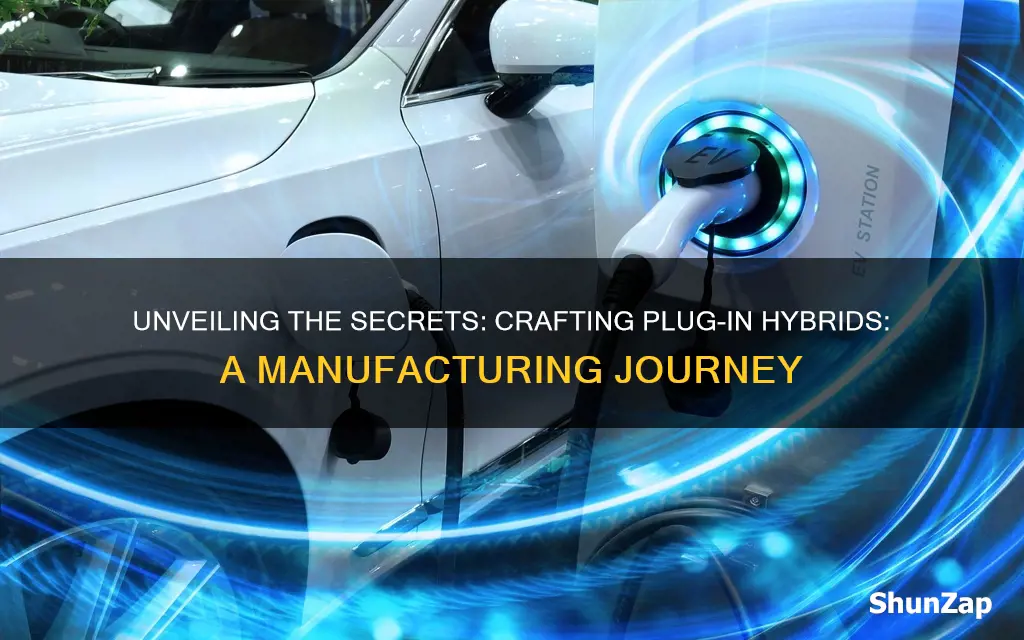
Plug-in hybrid electric vehicles (PHEVs) are innovative automobiles that combine a traditional internal combustion engine with an electric motor and a high-capacity battery. The manufacturing process of PHEVs involves several key steps. Firstly, the vehicle's body and chassis are assembled, ensuring a sturdy and lightweight structure. Next, the hybrid powertrain, consisting of the electric motor, battery pack, and internal combustion engine, is integrated into the vehicle. This powertrain allows for both electric-only driving and a seamless transition between the two power sources. The manufacturing process also includes the installation of advanced electronics and control systems, which manage the energy flow and optimize performance. Finally, the interior and exterior components are fitted, including the dashboard, seats, and exterior styling, to create a comfortable and aesthetically pleasing driving experience. The production of PHEVs requires a meticulous and specialized assembly process to achieve the balance between electric efficiency and traditional performance.
What You'll Learn
- Engine and Transmission: Integrating a conventional engine with an electric motor and transmission
- Battery Pack: Designing and manufacturing a high-capacity battery pack for energy storage
- Power Electronics: Managing power flow between the battery, motor, and engine
- Hybrid Control Unit: Software for optimizing energy usage and performance
- Body and Aerodynamics: Streamlining the vehicle's design for improved efficiency
Engine and Transmission: Integrating a conventional engine with an electric motor and transmission
The integration of a conventional internal combustion engine (ICE) with an electric motor and transmission is a crucial aspect of plug-in hybrid electric vehicle (PHEV) design. This process involves carefully combining these components to ensure optimal performance, efficiency, and smooth operation. Here's a detailed breakdown of this integration process:
Engine and Motor Integration: In a PHEV, the ICE and electric motor are often integrated to provide a seamless power source for the vehicle. The ICE, typically a gasoline or diesel engine, is designed to work in conjunction with the electric motor. When the vehicle is in hybrid mode, the ICE and electric motor can operate independently or in parallel. During parallel operation, the electric motor provides additional power to the wheels, while the ICE can act as a generator, recharging the battery or providing extra torque. This integration allows for efficient power distribution and ensures that the vehicle can operate in both electric-only and hybrid modes.
Transmission Design: The transmission plays a vital role in managing the power flow between the ICE, electric motor, and the wheels. In PHEVs, transmissions are often designed to handle the dual power sources. A typical transmission system includes a multi-speed automatic or manual transmission, which routes power from the ICE or electric motor to the drive train. The transmission's gear ratios are carefully selected to optimize performance and efficiency across various driving conditions. During electric-only mode, the transmission may direct power directly to the wheels, bypassing the ICE. In hybrid mode, it manages the power split between the ICE and electric motor, ensuring smooth acceleration and efficient energy usage.
Start-Stop Technology: An essential feature of PHEVs is the ability to shut down the ICE during stops and restart it when needed. This is achieved through start-stop technology, which integrates the ICE and transmission to optimize fuel efficiency. When the vehicle comes to a stop, the ICE and electric motor are synchronized to shut down, and the vehicle relies on the electric motor or regenerative braking to power the accessories and maintain battery charge. When the driver needs to accelerate, the ICE restarts, and the transmission shifts to the appropriate gear to provide the required power.
Energy Management System: The integration of the ICE, electric motor, and transmission is controlled by an advanced energy management system. This system monitors the vehicle's speed, battery charge, and driver input to determine the optimal power distribution. It adjusts the ICE's speed, torque, and fuel injection to match the electric motor's output, ensuring a smooth and efficient driving experience. The energy management system also optimizes energy recovery during braking, capturing and storing energy in the battery.
Performance and Efficiency: The successful integration of these components results in improved performance and fuel efficiency. PHEVs can offer better acceleration and higher top speeds compared to conventional vehicles due to the combined power of the ICE and electric motor. Additionally, the efficient energy management system ensures that the vehicle can travel longer distances in electric-only mode, reducing fuel consumption and emissions.
Unleash the Power: 5 Signs to Identify Your Hybrid Electric Vehicle
You may want to see also
Battery Pack: Designing and manufacturing a high-capacity battery pack for energy storage
The battery pack is a critical component of plug-in hybrid electric vehicles (PHEVs), as it stores the energy required to power the vehicle during electric-only driving modes. Designing and manufacturing a high-capacity battery pack involves several key steps to ensure optimal performance, safety, and longevity.
Design Considerations:
The design process begins with defining the vehicle's energy requirements. Engineers calculate the total energy needed for electric driving, considering factors like vehicle weight, efficiency, and desired range. This energy demand dictates the battery pack's capacity, typically measured in kilowatt-hours (kWh). Designers also consider the pack's physical dimensions, weight, and mounting location within the vehicle to ensure it fits seamlessly and doesn't compromise performance or safety.
Battery Cell Selection:
Choosing the right battery cells is crucial. Engineers select cells based on their energy density, power output, cycle life, and safety characteristics. Common cell types for PHEVs include lithium-ion (Li-ion) cells, known for their high energy density and relatively low self-discharge rate. The cells are often arranged in a series-parallel configuration to achieve the desired voltage and current levels while maximizing energy storage capacity.
Pack Architecture:
The battery pack's architecture involves arranging the cells in a specific pattern. This can include a prismatic design, where cells are stacked in a rectangular shape, or a cylindrical design, where cells are arranged in a cylindrical form. The choice of architecture depends on factors like pack size, cooling requirements, and manufacturing ease.
Cooling System:
Effective cooling is essential to maintain optimal battery performance and longevity. PHEVs generate heat during operation, so the battery pack must be designed with a cooling system to prevent overheating. This can involve liquid cooling, where a coolant circulates through the pack, or air cooling, where fans or vents facilitate heat dissipation.
Safety Mechanisms:
Safety is paramount in battery pack design. Manufacturers incorporate various safety mechanisms to prevent overheating, short circuits, and other potential hazards. These include thermal management systems, over-voltage and under-voltage protection circuits, and advanced battery management systems (BMS) that monitor cell temperatures, voltage, and current.
Manufacturing Process:
The manufacturing process involves assembling the battery cells, modules, and pack. This includes cell stacking, interconnecting cells in series and parallel, and integrating the pack into the vehicle's chassis. Automated processes are often used to ensure precision and consistency. Quality control measures are implemented throughout the manufacturing process to ensure the pack meets stringent safety and performance standards.
Australia's Electric Car Revolution: A Look at the Growing EV Market
You may want to see also
Power Electronics: Managing power flow between the battery, motor, and engine
Power electronics play a crucial role in plug-in hybrid electric vehicles (PHEVs) by efficiently managing the power flow between the battery, electric motor, and internal combustion engine. This intricate process ensures optimal performance, energy efficiency, and smooth operation of the vehicle. Here's a detailed breakdown of how power electronics facilitate this complex task:
Power Electronics: The Power Management Hub
At the heart of a PHEV's power system are power electronics modules, often referred to as power electronic converters or inverters. These modules act as the central hub, orchestrating the power distribution and conversion between the battery, electric motor, and engine. They are responsible for controlling the flow of electrical energy, ensuring it is directed where it's needed at the right time and in the appropriate amount.
Battery-Motor Interaction
During electric-only operation, the power electronics system connects the battery to the electric motor. Here, the inverter plays a vital role in converting the direct current (DC) from the battery into alternating current (AC) required by the motor. This process involves switching and filtering techniques to ensure smooth power delivery and efficient motor operation. When the vehicle is in hybrid mode, the power electronics manage the complex interplay between the battery, motor, and engine.
Engine-Motor Interaction
In hybrid mode, the power electronics facilitate communication and coordination between the internal combustion engine and the electric motor. This involves managing the power flow from the engine to the motor and vice versa. For instance, during regenerative braking, the power electronics capture the kinetic energy from the motor's rotation and convert it back into usable electrical energy, recharging the battery.
Optimizing Efficiency
The primary goal of power electronics in PHEVs is to optimize energy efficiency. This is achieved through various strategies:
- Variable Power Distribution: Power electronics allow for dynamic adjustment of power distribution between the battery, motor, and engine based on driving conditions and demands.
- Regenerative Braking Control: Efficiently managing regenerative braking ensures maximum energy recovery and minimizes energy wastage.
- Start-Stop Functionality: Power electronics enable smooth start-stop operations, turning off the engine when stationary and restarting it when needed, saving fuel and reducing emissions.
- Energy Recovery: During deceleration, the power electronics capture excess energy from the motor and store it in the battery, further enhancing efficiency.
Power electronics are the unsung heroes of PHEVs, enabling seamless power management and optimizing energy efficiency. Their ability to control and convert electrical power ensures that the vehicle operates smoothly, efficiently, and with minimal environmental impact. As technology advances, power electronics will continue to play a pivotal role in the development of more sophisticated and environmentally friendly hybrid vehicles.
Exploring the Electric Vehicle Revolution: A Comprehensive Guide
You may want to see also
Hybrid Control Unit: Software for optimizing energy usage and performance
The Hybrid Control Unit (HCU) is a critical component in plug-in hybrid electric vehicles (PHEVs), acting as the brain that manages the complex interplay of energy sources and systems. This sophisticated software unit is designed to optimize the vehicle's performance, fuel efficiency, and overall driving experience by making real-time decisions regarding energy distribution and usage. At its core, the HCU is responsible for coordinating the operation of the internal combustion engine (ICE) and electric motor(s), ensuring seamless transitions between the two power sources.
The software within the HCU is a complex algorithm that continuously monitors and analyzes various vehicle parameters, such as speed, acceleration, battery charge level, and driver input. It uses this data to make strategic decisions, such as when to engage the ICE, the electric motor, or both, to achieve the most efficient energy usage. For instance, during deceleration, the HCU might instruct the electric motor to act as a generator, converting kinetic energy back into electrical energy to recharge the battery, a process known as regenerative braking. This not only improves energy efficiency but also extends the range of the vehicle, especially in all-electric mode.
One of the key challenges for the HCU is managing the trade-off between performance and efficiency. When the driver demands high acceleration, the HCU must decide how much power to draw from the ICE and the battery to meet the request while also maintaining the vehicle's overall efficiency. This involves a delicate balance, especially during rapid acceleration or when the vehicle is carrying heavy loads. The software must also consider the state of charge of the battery, ensuring that it is not depleted too quickly, which could lead to reduced range anxiety for the driver.
Furthermore, the HCU's software is designed to learn and adapt over time. It can optimize its strategies based on the vehicle's usage patterns, environmental conditions, and even the driver's preferences. For example, if a driver frequently uses the electric motor for short city drives, the HCU can adjust its algorithms to prioritize battery usage during these trips, improving the overall efficiency of the vehicle. This adaptive nature of the HCU is a significant advantage, as it ensures that the vehicle's performance and energy usage are tailored to the specific needs of the driver and the vehicle's operating environment.
In summary, the Hybrid Control Unit's software is a sophisticated piece of technology that plays a pivotal role in the efficient operation of PHEVs. By making real-time decisions and adapting to various driving conditions, it ensures that the vehicle's energy is used optimally, enhancing both performance and fuel efficiency. The HCU's ability to learn and adjust its strategies over time further contributes to the overall driving experience, making PHEVs a more appealing and practical choice for environmentally conscious consumers.
Understanding the Electrical Nature of Vehicle Modules
You may want to see also
Body and Aerodynamics: Streamlining the vehicle's design for improved efficiency
The body and aerodynamics of a plug-in hybrid electric vehicle (PHEV) play a crucial role in enhancing efficiency and performance. Designers and engineers focus on streamlining the vehicle's exterior to reduce drag and improve overall aerodynamics. This involves careful consideration of the vehicle's shape, surface contours, and various design elements.
One key aspect is the roofline, which significantly impacts frontal area and drag. Designers often opt for a sloping or curved roof to minimize drag and create a sleek appearance. The front end is another critical area, where the shape of the grille, headlights, and overall fascia contribute to aerodynamic efficiency. Designers aim to direct airflow efficiently around the vehicle, reducing turbulence and drag forces.
Side mirrors and door handles are also carefully designed to minimize drag. These small components can create significant turbulence if not optimized. Engineers use wind tunnel testing and computational fluid dynamics (CFD) simulations to analyze airflow patterns and identify areas for improvement. The goal is to ensure that the vehicle's body shape and surface contours work in harmony with the air, reducing drag and improving fuel efficiency.
Aerodynamic enhancements extend to the underbody as well. Designers pay attention to the shape and placement of the underbody panels, exhaust systems, and wheels to minimize drag. Smooth, curved surfaces and carefully designed diffusers help manage airflow and reduce turbulence. Additionally, some PHEVs incorporate active aerodynamics, such as adjustable grilles or air dams, which can be modified based on driving conditions to optimize performance and efficiency.
The overall design philosophy is to create a vehicle that appears sleek and modern while also being highly efficient. This involves a meticulous approach to body styling, ensuring that every curve and contour serves a purpose in reducing drag and improving the vehicle's aerodynamic performance. By combining these design elements, plug-in hybrid electric vehicles can achieve better fuel economy, reduced emissions, and an enhanced driving experience.
Ford's Future: Electric Vehicles in Transition
You may want to see also
Frequently asked questions
A PHEV typically consists of a traditional internal combustion engine (ICE), an electric motor, a high-voltage battery pack, a power electronics system, and a sophisticated control unit. The ICE provides the vehicle with conventional driving range, while the electric motor offers an additional power source for improved performance and efficiency. The battery pack stores electrical energy, which can be used to power the electric motor or recharge it through regenerative braking.
The battery pack is usually mounted in the vehicle's underbody or trunk, depending on the specific design and layout. It is designed to be lightweight, compact, and safe. The pack is often made up of multiple individual cells, which are arranged in modules and then integrated into the vehicle's structure. This integration ensures the battery pack is securely mounted and helps maintain the overall balance and aesthetics of the vehicle.
The power electronics system acts as the intermediary between the battery pack, electric motor, and the vehicle's electrical and mechanical systems. It manages the flow of energy, converting direct current (DC) from the battery to alternating current (AC) for the electric motor and vice versa. This system also controls the charging and discharging of the battery, ensuring efficient energy management and optimizing the vehicle's performance during both electric and hybrid modes of operation.