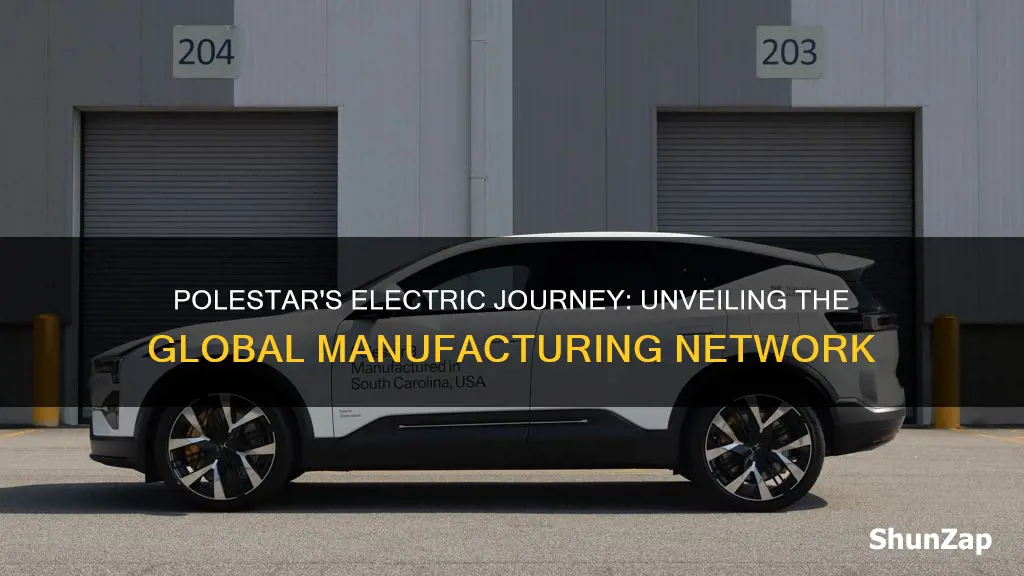
Polestar, a Swedish electric vehicle manufacturer, has established itself as a prominent player in the automotive industry. The company's electric vehicles are produced in a state-of-the-art facility located in Chengdu, China, and in a new plant in South Carolina, USA. This strategic decision to have manufacturing hubs in both Europe and North America allows Polestar to cater to a global market and reduce transportation costs. The production process is highly automated, utilizing advanced robotics and AI to ensure precision and efficiency. This introduction sets the stage for a deeper exploration of Polestar's manufacturing operations and their impact on the company's success.
Characteristics | Values |
---|---|
Country of Origin | Sweden |
Manufacturing Locations | Sweden (Gislaved), China (Lishui), United States (South Carolina) |
Assembly Plants | 3 (Sweden, China, USA) |
Battery Production | In-house battery production in Sweden and China |
Supply Chain | Global supply chain with components sourced from various countries |
Market Focus | Global market with a strong presence in Europe, North America, and Asia |
Ownership | Volvo Cars (part of Geely Holding) |
Production Capacity | Varies by location and model |
Electric Vehicle Models | Polestar 1, Polestar 2, Polestar 3 |
Future Expansion | Plans for additional manufacturing sites in Europe and North America |
What You'll Learn
- Manufacturing Locations: Polestar EVs are primarily produced in Sweden and China
- Supply Chain: The company's supply chain spans multiple countries
- Assembly Process: Each vehicle undergoes a meticulous assembly process in dedicated facilities
- Local Production: Some models are locally produced to meet regional demand
- Expansion Plans: Future production sites are under consideration for global reach
Manufacturing Locations: Polestar EVs are primarily produced in Sweden and China
Polestar, the Swedish electric vehicle manufacturer, has established a strong presence in the automotive industry with its focus on sustainable and innovative mobility. The company's manufacturing operations are strategically located in two key regions: Sweden and China.
In Sweden, Polestar's home country, the brand has its roots and a deep-rooted connection to the automotive heritage of the region. The company's first manufacturing facility is situated in the city of Trollhättan, which has been a significant hub for automotive production for decades. This location is where Polestar's iconic models, such as the Polestar 1 and the upcoming Polestar 3, are assembled. The Swedish facility showcases Polestar's commitment to its Scandinavian origins and its dedication to utilizing the country's advanced manufacturing capabilities. With a focus on precision engineering and a skilled workforce, the Trollhättan plant ensures that Polestar vehicles meet the highest standards of quality and craftsmanship.
In addition to its Swedish base, Polestar has expanded its manufacturing capabilities in China, a strategic move to tap into the rapidly growing electric vehicle market in the region. The company's Chinese manufacturing partner, Zhejiang Geely Holding Group, has established a dedicated production facility for Polestar vehicles. This facility is designed to produce the Polestar 2, a popular compact SUV, and is located in the city of Liuzhou. The Chinese manufacturing operation showcases Polestar's ability to adapt to different markets and its commitment to global expansion. By leveraging Geely's expertise and resources, Polestar ensures efficient production processes and a strong presence in the Asian market.
The dual-location manufacturing strategy allows Polestar to cater to diverse markets and optimize its production processes. Sweden's focus on craftsmanship and quality complements China's advanced manufacturing capabilities and market proximity. This approach enables Polestar to deliver its electric vehicles to customers worldwide while maintaining a strong connection to its Scandinavian heritage.
As Polestar continues to grow and expand its product line, the company's manufacturing locations will play a crucial role in its success. The strategic choice of Sweden and China as production hubs demonstrates Polestar's commitment to innovation, sustainability, and global accessibility in the electric vehicle space.
Unraveling the Electric Vehicle Market: Trends, Challenges, and Opportunities
You may want to see also
Supply Chain: The company's supply chain spans multiple countries
Polestar, the Swedish electric vehicle manufacturer, has a global supply chain that is an intricate web of partnerships and production sites across various countries. This strategic approach allows the company to optimize its operations and cater to a diverse market. The supply chain's complexity is a testament to Polestar's commitment to delivering high-quality electric vehicles while maintaining a sustainable and efficient production process.
The manufacturing process begins with the sourcing of raw materials, primarily lithium-ion batteries, which are crucial for the vehicles' performance and range. These batteries are sourced from suppliers in China, South Korea, and Japan, renowned for their expertise in battery technology. The company's partnership with these suppliers ensures a consistent supply of high-quality batteries, which are then integrated into the vehicle's design.
Polestar's production facilities are strategically located to minimize transportation costs and environmental impact. The company has established manufacturing hubs in China and the United States, with plans for further expansion. The Chinese facility, located in Chengdu, is a key production site, where the Polestar 2, a popular sedan, is assembled. This site utilizes advanced robotics and automation to ensure precision and efficiency in the manufacturing process.
In addition to manufacturing, Polestar's supply chain also encompasses design and engineering centers. These centers are strategically positioned in key markets, such as Sweden, the United States, and China. Here, a team of experts works on vehicle design, software development, and engineering, ensuring that Polestar vehicles meet the highest standards of performance, safety, and sustainability. This global network of talent allows the company to innovate and adapt to the ever-evolving automotive industry.
Furthermore, Polestar's supply chain management is characterized by a focus on sustainability and ethical practices. The company has implemented rigorous standards for its suppliers, ensuring that they adhere to environmental and social responsibility guidelines. This includes responsible sourcing of materials, efficient waste management, and a commitment to reducing the carbon footprint of its production processes. By prioritizing sustainability, Polestar aims to create a more environmentally conscious supply chain, setting an example for the industry.
Unveiling the Hazards: Inside Electric Vehicle Batteries
You may want to see also
Assembly Process: Each vehicle undergoes a meticulous assembly process in dedicated facilities
The assembly of Polestar electric vehicles is a meticulous and intricate process, carried out in state-of-the-art dedicated facilities. These facilities are designed to ensure the highest level of precision and quality control, reflecting Polestar's commitment to excellence. The assembly line is a carefully choreographed dance of robotics and human expertise, where each component is meticulously fitted and tested.
The process begins with the arrival of individual parts, which are then carefully inspected and sorted. This initial stage is crucial, as it sets the foundation for the entire assembly. Each part, from the engine to the interior trim, is scrutinized to ensure it meets the stringent standards set by Polestar. This includes checking for any defects, verifying the correct specifications, and ensuring that all components are compatible with each other.
Once the parts are approved, they are transported to the assembly line. Here, the real magic happens. Skilled technicians and engineers work in harmony, following a detailed set of instructions for each vehicle. The assembly line is a well-oiled machine, with each station dedicated to a specific task. For instance, one station might focus on installing the electric motor, while another might be responsible for wiring and connecting the various systems.
As the vehicle moves along the line, it undergoes a series of tests and inspections. This includes checking the performance of the electric motor, ensuring the battery pack is securely mounted, and verifying the functionality of the charging port. Each step is critical to the overall success of the vehicle, and any issues are immediately addressed by the team.
The final stage of assembly involves the completion of the vehicle's interior and exterior. This includes fitting the dashboard, seats, and all the electronic systems. The exterior is then finished with the final paint job and any additional trim. Once complete, the vehicle undergoes a thorough inspection to ensure it meets all safety and quality standards. This meticulous assembly process is a testament to Polestar's dedication to delivering exceptional electric vehicles.
Unraveling the Mystery: Common Causes of Electric Fires in Vehicles
You may want to see also
Local Production: Some models are locally produced to meet regional demand
Polestar, the Swedish electric vehicle manufacturer, has adopted a strategic approach to production, including local manufacturing to cater to specific regional markets. This approach ensures that the company can efficiently meet the demands of various regions, offering a tailored experience to its customers. By producing some models locally, Polestar aims to reduce lead times and enhance customer satisfaction, especially in markets with high demand.
The local production strategy is particularly evident in regions with strong automotive industries and established supply chains. For instance, Polestar's decision to manufacture its vehicles in China is a response to the country's growing demand for electric cars and its well-developed automotive infrastructure. This local production enables Polestar to tap into the Chinese market, offering its sustainable and innovative vehicles to a large and rapidly expanding customer base.
In other regions, such as Europe, Polestar also leverages local production to its advantage. The company's collaboration with local suppliers and the utilization of regional manufacturing hubs ensure that the vehicles are produced with a high level of quality and efficiency. This approach not only reduces transportation costs but also minimizes the environmental impact associated with long-distance logistics.
The benefits of local production extend beyond cost savings and environmental considerations. By producing vehicles closer to the market, Polestar can better understand and respond to regional preferences and regulations. This includes adapting to local safety standards, emission norms, and customer expectations, ensuring that the vehicles meet the specific needs of each market.
Furthermore, local production fosters a stronger connection between Polestar and its customers. It allows for more personalized interactions, as the company can engage directly with local communities, understand their unique requirements, and provide tailored solutions. This level of engagement is crucial in building a loyal customer base and establishing a strong brand presence in various regions.
Electric Vehicle Ownership: The American Shift to Green Transportation
You may want to see also
Expansion Plans: Future production sites are under consideration for global reach
Polestar, the Swedish electric vehicle manufacturer, has been on an ambitious expansion journey, aiming to solidify its position in the global market. The company's future plans involve a strategic approach to production site expansion, with a focus on global reach and accessibility. Here's an overview of their expansion strategy:
Global Production Network: Polestar is strategically planning to establish a robust production network worldwide. The company aims to reduce reliance on a single manufacturing hub and instead diversify its production sites. By doing so, they can cater to a broader market and ensure a more efficient supply chain. This global approach will enable Polestar to meet the growing demand for its electric vehicles (EVs) and provide a more localized experience for customers worldwide.
New Manufacturing Facilities: The expansion plans include the construction of new manufacturing facilities in key markets. For instance, Polestar has announced its intention to build a factory in the United States, targeting the West Coast region. This move will enable the company to tap into the vast EV market in North America and reduce the time it takes for vehicles to reach customers in this region. Additionally, they are considering locations in Europe and Asia, ensuring a more comprehensive global presence. These new sites will not only increase production capacity but also create job opportunities in various regions.
Localizing Production: One of the key aspects of Polestar's expansion strategy is localizing production. By establishing manufacturing facilities closer to key markets, they can reduce transportation costs and carbon emissions associated with long-distance shipping. This approach also allows for better customization and adaptation to regional preferences, ensuring that Polestar vehicles meet the unique demands of different markets. For example, producing EVs closer to Asian markets can cater to the region's specific requirements and cultural preferences.
Supply Chain Optimization: As part of its expansion, Polestar is also focusing on optimizing its supply chain. This includes forming strategic partnerships with local suppliers and component manufacturers in various regions. By localizing the supply chain, the company can ensure a steady supply of raw materials and parts, reducing potential bottlenecks. Efficient supply chain management will be crucial in supporting the increased production volumes and maintaining the high quality and reliability of Polestar vehicles.
In summary, Polestar's expansion plans are well-thought-out and strategically designed to capture the global EV market. By establishing a worldwide production network, the company aims to increase its accessibility, reduce transportation costs, and provide a more tailored experience for customers. This approach demonstrates Polestar's commitment to becoming a leading global player in the electric vehicle industry while maintaining its Swedish heritage and innovation.
A Journey Through Time: Unveiling the Market's Oldest Electric Vehicle
You may want to see also
Frequently asked questions
Polestar, a Swedish electric vehicle manufacturer, has a strong focus on sustainability and innovation. Their vehicles are produced in two strategic locations: the Volvo Car Plant in Ghent, Belgium, and the Tesla Gigafactory Shanghai in China. The Ghent plant, a state-of-the-art facility, is where the Polestar 2 is assembled, utilizing a combination of traditional and electric assembly techniques. The Shanghai Gigafactory, a joint venture with Tesla, is responsible for the production of the Polestar 3, an SUV designed for the global market.
Polestar's manufacturing strategy is designed to cater to various markets worldwide. The Polestar 2, for instance, is primarily produced in Ghent, Belgium, and is also available in right-hand drive versions for markets like the United Kingdom and Japan. The Polestar 3, on the other hand, is manufactured in Shanghai, China, to meet the demands of the Asian market and other regions where the vehicle is sold.
Polestar has ambitious plans for growth and has announced its intention to expand its production capabilities. The company aims to increase its global production capacity by utilizing existing partnerships and potentially exploring new manufacturing sites. This expansion will enable Polestar to meet the rising demand for its electric vehicles and solidify its position as a leading sustainable car brand.
Polestar places a high priority on quality and has implemented rigorous quality control measures throughout its production process. At the Ghent plant, advanced robotics and automated systems are employed to ensure precision and consistency in vehicle assembly. Additionally, Polestar conducts extensive testing and quality checks at various stages of production, including pre-production and final assembly, to guarantee that every vehicle meets the brand's high standards.