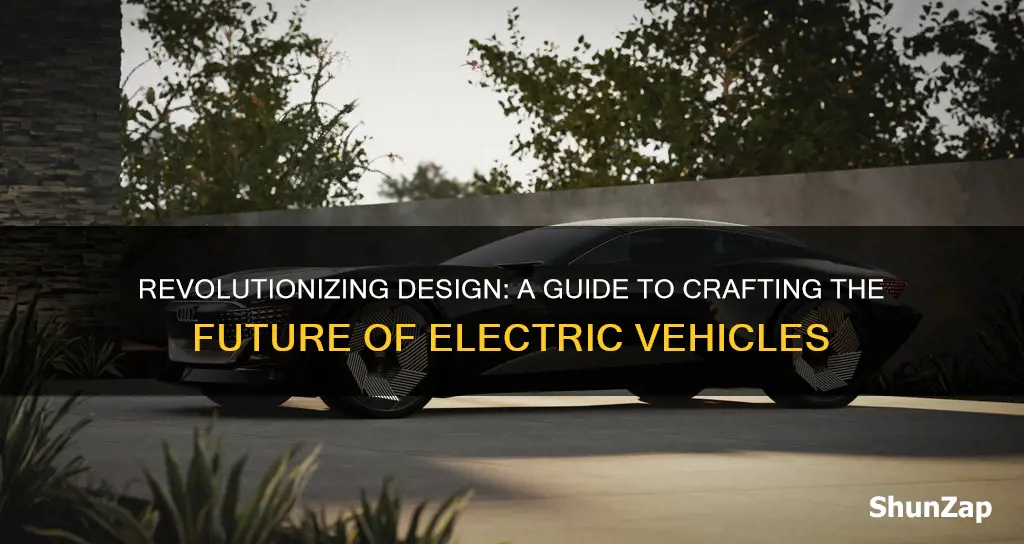
Designing an electric vehicle (EV) is a complex and innovative process that involves a multitude of engineering disciplines. It requires a deep understanding of electrical and mechanical systems, as well as a focus on sustainability and performance. The design process begins with defining the vehicle's purpose, range, and target market, followed by creating a detailed blueprint that includes the layout of the battery pack, motor placement, and the integration of various electronic components. This stage also involves optimizing the vehicle's aerodynamics, weight distribution, and overall efficiency to ensure it meets the desired performance and environmental standards. The design team must also consider factors such as user experience, safety, and the latest technological advancements to create a successful and market-ready electric vehicle.
What You'll Learn
- Battery Technology: Choose efficient, high-capacity batteries for optimal range and performance
- Motor Selection: Opt for powerful, efficient electric motors suited to vehicle size and purpose
- Power Electronics: Design efficient power electronics for optimal energy conversion and vehicle performance
- Thermal Management: Implement effective cooling systems to maintain battery and motor temperatures
- Vehicle Architecture: Consider lightweight materials and streamlined designs for improved efficiency and handling
Battery Technology: Choose efficient, high-capacity batteries for optimal range and performance
Battery technology is a critical component in the design and performance of electric vehicles (EVs). The choice of battery directly impacts the vehicle's range, efficiency, and overall driving experience. When designing an EV, engineers must carefully select batteries that offer both high energy density and efficient power output to meet the demands of the vehicle's operation.
One key consideration is the energy density of the battery. Energy density refers to the amount of energy that can be stored in a given volume or weight. For EVs, a higher energy density means more energy can be packed into a smaller space, allowing for a longer driving range without increasing the vehicle's size or weight. Modern lithium-ion batteries are often the preferred choice due to their relatively high energy density, which can provide the necessary power for EV applications.
In addition to energy density, the capacity of the battery is another crucial factor. Battery capacity is measured in ampere-hours (Ah) or kilowatt-hours (kWh) and indicates the amount of energy the battery can store. A higher capacity battery will enable the vehicle to travel longer distances on a single charge. For instance, a 100 kWh battery pack could provide a significant range advantage over a smaller capacity pack, making it essential to choose batteries with sufficient capacity to meet the vehicle's range requirements.
Furthermore, the efficiency of the battery is vital. Battery efficiency refers to the ratio of electrical energy output to the energy input. High-efficiency batteries can convert a larger portion of the stored energy into useful power, reducing energy waste and improving overall vehicle efficiency. This is especially important in EVs, where maximizing energy efficiency contributes to longer driving ranges and reduced charging times.
When selecting batteries, engineers should also consider factors such as temperature performance, cycle life, and safety. High-performance batteries should operate efficiently across a wide temperature range, ensuring consistent performance in various climates. Additionally, batteries should have a long cycle life, allowing for numerous charge-discharge cycles without significant capacity degradation. Safety is another critical aspect, as batteries must be designed to prevent overheating, short circuits, and other potential hazards.
In summary, the choice of battery technology is pivotal in the design of electric vehicles. Engineers must prioritize efficient, high-capacity batteries to achieve optimal range and performance. By selecting batteries with superior energy density, capacity, and efficiency, while also considering temperature performance, cycle life, and safety, EV designers can create vehicles that offer an exceptional driving experience and meet the growing demand for sustainable transportation.
The Ultimate Guide to Choosing the Best EV: A Comprehensive Comparison
You may want to see also
Motor Selection: Opt for powerful, efficient electric motors suited to vehicle size and purpose
Motor selection is a critical aspect of designing an electric vehicle (EV) as it directly impacts performance, efficiency, and overall driving experience. When choosing the right electric motors for your EV, several factors need to be considered to ensure optimal power delivery and efficiency tailored to the vehicle's specifications.
For electric vehicles, the motor's role is to convert electrical energy into mechanical energy, propelling the vehicle forward. The power and efficiency of the motor are key considerations. Powerful motors provide the necessary acceleration and top speed, especially for high-performance EVs. However, efficiency is equally important, as it directly affects the vehicle's range and overall energy consumption. Modern electric motors are designed to offer a balance between power and efficiency, ensuring the vehicle can deliver the required performance while optimizing energy usage.
The size and type of vehicle also play a significant role in motor selection. For instance, compact EVs or city cars may benefit from smaller, lightweight motors that provide adequate power without adding excessive weight. In contrast, larger vehicles, such as SUVs or trucks, might require more robust motors to handle increased torque and power demands. Additionally, the vehicle's intended purpose should guide motor choice. Sports cars or racing EVs may demand high-performance motors for rapid acceleration and top speeds, while utility vehicles or family cars might prioritize efficiency and range.
Efficiency is a critical aspect of motor design, especially for electric vehicles, where energy efficiency directly translates to longer ranges and reduced charging times. Advanced motor technologies, such as permanent magnet synchronous motors (PMSMs), offer improved efficiency by utilizing rare-earth magnets and sophisticated control algorithms. These motors can provide high torque at low speeds, making them ideal for city driving and rapid acceleration. Furthermore, regenerative braking systems can capture and reuse energy, further enhancing overall efficiency.
In summary, motor selection for electric vehicles involves a careful consideration of power, efficiency, vehicle size, and purpose. Engineers must choose motors that deliver the required performance while optimizing energy usage. Modern electric motor technologies offer a range of options, from compact and efficient designs for city cars to powerful and robust motors for high-performance EVs. By selecting the right motors, designers can create electric vehicles that offer an exceptional driving experience, combining performance, efficiency, and sustainability.
Upgrading Your Ride: A Guide to Converting Vehicle Axles to Electric Brakes
You may want to see also
Power Electronics: Design efficient power electronics for optimal energy conversion and vehicle performance
Power electronics play a pivotal role in the design and performance of electric vehicles (EVs), acting as the bridge between the vehicle's battery and the electric motor, and ensuring efficient energy conversion. The primary goal in designing power electronics for EVs is to optimize energy usage, enhance vehicle efficiency, and improve overall performance. This involves a meticulous approach to component selection, circuit design, and system integration.
One of the key considerations in power electronics design is the efficiency of power conversion. This is achieved through the use of high-frequency switching devices, such as insulated-gate bipolar transistors (IGBTs) and metal-oxide-semiconductor field-effect transistors (MOSFETs). These devices enable rapid and precise control of the flow of electricity, allowing for the conversion of direct current (DC) from the battery to alternating current (AC) for the motor, and vice versa. The design should aim for minimal power loss during these conversions, ensuring that the majority of the energy stored in the battery is utilized effectively.
The design process should also focus on thermal management. Power electronics generate significant heat during operation, and efficient cooling is essential to prevent overheating and maintain reliability. This can be achieved through the use of advanced cooling systems, such as liquid cooling or advanced air-cooling techniques, ensuring that the temperature of the power electronics remains within safe operating limits. Effective thermal management also contributes to the overall efficiency of the system by reducing energy losses due to heat.
Another critical aspect is the design of the power electronics to handle the specific voltage and current requirements of the EV. This involves selecting appropriate components that can withstand the electrical stresses and ensure reliable operation. For instance, the choice of IGBTs or MOSFETs should consider their voltage and current ratings, ensuring they can handle the peak and average power demands of the vehicle. Additionally, the design should incorporate protection mechanisms to safeguard against electrical faults, such as short circuits and over-current conditions.
Incorporating advanced control algorithms is also vital for optimizing vehicle performance. These algorithms can dynamically adjust the power electronics' operation based on real-time data, such as vehicle speed, battery state-of-charge, and driver input. By fine-tuning the power electronics' output, the vehicle can achieve better acceleration, improved range, and enhanced overall efficiency. This level of control also contributes to a smoother and more responsive driving experience.
In summary, designing efficient power electronics for EVs requires a comprehensive approach that considers efficiency, thermal management, electrical specifications, and control strategies. By optimizing these aspects, engineers can create power electronics systems that deliver high performance, reliability, and energy efficiency, ultimately contributing to the success of electric vehicles in the market.
Unlocking EV Savings: A Guide to Claiming Your Subsidy
You may want to see also
Thermal Management: Implement effective cooling systems to maintain battery and motor temperatures
Thermal management is a critical aspect of electric vehicle (EV) design, as it directly impacts the performance, efficiency, and longevity of the battery and motor systems. Effective cooling systems are essential to maintain optimal operating temperatures, ensuring the EV's overall reliability and range. Here's an overview of the key considerations for thermal management in EV design:
Battery Cooling:
- Lithium-ion batteries, commonly used in EVs, generate heat during operation due to internal resistance and chemical reactions. Excessive heat can degrade battery performance and reduce its lifespan. Therefore, implementing an efficient cooling system is vital.
- One approach is to use liquid cooling, where a coolant circulates through the battery pack, absorbing heat and transferring it to a radiator or heat exchanger. This method provides excellent temperature control and is often used in high-performance EVs.
- Alternatively, air cooling can be employed by directing a steady flow of air over the battery cells. This is a more cost-effective solution and can be achieved through active cooling systems with fans or passive cooling designs that optimize airflow.
- The cooling system should be designed to maintain the battery within a safe temperature range, typically between 15°C and 35°C, to maximize energy efficiency and minimize thermal stress.
Motor Cooling:
- Electric motors also require effective cooling to operate efficiently and prevent overheating. The cooling method depends on the motor type and design.
- For internal combustion engine (ICE) conversions, a similar cooling system can be used, with coolant circulation and radiators to dissipate heat. However, in pure electric vehicles, the motor design often incorporates cooling channels within the motor housing.
- Some advanced EV designs utilize liquid cooling directly within the motor, where a coolant flows through the motor's windings and stator, efficiently transferring heat away from the critical components.
- Proper motor cooling ensures optimal performance, reduces energy losses, and prevents damage to the motor's windings and insulation.
Integrated Design:
- Thermal management in EVs often involves an integrated approach, where the cooling systems are designed to work together harmoniously. This includes coordinating the placement of batteries, motors, and cooling components to optimize airflow and heat dissipation.
- The design should consider the overall layout of the vehicle, ensuring that cooling systems do not interfere with other components and that access for maintenance is straightforward.
- Advanced thermal management systems might include smart sensors and controls that monitor temperature, adjust fan speeds, or activate additional cooling mechanisms as needed, ensuring the EV's performance remains consistent across various driving conditions.
Materials and Insulation:
- Choosing appropriate materials for the cooling system and battery pack is crucial. Materials with high thermal conductivity, such as certain metals and composites, can enhance heat transfer.
- Insulation materials should be used to minimize heat loss between components and the environment, especially in cold climates.
- The design should also consider the thermal expansion and contraction of materials to prevent stress and potential damage over time.
Effective thermal management is a complex but essential part of EV design, ensuring the vehicle's performance, efficiency, and longevity. By implementing well-designed cooling systems, EV manufacturers can optimize the operation of batteries and motors, contributing to a more reliable and sustainable electric transportation future.
Unlocking Savings: A Guide to Colorado's EV Tax Credit
You may want to see also
Vehicle Architecture: Consider lightweight materials and streamlined designs for improved efficiency and handling
When designing an electric vehicle (EV), one of the most critical aspects to focus on is vehicle architecture, particularly the choice of materials and the overall design. Lightweight materials and streamlined designs are key elements that contribute to improved efficiency and handling, making EVs more competitive and appealing to consumers.
Lightweight Materials:
The use of lightweight materials is essential in EV design as it directly impacts the vehicle's overall weight. Lighter vehicles offer several advantages, including improved acceleration, enhanced range, and better overall performance. Materials such as advanced composites, high-strength steel alloys, and aluminum alloys are commonly utilized in EV construction. Carbon fiber-reinforced polymers (CFRP) are particularly notable for their exceptional strength-to-weight ratio, making them ideal for structural components like body panels and vehicle frames. By employing these lightweight materials, engineers can reduce the vehicle's mass without compromising structural integrity, thus contributing to increased efficiency.
Streamlined Design:
Streamlining the vehicle's design is another crucial factor in enhancing efficiency and handling. Aerodynamics play a significant role in reducing drag, which is the force that opposes the motion of the vehicle. A well-designed EV with a streamlined body can minimize air resistance, allowing for smoother and more efficient driving. Designers should focus on creating a sleek and aerodynamic shape, ensuring that the vehicle's front end, sides, and rear are all optimized to cut through the air efficiently. This includes carefully shaping the roof, windows, and rear spoiler to reduce drag and improve stability at high speeds.
To achieve this, designers can employ various techniques, such as using smooth curves instead of sharp edges, integrating air intakes and vents in aerodynamic locations, and optimizing the vehicle's underbody to minimize turbulence. Additionally, the use of active aerodynamics, such as adjustable air dams or spoilers, can further enhance performance by optimizing drag at different speeds and driving conditions.
By combining lightweight materials with a streamlined design, EV manufacturers can create vehicles that offer improved efficiency, reduced energy consumption, and enhanced handling characteristics. This approach not only benefits the environment by reducing emissions but also provides a more engaging and responsive driving experience for EV owners.
Transform Your Ride: The Ultimate Guide to Electric Vehicle Conversion
You may want to see also
Frequently asked questions
Designing the battery system is a critical aspect of EV development. Key considerations include choosing the right battery chemistry (such as lithium-ion), determining the capacity and energy density requirements based on the vehicle's range and performance needs, and optimizing the battery pack layout for space efficiency and thermal management. Safety is paramount, so advanced cooling systems and protective circuitry are essential.
Electric motor design focuses on maximizing power and torque while ensuring efficiency. This involves selecting the appropriate motor type (AC or DC) and size based on the vehicle's performance goals. Engineers optimize the motor's efficiency by minimizing losses, using advanced materials for reduced weight and improved heat dissipation, and implementing precise control algorithms to manage torque and speed effectively.
Thermal management is crucial to maintain optimal performance and longevity. Challenges include managing heat generation from the battery pack, electric motors, and power electronics. Designers must ensure efficient cooling to prevent overheating, especially in compact EV designs. This often involves complex cooling systems, such as liquid cooling or advanced air management, to maintain ideal operating temperatures for all components.
Power electronics play a vital role in converting and controlling electrical energy. Designers focus on developing compact and efficient inverters and converters to manage power flow. This includes optimizing voltage and current levels, minimizing losses during power conversion, and ensuring fast response times for smooth acceleration and regenerative braking. Advanced cooling techniques are also applied to manage heat dissipation.
Structural integrity and lightweight design are essential for EV efficiency and performance. Designers consider factors like material selection (often lightweight composites or advanced alloys), body-in-white construction techniques, and crash safety. The goal is to create a robust yet lightweight structure that provides excellent aerodynamics, reduces weight, and ensures passenger safety.