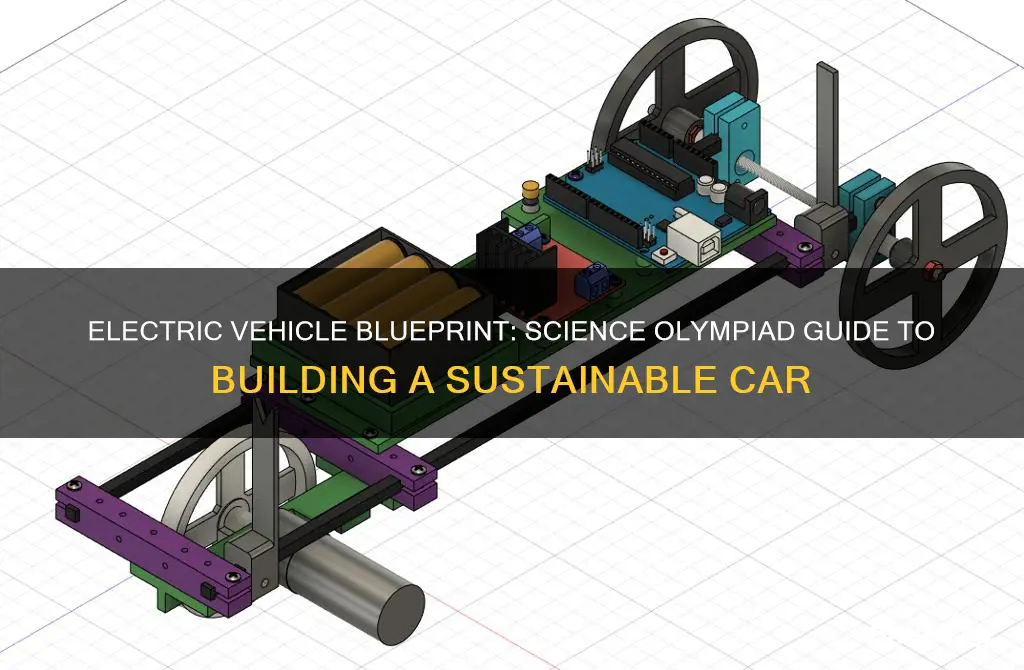
Building an electric vehicle for the Science Olympiad is an exciting and challenging project that combines engineering, physics, and creativity. This project involves designing and constructing a vehicle powered by electricity, which can be a great way to explore sustainable energy solutions and develop practical skills. The competition often requires participants to optimize their vehicles for speed, efficiency, and stability, making it a comprehensive learning experience. In this guide, we will explore the key steps and considerations for building an electric vehicle, including choosing the right components, understanding electrical systems, and ensuring safety and performance.
What You'll Learn
- Battery Selection: Choose the right battery for your EV's power needs
- Motor Types: Understand DC, AC, and stepper motors for propulsion
- Power Electronics: Design circuits to control motor speed and direction
- Vehicle Frame: Build a sturdy, lightweight frame for structural integrity
- Safety Measures: Implement safety features to protect against electrical hazards
Battery Selection: Choose the right battery for your EV's power needs
When building an electric vehicle for the Science Olympiad, battery selection is a critical aspect that can significantly impact your vehicle's performance, efficiency, and overall success in the competition. The right battery choice will determine how far your EV can travel, how quickly it can accelerate, and how well it can handle various driving conditions. Here's a detailed guide to help you make an informed decision:
Understanding Battery Requirements: Begin by understanding the power requirements of your electric vehicle. Consider the size and weight of your car, the desired speed, and the expected driving range. For instance, a lightweight, high-speed EV might require a more powerful battery, while a slower, more energy-efficient vehicle could benefit from a compact, high-capacity battery. Calculate the total watt-hours (Wh) or ampere-hours (Ah) needed to ensure your battery can meet these demands.
Types of Batteries: There are several types of batteries commonly used in electric vehicles, each with its advantages and disadvantages:
- Lead-Acid Batteries: These are traditional and affordable, but they are heavy and have a relatively low energy density. Lead-acid batteries are suitable for low-performance EVs but may not provide the required power for more demanding applications.
- Ni-Cd (Nickel-Cadmium) Batteries: Ni-Cd batteries offer good cycle life and can handle high discharge rates. They are commonly used in hobbyist EVs but can be expensive and have a higher self-discharge rate compared to other types.
- Ni-MH (Nickel-Metal Hydride) Batteries: Ni-MH batteries provide a good balance of energy density and cost. They are lighter and more environmentally friendly than lead-acid batteries, making them a popular choice for science projects.
- Lithium-Ion (Li-ion) Batteries: Li-ion batteries are the most common choice for electric vehicles due to their high energy density, lightweight, and long cycle life. They offer excellent performance and efficiency, making them ideal for high-performance EVs.
Factors to Consider:
- Voltage and Capacity: Choose a battery with a voltage and capacity that matches your EV's requirements. Higher voltage batteries can provide more power, while higher capacity batteries will allow for longer driving ranges.
- Discharge Rate: Consider the discharge rate of the battery, which determines how quickly it can deliver power. Higher discharge rates are suitable for high-performance EVs, but they may reduce the battery's overall lifespan.
- Size and Weight: The physical dimensions and weight of the battery are crucial, especially for lightweight EVs. Ensure the battery fits within your vehicle's frame and does not compromise its structural integrity.
- Safety and Environmental Impact: Opt for batteries with safety features and low environmental impact. Lithium-ion batteries, for example, have built-in safety mechanisms to prevent overheating and short circuits.
Testing and Simulation: Before finalizing your battery choice, consider testing and simulating different battery options. This can be done through computer simulations or by building prototypes to evaluate their performance in your specific EV design. Testing will help you understand the battery's behavior under various conditions, ensuring it meets your power needs.
Remember, the goal is to find a battery that provides the required power, efficiency, and longevity while considering the overall weight and size constraints of your electric vehicle. Proper battery selection will contribute to a successful and well-performing EV in the Science Olympiad competition.
Unveiling the Electric Mystery: Are Electric Wheelchairs Electric Vehicles?
You may want to see also
Motor Types: Understand DC, AC, and stepper motors for propulsion
When building an electric vehicle for the Science Olympiad, understanding the different motor types is crucial for achieving optimal performance and efficiency. This guide will focus on three primary motor types: Direct Current (DC) motors, Alternating Current (AC) motors, and Stepper motors, each with its unique characteristics and applications.
DC Motors:
DC motors are a popular choice for electric vehicles due to their simplicity, reliability, and ease of control. These motors operate on direct current, which means the flow of electricity is constant and in one direction. The basic principle behind DC motors is the interaction between a magnetic field and a current-carrying conductor. When a DC current is applied to the motor's armature (the rotating part), it creates a magnetic field that interacts with the field of permanent magnets or an electromagnet, causing the motor to rotate. The speed of the motor can be controlled by adjusting the voltage or current supplied to the armature, making it highly versatile. For electric vehicles, DC motors are often used in the rear or front wheels to provide propulsion.
AC Motors:
AC motors, also known as induction motors, are another common choice for electric vehicles. These motors operate on alternating current, where the direction of the current periodically reverses. AC motors are known for their robustness, simplicity, and ability to handle high starting torques. The operation of an AC motor involves the creation of a rotating magnetic field by alternating the current in the windings. This field then interacts with the magnetic field of the stator (the stationary part of the motor), causing the rotor (the rotating part) to turn. AC motors are typically more efficient than DC motors at lower speeds, making them suitable for vehicles that require smooth acceleration and deceleration.
Stepper Motors:
Stepper motors are unique in that they can be precisely controlled to rotate in small, discrete steps. This characteristic makes them ideal for applications requiring accurate positioning and control. Stepper motors use a series of electromagnets arranged around a rotor with permanent magnets. By selectively energizing these electromagnets, the rotor can be moved in precise increments. In an electric vehicle, stepper motors can be used for steering or for precise control of the vehicle's movement, especially in tight spaces or when maneuvering. However, stepper motors may not provide the same continuous power as DC or AC motors, so they are often used in conjunction with other motor types for optimal performance.
Understanding the differences between DC, AC, and stepper motors is essential for designing an efficient and effective electric vehicle for the Science Olympiad. Each motor type has its advantages and is suited to specific tasks, allowing for customization based on the vehicle's requirements.
Electric Vehicles: Safer or Riskier on the Roads?
You may want to see also
Power Electronics: Design circuits to control motor speed and direction
When designing circuits for controlling motor speed and direction in an electric vehicle for the Science Olympiad, it's crucial to understand the fundamentals of power electronics and motor control. The goal is to create a system that can precisely regulate the motor's performance, ensuring smooth acceleration, deceleration, and direction changes. Here's a detailed guide to help you through the process:
Motor Control Basics: Start by familiarizing yourself with the types of motors commonly used in electric vehicles, such as DC (Direct Current) motors or AC (Alternating Current) motors. DC motors are often preferred for their simplicity and direct speed control, while AC motors offer advantages in terms of efficiency and torque. Understanding the motor's characteristics, including its voltage, current, and power ratings, is essential for designing an appropriate control circuit.
Speed Control Methods: There are several techniques to control motor speed, including voltage control and frequency control. For DC motors, adjusting the supply voltage is a common method. By varying the voltage, you can change the motor's speed according to the relationship between voltage and speed. For AC motors, frequency control is often used. This involves modifying the supply frequency to regulate the motor's speed. You can use devices like inverters or variable frequency drives (VFDs) to achieve this.
Direction Control: To make the vehicle move forward, backward, or change direction, you need to control the motor's rotation. This can be achieved by reversing the motor's polarity or changing the direction of current flow. In DC motor systems, this is typically done by switching the motor's connections, creating a simple H-bridge circuit. For AC motors, phase control is used, where the supply voltage is adjusted to change the motor's rotation direction.
Circuit Design: The circuit design will depend on the chosen motor type and control method. For DC motors, you might use a simple transistor-based circuit to switch the motor's power supply. H-bridge circuits, which consist of four transistors, are commonly used for bidirectional control. For AC motors, inverters or VFDs are essential components. These devices convert the DC supply to AC and can adjust the frequency and voltage to control speed and direction.
Safety and Efficiency: Ensure that your circuit design includes safety measures, such as overcurrent protection and thermal management. Efficient power electronics can also contribute to the overall performance of the vehicle. Consider using high-efficiency components and optimizing the circuit layout to minimize energy losses.
Remember, the key to a successful electric vehicle project is a well-designed control system that balances performance, efficiency, and safety. By focusing on these aspects, you can create a competitive and impressive entry for the Science Olympiad.
Electric Vehicle Tax Credit: Who's Eligible and How to Claim
You may want to see also
Vehicle Frame: Build a sturdy, lightweight frame for structural integrity
When constructing the frame for your electric vehicle, prioritizing structural integrity while minimizing weight is crucial. This delicate balance ensures your vehicle can handle the stresses of motion and power delivery without compromising safety or performance. Here's a detailed guide on achieving this:
Choose the Right Materials:
- Lightweight Metals: Opt for materials like aluminum alloys or titanium. These offer excellent strength-to-weight ratios, crucial for keeping your frame light yet robust.
- Tubular Design: Consider using hollow tubes instead of solid bars. This design reduces weight while maintaining structural integrity due to the inherent strength of hollow shapes.
- Composite Materials: Carbon fiber composites offer exceptional strength and stiffness while being remarkably lightweight. While they may be more expensive, they can significantly contribute to your vehicle's overall performance.
Design for Strength:
- Truss Structure: Think of your frame as a series of interconnected trusses. This design distributes forces evenly across multiple points, providing superior structural integrity compared to a solid, monolithic frame.
- Reinforcement at Joints: Pay special attention to the connections between frame members. Use robust welding techniques and consider adding gussets or brackets to reinforce these critical areas.
- Strategic Placement of Members: Position your frame members to efficiently absorb and redistribute forces generated during acceleration, deceleration, and cornering.
Optimize Dimensions:
- Minimize Unnecessary Material: Keep your frame as light as possible by avoiding excessive material where it's not needed. Carefully consider the size and thickness of each component.
- Consider Offset Design: Explore designs where certain frame elements are offset from others. This can help reduce overall weight while maintaining the necessary structural rigidity.
Testing and Iteration:
- Computer-Aided Engineering (CAE): Utilize CAE software to simulate your frame's performance under various loads. This allows you to identify potential weaknesses and make design adjustments before physical construction.
- Prototyping: Build a small-scale prototype of your frame to physically test its strength and identify areas for improvement. Iterate on your design based on these findings.
Remember, the goal is to create a frame that is both strong and lightweight. By carefully selecting materials, designing for strength, optimizing dimensions, and rigorously testing your creation, you can build a robust and efficient foundation for your electric vehicle.
Ford's Electric Future: A Doubtful Transition?
You may want to see also
Safety Measures: Implement safety features to protect against electrical hazards
When building an electric vehicle for the Science Olympiad, prioritizing safety is paramount, especially when dealing with electrical components. Here are some essential safety measures to consider:
- Insulation and Grounding: Ensure all electrical connections are properly insulated to prevent short circuits and electrical shocks. Use heat-resistant insulation materials that can withstand the vehicle's operating temperatures. Grounding is crucial; it provides a safe path for electrical faults, reducing the risk of electric shock. Connect the vehicle's frame to the ground to create a reference point for electrical currents.
- Fuse and Circuit Breaker Systems: Implement a comprehensive fuse system to protect against overcurrent situations. Fuses should be rated appropriately for the expected current draw of your vehicle's electrical system. Additionally, consider installing circuit breakers, which offer more advanced protection by automatically tripping when excessive current is detected. This feature is vital for preventing potential fires and ensuring the safety of the vehicle and its operators.
- Overload Protection: Design your electrical system with overload protection in mind. This can be achieved by using devices like current-limiting resistors or employing a smart battery management system that monitors and controls power distribution. Overload protection is critical to prevent damage to the vehicle's components and ensure the safety of the operators.
- Emergency Stop Mechanism: Incorporate a reliable emergency stop button or switch. This feature allows operators to quickly shut down the vehicle's power supply in case of an emergency. It is a standard safety practice in electric vehicle construction and can be a lifesaver in unexpected situations.
- Regular Maintenance and Inspections: Establish a maintenance schedule to inspect and test the electrical system regularly. This includes checking for frayed wires, loose connections, and potential hazards. Regular maintenance ensures that any issues are identified and resolved before they become safety concerns during the competition.
The Mystery of LCO Batteries in EVs: Unlocking the Secret
You may want to see also
Frequently asked questions
The essential components include a powerful electric motor, a lightweight yet sturdy vehicle frame, a high-capacity lithium-ion battery pack, an efficient power electronics system (such as a inverter and charger), and a well-designed suspension system for stability. Additionally, you'll need a robust braking system, a steering mechanism, and a reliable drivetrain to transfer power from the motor to the wheels.
Selecting the appropriate motor depends on various factors. Consider the vehicle's weight, desired speed, and the required torque. Brushless DC motors are popular choices for their efficiency and high-speed capabilities. Ensure the motor's power output aligns with your vehicle's specifications and consider factors like cooling methods and control systems for optimal performance.
Safety is crucial when building an electric vehicle. Always wear protective gear, especially when handling batteries and electronics. Ensure proper grounding to prevent electrical hazards. Implement a robust cooling system to manage heat dissipation, especially for the battery and motor. Test and inspect all electrical connections regularly to avoid short circuits. Additionally, consider adding safety features like speed governors and emergency stop mechanisms.
To enhance performance, focus on minimizing weight while maximizing structural integrity. Use lightweight materials for the vehicle's body and components. Optimize the motor-to-wheel power transfer by selecting an appropriate gear ratio. Fine-tune the vehicle's suspension and braking systems for better handling and stopping power. Regularly test and adjust the vehicle's performance, and consider using advanced control algorithms to improve efficiency and overall vehicle dynamics.