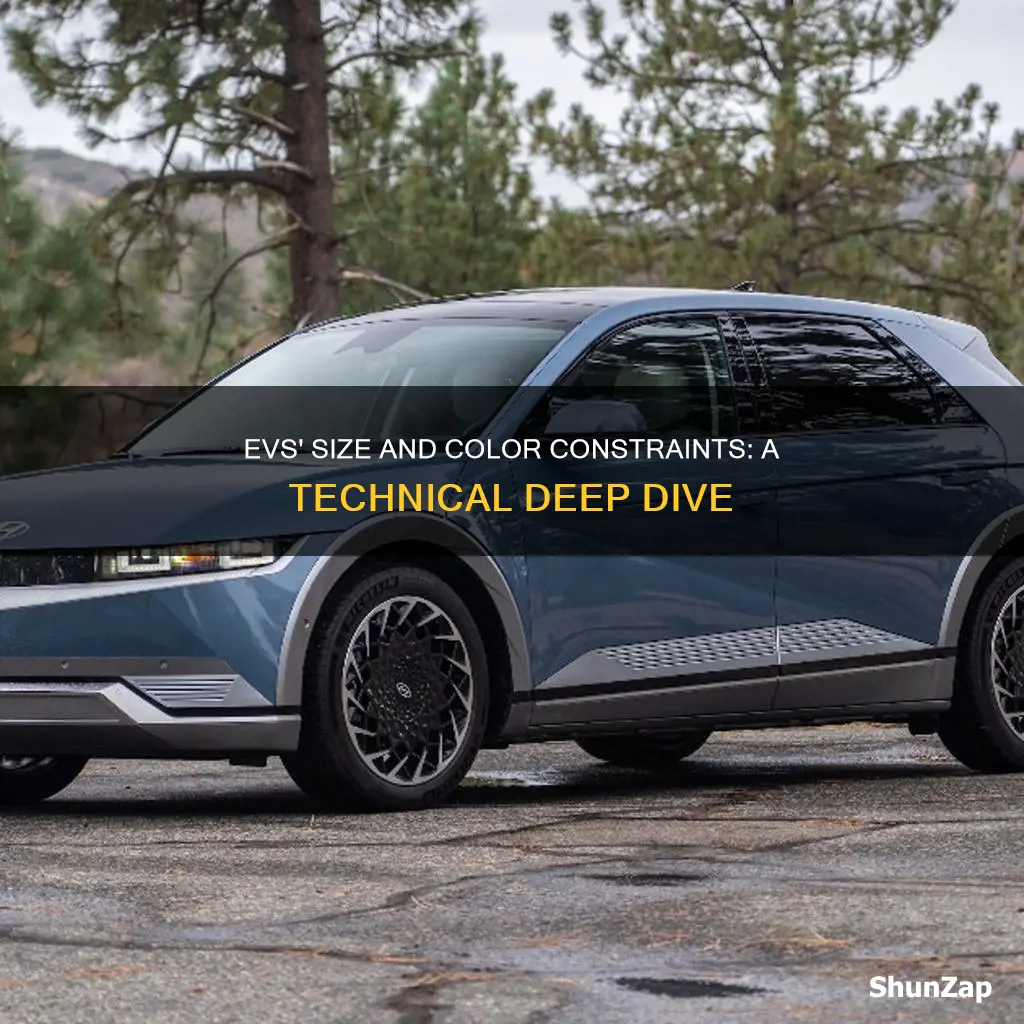
Electric vehicles (EVs) are revolutionizing the automotive industry, but their design and capabilities are often constrained by several factors. One significant limitation is their size, which is primarily due to the placement of the battery pack and the need for efficient cooling systems. The battery pack, being a heavy and space-consuming component, dictates the overall dimensions of the vehicle, making it challenging to create spacious interiors without compromising on performance and range. Additionally, the color options for EVs are often limited due to the materials used in their construction. The lightweight, composite materials employed in EV manufacturing may have restricted color choices, as certain pigments and dyes can be incompatible with these materials, leading to a more limited palette compared to traditional vehicles. These constraints highlight the intricate balance between innovation and practicality in the development of electric vehicles.
What You'll Learn
- Battery Constraints: Limited battery capacity restricts vehicle size and weight
- Aerodynamics: Design must prioritize efficiency, limiting exterior dimensions and color options
- Manufacturing Costs: Smaller, standardized designs reduce production costs and increase profitability
- Range Anxiety: Smaller EVs offer shorter ranges, impacting color and size choices
- Market Demand: Consumer preferences for compact, affordable vehicles influence design and color options
Battery Constraints: Limited battery capacity restricts vehicle size and weight
The primary constraint on the size and weight of electric vehicles (EVs) is the battery. The battery is the heart of an EV, storing the energy that powers the vehicle. However, the technology used in EV batteries has limitations that restrict their size and weight.
Firstly, the energy density of current lithium-ion batteries is relatively low compared to traditional internal combustion engines. This means that to store the same amount of energy, an EV battery will be larger and heavier than a gasoline or diesel tank. For example, a typical EV battery pack might weigh around 400-500 kg, while a similar-sized internal combustion engine weighs much less. This weight is a significant factor in the overall design and engineering of EVs, as it affects the vehicle's center of gravity, handling, and performance.
Secondly, the physical size of the battery itself is limited by the space available within the vehicle's chassis. EVs have a smaller footprint compared to conventional cars due to the absence of an engine and transmission. This reduced space means that the battery must be compact and efficient to fit within the vehicle's structure. As a result, EV manufacturers often have to make trade-offs between battery capacity, vehicle size, and other design considerations.
The limited battery capacity also impacts the range of EVs. While advancements in battery technology have improved range, it remains a critical factor in vehicle design. Longer-range EVs often require larger and heavier batteries, further contributing to the overall size and weight of the vehicle. This is why many EVs are designed with a focus on efficiency and lightweight materials to optimize performance and range.
In summary, the battery is the key constraint that influences the size and weight of electric vehicles. The need for efficient energy storage, combined with physical space limitations, results in EVs often being smaller and lighter than their conventional counterparts. As battery technology continues to evolve, we can expect to see improvements in range and potentially a reduction in the size and weight of EV batteries, leading to more versatile and powerful electric vehicles.
Unraveling VCU: The Brain Behind Electric Vehicle Performance
You may want to see also
Aerodynamics: Design must prioritize efficiency, limiting exterior dimensions and color options
The design of electric vehicles (EVs) is heavily influenced by the need for aerodynamic efficiency, which plays a crucial role in their performance and range. Aerodynamics is a critical factor in the development of EVs, as it directly impacts their energy consumption and overall efficiency. The primary goal is to minimize drag, which is the force that opposes the motion of the vehicle, allowing EVs to travel farther on a single charge. This is achieved through careful consideration of the vehicle's shape, size, and surface design.
One of the key reasons for the limited exterior dimensions of EVs is the requirement for aerodynamic efficiency. Designers aim to create a streamlined shape that reduces air resistance, ensuring that the vehicle can glide through the air with minimal effort. This involves shaping the car's body, roof, and windows to create a smooth, continuous surface that minimizes turbulence. By reducing the frontal area and optimizing the vehicle's profile, engineers can significantly decrease drag, resulting in improved energy efficiency.
Color options are also limited due to aerodynamic considerations. Bright and vibrant colors often require multiple layers of paint, which can increase the vehicle's weight and reduce its overall efficiency. Additionally, certain colors may not provide the necessary camouflage in urban environments, making the vehicle more visible and potentially increasing the risk of accidents. As a result, EV manufacturers often offer a more limited color palette, focusing on neutral and dark shades that provide better aerodynamics and visibility.
The design process involves extensive wind tunnel testing and computational fluid dynamics (CFD) simulations to optimize the vehicle's shape. These methods help engineers identify areas of high drag and make adjustments to improve airflow. For instance, designers might modify the front grille, side mirrors, or rear spoiler to enhance aerodynamics without compromising the vehicle's functionality. The goal is to create a design that is both aesthetically pleasing and highly efficient, ensuring that the EV can travel long distances on a single battery charge.
In summary, the design of electric vehicles is constrained by the need for aerodynamic efficiency, which directly impacts their performance and range. By prioritizing streamlined shapes, minimizing exterior dimensions, and offering limited color options, EV manufacturers aim to reduce drag and improve energy efficiency. This approach ensures that EVs can compete with traditional vehicles in terms of range and practicality, making them a viable and sustainable transportation option for the future.
Mastering EV Battery Care: Tips for Optimal Performance and Longevity
You may want to see also
Manufacturing Costs: Smaller, standardized designs reduce production costs and increase profitability
The manufacturing of electric vehicles (EVs) is a complex process, and one of the key factors influencing their design and production is the cost. Smaller, standardized designs are a strategic approach to reducing manufacturing costs and improving the overall profitability of electric vehicles. This approach is a direct response to the unique challenges and opportunities presented by the EV market.
In the automotive industry, the concept of economies of scale is crucial. Larger vehicles often benefit from reduced per-unit production costs due to the ability to produce more units in a given time frame. However, this is not the case for EVs. The market for electric vehicles is relatively niche, and the demand for these vehicles is often more specific and smaller compared to traditional internal combustion engine (ICE) cars. As a result, manufacturers of EVs need to adopt a different strategy to remain competitive and profitable.
Smaller designs in EVs have multiple advantages. Firstly, they reduce the amount of raw materials required for production. This is especially important for battery-powered vehicles, where the weight and volume of the battery pack are significant factors. By minimizing the size of the vehicle, manufacturers can optimize the use of materials, reduce waste, and lower the overall cost of production. This is a critical aspect of EV manufacturing, as batteries are one of the most expensive components, and any reduction in material usage can significantly impact the bottom line.
Standardization plays a vital role in this process. By adhering to a set of predefined specifications and designs, manufacturers can streamline the production process. This includes the use of interchangeable parts, which further reduces costs. Standardized designs also enable manufacturers to optimize their supply chain, ensuring that components are readily available and can be sourced efficiently. This level of standardization can lead to a more consistent and reliable production process, reducing the time and resources spent on customization and individual vehicle adjustments.
The benefits of this approach extend beyond cost reduction. Smaller, standardized EVs can also lead to increased efficiency in the supply chain and logistics. These vehicles are often designed with modularity in mind, allowing for easier transportation and assembly. This efficiency can result in reduced lead times and improved inventory management, ensuring that the manufacturing process is not only cost-effective but also timely. Ultimately, this strategy enables EV manufacturers to offer competitive pricing, making electric vehicles more accessible to a wider range of consumers.
The Rise of Electric Vehicles: A Green Revolution
You may want to see also
Range Anxiety: Smaller EVs offer shorter ranges, impacting color and size choices
The concept of 'range anxiety' is a significant factor that influences the design and production of electric vehicles (EVs), particularly those with smaller dimensions. This anxiety refers to the fear or worry that an EV's battery will run out of power before reaching its destination, leading to a stressful and potentially dangerous situation for drivers. Smaller EVs, often more compact and lightweight, are designed to address the challenges of urban mobility and environmental sustainability. However, their reduced size directly correlates to a shorter driving range, which can significantly impact the choices available to consumers.
For instance, a smaller EV might offer a range of 100-150 miles on a single charge, which is adequate for daily commutes in urban areas but may not be sufficient for longer journeys or for those who frequently travel to remote locations. This limitation in range can influence the color and size decisions made by manufacturers. On one hand, smaller EVs often have a more limited color palette, as larger vehicles can accommodate a wider range of paint options. This is because the production of smaller EVs is often focused on efficiency and cost-effectiveness, which may not include the same variety of color choices as their larger counterparts.
Additionally, the size of an EV plays a crucial role in its overall performance and range. Smaller EVs tend to have smaller batteries, which directly impact their driving range. A larger battery pack can store more energy, allowing for an extended driving range. However, increasing the battery size also increases the vehicle's weight and overall cost, which can be a trade-off that manufacturers must consider. As a result, the design of smaller EVs often prioritizes practicality and efficiency, leading to a more limited range compared to larger vehicles.
To address range anxiety, some EV manufacturers are developing advanced battery technologies and implementing strategies such as regenerative braking systems, which help to extend the vehicle's range. These innovations aim to provide drivers with peace of mind and reduce the anxiety associated with running out of power. Furthermore, the integration of fast-charging infrastructure is becoming increasingly important, allowing for quicker charging times and reducing the wait time for drivers.
In conclusion, the concept of range anxiety is a critical consideration in the design and production of smaller EVs, influencing the color and size options available to consumers. While smaller EVs offer numerous advantages, such as lower environmental impact and ease of parking, their limited range can be a significant drawback. Manufacturers are continually working on improving battery technology and implementing efficient systems to mitigate range anxiety, ensuring that electric vehicles become a more viable and appealing option for a wide range of drivers.
Powering Your Ride: Understanding Vehicle Electrical Connectors
You may want to see also
Market Demand: Consumer preferences for compact, affordable vehicles influence design and color options
The market demand for electric vehicles (EVs) has been a driving force behind the design and production decisions of manufacturers, particularly in the context of size and color options. Consumer preferences play a pivotal role in shaping the offerings of the EV market, and this is especially true for compact and affordable vehicles.
In the automotive industry, the term "compact" often refers to a vehicle's overall dimensions, including its length, width, and height. Consumers increasingly seek smaller, more maneuverable cars, especially in urban areas where parking spaces are limited and traffic congestion is high. Compact EVs offer the advantage of easier parking, navigation through tight spaces, and reduced environmental impact due to lower energy consumption. This demand for compactness has led manufacturers to focus on designing smaller yet efficient vehicles, ensuring that performance and practicality are not compromised.
Affordability is another critical factor influencing the design and color options of EVs. Many consumers view electric vehicles as a more sustainable and environmentally friendly alternative to traditional gasoline-powered cars. However, the initial cost of purchasing an EV can be a significant barrier, especially for those on a tight budget. To address this, manufacturers often opt for more cost-effective production methods, which may include using fewer color options or offering a limited range of colors. This strategy helps to keep the overall price of the vehicle competitive and accessible to a broader market segment.
Consumer preferences for specific colors and designs can vary widely, and manufacturers must carefully consider these preferences to ensure market success. While some consumers may prefer bolder, more vibrant colors, others might opt for more subtle and neutral tones. The availability of color options can significantly impact a vehicle's perceived value and appeal to potential buyers. By offering a range of colors, manufacturers can cater to diverse tastes, allowing consumers to personalize their EVs and make a statement with their choice of vehicle.
In summary, market demand for compact and affordable electric vehicles has a direct influence on the design and color options available. Manufacturers must balance the need for smaller, more efficient vehicles with consumer preferences for affordability and design choices. This delicate equilibrium ensures that the EV market caters to the needs of environmentally conscious consumers while also providing them with the options they desire. As the market continues to evolve, understanding and responding to these consumer preferences will be crucial for the success of electric vehicle manufacturers.
Battery Swapping: The Future of EV Convenience
You may want to see also
Frequently asked questions
The primary reason for the size limitation of EVs is battery technology. Electric vehicles rely on lithium-ion batteries, which are currently more energy-dense and compact than traditional internal combustion engines. However, batteries are heavy and take up a significant amount of space. To optimize performance and range, EV manufacturers aim to minimize the size of the battery pack while ensuring it fits within the vehicle's structure. Smaller EVs also have advantages in terms of agility, easier parking, and lower material costs.
While electric vehicles do not have inherent limitations on color choices, there can be practical considerations. The color of an EV is often determined by the available paint options from the manufacturer. Some brands offer a wide range of colors, while others may have more limited palettes. Additionally, certain colors might require additional preparation or special painting techniques, which can impact production timelines and costs. However, with advancements in technology, the automotive industry is constantly working on improving color options and customization for electric vehicles.
The choice of solid colors for electric vehicles is primarily due to practical and aesthetic reasons. Solid colors are easier to apply and maintain, especially when compared to metallic or pearl-effect paints. These specialized paints can be more challenging to spray and may require additional layers or treatments. Additionally, solid colors offer a cleaner and more modern look, which aligns with the contemporary design language of many electric car models. However, this trend is not set in stone, and some manufacturers are exploring innovative ways to offer a diverse range of color options for their electric vehicle lineup.