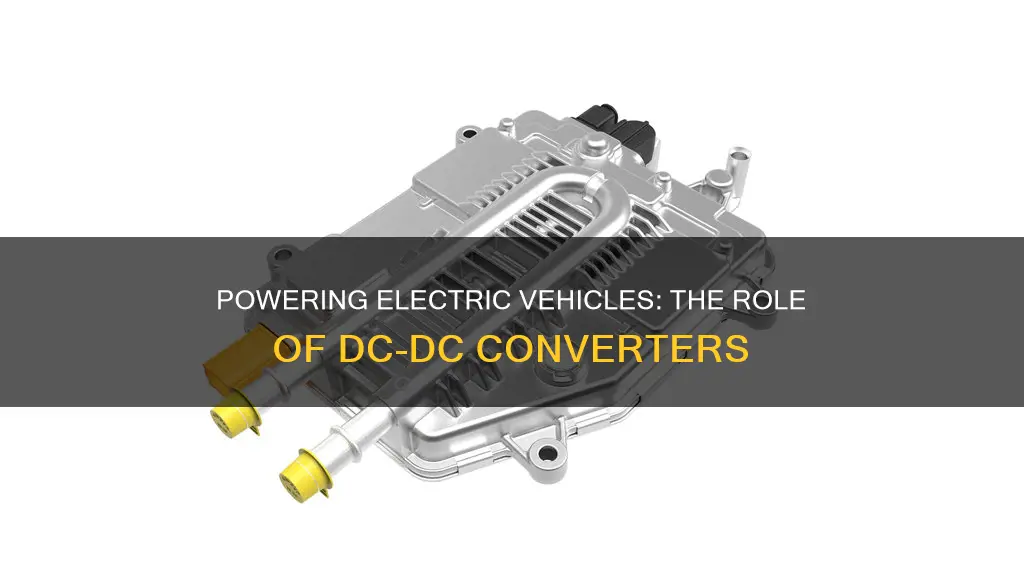
A DC-DC converter is a crucial component in electric vehicles (EVs), playing a vital role in managing power distribution and efficiency. It is a type of electronic device that converts direct current (DC) from one voltage level to another, ensuring that the EV's battery pack can supply the appropriate voltage to various electrical systems and components. This converter is essential for optimizing power usage, enabling efficient charging, and maintaining stable voltage levels throughout the vehicle's electrical architecture. By converting and regulating voltage, the DC-DC converter contributes to the overall performance and reliability of electric vehicles.
Characteristics | Values |
---|---|
Definition | A DC-DC converter is a power electronic device that converts a direct current (DC) voltage from one level to another. In electric vehicles (EVs), it is used to regulate and optimize the voltage and power levels within the battery pack and the electrical system. |
Function | The primary function is to step down the high voltage from the battery pack to a lower voltage required by various vehicle components like motors, inverters, and accessories. It also provides isolation, protection, and efficient power management. |
Efficiency | High efficiency is crucial, typically above 90%, to minimize energy losses during the conversion process. |
Size and Weight | Due to space constraints in EVs, these converters are designed to be compact and lightweight while maintaining high performance. |
Protection | Built-in protection mechanisms include over-voltage, over-current, short-circuit, and thermal protection to ensure safe operation and prevent damage to the vehicle's electrical system. |
Regulation | Precise voltage regulation is essential to maintain stable power supply to the vehicle's components, ensuring optimal performance and longevity. |
Isolation | Provides electrical isolation between the battery and the load, enhancing safety and allowing for efficient power distribution. |
Switching Frequency | Operates at high switching frequencies, typically in the range of 100 kHz to 1 MHz, to achieve fast response times and efficient power conversion. |
Applications | Used in various EV systems, including battery management, motor control, charging systems, and power electronics integration. |
Advantages | Enables efficient power distribution, reduces weight and size of the electrical system, and improves overall vehicle performance and range. |
What You'll Learn
- Principle: DC-DC converters in EVs convert voltage to regulate power efficiently
- Efficiency: These converters optimize energy use, reducing waste heat
- Topologies: Different converter topologies offer unique advantages for EV systems
- Regulation: Voltage regulation ensures stable power supply for EV electronics
- Integration: DC-DC converters seamlessly integrate with EV battery systems
Principle: DC-DC converters in EVs convert voltage to regulate power efficiently
DC-DC converters play a crucial role in electric vehicles (EVs) by enabling efficient voltage conversion and power regulation. These converters are essential components of the vehicle's power electronics system, ensuring that the electrical energy stored in the battery is utilized optimally throughout the vehicle's various systems. The primary function of a DC-DC converter in an EV is to adjust the voltage levels to meet the specific requirements of different electrical loads and subsystems.
In an EV, the battery typically operates at a higher voltage than what is needed for most onboard systems. For instance, a common battery voltage in EVs might be around 300-400 volts, while many onboard devices and motors require lower voltages for efficient operation. This is where the DC-DC converter comes into play. It takes the high-voltage DC input from the battery and converts it into the desired lower voltage DC output. This process is essential for ensuring that the vehicle's electrical systems, such as the motor, charging system, and accessories, receive the appropriate voltage levels.
The principle of operation involves switching the input voltage on and off at a specific frequency, which is controlled by a feedback loop. This switching action allows the converter to regulate the output voltage by adjusting the duty cycle of the switch. When the duty cycle is increased, more of the input voltage is transferred to the output, resulting in a higher output voltage. Conversely, a decreased duty cycle reduces the output voltage. This dynamic control enables the DC-DC converter to provide the necessary voltage regulation for various EV subsystems.
Efficiency is a critical aspect of DC-DC converters in EVs. These converters are designed to minimize power losses during the conversion process. They achieve this through the use of high-frequency switching and advanced switching techniques, such as pulse-width modulation (PWM). PWM allows the converter to create a smooth and continuous output voltage by rapidly switching the input voltage on and off, effectively reducing energy losses and improving overall system efficiency.
Furthermore, DC-DC converters contribute to the overall performance and range of electric vehicles. By efficiently managing voltage levels, these converters ensure that the vehicle's electrical systems operate optimally, maximizing the utilization of the available battery power. This efficient power regulation is vital for maintaining the vehicle's performance, especially during acceleration and when powering various accessories. In summary, DC-DC converters in EVs are essential for voltage conversion, power regulation, and overall system efficiency, playing a significant role in the successful operation of electric vehicles.
Electric Vehicles: Are They Worth the Price Tag?
You may want to see also
Efficiency: These converters optimize energy use, reducing waste heat
In electric vehicles (EVs), efficiency is a critical factor in maximizing the range and performance of the vehicle. One key component that contributes to this efficiency is the DC-DC converter. These converters play a vital role in managing the electrical power within the vehicle, ensuring that energy is utilized effectively and minimizing waste heat generation.
The primary function of a DC-DC converter is to regulate and convert the direct current (DC) voltage in an EV's power system. EVs typically operate on high-voltage DC power, which is supplied by the battery pack. However, different components within the vehicle, such as motors, sensors, and electronic controls, require specific voltage levels. Here, the DC-DC converter steps in to adjust the voltage, ensuring that each component receives the appropriate amount of power. This process is essential for maintaining optimal performance and efficiency.
Efficiency in DC-DC converters is achieved through several design and operational techniques. Firstly, these converters utilize advanced switching topologies, such as buck, boost, and buck-boost converters, which enable precise voltage regulation. By employing high-frequency switching, they can rapidly adjust the output voltage, ensuring that the power supply remains stable and efficient. This dynamic voltage control is crucial for managing the varying power demands of the EV's components.
Additionally, DC-DC converters incorporate features like power loss minimization and high-frequency transformer designs. These elements help reduce energy losses during the conversion process, which are often in the form of heat. By minimizing power losses, the converters ensure that more of the electrical energy is utilized for the vehicle's intended functions, thereby improving overall efficiency.
The benefits of efficient DC-DC converters in EVs are significant. By optimizing energy use, these converters contribute to increased driving range, reduced battery charging times, and improved overall vehicle performance. Moreover, the reduced waste heat generated by the converters can lead to more efficient cooling systems, further enhancing the vehicle's efficiency and reliability. This technology is a crucial enabler in the development of more sustainable and high-performing electric vehicles.
Jeep's Electric Revolution: Rumors of a Green Future
You may want to see also
Topologies: Different converter topologies offer unique advantages for EV systems
The DC-DC converter is a crucial component in electric vehicles (EVs), playing a vital role in managing the power flow and voltage levels within the vehicle's electrical system. These converters are essential for optimizing the performance and efficiency of EVs by converting the high-voltage direct current (DC) from the battery to the appropriate lower voltage levels required by various vehicle subsystems. This process ensures that the electrical components receive the correct voltage, enabling efficient operation and maximizing energy efficiency.
There are several topologies or circuit configurations that DC-DC converters can adopt, each offering distinct advantages for EV systems. One common topology is the buck converter, which is highly efficient and suitable for step-down voltage conversion. In this converter, the input voltage is higher than the output voltage, and it operates by reducing the input voltage to a lower level while maintaining a constant output current. Buck converters are known for their simplicity and are often used in EV applications where a stable and regulated lower voltage is required, such as powering the vehicle's accessories and electronics.
Another popular topology is the boost converter, which is designed to increase the input voltage to a higher level. This converter is particularly useful in EVs when the battery voltage needs to be stepped up to power high-current devices or when a higher voltage is required for specific subsystems. Boost converters are efficient and can provide a stable output voltage, making them ideal for applications like charging the vehicle's high-voltage battery pack or powering electric motors.
The buck-boost converter is a versatile topology that combines the features of both buck and boost converters. It can either step up or step down the voltage, depending on the input and output voltage requirements. This converter is advantageous in EVs as it provides flexibility in voltage conversion, allowing for efficient power management in various driving conditions. Buck-boost converters are often used in applications where the voltage needs to be adjusted dynamically, such as in regenerative braking systems or when balancing the vehicle's battery pack.
Additionally, the SEPIC (Single-Ended Primary-Inductive Converter) topology offers unique benefits for EV systems. SEPIC converters provide a fixed output voltage, regardless of the input voltage, and are highly efficient. They are particularly useful in applications where a constant voltage is required, such as powering the vehicle's infotainment system or sensors. The SEPIC converter's ability to maintain a stable output voltage makes it a reliable choice for EV manufacturers.
In summary, different DC-DC converter topologies offer specific advantages for EV systems, allowing for efficient power management and voltage regulation. The choice of topology depends on the specific requirements of the vehicle's electrical system, such as voltage conversion needs, efficiency, and the type of subsystems being powered. Understanding these topologies is essential for engineers and designers to optimize the performance and efficiency of electric vehicles.
The Ultimate Guide to Choosing the Best EV: A Comprehensive Comparison
You may want to see also
Regulation: Voltage regulation ensures stable power supply for EV electronics
Voltage regulation is a critical aspect of electric vehicle (EV) design, ensuring that the power supply remains stable and reliable for the various electronic components within the vehicle. In the context of DC-DC converters, voltage regulation plays a pivotal role in maintaining a consistent output voltage despite variations in input voltage or load conditions. This is particularly important in EVs, where the power electronics system must handle a wide range of operating conditions and provide stable power to the vehicle's electronics.
DC-DC converters are essential components in EV power electronics, responsible for converting the high-voltage DC power from the battery to the lower-voltage DC levels required by various vehicle systems. These converters must regulate the output voltage to ensure that sensitive electronics, such as motors, power controls, and infotainment systems, receive the correct voltage levels. Without proper voltage regulation, these systems could malfunction or even fail, leading to potential safety hazards and reduced vehicle performance.
The primary function of voltage regulation in DC-DC converters is to maintain a constant output voltage, typically around 12V or 24V, depending on the vehicle's design. This is achieved through various control mechanisms, such as feedback loops and switching frequency modulation. When the input voltage fluctuates due to changes in battery charge or load, the converter adjusts its output to maintain a stable voltage level. For instance, if the input voltage drops, the converter might increase the switching frequency to maintain the desired output voltage, ensuring that the vehicle's electronics operate optimally.
In addition to input voltage variations, DC-DC converters must also account for changes in load current. As the vehicle's electronics draw more power, the converter needs to regulate the output voltage to prevent a drop in voltage levels. This is crucial to ensure that the vehicle's systems receive the required power, especially during high-load conditions, such as acceleration or when multiple accessories are in use. Voltage regulation helps prevent voltage sags and ensures that the vehicle's electronics remain functional and efficient.
Advanced voltage regulation techniques in DC-DC converters for EVs include pulse-width modulation (PWM) control and closed-loop feedback systems. PWM control adjusts the duty cycle of the converter, modulating the input voltage to achieve the desired output. Closed-loop feedback systems continuously monitor the output voltage and make real-time adjustments to maintain stability. These techniques enable DC-DC converters to provide highly accurate voltage regulation, ensuring that EV electronics operate within safe and efficient parameters.
Unveiling the Green Myth: Is the Toyota Prius an Electric Car?
You may want to see also
Integration: DC-DC converters seamlessly integrate with EV battery systems
DC-DC converters play a crucial role in electric vehicles (EVs) by efficiently managing power flow between the battery and the electrical system. These converters are designed to integrate seamlessly with EV battery systems, ensuring optimal performance and longevity. The integration process involves careful consideration of various factors to ensure a harmonious and efficient power management system.
When integrating DC-DC converters with EV batteries, engineers focus on minimizing power losses and maximizing efficiency. This is achieved through the use of high-quality components and precise control algorithms. The converters are typically designed to operate within a specific voltage range, and they must be compatible with the battery's voltage output. By matching the converter's input and output voltages, engineers can ensure that power is transferred efficiently without unnecessary losses.
One key aspect of integration is the ability to handle varying loads and power demands. EV batteries supply power to various components, including the electric motor, accessories, and onboard electronics. DC-DC converters must be capable of dynamically adjusting their output power to meet these varying requirements. This flexibility ensures that the EV's electrical system remains stable and responsive, even during sudden changes in power consumption.
The integration process also involves thermal management. DC-DC converters generate heat during operation, and proper cooling mechanisms must be in place to prevent overheating. This is particularly important in EVs, where space is limited, and efficient heat dissipation is essential for overall system reliability. Engineers design cooling systems that effectively dissipate heat from the converters, ensuring they operate within safe temperature limits.
Furthermore, the integration of DC-DC converters with EV battery systems requires careful consideration of safety. These converters must adhere to strict regulations and standards to ensure they do not pose any hazards. This includes implementing protective measures such as short-circuit protection, over-voltage protection, and temperature monitoring. By integrating these safety features, the overall system becomes more robust and reliable, providing peace of mind to EV owners.
Electric Vehicles: The Indian Advantage? Exploring the Benefits
You may want to see also
Frequently asked questions
A DC-DC converter is an essential component in electric vehicles (EVs) that plays a crucial role in managing the electrical power system. It is a type of electronic device that converts a direct current (DC) voltage from one level to another, allowing for efficient power distribution and regulation within the vehicle.
In an electric vehicle, the DC-DC converter takes the high-voltage DC power from the battery pack and converts it to various lower voltage levels required by different subsystems. This conversion ensures that each component, such as the motor, inverter, and accessories, receives the appropriate voltage for optimal performance. The converter also helps in maintaining a stable voltage output, even during varying load conditions.
The primary advantage of a DC-DC converter is its ability to optimize power usage, improve efficiency, and enhance the overall performance of the electric vehicle. It enables the vehicle to operate with multiple voltage levels, making it compatible with various components. Additionally, it helps in reducing energy losses, improving battery life, and ensuring a reliable power supply to critical systems, even during rapid acceleration or regenerative braking.
Yes, DC-DC converters are not exclusive to electric vehicles. They are also used in conventional hybrid vehicles and some internal combustion engine vehicles. In these vehicles, the converter serves a similar purpose, managing voltage levels and ensuring efficient power distribution. However, in EVs, the DC-DC converter's role becomes even more critical due to the high-voltage battery packs and the need for precise voltage regulation.