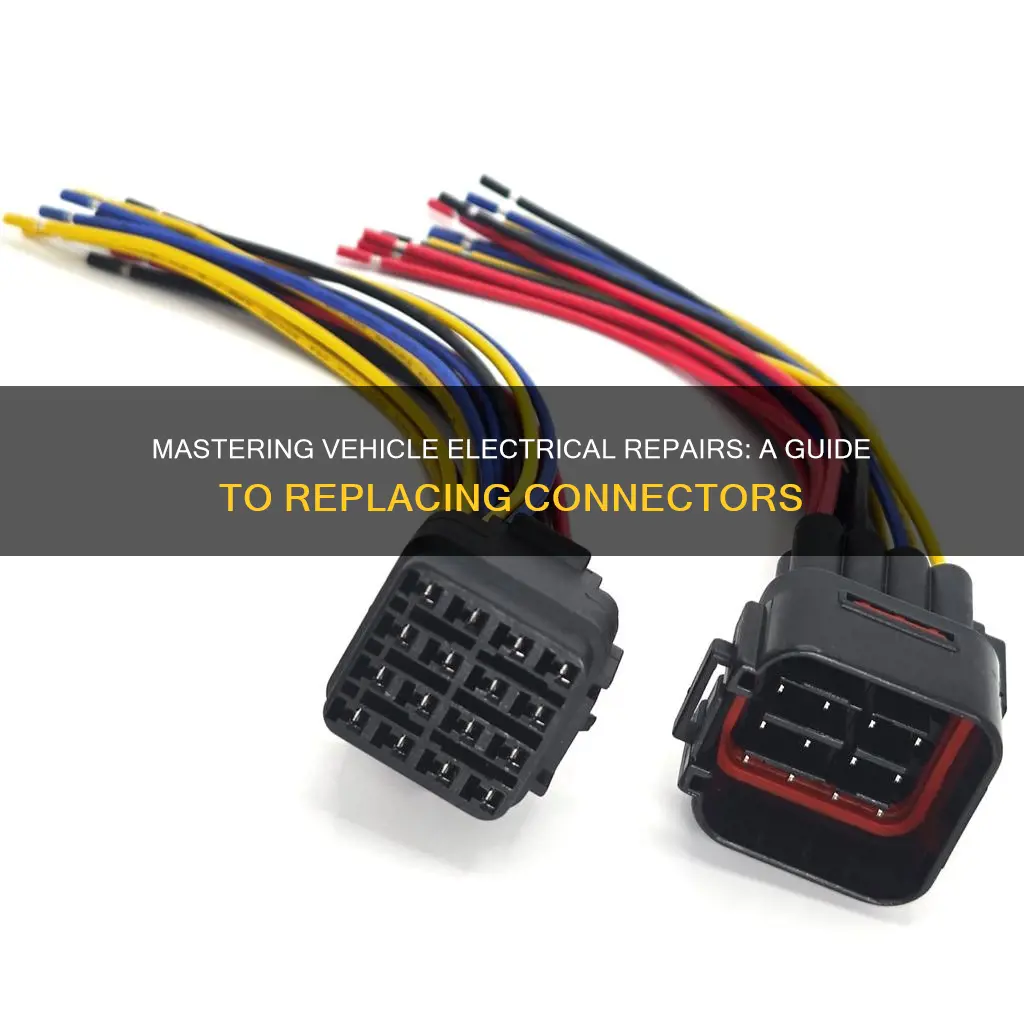
Replacing vehicle electrical connectors is a crucial task for maintaining your car's performance and safety. These connectors, often found in various systems like the engine, lights, and sensors, can wear out over time due to exposure to heat, moisture, and vibration. This guide will provide a step-by-step process to replace these connectors, ensuring you have the necessary tools and knowledge to complete the task safely and effectively. By following these instructions, you can ensure your vehicle's electrical system remains reliable and efficient.
What You'll Learn
- Preparation: Gather tools, understand wiring diagram, and ensure safety precautions
- Diagnosis: Identify faulty connector, check for corrosion, and test continuity
- Disassembly: Carefully remove old connector, clean contacts, and label wires
- Installation: Route new connector, secure it, and reconnect wires following diagram
- Testing: Verify functionality, check for loose connections, and ensure proper operation
Preparation: Gather tools, understand wiring diagram, and ensure safety precautions
Before you begin the process of replacing vehicle electrical connectors, it's crucial to prepare and ensure you have the necessary tools and knowledge to complete the task safely and effectively. Here's a step-by-step guide to help you get ready:
Gather the Right Tools: Replacing electrical connectors requires specific tools to avoid damage. Start by collecting a set of tools that includes a screwdriver set (both flat and Phillips head), a wire brush or cleaning tool, a pair of pliers, and a multimeter. Additionally, you might need a soldering iron and solder if the connector requires soldering. Ensure you have the appropriate tools for the type of connector you're dealing with.
Study the Wiring Diagram: Understanding the vehicle's wiring diagram is essential. Obtain a diagram specific to your vehicle's make and model. This diagram will illustrate the various electrical systems and the connections between them. Pay close attention to the location of the connector you need to replace and identify the wires connected to it. Knowing the wiring arrangement will help you avoid any potential issues during the replacement process.
Safety First: Electrical work can be hazardous, so prioritizing safety is paramount. Ensure the vehicle's engine is turned off and the battery is disconnected to prevent any accidental electrical discharges. Wear safety gear, such as gloves and eye protection, to safeguard yourself from potential hazards. Work in a well-ventilated area, and if possible, perform the replacement in a controlled environment to minimize risks.
Prepare the Work Area: Set up your work area to be organized and well-lit. Lay out all the necessary tools and components to have them within reach. Ensure you have a stable work surface, and consider using a lift or jack to access the connector if it's located beneath the vehicle. Proper preparation will make the replacement process smoother and more efficient.
Understand the Connector Type: Different vehicle connectors have unique designs and requirements. Familiarize yourself with the specific type of connector you're replacing. This knowledge will help you identify the correct replacement part and ensure a proper fit. Check the manufacturer's specifications or consult online resources to gather information about the connector's design, pinout, and any special considerations for installation.
By following these preparation steps, you'll be well-equipped to tackle the replacement of vehicle electrical connectors. Taking the time to gather the right tools, study the wiring diagram, and prioritizing safety will contribute to a successful and safe repair process.
Mastering Electrical Connections: A Guide to Disconnecting Vehicle Connectors
You may want to see also
Diagnosis: Identify faulty connector, check for corrosion, and test continuity
When dealing with vehicle electrical issues, identifying and replacing faulty connectors is a crucial step in the repair process. Here's a detailed guide on how to diagnose and address these problems:
Identifying the Faulty Connector: Start by visually inspecting the electrical connectors in your vehicle. Look for any signs of damage, such as melted plastic, burnt marks, or visible corrosion. Often, faulty connectors can be identified by their appearance. Check the wiring harnesses and fuses for any disconnections or damaged insulation. If you notice any issues, it's essential to isolate the problem to a specific connector or wiring section.
Checking for Corrosion: Corrosion is a common issue with electrical connectors, especially in older vehicles or those exposed to harsh weather conditions. Use a bright flashlight to inspect the connectors for any white or green powdery substances, which indicate corrosion. Carefully clean the affected areas using a small brush or a cotton swab dipped in isopropyl alcohol. Ensure you remove any corrosion to restore proper contact.
Testing Continuity: To determine if a connector is faulty, you can perform a continuity test. This test checks if the electrical path is uninterrupted between the connector's terminals. You'll need a multimeter for this. Set the multimeter to the ohms setting and touch the probes to the connector's terminals. A low resistance reading (close to zero ohms) indicates a good connection. If the reading is infinite (no continuity), it suggests a broken wire or a faulty connector. Repeat this test for all relevant connectors to ensure a comprehensive diagnosis.
Additionally, you can use a digital multimeter to measure voltage at the connector to ensure it matches the expected value for the specific circuit. This step helps identify if the issue is related to power supply or ground connections. Remember, proper diagnosis is key to successful repairs, and these steps will help you pinpoint the faulty connector(s) in your vehicle's electrical system.
Electric Vehicle Decision: Factors to Consider for Your Next Car
You may want to see also
Disassembly: Carefully remove old connector, clean contacts, and label wires
Disassembly is a crucial step in the process of replacing vehicle electrical connectors, ensuring a smooth and efficient repair. When tackling this task, it's essential to approach it with precision and care to avoid any potential issues. Here's a detailed guide on how to carefully remove the old connector, clean the contacts, and label the wires:
Removing the Old Connector: Start by locating the connector you want to replace. It is typically found along the wiring harness, often near the engine bay or the dashboard. Use the appropriate tools for prying, such as a flathead screwdriver or a specialized connector removal tool, to gently pry open the connector housing. Be cautious not to force it, as excessive pressure might damage the connector or surrounding components. Once the housing is open, carefully extract the old connector by pulling it straight up and away from the wiring harness. Take note of the orientation of the connector to ensure proper reinstallation.
Cleaning the Contacts: After removing the old connector, inspect the contacts inside. Over time, these contacts can accumulate dirt, corrosion, or oxidation, leading to poor electrical connections. Use a soft-bristled toothbrush or a small brush specifically designed for electronics to gently clean the contacts. You can also use isopropyl alcohol or a specialized contact cleaner to remove any stubborn grime. Ensure that you wipe the contacts dry with a lint-free cloth to remove any moisture. This step is vital to guarantee a reliable connection for the new connector.
Labeling the Wires: Proper labeling is essential to avoid confusion during the reassembly process. Take the time to label each wire with its corresponding function or location. You can use electrical tape, wire markers, or even a permanent marker to create clear and durable labels. Write down the wire colors or their respective functions on a piece of paper for easy reference. This step will make the reinstallation process much simpler and reduce the risk of incorrect wiring.
By following these steps, you'll ensure that the disassembly process is thorough and organized. Remember, taking the time to clean and label the wires can prevent potential issues during the repair, making the overall process more efficient and less prone to errors.
Boosting EV Adoption: Strategies for Expanding Charging Network Infrastructure
You may want to see also
Installation: Route new connector, secure it, and reconnect wires following diagram
When replacing a vehicle's electrical connectors, the installation process involves several steps to ensure a secure and functional connection. Begin by carefully routing the new connector through the designated path, ensuring it aligns with the original connector's position. This step requires patience and precision to avoid any damage to the vehicle's interior components. Once the connector is in place, it's crucial to secure it firmly. You can use specialized clips or brackets designed for this purpose, ensuring the connector remains stable and doesn't move or vibrate during operation. This security measure is vital to prevent potential disconnections and maintain the integrity of the electrical system.
After securing the connector, the next step is to reconnect the wires. Refer to the provided diagram or wiring harness diagram for your specific vehicle model. Carefully match each wire to its corresponding terminal on the new connector. Pay close attention to the color-coding or markings on the wires and terminals to ensure correct placement. Strip the insulation from the wire ends and insert them into the appropriate holes or slots on the connector, ensuring a snug fit. Use a small amount of electrical tape or heat-shrink tubing to secure the wires in place, providing additional insulation and preventing accidental disconnection.
When reconnecting the wires, it's essential to follow the diagram meticulously. Each wire should be connected to the correct terminal, and the polarity must be maintained. Incorrect wiring can lead to electrical issues and potential safety hazards. Take your time to double-check the connections, ensuring that all wires are securely attached and there are no loose ends. Once all wires are reconnected, double-check the diagram to confirm that the wiring matches the original setup.
Securing the new connector in place is the final step. Ensure that all mounting clips or screws are tightened to hold the connector firmly. This step guarantees that the connector will remain in position even under varying driving conditions. With the connector installed and wires reconnected, your vehicle's electrical system should now function as intended. Always test the system after installation to ensure all components are working correctly.
Revolutionizing Design: A Guide to Crafting the Future of Electric Vehicles
You may want to see also
Testing: Verify functionality, check for loose connections, and ensure proper operation
When replacing vehicle electrical connectors, thorough testing is essential to ensure the system's reliability and safety. Here's a step-by-step guide to verifying functionality, checking for loose connections, and ensuring proper operation:
- Verify Functionality: After replacing the connectors, it's crucial to test each circuit to confirm that it functions as intended. This involves using a multimeter or an ohmmeter to measure resistance and continuity. Start by identifying the specific circuits related to the replaced connectors. For example, if you replaced the ignition switch connectors, test the circuits responsible for starting the engine, lighting, and accessory functions. Connect the multimeter probes to the appropriate test points and check for the expected voltage or current. Compare the readings with the vehicle's manual or a technical reference to ensure they fall within the normal range. If any circuit doesn't meet the expected criteria, further investigation is required to identify the cause of the malfunction.
- Check for Loose Connections: Proper connection is vital for the reliable operation of electrical systems. Inspect all connectors and wiring harnesses for any signs of looseness or damage. Start with the newly installed connectors and ensure they are securely attached to the corresponding terminals. Gently wiggle the connectors to check for any play or movement. Tighten any loose connections using the appropriate tools, ensuring they are not overtightened to avoid damage. Also, inspect the wiring harnesses for any frayed or damaged insulation, as this can lead to loose connections over time.
- Ensure Proper Operation: Once the connections are secure, it's time to test the overall system operation. Start the vehicle and monitor all critical functions. This includes checking the engine performance, lighting, indicators, and any other accessories powered by the affected circuits. Pay close attention to any warning lights or error messages that may appear on the dashboard. If everything functions as expected, the replacement was successful. However, if any issues arise, such as flickering lights or erratic behavior, it indicates a potential problem with the new connectors or wiring. In such cases, carefully inspect the connections again and consider consulting a professional mechanic for further diagnosis.
- Final Inspection: After testing, perform a final visual inspection of all connectors and wiring. Look for any signs of corrosion, melted insulation, or damaged components. Ensure that no wires are chafed against moving parts or exposed to excessive heat. Clean any corrosion from the connectors using a suitable cleaner and ensure that all connections are free of debris.
Remember, proper testing and inspection are critical to ensuring the longevity and safety of your vehicle's electrical system. If you're unsure about any step, it's always best to consult a qualified mechanic or refer to the vehicle's manufacturer guidelines.
Boosting Electric Vehicle Range: Tips for Longer, Stress-Free Drives
You may want to see also
Frequently asked questions
Replacing electrical connectors typically involves a few essential tools. You will need a set of screwdrivers, especially a flathead and a Phillips head, to remove any screws holding the connector in place. A pair of pliers or a wire cutter/stripper will be useful for handling wires and ensuring clean cuts. Additionally, having a small flashlight can help with visibility in tight spaces.
Accessing the connector might require some careful disassembly. Start by identifying the specific area where the connector is located. Often, it can be found under the dashboard, behind the glove compartment, or in the engine bay. Carefully remove any trim panels or covers that might be in the way. Use a gentle approach to avoid pulling wires or causing damage. Remember to label or take pictures of the wiring harness to ensure you can reassemble it correctly.
Yes, there are a few steps to safely remove the old connector. First, ensure the vehicle's engine is off and the battery is disconnected to avoid any electrical hazards. Locate the connector and identify the wires connected to it. Carefully cut or strip the wire insulation, being mindful of the wire colors to avoid confusion during installation. Then, gently pull the connector away from the wiring harness, ensuring you don't damage any surrounding components. Keep track of the connector's orientation to facilitate a smooth installation of the new part.