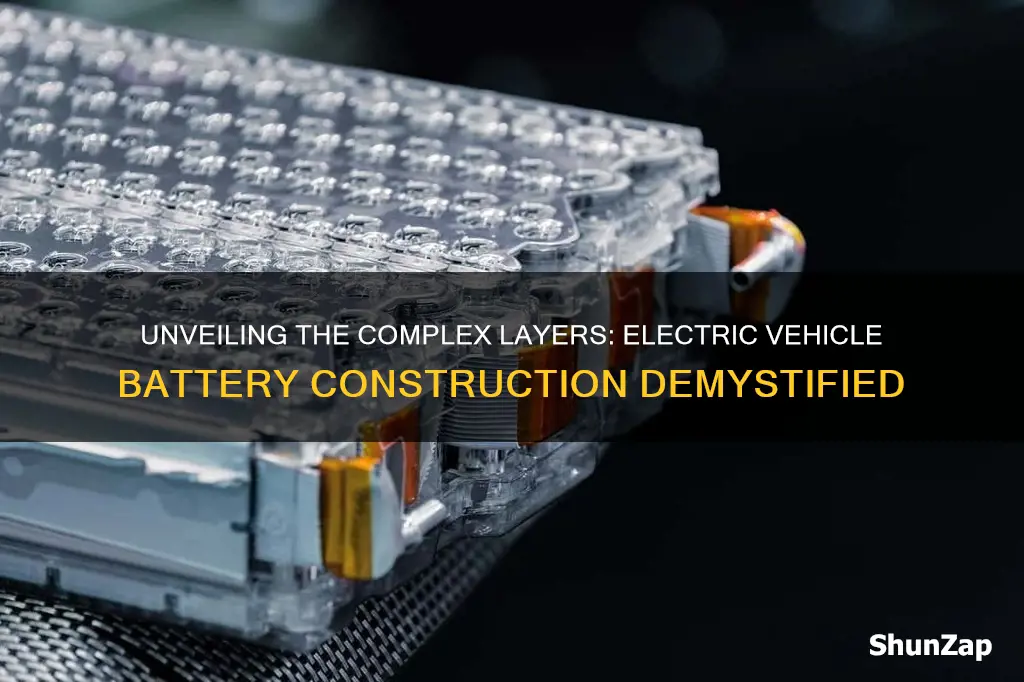
The construction of an electric vehicle battery is a complex process that involves multiple layers and components working together to store and deliver energy efficiently. At its core, a battery consists of one or more cells, each containing an anode, cathode, and electrolyte. The anode and cathode are typically made from materials like lithium cobalt oxide and graphite, respectively, while the electrolyte facilitates the movement of ions between the two electrodes. These cells are then stacked and encased in a protective housing, often made of a lightweight, durable material such as aluminum or composite materials. The entire assembly is designed to be compact, lightweight, and safe, ensuring optimal performance and longevity in the demanding environment of an electric vehicle.
What You'll Learn
- Cell Chemistry: Different materials like lithium-ion or solid-state offer unique advantages for energy density and safety
- Electrode Manufacturing: Processes like coating, slurry mixing, and drying create the positive and negative electrodes
- Separator Design: Porous membranes prevent short circuits while allowing ion movement, crucial for battery performance
- Electrolyte Selection: Liquid, gel, or solid electrolytes conduct ions and influence battery stability and temperature range
- Packaging and Assembly: Enclosures, cooling systems, and interconnects are added to protect and optimize the battery's functionality
Cell Chemistry: Different materials like lithium-ion or solid-state offer unique advantages for energy density and safety
The construction of electric vehicle batteries involves intricate cell chemistry, where the choice of materials significantly impacts performance and safety. One of the most prevalent cell chemistries in electric vehicles is lithium-ion. These batteries utilize a lithium-based cathode and anode, typically made from materials like lithium cobalt oxide (LCO) or lithium iron phosphate (LFP). The electrolyte, a crucial component, facilitates the movement of lithium ions between the cathode and anode during charging and discharging. Lithium-ion batteries offer high energy density, allowing for compact designs and longer driving ranges. However, they can be susceptible to thermal runaway, especially under extreme conditions, which has led to safety concerns.
In contrast, solid-state batteries present an alternative cell chemistry with unique advantages. Instead of a liquid or gel electrolyte, solid-state batteries use a solid conductive material, often a ceramic or polymer. This design offers improved safety as it mitigates the risk of thermal runaway associated with liquid electrolytes. Solid-state batteries can provide higher energy density and faster charging capabilities. For instance, lithium-sulfur (Li-S) batteries, a type of solid-state battery, have a theoretical energy density much higher than lithium-ion, but they are still in the development stage due to challenges in managing sulfur's reactivity.
The choice between lithium-ion and solid-state cell chemistry depends on various factors, including cost, performance requirements, and safety considerations. Lithium-ion batteries have already proven their reliability and are widely used in electric vehicles due to their maturity and cost-effectiveness. They offer a good balance between energy density and safety, making them a popular choice for mass production. On the other hand, solid-state batteries, while promising, are still in the research and development phase, aiming to address the challenges of scalability and cost-effectiveness.
The development of solid-state batteries is an active area of research, with various materials and structures being explored. For example, lithium-metal batteries, a type of solid-state battery, use lithium metal as the anode, offering high energy density but requiring careful management to prevent short circuits. Another approach is the use of polymer electrolytes, which can provide flexibility and improved safety. The goal is to create solid-state batteries that can match or exceed the performance of lithium-ion batteries while addressing their safety concerns.
In summary, the cell chemistry of electric vehicle batteries is a critical aspect that influences performance and safety. Lithium-ion batteries, with their established technology, offer a balance between energy density and safety. Meanwhile, solid-state batteries, including lithium-sulfur and lithium-metal varieties, present opportunities for higher energy density and improved safety but require further development. The choice of cell chemistry will continue to evolve as researchers strive to meet the demands of the electric vehicle market while ensuring the safety and reliability of these power sources.
Ford's Electric Future: Rumors and Reality
You may want to see also
Electrode Manufacturing: Processes like coating, slurry mixing, and drying create the positive and negative electrodes
The manufacturing of electrodes is a critical step in the construction of electric vehicle batteries, as it directly impacts the battery's performance, energy density, and overall efficiency. This process involves several intricate steps to create the positive and negative electrodes, which are the heart of the battery's ability to store and release electrical energy.
Coating: The first step in electrode manufacturing is coating, where active materials are applied to a current collector. For the positive electrode, typically, lithium-based materials like lithium cobalt oxide (LCO) or lithium nickel manganese cobalt oxide (NMC) are used. These materials are carefully coated onto a metal substrate, often aluminum foil, which serves as the current collector. The coating process ensures a uniform layer of active material, providing a high surface area for electrochemical reactions. Similarly, for the negative electrode, materials such as graphite or lithium metal phosphate are coated onto a copper foil current collector. The choice of material and coating technique can vary depending on the battery design and desired performance characteristics.
Slurry Mixing: After coating, the slurry mixing process is employed to create a homogeneous mixture of the active material, binder, and conductive additives. The binder, usually a polymeric material, ensures the active material particles adhere to the current collector and each other. Conductive additives, such as carbon black or graphite, improve the electrical conductivity of the electrode. The slurry is carefully mixed to achieve the desired consistency, ensuring the active material is evenly distributed. This step requires precision to maintain the integrity of the electrode structure and optimize its performance during battery operation.
Drying and Calendering: Following slurry mixing, the electrodes undergo drying to remove any remaining solvents and ensure a solid, stable structure. This process is crucial to prevent any moisture-related issues during battery assembly and operation. After drying, calendering is performed to compress the electrode material and control its thickness. Calendering helps to optimize the porosity and surface area of the electrode, influencing the battery's power and energy output. The calendering process also contributes to the overall mechanical strength and flexibility of the electrode, ensuring it can withstand the rigors of battery manufacturing and usage.
These manufacturing processes are highly controlled and automated to maintain consistency and quality. The specific techniques and materials used can vary depending on the battery chemistry and design, but the fundamental goal remains the same: to create electrodes that efficiently store and release energy, contributing to the overall performance and longevity of electric vehicle batteries.
Electric Vehicles: Manual or Automated? Transmission Explained
You may want to see also
Separator Design: Porous membranes prevent short circuits while allowing ion movement, crucial for battery performance
The separator is a critical component in the design of lithium-ion batteries, especially those used in electric vehicles (EVs). Its primary function is to separate the positive and negative electrodes while facilitating the movement of ions, which is essential for the battery's overall performance and safety. This component is typically made from a thin, flexible material that can withstand the high temperatures and pressures within the battery during operation.
One of the key innovations in separator design is the use of porous membranes. These membranes are engineered to have a highly porous structure, allowing for the free movement of ions while acting as a physical barrier to prevent direct contact between the electrodes. The porosity is carefully controlled to ensure that the membrane can accommodate the movement of lithium ions, which are the primary charge carriers in lithium-ion batteries. This design feature is crucial because it enables the efficient transport of ions between the electrodes, facilitating the charging and discharging processes.
Porous separators are typically made from polymer materials, such as polyolefins (e.g., polyethylene or polypropylene) or polyesters. These polymers are chosen for their chemical stability, high thermal stability, and ability to form a porous structure. The manufacturing process involves stretching and drawing the polymer film to create a highly porous network of tiny pores, often on the nanometer scale. This microstructure is vital as it provides a large surface area for ion exchange while maintaining the necessary mechanical strength to handle the battery's internal pressures.
The design of these porous membranes also considers the prevention of short circuits. To achieve this, the membrane must have a uniform thickness and a consistent pore size distribution. Any defects or variations in the membrane's structure could lead to short circuits, which can cause the battery to overheat, catch fire, or even explode. Therefore, rigorous quality control measures are implemented during the manufacturing process to ensure that the separators meet the required specifications.
In summary, the separator design, particularly the use of porous membranes, is a critical aspect of electric vehicle battery construction. It ensures the safe and efficient operation of the battery by preventing short circuits while facilitating the movement of ions. This design feature, combined with other innovative materials and manufacturing processes, contributes to the overall performance and reliability of lithium-ion batteries in EVs.
The Ultimate Guide to Efficient Electric Vehicles: Top Performers Revealed
You may want to see also
Electrolyte Selection: Liquid, gel, or solid electrolytes conduct ions and influence battery stability and temperature range
The choice of electrolyte in an electric vehicle (EV) battery is a critical aspect of its design, impacting performance, safety, and longevity. Electrolytes are essential components that facilitate the movement of ions between the battery's anode and cathode, enabling the flow of electrical current. They can be categorized into three main types: liquid, gel, and solid electrolytes, each with distinct characteristics and advantages.
Liquid electrolytes, typically composed of organic solvents and dissolved salts, have been traditionally used in EV batteries. These electrolytes offer high ionic conductivity, allowing for efficient ion movement. However, they have some drawbacks. Liquid electrolytes are sensitive to temperature changes, which can affect their performance and stability. In extreme temperatures, they may lose their conductivity or even freeze, leading to reduced battery efficiency. Additionally, liquid electrolytes can be volatile and may pose safety risks if not properly contained.
Gel electrolytes address some of the concerns associated with liquid electrolytes. They are created by incorporating a gelling agent into the liquid electrolyte, resulting in a semi-solid or gel-like state. This modification enhances the electrolyte's stability and reduces its sensitivity to temperature variations. Gel electrolytes provide better thermal stability, making them suitable for a wider temperature range. They also offer improved safety characteristics as they are less prone to leakage and have a higher resistance to mechanical damage.
Solid electrolytes, on the other hand, offer a unique set of advantages. These electrolytes are typically made from ceramic materials or polymers and provide excellent thermal and chemical stability. Solid-state batteries can operate over a wide temperature range without significant performance degradation. They also eliminate the risk of electrolyte leakage, making them inherently safer. However, solid electrolytes face challenges in terms of ionic conductivity, which is generally lower compared to liquid and gel electrolytes. Researchers are actively working on improving the conductivity of solid electrolytes to make them more viable for EV applications.
The selection of the appropriate electrolyte depends on various factors, including the specific battery design, operating conditions, and desired performance characteristics. For instance, liquid electrolytes might be preferred in certain high-performance applications where rapid ion movement is essential. Gel electrolytes offer a balance between conductivity and stability, making them suitable for a wide range of EV battery designs. Solid electrolytes, with their superior thermal stability and safety features, could be the ideal choice for batteries that require operation in extreme environments or where safety is a paramount concern.
The Ultimate Guide to Choosing Your Perfect Electric Vehicle
You may want to see also
Packaging and Assembly: Enclosures, cooling systems, and interconnects are added to protect and optimize the battery's functionality
The construction of electric vehicle batteries involves a meticulous process of packaging and assembly, which is crucial for ensuring optimal performance and longevity. Once the battery cells are manufactured and stacked, the next step is to create a protective and efficient enclosure. This enclosure serves multiple purposes: it safeguards the battery pack from external elements, prevents damage from vibrations or impacts, and provides a structural framework for the entire assembly. Typically, enclosures are made from lightweight yet robust materials such as aluminum or composite materials, designed to withstand the rigors of the vehicle's environment.
Cooling systems are an integral part of this process. Electric vehicle batteries generate heat during operation, and efficient cooling is essential to maintain optimal performance and prevent overheating. Enclosures are often equipped with cooling channels or fins to facilitate heat dissipation. These channels are strategically designed to direct air or liquid coolant through the battery pack, ensuring that each cell remains within the ideal temperature range. Effective cooling systems contribute to improved battery efficiency and extend the overall lifespan of the battery.
Interconnects are another critical component in the packaging and assembly process. These are the electrical connections that link the individual battery cells together to form a functional battery pack. Interconnects must be carefully designed and positioned to ensure minimal resistance and optimal power transfer. They are typically made from high-quality materials like copper or aluminum, chosen for their excellent conductivity and ability to withstand the electrical demands of the battery. The interconnects are soldered or welded in place, ensuring a secure and reliable connection between the cells.
The assembly process also involves the integration of various electronic control units (ECUs) and sensors. These components monitor the battery's performance, temperature, and state of charge, providing vital data for the vehicle's management system. ECUs are connected to the battery pack via specialized wiring harnesses, ensuring efficient data transmission. Sensors, such as temperature sensors and pressure sensors, are strategically placed within the enclosure to provide real-time feedback on the battery's health and performance.
In summary, the packaging and assembly phase of electric vehicle battery construction is a complex process that involves creating protective enclosures, implementing efficient cooling systems, and carefully designing interconnects. These steps are essential to safeguard the battery's performance, ensure its longevity, and provide the necessary protection against environmental factors. By optimizing the battery's functionality through these packaging and assembly techniques, electric vehicle manufacturers can deliver reliable and high-performing power sources for sustainable transportation.
Unleash India's EV Potential: A Guide to Starting Your Green Venture
You may want to see also
Frequently asked questions
The construction of electric vehicle batteries primarily involves the use of lithium-ion technology, which utilizes a combination of lithium metal oxide, graphite, and a liquid or gel electrolyte. These materials are carefully selected for their ability to store and release energy efficiently.
Battery cells are typically assembled in a layered or prismatic structure. In the layered design, the anode, cathode, and electrolyte are stacked in layers, while prismatic cells have a cylindrical shape with a flat top and bottom. These cells are then connected in series and/or parallel to form the desired voltage and capacity.
The BMS is a crucial component that monitors and controls the battery's performance. It manages the charging and discharging processes, ensuring optimal voltage, temperature, and current levels. The BMS also protects the battery pack from overcharging, over-discharging, and short circuits, thus extending the battery's lifespan.
Battery modules, which are groups of individual cells, are connected in series and/or parallel arrangements to create a battery pack. This configuration determines the overall voltage and current output. High-voltage batteries often use a series connection, while parallel connections are common for increasing the available current.
Designing EV batteries presents several challenges, including energy density requirements, thermal management, and safety. Engineers must ensure the battery pack is lightweight, compact, and can store enough energy for the vehicle's range. Additionally, managing heat generation and preventing thermal runaway are critical aspects of battery construction to ensure the safety and reliability of the entire system.