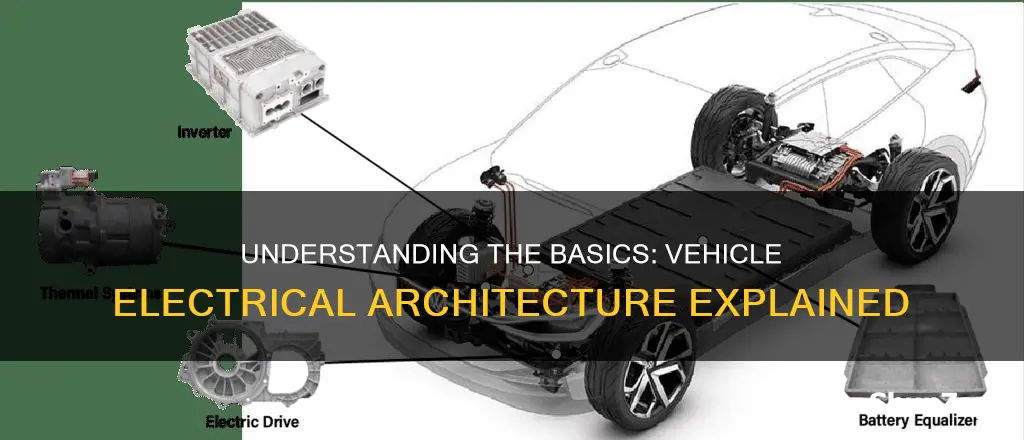
Vehicle electrical architecture refers to the intricate network of electrical and electronic systems within a vehicle, which has become increasingly complex with the advent of modern automobiles. This architecture encompasses various components such as sensors, actuators, control units, and communication networks that work together to enable a vehicle's functionality and performance. It involves the design and integration of these systems to ensure efficient power distribution, data processing, and control, ultimately contributing to the overall safety, comfort, and efficiency of the vehicle. Understanding this architecture is crucial for engineers and technicians to maintain and troubleshoot modern vehicles effectively.
What You'll Learn
- Power Distribution: How electrical energy is supplied to various vehicle systems
- Wiring Harness Design: The layout and organization of wires in a vehicle
- Electronic Control Units (ECUs): Microcontrollers managing vehicle functions via software
- Communication Protocols: Standards for data exchange between vehicle components
- Safety Mechanisms: Redundancy and fail-safe systems to prevent electrical failures
Power Distribution: How electrical energy is supplied to various vehicle systems
The vehicle electrical architecture is a complex network that powers and controls various systems in modern automobiles. Power distribution is a critical component of this architecture, ensuring that electrical energy is efficiently and safely routed to where it's needed. This process involves several key components and principles.
At the heart of power distribution is the battery, which stores electrical energy and provides the initial power source. When the vehicle is running, the battery is connected to the alternator, which generates electricity through the process of electromagnetic induction. This alternator is typically driven by the engine, ensuring a continuous supply of electrical power. The generated electricity is then distributed throughout the vehicle's electrical system.
The power distribution system uses a network of wires, fuses, and relays to route electricity to different components. This network is carefully designed to handle specific voltage and current requirements. For instance, high-current circuits, such as those powering the starter motor or electric fans, are equipped with heavy-duty wires and fuses to prevent overheating and potential damage. Relays are used to control high-power circuits, allowing for efficient management of energy distribution.
One critical aspect of power distribution is the use of a central power distribution module or relay box. This module acts as a central hub, distributing power to various subsystems. It ensures that each system receives the appropriate voltage and current levels, optimizing performance and safety. For example, the engine control unit (ECU) requires a stable and precise voltage supply to manage engine operations, while the lighting system needs a higher current for illumination.
Modern vehicles also incorporate advanced power management systems, especially in hybrid and electric vehicles. These systems optimize energy usage, ensuring that power is distributed efficiently and that the battery is charged and discharged effectively. Advanced power electronics, such as power semiconductors and inverters, play a crucial role in managing power distribution, especially in electric powertrains. These components enable the conversion and control of electrical energy, allowing for the smooth operation of various vehicle systems.
Firefighting Strategies: Extinguishing EV Fires: A Comprehensive Guide
You may want to see also
Wiring Harness Design: The layout and organization of wires in a vehicle
The wiring harness is a critical component of a vehicle's electrical architecture, acting as the backbone that connects various subsystems and ensures the smooth operation of the entire system. The design of this harness is a complex process that requires careful consideration of numerous factors to ensure optimal performance, reliability, and safety.
In the context of vehicle electrical architecture, the wiring harness design involves the strategic arrangement of wires, cables, and connectors to facilitate the efficient transfer of electrical signals and power throughout the vehicle. This design process is crucial as it directly impacts the vehicle's overall performance, safety, and longevity. A well-designed harness should be able to withstand the harsh environmental conditions inside a vehicle, including extreme temperatures, vibrations, and exposure to moisture.
The layout of the wiring harness is a critical aspect of its design. It involves determining the optimal path for wires to connect different components while minimizing the overall length of the harness. This is achieved through a process called 'routing', where engineers carefully plan the path of wires to avoid interference with other components, ensure easy access for maintenance, and maintain a neat and organized appearance. Proper routing also helps in reducing electromagnetic interference, ensuring that sensitive electronic components are not affected by electrical noise.
Organization is another key element in wiring harness design. This includes the use of color-coding, labeling, and grouping wires to make identification and maintenance easier. Each wire should be clearly labeled with its function and location, allowing technicians to quickly understand its purpose during repairs or maintenance. Color-coding can also be employed to differentiate between power, ground, and signal wires, further enhancing the harness's organization.
Additionally, the design process involves selecting appropriate wire gauges and materials to handle the expected current loads and environmental conditions. Thicker wires are used for high-current applications, while thinner ones are suitable for low-current signals. The choice of insulation material is also vital, ensuring it can withstand the operating temperatures and chemical exposure within the vehicle.
In summary, wiring harness design is a meticulous process that plays a pivotal role in the functionality and safety of a vehicle's electrical system. It requires a deep understanding of electrical principles, attention to detail, and the ability to balance performance, reliability, and aesthetics. Effective harness design ensures that the vehicle's electrical architecture is robust, efficient, and capable of meeting the demands of modern automotive technology.
Unveiling the World of Light Electric Vehicles: A Comprehensive Guide
You may want to see also
Electronic Control Units (ECUs): Microcontrollers managing vehicle functions via software
The modern vehicle's electrical architecture is a complex network of interconnected components, with the heart of this system being the Electronic Control Units (ECUs). These microcontrollers are the brains behind the operation, managing and coordinating various vehicle functions through sophisticated software. Each ECU is dedicated to a specific task, ensuring precise control and optimization of vehicle performance.
In the automotive world, ECUs have revolutionized the way vehicles operate. They are responsible for receiving input from various sensors and actuators, processing this data, and making decisions accordingly. For instance, the Engine Control Unit (ECU) monitors engine speed, temperature, and fuel levels, adjusting the fuel injection and ignition timing to optimize performance and fuel efficiency. Similarly, the Transmission Control Unit (TCU) manages gear shifts, ensuring smooth and efficient power transmission.
The software within these ECUs is meticulously designed to handle specific vehicle functions. It employs algorithms and data processing techniques to make real-time decisions, often with millisecond precision. For example, the Anti-Lock Braking System (ABS) ECU continuously analyzes wheel speed and vehicle dynamics, adjusting brake pressure to prevent skidding. This software-driven approach allows for dynamic adjustments, ensuring the vehicle responds appropriately to various driving conditions.
ECUs also facilitate communication between different vehicle systems. They use Controller Area Network (CAN) buses to exchange data, enabling coordination and synchronization. For instance, the ECU can communicate with the Body Control Module (BCM) to adjust the interior lighting or with the Airbag Control Unit (ACU) to deploy airbags in an accident. This interconnectedness ensures a seamless and safe driving experience.
The advancement of ECUs has led to improved vehicle performance, fuel efficiency, and safety. Modern vehicles can offer features like adaptive cruise control, lane-keeping assist, and automatic parking, all made possible by the intricate software and microcontrollers within the ECUs. As technology continues to evolve, these ECUs will play a pivotal role in shaping the future of automotive engineering.
Unveiling the Green Revolution: Electric Vehicle Ecosystems Explained
You may want to see also
Communication Protocols: Standards for data exchange between vehicle components
Vehicle electrical architecture refers to the intricate network of electrical and electronic systems within a vehicle, enabling various components to communicate and function harmoniously. At the heart of this architecture are communication protocols, which serve as the language and standards for data exchange between different vehicle components. These protocols are essential for ensuring efficient, reliable, and safe operation of modern vehicles.
Communication protocols define the rules and procedures for transmitting data between various vehicle systems, such as the engine control unit (ECU), sensors, actuators, and entertainment systems. They establish a structured framework for data formatting, transmission, and reception, ensuring that information is accurately conveyed and interpreted by the receiving component. The primary goal is to enable real-time communication, allowing for immediate responses and adjustments to changing conditions.
One of the key standards in vehicle communication protocols is the Controller Area Network (CAN) bus. CAN is a widely adopted protocol that enables high-speed data exchange between multiple microcontrollers and devices. It operates on a single twisted-pair cable, making it cost-effective and easy to implement. The CAN bus uses a distributed network architecture, where each node can transmit and receive data, ensuring that information is shared efficiently across the vehicle's network. This protocol is particularly useful for time-critical applications, such as engine control and safety systems.
Another important protocol is the Local Interconnect Network (LIN), which is designed for cost-effective and flexible communication in automotive applications. LIN operates at lower data rates compared to CAN, making it suitable for simpler control units and sensors. It supports a master-slave architecture, where a central master node coordinates communication with multiple slave nodes. LIN is often used for applications like engine management, climate control, and body control systems.
Additionally, the FlexRay protocol is gaining popularity in advanced vehicle architectures. FlexRay offers high-speed data transmission and real-time performance, making it ideal for safety-critical systems. It employs a fault-tolerant architecture with multiple communication channels, ensuring reliable data exchange even in the presence of faults. FlexRay is particularly useful for applications requiring strict timing requirements, such as advanced driver-assistance systems (ADAS) and autonomous driving functions.
In summary, communication protocols are the backbone of vehicle electrical architecture, enabling seamless data exchange between various components. Standards like CAN, LIN, and FlexRay provide efficient, reliable, and standardized ways for vehicles to communicate, ensuring optimal performance, safety, and functionality. As vehicle technology continues to evolve, these communication protocols will play a crucial role in enabling advanced driver-assistance systems, autonomous driving, and other innovative features.
Electric Vehicles: Uncovering the Hidden Drawbacks
You may want to see also
Safety Mechanisms: Redundancy and fail-safe systems to prevent electrical failures
The modern vehicle's electrical architecture is a complex network of interconnected components, each contributing to the overall functionality and safety of the vehicle. One critical aspect of this architecture is the implementation of safety mechanisms, particularly redundancy and fail-safe systems, to prevent electrical failures and ensure the vehicle's safe operation.
Redundancy is a fundamental principle in electrical architecture, especially in safety-critical systems. It involves having multiple independent systems or components that can perform the same function. For example, in a vehicle's braking system, redundancy might be achieved by having two separate circuits, each with its own set of sensors and actuators. If one circuit fails, the other can take over, ensuring that the vehicle can still stop effectively. This approach significantly reduces the risk of a complete system failure, as the loss of one component does not necessarily lead to a complete loss of function.
Fail-safe systems are another crucial element of electrical architecture, designed to minimize the impact of potential failures. These systems are configured to enter a safe state or mode in the event of a malfunction, preventing hazardous situations. For instance, in a vehicle's engine control unit (ECU), a fail-safe mechanism might be implemented to shut down the engine if a critical sensor fails, preventing potential damage or loss of control. This could involve a backup power supply or a manual override, ensuring that the vehicle remains safe even if the primary system fails.
The design of these safety mechanisms requires a thorough understanding of potential failure modes and their consequences. Engineers must identify critical components and systems, assess their failure rates, and then implement appropriate redundancy and fail-safe measures. This process often involves extensive testing and simulation to ensure that the safety mechanisms can effectively respond to various failure scenarios.
Furthermore, the integration of these safety features into the vehicle's electrical architecture requires careful planning. Designers must consider the communication and data flow between different systems to ensure that redundancy and fail-safe mechanisms work seamlessly. This includes the use of diagnostic tools and error-handling routines to detect and manage failures promptly.
In summary, the vehicle's electrical architecture incorporates redundancy and fail-safe systems as essential safety mechanisms. These systems are designed to prevent electrical failures by providing backup functionality and entering safe modes in the event of malfunctions. Through careful engineering and testing, these safety features contribute to the overall reliability and safety of modern vehicles, ensuring that drivers and passengers can travel with confidence.
The Green Promise of Electric Vehicles: Unveiling the Reality
You may want to see also
Frequently asked questions
Vehicle electrical architecture refers to the design and organization of electrical systems within a vehicle, including the wiring harnesses, electronic control units (ECUs), sensors, actuators, and other components that enable the vehicle's functionality and performance. It involves the layout, connectivity, and integration of these components to ensure efficient and reliable operation.
Modern vehicles heavily rely on electrical architecture to provide advanced features and improve overall performance. It enables the integration of various subsystems, such as engine control, transmission, lighting, entertainment, and safety systems. By utilizing a well-designed electrical architecture, manufacturers can achieve better fuel efficiency, enhanced driver assistance, improved diagnostics, and seamless connectivity with other smart devices.
The key components typically include the Central Electronic Control Unit (ECU), sensors, actuators, wiring harnesses, and communication networks. The ECU acts as the brain, processing data and controlling vehicle functions. Sensors provide real-time information about various parameters, while actuators perform physical actions. Wiring harnesses connect these components, and communication networks ensure data exchange between different systems, allowing for coordinated operation and advanced vehicle capabilities.