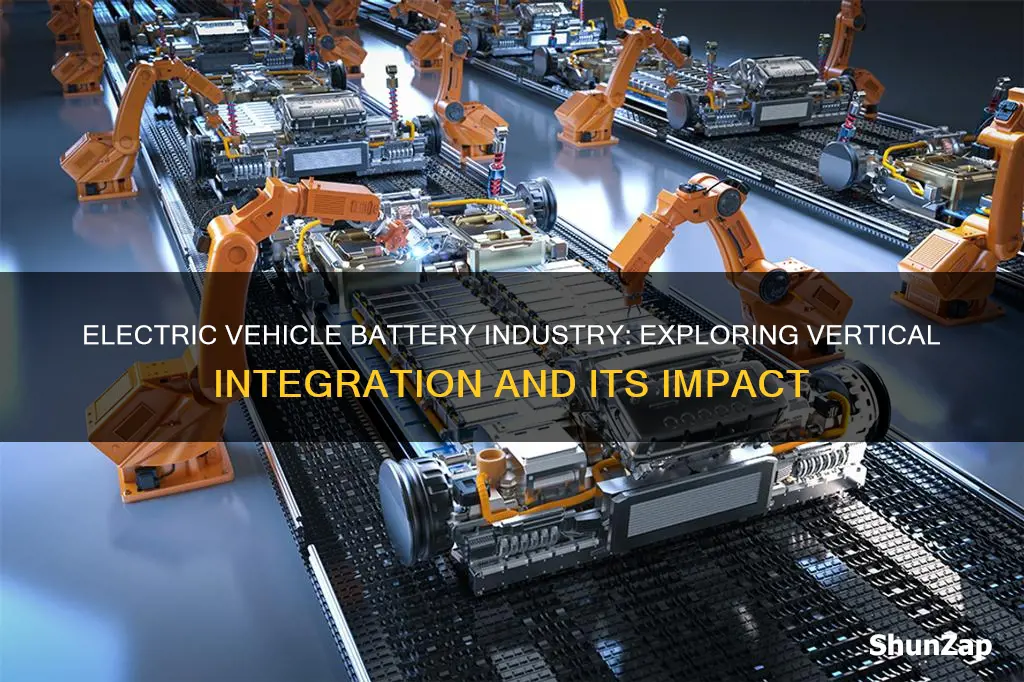
The electric vehicle (EV) battery industry has seen significant growth and innovation in recent years, driven by the global shift towards sustainable transportation. As the demand for electric cars and other electric mobility solutions increases, the question of vertical integration within the battery supply chain becomes increasingly relevant. Vertical integration in this context refers to the degree to which a company controls its production processes, from raw material sourcing to final product assembly. This exploration aims to delve into the current state of vertical integration in the EV battery industry, examining the strategies employed by key players and the potential implications for the market.
What You'll Learn
- Battery Manufacturing: Vertical integration in the EV battery industry involves controlling the entire production process, from raw materials to finished batteries
- Supply Chain Management: Integrating suppliers and distributors to ensure a consistent and reliable supply of materials and components for battery production
- Research and Development: In-house R&D capabilities for battery technology advancements and innovation, reducing reliance on external partners
- Recycling and Disposal: Vertical integration can include establishing recycling facilities to manage end-of-life batteries and promote sustainability
- Market Strategy: Integrating sales, marketing, and distribution channels to control the entire customer journey and maintain a competitive edge
Battery Manufacturing: Vertical integration in the EV battery industry involves controlling the entire production process, from raw materials to finished batteries
The electric vehicle (EV) battery industry has indeed embraced vertical integration as a strategic approach to ensure quality, efficiency, and cost-effectiveness. This concept involves a company or entity taking control of the entire production process, from the sourcing of raw materials to the final assembly of batteries. By doing so, they aim to optimize every stage of manufacturing and gain a competitive edge in the market.
Vertical integration in the EV battery sector allows companies to have precise control over the quality of raw materials, which is crucial for battery performance and longevity. This includes the selection of specific minerals, metals, and chemicals, ensuring they meet or exceed industry standards. For instance, lithium-ion batteries rely on high-purity lithium, cobalt, and nickel, and controlling the supply chain for these materials is essential to maintain product reliability.
The manufacturing process itself is a complex journey, starting with the mixing and formation of battery cells, followed by assembly, testing, and quality control. By integrating these processes, companies can streamline production, reduce waste, and ensure consistency in the final product. This level of control also enables them to respond quickly to market demands and adapt to technological advancements.
Furthermore, vertical integration provides an opportunity to innovate and develop proprietary technologies. Companies can invest in research and development to create more efficient battery designs, improve charging infrastructure, and enhance recycling methods. This not only benefits their own operations but also contributes to the overall advancement of the EV battery industry.
In summary, the EV battery industry's adoption of vertical integration is a strategic move to gain control, improve quality, and drive innovation. It allows companies to optimize the entire production chain, from raw materials to finished batteries, ultimately benefiting both the business and the environment by ensuring a more sustainable and efficient approach to power EV vehicles.
Beyond the Gender Divide: Uncovering the Real Reasons Women Opt Out of EVs
You may want to see also
Supply Chain Management: Integrating suppliers and distributors to ensure a consistent and reliable supply of materials and components for battery production
The electric vehicle (EV) battery industry's supply chain management is a complex and critical aspect of the overall production process. Vertical integration is a key strategy employed by many companies in this sector to ensure a consistent and reliable supply of materials and components, which is essential for the mass production of batteries. This approach involves the integration of various stages of the supply chain, from raw material sourcing to the final assembly of batteries. By doing so, manufacturers can maintain control over the quality and availability of materials, which is crucial for the production of high-performance batteries.
In the context of vertical integration, battery producers often establish long-term relationships with suppliers and distributors, ensuring a steady supply of essential materials such as lithium, cobalt, nickel, and graphite. These raw materials are then processed and transformed into battery components like cathodes, anodes, and electrolytes. The integration process allows companies to have a more comprehensive understanding of the supply chain, enabling them to anticipate and mitigate potential disruptions. For instance, by having direct control over or close relationships with suppliers, manufacturers can ensure that the necessary quantities of raw materials are available when needed, preventing production delays.
Effective supply chain management also involves the optimization of transportation and logistics. Battery producers need to ensure that components and materials are transported efficiently and securely to various production sites. This includes managing the distribution of raw materials to processing facilities and then coordinating the movement of finished battery packs to assembly plants. Efficient logistics can reduce lead times and ensure that production lines are consistently supplied, which is vital for maintaining a steady output of batteries.
Furthermore, vertical integration allows battery manufacturers to implement quality control measures at multiple stages of production. By having a direct influence on the supply chain, companies can set and maintain high standards for material sourcing, processing, and assembly. This ensures that the final product meets the required specifications and performance standards. For example, integrated suppliers can provide real-time feedback on material quality, allowing producers to make immediate adjustments to production processes if needed.
In summary, the electric vehicle battery industry's supply chain management is a critical aspect of ensuring the reliability and consistency of battery production. Vertical integration enables companies to maintain control over the supply of raw materials and components, optimize transportation and logistics, and implement rigorous quality control measures. This strategic approach is essential for the industry's growth and the successful mass production of electric vehicle batteries.
Uncover the Top EV Tax Rebate Destinations
You may want to see also
Research and Development: In-house R&D capabilities for battery technology advancements and innovation, reducing reliance on external partners
The electric vehicle (EV) battery industry has indeed embraced vertical integration, a strategic approach that allows companies to control various stages of production, from raw material sourcing to end-product assembly. This integration is particularly evident in the realm of research and development (R&D), where in-house capabilities play a pivotal role in driving innovation and reducing dependency on external partners.
In-house R&D facilities enable EV battery manufacturers to foster a culture of innovation, allowing them to stay at the forefront of battery technology advancements. These internal teams can focus on specific areas of development, such as improving energy density, extending battery life, or enhancing safety features. By having dedicated resources, companies can respond swiftly to market demands and stay ahead of the competition. For instance, they can quickly adapt to the growing need for longer-range batteries or address concerns related to battery degradation over time.
Vertical integration in R&D also empowers companies to maintain a competitive edge by reducing reliance on external partners. While collaboration with external research institutions or suppliers can be beneficial, having in-house expertise ensures a more streamlined and efficient process. In-house R&D teams can work closely with production and engineering departments, facilitating a seamless transition from research to development and, ultimately, manufacturing. This internal synergy can lead to faster time-to-market for new battery technologies and more efficient resource allocation.
Furthermore, vertical integration in R&D allows companies to protect their intellectual property (IP) and maintain a competitive advantage. By developing cutting-edge technologies in-house, they can safeguard their innovations and prevent potential IP leaks associated with external partnerships. This is crucial in an industry where battery technology is rapidly evolving, and staying ahead of the curve is essential for market success.
In summary, the electric vehicle battery industry's adoption of vertical integration in R&D is a strategic move that fosters innovation, reduces external dependencies, and ensures a competitive edge. In-house R&D capabilities enable companies to drive advancements in battery technology, address market demands, and maintain a strong position in the rapidly evolving EV market. This approach empowers manufacturers to take control of their development processes and ultimately contribute to the overall growth and sustainability of the industry.
The Pioneers of Electric Vehicles: A Historical Journey
You may want to see also
Recycling and Disposal: Vertical integration can include establishing recycling facilities to manage end-of-life batteries and promote sustainability
The electric vehicle (EV) battery industry's vertical integration has sparked interest in sustainable practices, particularly in the realm of recycling and disposal. As the demand for EVs rises, so does the need for efficient end-of-life battery management, which is where vertical integration plays a crucial role. By integrating various stages of the battery lifecycle, manufacturers can ensure a more sustainable approach to EV battery production and disposal.
One key aspect of this integration is the establishment of specialized recycling facilities. These facilities are designed to handle the unique challenges associated with EV batteries, which often contain hazardous materials and require specific recycling processes. Vertical integration allows companies to control the entire recycling process, from collecting used batteries to processing and reusing the materials. This ensures that end-of-life batteries are managed responsibly, minimizing environmental impact and maximizing resource recovery.
In these recycling centers, advanced techniques are employed to extract valuable materials such as lithium, cobalt, and nickel. These materials can then be reused in the manufacturing of new batteries or other products, reducing the need for virgin resources. For instance, recycled lithium can be used to produce new battery cells, contributing to a circular economy and reducing the industry's reliance on finite natural resources.
Furthermore, vertical integration enables companies to develop comprehensive disposal strategies. This includes implementing proper storage and transportation methods for used batteries to prevent environmental contamination. By controlling the entire disposal process, manufacturers can ensure that batteries are handled and disposed of in compliance with environmental regulations, reducing the risk of soil and water pollution.
In summary, vertical integration in the EV battery industry fosters a more sustainable approach to recycling and disposal. By establishing dedicated recycling facilities and controlling the entire lifecycle, manufacturers can effectively manage end-of-life batteries, extract valuable materials, and minimize environmental impact. This integration is essential for the long-term viability of the EV industry and its commitment to reducing the ecological footprint associated with battery production and disposal.
Toyota's Electric Revolution: Rumors of an EV in the Works
You may want to see also
Market Strategy: Integrating sales, marketing, and distribution channels to control the entire customer journey and maintain a competitive edge
The electric vehicle (EV) battery industry is a complex and rapidly evolving market, and understanding the dynamics of vertical integration is crucial for companies aiming to gain a competitive advantage. Vertical integration in this context refers to the strategic alignment and control of various stages of the supply chain, from raw material sourcing to the final product delivery. In the EV battery sector, this can involve a company's efforts to manage its own or its suppliers' production, distribution, and sales processes.
One key aspect of vertical integration in the EV battery industry is the integration of sales and marketing channels. By controlling these channels, companies can ensure a seamless and consistent customer experience. This includes building strong relationships with retailers and dealers, especially in the case of original equipment manufacturers (OEMs) who sell batteries directly to vehicle manufacturers. OEMs can leverage their brand power and customer base to negotiate favorable terms with retailers, ensuring their batteries are prominently displayed and well-marketed. This level of control allows companies to influence customer perceptions and build brand loyalty.
Distribution is another critical component of vertical integration. Efficient distribution networks can significantly impact customer satisfaction and the overall success of a product. Companies can optimize their distribution channels by establishing direct links with customers, reducing the need for intermediaries. This approach can lead to faster delivery times, better inventory management, and improved customer service. For instance, some EV battery manufacturers have invested in their own logistics and distribution networks, allowing them to offer customized solutions and respond quickly to market demands.
Furthermore, integrating sales, marketing, and distribution channels enables companies to gather valuable customer data and insights. By analyzing sales patterns, marketing campaign effectiveness, and customer feedback, businesses can make data-driven decisions to improve their products and services. This level of integration allows for a more responsive and agile approach to market changes, ensuring that the company can quickly adapt to customer needs and stay ahead of the competition.
In summary, the electric vehicle battery industry's adoption of vertical integration strategies can provide a significant competitive edge. By controlling sales, marketing, and distribution channels, companies can enhance customer satisfaction, improve operational efficiency, and make informed decisions based on real-time data. This approach allows businesses to navigate the challenges of a dynamic market and establish a strong presence in the EV battery sector.
Electric Revolution: Overcoming Barriers to Mass Adoption
You may want to see also
Frequently asked questions
Vertical integration refers to the control or ownership of multiple stages in a production or supply chain by a single company. In the electric vehicle (EV) battery industry, this could mean a company owning or controlling both the raw material extraction, manufacturing, assembly, and even the end-user product or service.
Vertical integration can provide several advantages. Firstly, it ensures a consistent quality of materials and products throughout the supply chain, as the company has direct control over each stage. This can lead to improved efficiency, reduced costs, and faster product development cycles. Secondly, it allows for better customization and tailoring of products to meet specific customer needs, as the company can integrate feedback from various stages of production.
While vertical integration has its benefits, it also comes with certain challenges. One potential issue is the high initial investment required to establish control over multiple stages of production. This may lead to financial strain, especially for smaller companies. Additionally, maintaining control over the entire supply chain can be complex and time-consuming, requiring dedicated resources and expertise.
Some companies may not have the resources or desire to own every stage of production, but they can still achieve vertical integration through strategic partnerships, joint ventures, or supply chain management. For instance, a company might collaborate with raw material suppliers to ensure consistent quality, or they could develop long-term contracts with manufacturers to secure production capacity. This approach allows for a more flexible and collaborative vertical integration strategy.