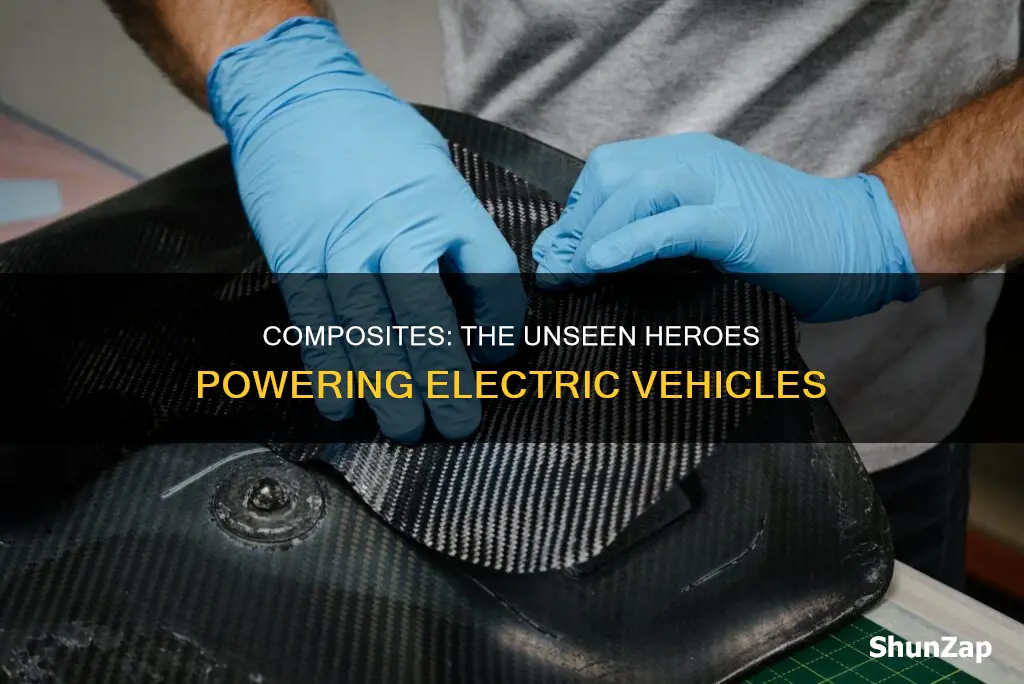
Composites play a crucial role in the development and advancement of electric vehicles (EVs). These innovative materials, which combine two or more substances to create a new material with enhanced properties, offer a range of benefits that contribute to the performance, efficiency, and sustainability of EVs. Composites are utilized in various components of electric vehicles, such as the body structure, battery enclosures, and even in the manufacturing of lightweight electric motors. Their unique characteristics, including high strength-to-weight ratios, excellent thermal management, and the ability to tailor properties for specific applications, make them essential in reducing vehicle weight, improving energy efficiency, and enhancing overall performance. This introduction sets the stage for a deeper exploration of the specific applications and advantages of composites in the electric vehicle industry.
What You'll Learn
- Material Properties: Composites offer lightweight, strong materials for EV components, enhancing performance and efficiency
- Battery Systems: Composite materials are used in battery cells and packs, improving energy density and safety
- Structural Design: Composites enable innovative, lightweight vehicle structures, reducing weight and increasing range
- Electrical Conductivity: Composites with conductive properties are used in wiring harnesses and electronic components
- Recycling and Sustainability: Composite recycling methods and eco-friendly production processes are crucial for EV environmental impact
Material Properties: Composites offer lightweight, strong materials for EV components, enhancing performance and efficiency
Composites have revolutionized the automotive industry, particularly in the realm of electric vehicles (EVs), by providing innovative materials that offer a unique blend of properties. One of the most significant advantages of composites is their ability to provide lightweight yet robust materials, which are essential for enhancing the performance and efficiency of EV components.
In the context of EVs, weight is a critical factor. Heavier vehicles require more energy to accelerate and maintain speed, reducing overall efficiency. Composites, being lightweight, offer a solution to this challenge. For instance, composite materials can be used to manufacture body panels, chassis components, and even battery enclosures. These parts, when made from composites, can significantly reduce the overall weight of the vehicle without compromising on structural integrity. This reduction in weight translates to improved acceleration, better handling, and increased range, all of which are crucial for the success of electric vehicles.
The strength of composite materials is another key aspect. Composites can be engineered to exhibit exceptional mechanical properties, including high tensile strength and stiffness. This makes them ideal for use in load-bearing components such as vehicle frames, wings, and even the body structure. By utilizing composites, manufacturers can ensure that their EVs can withstand the stresses of everyday use, including collisions and varying road conditions, while maintaining a lightweight design.
Furthermore, the design flexibility offered by composite materials allows for innovative and aerodynamic shapes, which can further enhance the performance of EVs. The ability to tailor the properties of composites through various manufacturing techniques, such as fiber orientation and matrix selection, enables engineers to create components that are not only lightweight and strong but also optimized for specific applications.
In summary, composites play a pivotal role in the development of electric vehicles by providing materials that offer a unique combination of lightweight design, strength, and performance. This enables EVs to achieve improved efficiency, better handling, and enhanced overall performance, making them more competitive in the market. As the automotive industry continues to embrace sustainable and innovative solutions, composites will undoubtedly remain a key material of choice for the future of electric mobility.
General Motors' Electric Revolution: A Green Future?
You may want to see also
Battery Systems: Composite materials are used in battery cells and packs, improving energy density and safety
The integration of composite materials in electric vehicle (EV) battery systems is a pivotal innovation that significantly enhances the performance and safety of these vehicles. Battery cells and packs, which are the heart of an EV's power source, benefit immensely from the unique properties of composites. These materials are designed to optimize energy density, a critical factor in the development of more efficient and powerful electric vehicles.
In the context of battery systems, composites are employed to create lightweight yet robust structures. This is particularly important as it directly influences the overall weight of the vehicle. By utilizing composite materials, engineers can reduce the weight of the battery pack without compromising on its structural integrity. Lighter batteries mean improved acceleration and handling, making the EV more responsive and appealing to consumers.
The role of composites in battery cells is multifaceted. Firstly, they contribute to the creation of thin, flexible, and lightweight battery separators. These separators are essential for preventing short circuits and ensuring the safe operation of the battery. Composite materials, such as polyolefin or polyethylene, offer the necessary thermal and chemical stability while maintaining excellent electrical insulation. This results in higher energy density and improved safety, as the risk of thermal runaway is significantly reduced.
Furthermore, composites are used in the manufacturing of battery electrodes. Carbon fiber composites, for instance, are employed in the production of anode materials, providing excellent electrical conductivity and structural support. This enables the creation of more efficient and durable batteries. The use of composites in electrode design also allows for better heat dissipation, which is crucial for maintaining optimal performance and safety during the charging and discharging cycles.
In battery packs, composite materials contribute to the overall design and assembly. Composite casings and enclosures provide protection and insulation, ensuring the safe operation of the battery pack. Additionally, composites can be used to create lightweight and durable mounting systems, allowing for easier integration of the battery into the vehicle's structure. This comprehensive use of composites in battery systems is a testament to their versatility and importance in the advancement of electric vehicles.
Powering Up: A Beginner's Guide to Home EV Charging
You may want to see also
Structural Design: Composites enable innovative, lightweight vehicle structures, reducing weight and increasing range
Composites have revolutionized the structural design of electric vehicles, offering a unique blend of strength, stiffness, and lightweight properties that are essential for enhancing performance and efficiency. In the automotive industry, the primary goal is to create vehicles that are not only powerful but also environmentally friendly, and composites play a pivotal role in achieving this balance.
One of the key advantages of using composites in vehicle construction is their ability to reduce overall weight. Electric vehicles (EVs) heavily rely on efficient weight management to maximize their range. By incorporating composite materials, such as carbon fiber-reinforced polymers (CFRP), into the vehicle's structure, manufacturers can achieve a significant reduction in weight without compromising strength. These composites offer an exceptional strength-to-weight ratio, allowing for the creation of sturdy yet lightweight components. For instance, the body panels, chassis, and even the vehicle's underbody can be designed with composite materials, resulting in a substantial weight decrease compared to traditional metal-based structures.
The innovative use of composites enables designers to create unique and aerodynamic shapes, which are crucial for optimizing the vehicle's performance. The lightweight nature of composites allows for the implementation of complex designs that would be challenging and costly to achieve with conventional materials. This results in improved aerodynamics, reducing drag and further enhancing the vehicle's efficiency. Additionally, the flexibility of composite materials enables the integration of advanced cooling systems, ensuring optimal heat management for the electric motor and battery pack.
In the context of structural design, composites offer a high degree of customization and tailoring to specific vehicle requirements. Engineers can precisely control the material's properties, such as stiffness and strength, by adjusting the fiber orientation and resin systems. This level of control is particularly beneficial for creating tailored structural components, such as the vehicle's floor pan or roof structure, which need to withstand specific loads and stresses. By optimizing the composite's properties, manufacturers can ensure the structural integrity of the vehicle while maintaining its lightweight nature.
Furthermore, the use of composites in electric vehicles contributes to a more sustainable approach to manufacturing. Composite materials can often be recycled, reducing the environmental impact of production and end-of-life disposal. This aspect is crucial for the automotive industry's transition towards more eco-friendly practices. As the demand for electric vehicles continues to grow, the role of composites in structural design will likely become even more prominent, driving innovation and efficiency in the automotive sector.
Understanding Shunting: A Deep Dive into Battery EV Maintenance
You may want to see also
Electrical Conductivity: Composites with conductive properties are used in wiring harnesses and electronic components
The integration of composites with electrical conductivity in electric vehicles (EVs) is a pivotal aspect of modern automotive engineering, offering a range of benefits that contribute to the overall performance and efficiency of these vehicles. Composites, which are materials formed by combining two or more substances, play a crucial role in enhancing the electrical conductivity within various components of EVs.
One of the primary applications of conductive composites in EVs is in the creation of wiring harnesses and electronic components. These harnesses are responsible for transmitting electrical power and signals throughout the vehicle, ensuring that all systems function optimally. Traditional wiring harnesses often relied on copper, a highly conductive metal. However, the use of conductive composites in these harnesses offers several advantages. Composites with conductive properties can provide improved flexibility, allowing for more intricate and adaptable wiring designs. This flexibility is particularly beneficial in the compact and space-constrained environments of modern EVs, where traditional rigid wiring systems might be less efficient.
Conductive composites are engineered to maintain or even enhance electrical conductivity while offering lightweight alternatives to traditional metals. This is a significant advantage in the automotive industry, where weight reduction is essential for improving vehicle performance, especially in terms of acceleration and overall efficiency. By utilizing these composites, manufacturers can create wiring harnesses that are not only more flexible but also contribute to the overall weight reduction of the vehicle. This is a critical factor in the development of more sustainable and environmentally friendly EVs.
In the context of electronic components, conductive composites find application in the manufacturing of circuit boards, sensors, and other electrical devices. These composites enable the creation of lightweight, high-performance components that can withstand the demanding conditions of an EV's operating environment. For instance, composite-based circuit boards can offer improved thermal management, which is crucial for the reliable operation of electronic systems in varying temperatures. Additionally, the use of conductive composites in sensors and actuators can lead to more responsive and accurate control systems, enhancing the overall driving experience.
The development of conductive composites for EVs has been a significant area of research and innovation. Scientists and engineers are continually exploring new materials and manufacturing techniques to optimize electrical conductivity, flexibility, and durability. This includes the use of carbon fibers, graphene, and other advanced materials to create composites with superior properties. As a result, the integration of composites with electrical conductivity is becoming increasingly sophisticated, contributing to the advancement of electric vehicle technology.
Unveiling the Green Revolution: Electric Vehicles' Environmental Impact
You may want to see also
Recycling and Sustainability: Composite recycling methods and eco-friendly production processes are crucial for EV environmental impact
The automotive industry is undergoing a significant transformation with the rise of electric vehicles (EVs), and composite materials are playing a pivotal role in this evolution. Composites, known for their lightweight and high-strength properties, are increasingly used in EV manufacturing, from body panels to battery components. However, the environmental impact of these materials, especially their disposal and recycling, is a critical aspect that requires attention. This is where the concepts of recycling and sustainability come into play, offering solutions to minimize the ecological footprint of EVs.
Recycling composite materials in EVs is a complex process due to the diverse nature of these materials. Composites often consist of a matrix (such as epoxy or polyester) reinforced with fibers like glass, carbon, or aramid. The recycling methods vary depending on the type of composite and the specific application. For instance, glass fiber composites can be recycled through processes like thermal treatment, where the fibers are separated from the matrix and then reprocessed into new materials. This process can significantly reduce the need for virgin resources and minimize the environmental impact of manufacturing.
Eco-friendly production processes are another crucial aspect of sustainability in the EV industry. Manufacturers are increasingly adopting green technologies to reduce the carbon footprint of composite production. One such method is the use of bio-based resins, which are derived from renewable resources like plant oils and sugars. These resins offer similar performance to traditional petroleum-based ones but with a reduced environmental impact. For example, bio-based epoxy resins have shown promising results in composite manufacturing, providing a more sustainable alternative without compromising on strength or durability.
In addition to recycling and eco-friendly production, the design of composite components in EVs can also contribute to sustainability. Engineers are now focusing on designing parts that are easier to disassemble and recycle at the end of their life cycle. This approach, known as 'cradle-to-cradle' design, ensures that the materials used in EVs can be efficiently recovered and reused, further reducing the environmental impact. By implementing these design principles, the automotive industry can move towards a more circular economy, where resources are used efficiently and waste is minimized.
The importance of recycling and sustainable practices in the EV industry cannot be overstated. As the demand for EVs grows, so does the need to address the environmental challenges associated with composite materials. By developing efficient recycling methods, adopting eco-friendly production processes, and implementing sustainable design principles, the automotive sector can significantly reduce its ecological footprint. This not only benefits the environment but also contributes to the long-term viability and acceptance of electric vehicles as a cleaner and more sustainable transportation option.
Ford's Future: Electric Vehicle Cuts and the Industry's Shift
You may want to see also
Frequently asked questions
Composites are materials made by combining two or more substances to create a new material with unique properties. In EVs, composites are utilized in various components, such as body panels, structural elements, and battery enclosures. They offer advantages like reduced weight, improved strength, and enhanced corrosion resistance compared to traditional materials like steel and aluminum.
Composites play a significant role in enhancing the performance of EVs. By using composite materials, manufacturers can achieve a lower vehicle weight, leading to improved acceleration and handling. Composites also enable the design of more aerodynamic shapes, reducing drag and increasing efficiency. Additionally, composites can contribute to better thermal management, allowing for more efficient battery operation.
Yes, composites can have a positive environmental impact in the EV industry. Composite materials often require less energy during manufacturing compared to traditional metals, reducing the carbon footprint. They can also contribute to recycling efforts, as some composites are designed to be recyclable or biodegradable. Furthermore, the lightweight nature of composites can lead to increased energy efficiency in EVs, resulting in lower energy consumption and reduced environmental impact.
While composites offer numerous advantages, there are challenges to be addressed. Manufacturing processes for composites can be complex and require specialized equipment. Ensuring the structural integrity of composite components is crucial, especially in load-bearing applications. Additionally, the cost of composite materials might be higher compared to conventional metals, which could impact the overall vehicle pricing. Manufacturers need to carefully consider the balance between performance benefits and production costs when integrating composites into EV designs.