates but may also accelerate degradation over time.
- The relationship between temperature and battery performance is often described by the 'temperature coefficient.' This coefficient quantifies the percentage change in capacity relative to a reference temperature, usually 25°C (77°F).
Impact on Calculations:
- When calculating battery capacity for an EV, it's essential to consider the operating temperature range. This range typically includes the lowest and highest temperatures the vehicle is expected to encounter. For example, a vehicle operating in a cold climate might experience significant capacity loss at sub-zero temperatures.
- To account for temperature effects, you can use the temperature coefficient to adjust the battery's capacity at different temperatures. This involves creating a temperature-capacity curve or table, which provides the capacity value for a given temperature. For instance, if the temperature coefficient is -0.5% per degree Celsius, the capacity at -10°C would be 5% lower than at 25°C.
Practical Considerations:
- In practice, EV manufacturers often use sophisticated battery management systems (BMS) to monitor and control temperature. These systems can adjust charging and discharging rates to optimize performance and extend battery life.
- For accurate calculations, it's crucial to have real-world data on battery performance at various temperatures. This data can be obtained through testing or by analyzing vehicle performance in different climates.
Temperature Management Strategies:
- To mitigate temperature-related performance issues, EV designers employ various strategies. These include using thermal insulation, liquid cooling systems, or advanced battery materials that have a more favorable temperature coefficient.
- Proper temperature management is essential for maintaining the efficiency and reliability of electric vehicles, especially in extreme weather conditions.
By understanding the temperature impact on battery performance, engineers can design more efficient and reliable EV battery systems, ensuring optimal capacity utilization across different environmental conditions. This knowledge is vital for accurate capacity calculations and overall EV performance optimization.
EE's Electric Revolution: US Market Dominance Unveiled
You may want to see also
Frequently asked questions
The battery capacity for electric vehicles is typically measured in ampere-hours (Ah) or kilowatt-hours (kWh). The calculation involves multiplying the battery voltage by the ampere-hour rating. For example, if you have a 12V battery with a capacity of 100Ah, the capacity in kWh is 0.1 (100Ah / 1000).
If you don't have the exact specifications, you can estimate it by measuring the battery's weight and volume. Different battery types have varying energy densities, so you can use industry-standard values for lithium-ion batteries, for instance. Online resources and EV manufacturer data can provide approximate values to help with calculations.
Yes, battery capacity directly influences the range an EV can achieve. You can estimate the range by multiplying the battery capacity (in kWh) by the vehicle's efficiency, often measured in kilometers per kWh. This calculation provides an estimate of the distance the EV can travel on a full charge.
Several factors can impact the real-world battery capacity. These include temperature, age, charging habits, and the number of charge-discharge cycles. Colder temperatures can reduce capacity, and over time, batteries may experience capacity degradation. Proper charging practices and regular maintenance can help optimize battery performance.