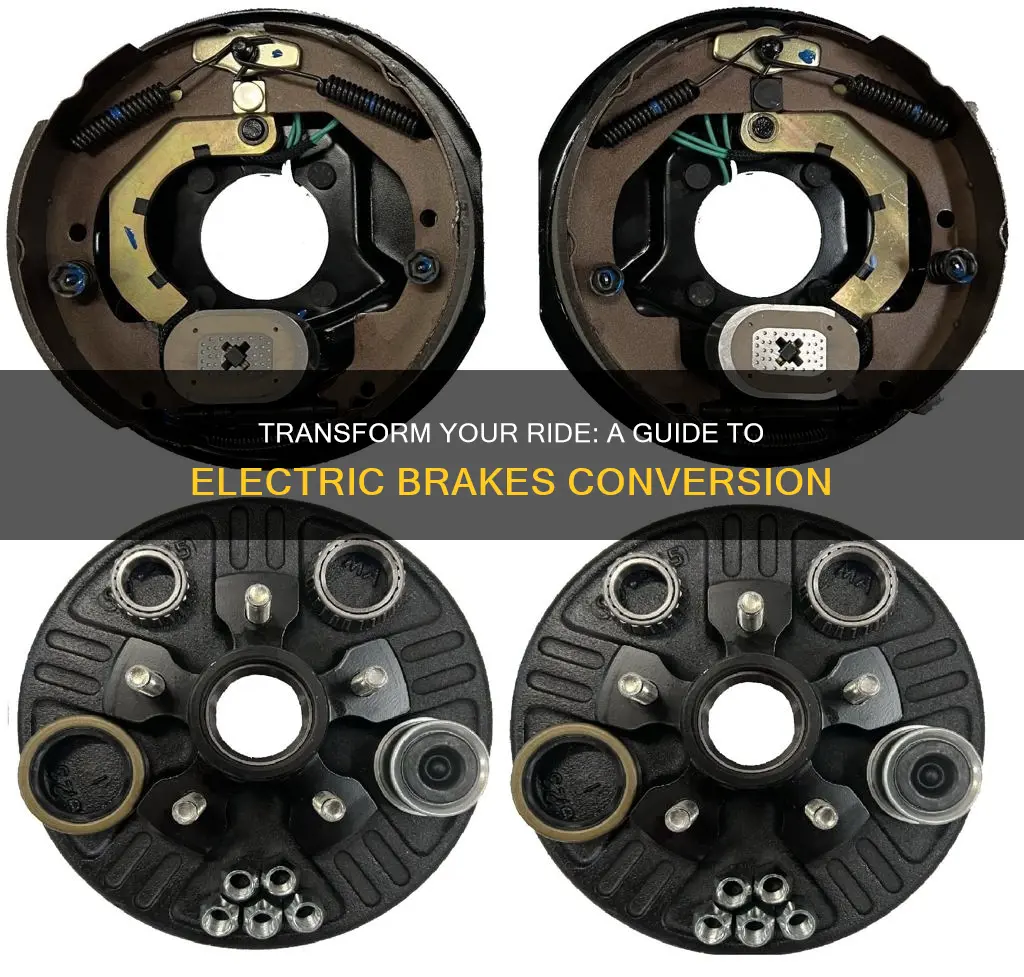
Converting traditional vehicle brakes to electric systems is an innovative approach to enhancing vehicle performance and efficiency. This process involves replacing the mechanical components of the braking system with electric actuators and sensors, allowing for precise control and improved braking power. The conversion process requires careful planning and technical expertise to ensure compatibility and safety. By understanding the mechanics of both traditional and electric braking systems, technicians can effectively transform a vehicle's braking capabilities, offering a smoother, more responsive driving experience while contributing to overall vehicle safety and environmental sustainability.
What You'll Learn
- Electric Motor Selection: Choose the right motor for your brake system's power and torque needs
- Brake Caliper Conversion: Adapt electric calipers to replace traditional hydraulic brakes
- Power Electronics: Design efficient inverters and converters for brake motor control
- Battery Integration: Optimize battery placement and charging systems for electric brake systems
- Brake Pad Materials: Develop new materials for electric brake pads with improved friction and longevity
Electric Motor Selection: Choose the right motor for your brake system's power and torque needs
When converting a vehicle's braking system to electric, the selection of the right electric motor is a critical aspect that can significantly impact the performance and efficiency of the system. The motor's power and torque capabilities must be carefully considered to ensure it can handle the demands of the braking application. Here's a detailed guide on how to choose the appropriate electric motor for your brake system:
Understanding Power and Torque Requirements: Begin by evaluating the braking power and torque needs of your vehicle. This involves analyzing the vehicle's weight, speed, and the desired braking performance. Heavier vehicles or those requiring rapid deceleration will demand higher power and torque from the motor. For instance, a sports car might need a more powerful motor to achieve quick stops, while a light-duty vehicle may require a smaller, more energy-efficient motor.
Motor Power Output: Electric motors are typically rated in terms of power output, measured in watts (W) or horsepower (hp). The power rating should match or exceed the braking power required by the vehicle. For example, if your vehicle needs a braking force of 500 N-m (Newton-meters), you should select a motor with a power output of at least 500 W or more, considering efficiency losses. Higher power motors can provide faster response times and improved braking performance.
Torque Considerations: Torque is another crucial factor, especially for electric vehicles. The motor's torque output should be sufficient to overcome the rolling resistance and provide the necessary braking force. A higher torque motor can deliver better acceleration and deceleration, ensuring smooth and responsive braking. For instance, a motor with a torque rating of 100-150 Nm per kilogram of vehicle weight can offer excellent performance.
Motor Size and Weight: The physical dimensions and weight of the motor are essential considerations. A larger motor may provide more power but will also add significant weight to the vehicle, affecting its overall performance. Opt for a motor that strikes a balance between power output and size/weight to ensure the vehicle's handling and efficiency remain optimal.
Efficiency and Speed: Consider the motor's efficiency and its ability to operate at various speeds. Different braking scenarios may require varying motor speeds. For instance, during gentle deceleration, a lower motor speed might be sufficient, while aggressive braking might demand higher motor speeds. Choose a motor with an efficient speed range that covers the expected braking conditions.
Controller and Inverter: The electric motor's performance is also influenced by the controller and inverter used. These components regulate the motor's speed and torque, ensuring it operates within the desired parameters. Select a controller and inverter that can handle the motor's power and torque requirements, providing precise control over the braking system.
In summary, the electric motor selection process involves a careful assessment of power, torque, size, and efficiency to match the vehicle's braking needs. By choosing the right motor, you can ensure a smooth, responsive, and efficient electric braking system, contributing to a safer and more enjoyable driving experience. This selection process is a key step in the successful conversion of traditional braking systems to electric power.
Unleash Savings: Your Guide to Federal EV Credit Claims
You may want to see also
Brake Caliper Conversion: Adapt electric calipers to replace traditional hydraulic brakes
The process of converting traditional hydraulic brakes to electric calipers is an exciting upgrade for vehicle owners seeking improved performance and efficiency. This conversion involves replacing the conventional brake calipers with electric-powered alternatives, offering a more sustainable and responsive braking system. Here's a step-by-step guide to achieving this transformation:
Understanding the Components: Begin by familiarizing yourself with the existing hydraulic brake system. The traditional calipers use hydraulic fluid to transmit force from the brake pedal to the pistons, which then clamp down on the brake rotors. The goal is to replicate this action with electric calipers, which operate through electromagnetic forces.
Choosing the Right Electric Calipers: Select electric calipers that are compatible with your vehicle's make and model. These calipers typically feature a motor and a solenoid valve, which work together to apply braking force. Look for calipers with adjustable braking power and quick-release mechanisms for easy installation.
Disassembly and Preparation: Carefully remove the old hydraulic calipers, ensuring you have all the necessary components, including the pistons, seals, and brackets. Clean and inspect the brake rotors to ensure they are in good condition. Prepare the mounting points for the new electric calipers, ensuring they are securely attached to the vehicle's frame.
Installation of Electric Calipers: Mount the electric calipers onto the prepared rotor mounts. Connect the motor and solenoid valve to the vehicle's power source and wiring harness. Ensure all connections are secure and aligned with the caliper's mounting bolts. Test the motor's functionality and adjust the braking force using the provided controls.
Caliper Adjustment and Testing: Fine-tune the electric calipers by adjusting the piston travel and brake pad thickness. This ensures optimal contact with the rotors for efficient braking. Test the system by applying pressure to the brake pedal and monitoring the caliper's response. Make any necessary adjustments to achieve the desired braking feel and performance.
Converting to electric calipers offers improved control, reduced maintenance, and a more eco-friendly braking system. This conversion process requires careful planning and technical knowledge, but the end result is a powerful and efficient braking setup. Remember to consult professional mechanics or follow manufacturer guidelines for a successful brake caliper conversion.
Unlocking EV Savings: A Guide to Claiming Your Subsidy
You may want to see also
Power Electronics: Design efficient inverters and converters for brake motor control
The process of converting traditional vehicle brakes to electric systems involves the integration of power electronics, particularly inverters and converters, to control the braking mechanism and motor. This conversion aims to enhance efficiency, improve safety, and provide regenerative braking capabilities. Here's a detailed guide on designing efficient inverters and converters for this application:
Understanding the System: Begin by comprehending the vehicle's braking system and the motor's specifications. The brake motor control system will typically consist of an electric motor, a speed sensor, and a power electronics module. The inverter's role is to convert the DC (direct current) power from the battery to AC (alternating current) to drive the motor, and it also controls the motor's speed and torque. The converter, on the other hand, manages the power flow between the motor and the battery during regenerative braking.
Inverter Design: Efficient inverter design is crucial for optimal motor performance. The inverter should be capable of handling the required power and voltage levels. One common approach is to use a three-phase inverter, which provides balanced power distribution and efficient motor control. The inverter's switching frequency and pulse-width modulation (PWM) techniques should be carefully selected to ensure smooth motor operation and minimize energy losses. Advanced inverter designs might include vector control algorithms to precisely regulate the motor's speed and torque.
Converter Topologies: The converter's primary function is to manage the energy flow during regenerative braking. Several converter topologies can be considered, such as the buck-boost converter, which provides voltage regulation and efficient power transfer. A three-phase bridge rectifier can also be employed to convert the AC output of the motor back to DC for recharging the battery. The choice of topology depends on the specific requirements of the vehicle, including voltage levels, power ratings, and desired efficiency.
Power Electronics Selection: Choosing the right power electronics components is essential. High-efficiency transistors or insulated-gate bipolar transistors (IGBTs) are commonly used due to their fast switching speeds and high voltage handling capabilities. The selection should consider factors like the operating temperature, switching frequency, and the need for high-voltage insulation. Additionally, the use of passive components like inductors and capacitors should be optimized to minimize energy losses and ensure efficient power conversion.
Thermal Management: Efficient heat dissipation is critical in power electronics, especially in high-power applications. Implement a robust thermal management system to prevent overheating, which can degrade performance and reduce the lifespan of the components. This might involve using heat sinks, cooling fans, or even liquid cooling systems, depending on the specific design and power density requirements.
By focusing on these design aspects, engineers can create efficient and reliable inverters and converters for electric brake motor control, contributing to improved vehicle performance and safety. This conversion technology is a significant step towards more sustainable and environmentally friendly transportation solutions.
Unlocking EV Benefits: A Guide to Claiming Your MA Electric Vehicle Credit
You may want to see also
Battery Integration: Optimize battery placement and charging systems for electric brake systems
The integration of electric brake systems into vehicles requires careful consideration of battery placement and charging systems to ensure optimal performance and efficiency. Here's a detailed guide on optimizing these aspects:
Battery Placement:
- Space Optimization: Electric brake systems demand a significant amount of power, so battery placement is crucial. The ideal location is often near the vehicle's center of gravity, ensuring a low-slung design that improves stability and reduces the risk of damage during collisions. Consider mounting batteries in the floor pan or beneath the vehicle's body to maintain a low center of gravity.
- Cooling and Ventilation: Efficient cooling is essential for battery performance and longevity. Design a cooling system that utilizes air or liquid cooling to maintain optimal temperatures. Proper ventilation is key, especially if the batteries are located in confined spaces. Ensure that the cooling system integrates seamlessly with the vehicle's overall design.
- Weight Distribution: The weight of the batteries can impact the vehicle's handling and performance. Aim for a balanced weight distribution by strategically placing the batteries. This might involve using lightweight materials or designing a modular system that allows for easy battery removal and replacement.
Charging Systems:
- On-Board Charger: Integrate a high-efficiency on-board charger that can rapidly recharge the batteries. This charger should be designed to handle the specific voltage and current requirements of the electric brake system. Consider using smart charging technology that optimizes charging based on vehicle usage and environmental factors.
- Regenerative Braking: Implement regenerative braking technology to capture and store energy that would otherwise be lost during braking. This system converts kinetic energy back into electrical energy, extending the range of the vehicle and improving overall efficiency. Ensure the regenerative braking system is seamlessly integrated with the electric brake actuators.
- Charging Port Accessibility: Position the charging port in a convenient and easily accessible location. This might be on the vehicle's exterior or within a dedicated charging bay. Ensure the charging port is weather-resistant and designed to prevent water ingress during normal driving conditions.
Optimization Techniques:
- Energy Management: Develop an energy management system that monitors and controls power distribution. This system should prioritize power allocation to critical components, such as the electric brake actuators, while optimizing energy usage. Consider using advanced algorithms to predict and manage energy consumption.
- Wireless Charging: Explore the possibility of implementing wireless charging technology for added convenience. Wireless charging pads or coils can be integrated into the vehicle's design, allowing for efficient and contactless charging. This technology can enhance the overall user experience and provide a unique selling point for electric vehicles.
- Battery Monitoring: Install advanced battery monitoring systems that provide real-time data on battery health, temperature, and state of charge. This data can be used to optimize charging schedules, predict maintenance needs, and ensure the longevity of the battery pack.
Maximize Your EV Purchase: A Guide to Claiming Tax Credits
You may want to see also
Brake Pad Materials: Develop new materials for electric brake pads with improved friction and longevity
The development of new materials for electric brake pads is a crucial aspect of converting traditional vehicle brakes to electric systems. The primary goal is to enhance friction performance and ensure the longevity of these brake pads, which are essential for safe and efficient electric vehicle (EV) braking. Here's an overview of the process and key considerations:
Material Selection: The first step involves choosing the right materials for brake pad construction. Traditional brake pads often use a combination of friction materials like steel fibers, graphite, and various types of rubber or plastics. For electric vehicles, the focus should be on materials that offer superior friction characteristics while also being compatible with the unique demands of electric braking. Advanced composite materials, such as carbon-carbon composites or specialized ceramic compounds, can be considered. These materials provide excellent heat resistance and friction performance, ensuring that the brake pads can handle the high-energy braking required by electric motors.
Friction and Wear Properties: One of the critical challenges in electric brake pad development is achieving the right balance between friction and wear. The friction material should provide a consistent and predictable braking force, allowing for precise control during deceleration. Researchers and engineers can experiment with different friction formulas and additives to optimize this property. Additionally, minimizing wear is essential to extend the lifespan of the brake pads. This can be achieved by using advanced bonding techniques, optimizing fiber orientation in composite materials, or incorporating wear-resistant coatings.
Heat Management: Electric vehicles generate significant heat during braking, which can affect the performance and longevity of the brake pads. New materials should be designed to withstand high temperatures without compromising friction or structural integrity. This might involve using heat-resistant ceramics or advanced carbon-based compounds that can dissipate heat more efficiently. Proper heat management is crucial to prevent brake fade and ensure consistent performance over extended periods.
Longevity and Durability: Electric brake pads must be engineered to withstand the unique demands of EV operation, including frequent and rapid braking. Developing materials with enhanced durability can reduce wear and tear, ensuring that the brake pads maintain their performance over thousands of braking cycles. This could involve incorporating advanced bonding agents, reinforcing materials with high-strength fibers, or implementing surface treatments to enhance wear resistance.
Testing and Validation: Once the new brake pad materials are developed, extensive testing is required. This includes laboratory simulations to assess friction, wear, and heat resistance, as well as real-world testing on electric vehicles. Validation ensures that the materials meet the required performance standards and can withstand the challenges of electric braking.
Green Revolution: A Guide to Fleet Conversion to Electric Vehicles
You may want to see also
Frequently asked questions
Electric brakes offer several advantages over traditional hydraulic systems. They provide improved braking performance, including shorter stopping distances and better heat dissipation, which can enhance safety and driving experience. Additionally, electric brakes are more energy-efficient, as they can be regenerative, converting kinetic energy back into electrical energy, and they eliminate the need for a separate master cylinder, reducing weight and complexity.
Yes, it is possible to retrofit an existing brake system with electric components. This process typically involves replacing the hydraulic master cylinder with an electric brake controller, which acts as the brain of the system. The controller receives input from the brake pedal and sends the appropriate signal to the electric motors, which then engage the brakes. This conversion can be done on most vehicles, but it's essential to consult a professional to ensure compatibility and proper installation.
Selecting the appropriate electric brake system depends on various factors, including your vehicle's make and model, desired braking performance, and budget. Consider the system's power output, which is measured in watts or horsepower, and ensure it matches or exceeds your vehicle's braking requirements. Also, look for features like regenerative braking, adjustable braking force, and compatibility with your vehicle's electrical system. Researching and comparing different brands and models will help you make an informed decision.
Yes, there might be legal implications to consider when modifying your vehicle's braking system. Different regions have specific regulations regarding vehicle modifications, especially those affecting safety-critical systems like brakes. It's crucial to check local laws and obtain any necessary approvals or certifications. Additionally, ensure that the electric brake system you choose complies with industry standards and is installed by qualified professionals to maintain legal compliance and vehicle reliability.