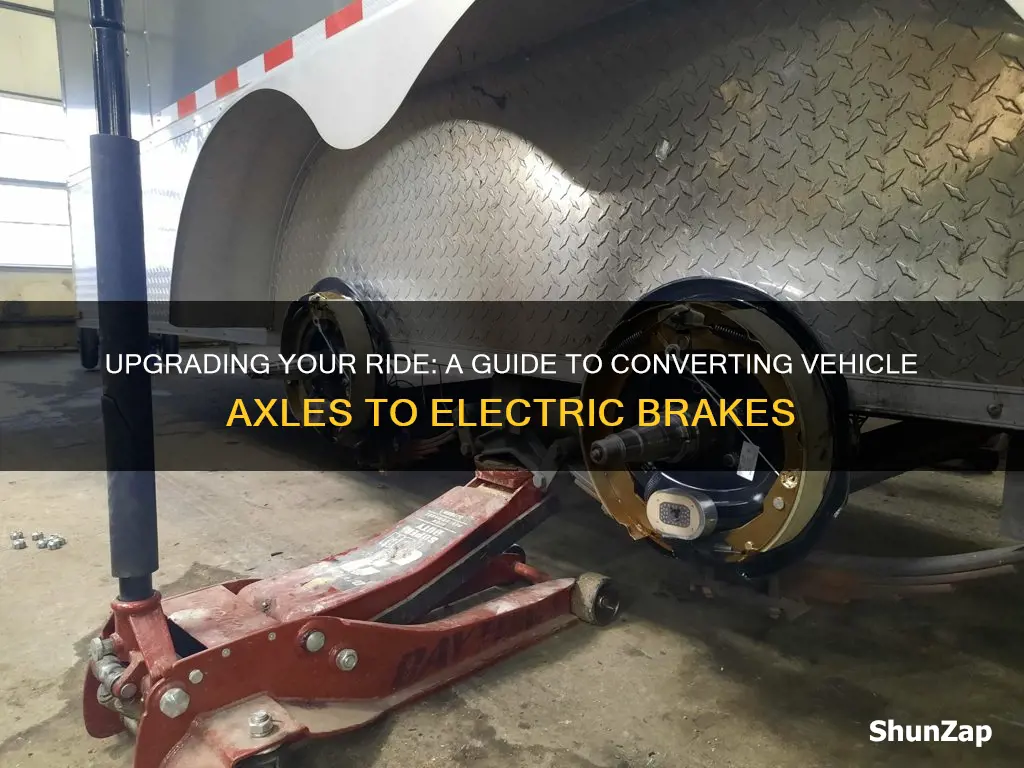
Converting a vehicle's axle to electric brakes is a popular modification for enthusiasts looking to enhance their vehicle's performance and safety. This process involves replacing the traditional hydraulic brake system with an electric one, which offers several advantages. Electric brakes provide improved braking efficiency, faster response times, and reduced maintenance compared to conventional systems. The conversion process typically includes installing an electric motor, controller, and sensors to manage the braking force. This guide will explore the step-by-step process of converting a vehicle's axle to electric brakes, covering essential components, installation techniques, and considerations for a successful conversion.
What You'll Learn
- Axle Design Considerations: Understand axle types and dimensions for electric brake compatibility
- Brake System Components: Identify and source electric brake parts like motors, sensors, and actuators
- Wiring and Connections: Plan wiring routes and ensure proper connections for brake control
- Software and Controls: Develop or adapt software for brake system management and performance
- Testing and Calibration: Rigorously test and calibrate the system for optimal braking performance
Axle Design Considerations: Understand axle types and dimensions for electric brake compatibility
When converting a vehicle's axle to accommodate electric brakes, understanding the various axle types and their dimensions is crucial for ensuring compatibility and optimal performance. The first step is to identify the axle type in your vehicle, as different designs require specific modifications. Common axle types include solid axles, independent front suspension (IFS) axles, and spindles. Solid axles are typically found in rear-wheel-drive vehicles and offer a robust and durable design. IFS axles, on the other hand, are more common in front-wheel-drive or all-wheel-drive setups, providing better traction and handling. Spindles are often used in front-wheel-drive vehicles and consist of a single steering knuckle that rotates around a fixed spindle.
The next consideration is the axle dimensions, which include the diameter, length, and bore size. These measurements are essential when selecting the appropriate electric brake assembly and mounting hardware. For instance, the axle diameter determines the size of the brake rotor and the caliper mounting points. A larger diameter often requires a more substantial brake assembly to handle the increased friction and heat dissipation. The length of the axle is critical, especially when dealing with longer vehicles or those requiring additional clearance for the brake components. Longer axles might necessitate custom-made brake assemblies or modifications to the existing brake system.
Bore size is another critical dimension, as it determines the type of wheel hub and bearing required. Different axle designs use various bore sizes, and ensuring compatibility with the electric brake system is essential. For example, some electric brake kits provide adapters to accommodate different bore sizes, allowing for a wider range of vehicle compatibility. It is also important to consider the axle's center bore, which is the hole in the center of the axle where the wheel hub is attached. This dimension affects the wheel's positioning and alignment, so precise measurements are necessary to maintain proper wheel alignment and balance.
Furthermore, the axle's material and construction play a significant role in electric brake compatibility. Solid axles, for instance, are typically made of sturdy materials like steel or aluminum, ensuring the structural integrity required for electric brake systems. The axle's surface finish and coating are also essential, as they can affect brake performance and longevity. A smooth, clean surface finish is generally preferred to ensure optimal brake pad-to-rotor contact and minimize friction-related wear.
In summary, when converting a vehicle's axle to electric brakes, a thorough understanding of axle types, dimensions, and construction is vital. Each axle type has unique characteristics, and matching these to the electric brake system's requirements ensures a successful conversion. Paying attention to axle dimensions, such as diameter, length, and bore size, allows for the proper selection of brake assemblies and mounting hardware. Additionally, considering the axle's material, surface finish, and coating contributes to the overall performance and longevity of the electric brake system.
Maximize Your EV Purchase: A Guide to Claiming Tax Credits
You may want to see also
Brake System Components: Identify and source electric brake parts like motors, sensors, and actuators
When converting a vehicle's axle to electric brakes, it's crucial to understand the various components that make up the braking system. The primary goal is to ensure that the electric brake system is not only efficient but also reliable and safe. Here's a detailed breakdown of the key components and the process of identifying and sourcing the right parts:
Motors: The heart of the electric brake system is the electric motor. These motors are typically brushless DC motors, designed to provide precise control over braking. When selecting a motor, consider factors such as torque, speed, and power output. Modern electric vehicles often use high-torque, low-speed motors to ensure effective braking. Look for motors with a high power-to-weight ratio and efficient heat dissipation to handle the demands of frequent braking.
Sensors: Sensors play a critical role in monitoring the vehicle's speed, wheel speed, and brake pad wear. Hall-effect sensors are commonly used to detect the position of the rotor and provide feedback to the controller. Additionally, speed sensors, such as optical or inductive encoders, are essential for accurate speed monitoring. These sensors ensure that the braking system responds precisely to driver input and maintains optimal performance.
Actuators: Electric brake actuators are responsible for applying the braking force to the rotors or drums. These can be in the form of hydraulic cylinders or mechanical actuators. Hydraulic actuators use pressurized fluid to exert force, while mechanical actuators often utilize a gear mechanism. When sourcing actuators, consider the force required to effectively slow down or stop the vehicle. Ensure that the actuators are compatible with the chosen motor and provide the necessary travel distance for effective braking.
Controller and Wiring: The controller is the brain of the electric brake system, managing the flow of power to the motor and receiving input from the sensors. It should be capable of handling the required current and voltage, and it must be programmed to respond to driver inputs and sensor data. Proper wiring is essential to ensure reliable communication between all components. Use high-quality wiring harnesses and connectors to minimize the risk of electrical issues.
Sourcing these components requires research and careful consideration. Start by identifying reputable suppliers or manufacturers that specialize in electric vehicle conversion parts. Online forums and communities can provide valuable insights and recommendations. When purchasing, ensure that the parts are compatible with your specific vehicle model and axle configuration. Additionally, consider the warranty and support offered by the supplier to ensure a smooth conversion process.
Unlocking EV Benefits: A Guide to Claiming Your MA Electric Vehicle Credit
You may want to see also
Wiring and Connections: Plan wiring routes and ensure proper connections for brake control
When converting a vehicle's axle to electric brakes, proper wiring and connections are crucial for the system's functionality and safety. Here's a detailed guide on planning and executing the wiring process:
Wiring Route Planning: Begin by studying the vehicle's existing brake system and identifying the path that the new electric brake wiring will take. Typically, the wiring will involve connecting the electric motor or actuator to the brake caliper or drum. Plan the route carefully, considering the length of the wiring, accessibility, and any potential obstacles or interference. Ensure that the wiring is routed away from high-heat areas, such as exhaust pipes or engine components, to prevent damage and ensure longevity. Use appropriate insulation and protective sleeves to safeguard the wiring from physical damage and environmental factors.
Component Connections:
- Brake Actuator/Motor: If you're using an electric motor or actuator, connect it to the brake caliper or drum mechanism. This connection should be secure and allow for precise control of the braking action. Ensure that the motor's output shaft is properly aligned and connected to the brake mechanism's input.
- Power Supply: Identify the vehicle's power source for the electric brakes. This could be the battery, alternator, or a dedicated power supply. Route the wiring from the power source to the brake actuator, ensuring a stable and sufficient power supply. Consider using a fuse or circuit breaker to protect the wiring and prevent overloading.
- Control Unit: If your system includes a control unit or module, connect it to the wiring harness. This unit will manage the braking action, allowing for features like speed control, regenerative braking, or anti-lock braking. Ensure proper grounding connections for the control unit to maintain signal integrity.
Grounding and Safety: Proper grounding is essential for electrical systems. Establish a solid ground connection from the control unit or motor to the vehicle's chassis. This ensures that any electrical interference or static discharge is safely dissipated. Additionally, consider implementing a safety interlock system to prevent unintended braking. This could be a mechanical or electrical switch that only activates the brakes when the vehicle is stationary or in a controlled manner.
Testing and Inspection: After completing the wiring, thoroughly test the system. Check for any loose connections, ensure proper voltage supply, and verify the functionality of the brakes. Inspect the wiring for any signs of damage or wear, especially in areas prone to vibration or heat. Address any issues promptly to ensure the system's reliability and safety.
Remember, when dealing with electrical systems, it's crucial to follow manufacturer guidelines and consult relevant resources for your specific vehicle. Proper planning and attention to wiring details will contribute to a successful electric brake conversion.
Unlocking EV Savings: A Guide to Claiming Your Subsidy
You may want to see also
Software and Controls: Develop or adapt software for brake system management and performance
The process of converting a vehicle's axle to electric brakes involves a significant software and control system overhaul. This is because the traditional hydraulic braking system needs to be replaced with an electric one, which requires sophisticated software to manage the new components and ensure optimal performance. Here's a detailed look at the software and control aspects of this conversion:
Software Development:
- Brake System Management: The primary software task is to manage the electric brake system's performance. This involves creating algorithms that control the flow of power to the electric motors, which in turn apply the brakes. The software must be able to interpret driver inputs (e.g., pedal pressure) and translate them into precise braking actions. It should also consider factors like vehicle speed, load, and road conditions to optimize braking performance.
- Sensor Integration: Electric brakes rely on various sensors for feedback. Software needs to interface with these sensors, such as speed sensors, current sensors, and temperature sensors, to gather real-time data. This data is crucial for monitoring the system's performance, diagnosing potential issues, and making adjustments to ensure safe and efficient braking.
- CAN Bus Integration: Modern vehicles use Controller Area Network (CAN) buses to communicate between different electronic control units (ECUs). The software must be designed to integrate seamlessly with the vehicle's CAN bus, allowing for communication with other systems like the engine control unit, ABS module, and driver assistance systems. This integration ensures that the electric brakes work harmoniously with the entire vehicle's electronics.
Control Strategies:
- Proportional-Integral-Derivative (PID) Control: This is a common control strategy used in brake systems. The software can employ PID controllers to regulate the electric motors' power output, ensuring smooth and precise braking. PID control takes into account the error between the desired brake pressure and the actual pressure, making real-time adjustments to maintain stability.
- Anti-lock Braking System (ABS) Adaptation: Converting to electric brakes often requires adapting the ABS system. The software must be programmed to manage the electric motors' response during emergency braking situations, preventing wheel lockup and maintaining control. This involves complex algorithms that consider vehicle dynamics and driver input.
- Regenerative Braking: Electric vehicles often utilize regenerative braking, where some of the energy from braking is captured and reused. The software should be capable of optimizing this process, managing the flow of energy back to the vehicle's power supply while ensuring the brakes remain effective.
Testing and Calibration:
After developing the software, extensive testing and calibration are necessary. This includes bench testing the software algorithms, simulating various driving conditions, and fine-tuning the control parameters. Calibration ensures that the electric brakes respond predictably and safely, meeting or exceeding the performance of the original hydraulic system.
In summary, converting a vehicle's axle to electric brakes requires a comprehensive software development approach, focusing on brake system management, sensor integration, and control strategies. The software must be designed to handle the unique challenges of electric braking while ensuring seamless integration with the vehicle's existing electronics. Thorough testing and calibration are essential to guarantee the safety and performance of the converted system.
Green Revolution: A Guide to Fleet Conversion to Electric Vehicles
You may want to see also
Testing and Calibration: Rigorously test and calibrate the system for optimal braking performance
When converting a vehicle's axle to electric brakes, thorough testing and calibration are essential to ensure optimal performance and safety. This process involves a series of steps to fine-tune the system, ensuring it functions as intended and meets the required standards. Here's a detailed guide on how to approach this critical phase:
Initial Testing: Begin by conducting a comprehensive test of the electric brake system. This should include both static and dynamic tests. Static testing involves measuring the brake's performance under no-load conditions, checking for proper engagement and release, and verifying the functionality of all components. Dynamic testing, on the other hand, simulates real-world driving conditions. This can be done on a test track or using a dynamometer to apply varying loads and speeds, allowing for the evaluation of the system's response, including brake torque, deceleration, and heat dissipation.
Brake Caliper and Rotor Inspection: During the testing phase, carefully inspect the brake calipers and rotors. Ensure that the calipers are properly aligned and that the rotors are balanced and free of defects. Any signs of warping, excessive wear, or damage should be noted and addressed before proceeding with calibration.
Calibration Process: Calibration is a critical step to ensure the system's accuracy and performance. This process involves adjusting various parameters to optimize braking efficiency. Start by setting the brake pedal feel, which determines the initial pressure required to activate the brakes. Fine-tune this setting to provide a smooth and progressive braking sensation. Next, calibrate the brake bias, which refers to the distribution of braking force between the front and rear wheels. This adjustment is crucial for maintaining stability and control during braking. Additionally, calibrate the braking distance, which is the distance the vehicle travels from the point of applying the brakes until it comes to a complete stop. This setting is vital for ensuring the vehicle's safety and performance.
Performance Evaluation: After calibration, rigorously evaluate the system's performance. This includes testing the brake's response time, fade resistance, and overall braking force. Use instruments like dynamometers and data loggers to record and analyze the system's behavior under different conditions. Compare the results against industry standards and the vehicle's original specifications to ensure the conversion meets or exceeds the required performance criteria.
Final Adjustments and Validation: Based on the test results, make any necessary final adjustments to the calibration settings. This may involve retuning the brake system to optimize performance and address any identified issues. Once all adjustments are made, conduct a final validation test to ensure the system functions flawlessly. This final test should cover various scenarios, including emergency stops, sustained braking, and different road conditions, to verify the reliability and safety of the electric brake conversion.
Unlocking Savings: A Guide to Colorado's EV Tax Credit
You may want to see also
Frequently asked questions
Converting a vehicle's axle to electric brakes involves replacing the traditional mechanical braking system with an electric one. This process typically includes installing an electric motor, a speed sensor, and a control unit. The motor is connected to the brake caliper, and when activated, it applies the brakes by extending a piston or using a similar mechanism.
Electric brakes offer several advantages. They provide more precise braking control, especially in heavy-duty vehicles, as the braking force can be adjusted based on the load. Electric brakes are also quieter, more responsive, and can improve the overall efficiency of the vehicle.
Yes, heavy-duty trucks, buses, and some off-road vehicles are popular choices for electric brake conversions. These vehicles often require more robust braking systems to handle increased weight and torque. However, the conversion process can be adapted for various vehicle types.
Selecting the appropriate electric brake system depends on factors like vehicle weight, desired braking performance, and the specific requirements of your vehicle. It's essential to consider the motor's power output, the type of brake caliper used, and the compatibility of the control unit with your vehicle's existing systems. Consulting with experts or referring to manufacturer guidelines is recommended.
One of the main challenges is ensuring proper integration with the vehicle's existing braking system. The conversion may require modifications to the vehicle's wiring and control systems. Additionally, finding compatible components and ensuring the system's reliability and safety is crucial. It is advisable to seek professional assistance or follow detailed guides specific to your vehicle model.