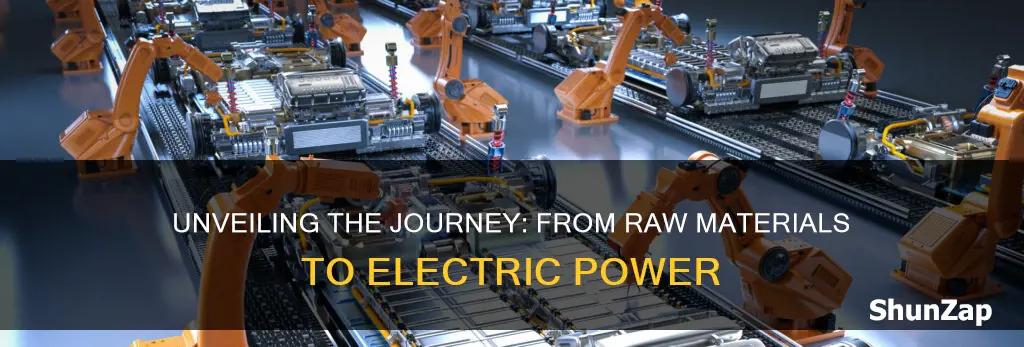
The production of batteries for electric vehicles (EVs) is a complex and intricate process that involves multiple stages and specialized materials. These batteries are designed to store and release energy efficiently, powering the vehicle's electric motor. The manufacturing process typically begins with the selection of raw materials, including lithium, cobalt, nickel, and manganese, which are extracted and refined to create the battery's core components. These materials are then assembled into cells, which are the building blocks of the battery, through a precise and controlled process. Each cell is carefully constructed, often involving the layering of electrodes, separators, and electrolytes, before being sealed and tested to ensure optimal performance and safety. The cells are then combined into modules and packs, which are further integrated into the EV's chassis, requiring advanced engineering to manage the weight, size, and cooling requirements of these powerful energy storage systems.
What You'll Learn
- Electrode Materials: Selection and preparation of materials like lithium cobalt oxide for cathodes and graphite for anodes
- Electrolyte Solutions: Liquid, gel, or solid electrolytes enable ion movement between electrodes
- Battery Cell Design: Architecture and arrangement of electrodes, separators, and current collectors
- Manufacturing Processes: Techniques like casting, coating, and rolling for electrode production
- Safety Features: Incorporation of safety mechanisms to prevent overheating, overcharging, and short circuits
Electrode Materials: Selection and preparation of materials like lithium cobalt oxide for cathodes and graphite for anodes
The selection and preparation of electrode materials are critical steps in the manufacturing of batteries for electric vehicles (EVs). These materials directly impact the battery's performance, energy density, and overall efficiency. For cathodes, lithium cobalt oxide (LiCoO2) is a commonly used material due to its high energy density and stability. This material is carefully synthesized through a process known as sol-gel or co-precipitation, where lithium, cobalt, and oxygen precursors are mixed and then heated to form a gel-like structure. This gel is then aged and dried, and finally, heat-treated to create the desired crystal structure. The preparation involves precise control of the composition and particle size to ensure optimal performance.
For anodes, graphite is a popular choice due to its excellent charge-discharge capabilities and stability. The preparation of graphite electrodes involves a process called exfoliation, where natural graphite is treated with strong acids to create thin graphite sheets. These sheets are then stacked and bound together to form the anode structure. The key to achieving high-performance anodes is to control the thickness and quality of the graphite layers, ensuring they can accommodate lithium ions during charging and discharging without degrading.
The selection of electrode materials is a complex process, considering various factors. For cathodes, the choice depends on the desired voltage, energy density, and thermal stability. Lithium nickel manganese cobalt oxide (NMC) and lithium iron phosphate (LFP) are alternative cathode materials, offering advantages in terms of safety and cost. NMC provides a higher voltage and improved thermal stability, while LFP is known for its long cycle life and safety. These materials are prepared through similar synthesis methods, ensuring consistent performance.
Anode materials also play a crucial role in battery performance. Silicon-based materials, for instance, offer a higher theoretical capacity than graphite but are more reactive. To mitigate this, silicon anodes are often coated with carbon or other materials to enhance stability. Additionally, research is ongoing to explore new anode materials like lithium metal, which, when paired with a suitable cathode, could significantly increase energy density.
In summary, the preparation of electrode materials is a meticulous process that involves the selection of specific compounds and the application of various synthesis techniques. The goal is to create electrodes that can efficiently store and release energy while maintaining stability and longevity, ultimately contributing to the overall performance and reliability of electric vehicle batteries.
Unveiling the Future: Understanding the Electrical Vehicle Revolution
You may want to see also
Electrolyte Solutions: Liquid, gel, or solid electrolytes enable ion movement between electrodes
The development of advanced electrolytes is a critical aspect of battery technology, especially for electric vehicles (EVs), as it directly impacts the performance, safety, and longevity of the battery. Electrolytes are essential components that facilitate the movement of ions between the electrodes, enabling the flow of electrical current within the battery. These solutions can be in the form of liquids, gels, or solids, each with its own advantages and challenges.
Liquid electrolytes have been traditionally used in batteries and offer several benefits. They typically provide good ionic conductivity, allowing for efficient ion movement between the electrodes. This type of electrolyte is often a liquid salt solution, where the salt dissociates into ions, facilitating the electrical charge transfer. For instance, lithium salt solutions, such as lithium hexafluorophosphate (LiPF6) or lithium bis(trifluoromethane)sulfonimide (LiTFSI), are commonly used in lithium-ion batteries. These liquid electrolytes have been widely adopted in the EV industry due to their high energy density and relatively low cost. However, they do present some challenges, such as the risk of leakage and the potential for thermal instability, especially at high temperatures.
To address some of the limitations of liquid electrolytes, researchers have explored the use of gel electrolytes. Gel electrolytes are created by incorporating a thickening agent into the liquid electrolyte, resulting in a semi-solid or gel-like state. This modification can enhance the safety of the battery by reducing the risk of electrolyte leakage and improving thermal stability. Gel electrolytes often maintain good ionic conductivity, ensuring efficient ion transport. For example, polyacrylate-based gels have been used in lithium-ion batteries, offering improved safety and thermal stability compared to liquid electrolytes. The gel form can also provide better mechanical stability, making it suitable for various battery designs.
Solid electrolytes represent another exciting avenue in battery technology. These electrolytes eliminate the need for a liquid or gel medium, instead relying on a solid material to facilitate ion movement. Solid-state batteries offer potential advantages such as higher energy density, improved safety, and longer cycle life. For instance, polymer electrolytes, like poly(ethylene oxide) (PEO) or poly(vinylidene fluoride) (PVDF), can conduct ions in the solid state. Additionally, ceramic materials, such as lithium aluminum silicate (LiAlSi) or lithium lanthanum titanium oxide (LLTO), have shown promise as solid electrolytes. Solid electrolytes can provide enhanced safety by reducing the risk of fire and explosion associated with liquid electrolytes. However, they may face challenges related to lower ionic conductivity compared to liquid or gel electrolytes, which can impact the overall battery performance.
The choice of electrolyte material depends on various factors, including the specific battery chemistry, desired performance characteristics, and safety requirements. Liquid electrolytes offer good conductivity and energy density but may require additional safety measures. Gel electrolytes provide improved safety and thermal stability, making them suitable for certain battery applications. Solid electrolytes, while presenting unique challenges, offer the potential for significant advancements in energy density and safety. Ongoing research and development efforts are focused on optimizing these electrolyte solutions to meet the demanding requirements of electric vehicle batteries.
Electric Vehicles in Brookhaven: A Comprehensive Guide
You may want to see also
Battery Cell Design: Architecture and arrangement of electrodes, separators, and current collectors
The design of battery cells for electric vehicles (EVs) is a critical aspect of their performance and efficiency. At the heart of this design are the components that directly influence the battery's energy storage and release capabilities: the electrodes, separators, and current collectors. Each of these elements plays a unique role in the overall architecture of the battery cell.
Electrodes: These are the primary components responsible for the chemical reactions that occur during charging and discharging. Typically, lithium-ion batteries use two electrodes: an anode and a cathode. The anode is where lithium ions are oxidized during discharge, and the cathode is where they are reduced. The choice of materials for these electrodes is crucial. For anodes, materials like graphite, lithium metal oxide, or silicon-based compounds are often used. Graphite, for instance, offers a high specific capacity and excellent cycle life, making it a popular choice. On the other hand, cathodes can be made from lithium metal phosphate, lithium manganese oxide, or nickel-based compounds, each offering different advantages in terms of energy density and stability. The electrode design also involves creating a porous structure to facilitate the movement of ions and electrons, ensuring efficient charge and discharge processes.
Separators: These thin, porous membranes are positioned between the electrodes to separate them while allowing the movement of ions. The primary function of separators is to prevent electrical contact between the electrodes while facilitating the transport of lithium ions. They are typically made of polymer materials, such as polyolefin or polyethylene oxide, which provide high ionic conductivity and mechanical stability. The separator's thickness and porosity are carefully controlled to balance the battery's performance. Thinner separators allow for higher energy density but may lead to increased safety risks due to reduced thermal stability. Porosity, on the other hand, affects the separator's ability to absorb and release electrolytes during charging and discharging.
Current Collectors: These are conductive materials that collect the electrical current generated or consumed by the electrodes. In a battery cell, current collectors are typically made of metal foils, such as copper or aluminum. For the anode, a copper current collector is often used to efficiently collect the electrons released during the discharge process. Similarly, a cathode current collector, usually made of aluminum, collects the electrons returning to the battery during charging. The arrangement of these current collectors is crucial for maintaining a uniform current density across the entire electrode surface, ensuring optimal performance and longevity.
The arrangement of these components within the battery cell design is a complex process. Electrodes are often stacked or wound to create a compact structure, with separators interleaved between them. This arrangement ensures that the active materials are in close contact with the current collectors, facilitating efficient charge transfer. The choice of stacking or winding configuration depends on the specific battery chemistry and desired performance characteristics. For instance, a wound configuration might be used for high-power applications, while a stacked design could be more suitable for high-energy density requirements.
In summary, the design of battery cells for electric vehicles involves a meticulous arrangement of electrodes, separators, and current collectors, each contributing to the overall performance and efficiency of the battery. The choice of materials and their arrangement directly impact the battery's energy storage capacity, power output, and safety. As technology advances, engineers continue to refine these designs to meet the ever-increasing demands of the EV market.
EV Tax Credit: Income-Based Phasing Out Explained
You may want to see also
Manufacturing Processes: Techniques like casting, coating, and rolling for electrode production
The manufacturing of batteries for electric vehicles involves a complex process that utilizes various techniques to ensure high-performance and long-lasting energy storage systems. One crucial aspect is the production of electrodes, which are fundamental components of the battery's ability to store and release energy. Here, we delve into the manufacturing processes, specifically focusing on the techniques of casting, coating, and rolling for electrode creation.
Casting is an initial step in electrode manufacturing, where active materials, such as lithium cobalt oxide (LCO) or lithium iron phosphate (LFP), are melted and poured into molds. This process allows for the precise shaping of the electrode material. The molten mixture is carefully controlled to ensure the desired composition and purity. After casting, the material is rapidly cooled, often using advanced cooling techniques to minimize the formation of large crystals, which can impact performance. This step is critical as it sets the foundation for the electrode's structure and properties.
Coating is a subsequent process that enhances the electrode's performance and longevity. It involves applying a thin layer of conductive material, typically a metal oxide or a conductive polymer, onto the cast active material. This coating serves multiple purposes: it improves the electrode's conductivity, facilitates the movement of ions during charging and discharging, and provides a protective barrier against degradation. The coating process can be achieved through various methods, including physical vapor deposition (PVD) or wet chemical methods, ensuring a uniform and adherent layer.
Rolling is a critical technique employed to transform the coated electrode material into a thin, flexible sheet. This process involves passing the coated material through a series of rollers, applying pressure and heat to achieve the desired thickness. The rolling process is meticulous, requiring precise control of speed, temperature, and pressure to maintain the integrity of the active material and the coating. Thicker electrodes are often rolled first, and then thinner layers are added to achieve the required electrode thickness for the battery cell. This technique is essential for creating electrodes with the optimal surface area and porosity, allowing for efficient electrochemical reactions.
These manufacturing processes are carefully orchestrated to produce high-quality electrodes that meet the demanding requirements of electric vehicle batteries. The combination of casting, coating, and rolling techniques enables the creation of electrodes with the right composition, structure, and properties, ultimately contributing to the overall performance, safety, and longevity of the battery. Each step requires precision and expertise to ensure the final product is fit for the challenging conditions of electric vehicle operation.
Tesla: The Ultimate Battery Electric Vehicle?
You may want to see also
Safety Features: Incorporation of safety mechanisms to prevent overheating, overcharging, and short circuits
The safety of electric vehicle (EV) batteries is paramount, and several critical safety features are incorporated into their design and manufacturing processes to prevent overheating, overcharging, and short circuits. These features are essential to ensure the reliability and longevity of EV batteries while also safeguarding against potential hazards.
One key safety mechanism is the use of thermal management systems. These systems actively monitor and control the temperature of the battery pack. They employ various techniques such as cooling fins, liquid cooling, or even phase-change materials to dissipate heat. By maintaining optimal operating temperatures, the risk of overheating is significantly reduced, which can lead to thermal runaway, a dangerous situation where the battery's temperature rises uncontrollably. Thermal management systems are especially crucial during charging and high-load driving conditions.
Overcharging protection is another vital safety feature. EV batteries are equipped with sophisticated charging systems that include smart sensors and microcontrollers. These systems monitor the battery's voltage and current levels during the charging process. If the battery's voltage exceeds a safe threshold, the charging process is automatically halted to prevent overcharging. Overcharging can cause damage to the battery's cells and potentially lead to safety hazards, including gas formation and increased fire risk.
Short-circuit protection is designed to safeguard against electrical faults. This feature involves implementing safety circuits and fuses that can detect and interrupt a short circuit. When a short circuit occurs, such as a damaged cable or a faulty component, the safety circuit triggers a rapid response, cutting off power to the affected area. This prevents excessive current flow, which could lead to overheating, fire, or even explosion. Short-circuit protection is critical in ensuring the overall safety of the EV battery system.
Additionally, advanced battery management systems (BMS) play a pivotal role in safety. BMS continuously monitors the battery's performance, including voltage, current, temperature, and state of charge. It provides real-time data and analytics, allowing for proactive safety measures. For instance, if a cell temperature exceeds a safe limit, the BMS can activate cooling mechanisms or even isolate the affected cell to prevent further issues. BMS also optimizes charging and discharging processes, ensuring they remain within safe parameters.
In summary, the safety features of EV batteries are comprehensive and essential for their reliable operation. From thermal management systems to overcharging and short-circuit protection, these mechanisms work together to prevent overheating, overcharging, and short circuits, ultimately ensuring the safety and longevity of electric vehicle batteries.
China's EV Subsidies: A Boost for Green Cars or a Hidden Cost?
You may want to see also
Frequently asked questions
The primary materials used in EV batteries include lithium, cobalt, nickel, manganese, and graphite. These materials are carefully selected and combined to create the cathode and anode, which are the key components of the battery cell.
Battery cells are designed with multiple layers, including a cathode, anode, separator, and current collectors. The cathode is typically made of a mixture of lithium cobalt oxide (LCO) or lithium nickel manganese cobalt oxide (NMC), while the anode is made of graphite. The separator is a porous membrane that allows ions to pass through while preventing electrical contact between the electrodes.
Manufacturing involves several steps. First, the raw materials are processed and mixed to create the cathode and anode materials. These are then coated onto current collectors and assembled into cells. The cells are stacked together to form modules, which are then integrated into battery packs. Each step requires precise control of temperature and pressure to ensure the quality and safety of the battery.
Testing and quality control are crucial in the production of EV batteries. Cells are subjected to various tests, including electrical performance tests, cycle life tests, and safety tests. These tests ensure that the batteries meet the required specifications and safety standards. Additionally, manufacturers use advanced inspection techniques, such as X-ray and ultrasound, to identify any defects or imperfections in the battery structure.