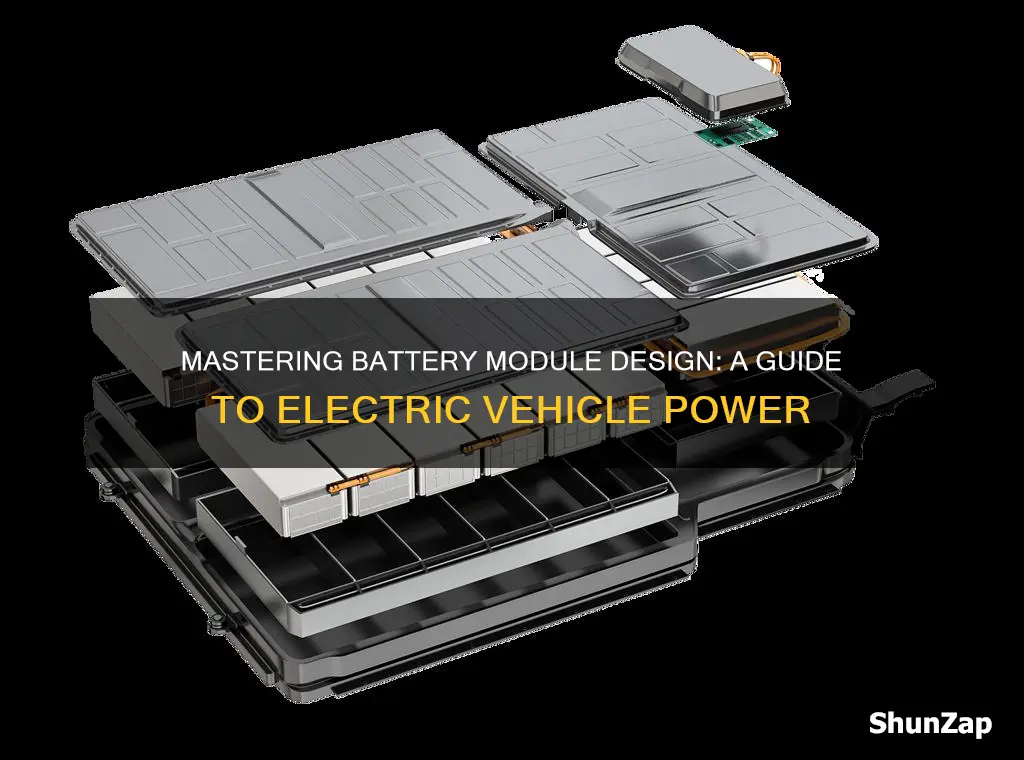
Designing a battery module for electric vehicles is a complex process that requires careful consideration of various factors to ensure optimal performance, safety, and efficiency. This involves selecting the right battery chemistry, such as lithium-ion, and determining the appropriate cell size, shape, and arrangement to meet the specific energy and power requirements of the vehicle. Engineers must also consider the thermal management system to maintain optimal operating temperatures, as well as the electrical architecture to ensure efficient power distribution. Additionally, the design should incorporate safety features to prevent overheating, short circuits, and other potential hazards. This comprehensive approach to battery module design is crucial for the successful integration of electric vehicles into the transportation landscape.
What You'll Learn
- Cell Selection: Choose cells with high energy density, safety, and temperature stability for optimal performance and longevity
- Packaging and Protection: Design robust, lightweight enclosures to shield cells from mechanical damage and environmental factors
- Thermal Management: Implement efficient cooling systems to maintain optimal operating temperatures and prevent overheating
- Safety Mechanisms: Integrate overcurrent, overvoltage, and short-circuit protection to ensure safe operation and prevent hazards
- System Integration: Optimize module layout, wiring, and connections for efficient power distribution and vehicle compatibility
Cell Selection: Choose cells with high energy density, safety, and temperature stability for optimal performance and longevity
When designing a battery module for electric vehicles, cell selection is a critical aspect that significantly impacts the overall performance, safety, and longevity of the battery pack. The choice of cells directly influences the energy density, power output, and reliability of the vehicle's battery system. Therefore, it is essential to carefully evaluate and select cells that meet specific criteria to ensure optimal performance.
One of the primary considerations is energy density. Electric vehicles require high-energy-density cells to maximize the range and efficiency of the car. Cells with advanced chemistries, such as lithium-ion or lithium-polymer, offer higher energy densities compared to traditional lead-acid or nickel-cadmium batteries. These advanced chemistries allow for a more compact and lightweight battery design, enabling longer driving ranges and improved vehicle performance. For instance, lithium-ion phosphate (LiFePO4) cells provide excellent energy density while offering enhanced safety characteristics, making them a popular choice for electric vehicle applications.
Safety is another critical factor in cell selection. Electric vehicle batteries must be designed with robust safety mechanisms to prevent thermal runaway, short circuits, and other potential hazards. Cells with inherent safety features, such as those with a stable electrolyte composition or those designed with multiple safety barriers, are preferred. For example, lithium-ion cells with a polymer electrolyte or those incorporating safety devices like pressure relief valves can mitigate the risks associated with overheating and fire. These safety-focused cell designs are crucial for ensuring the overall safety of the electric vehicle and its passengers.
Temperature stability is also a key consideration. Electric vehicle batteries operate in various environmental conditions, and cells with good temperature stability can maintain their performance and safety across a wide range of temperatures. Cells that can operate efficiently in both cold and hot climates are ideal, as they ensure consistent performance and longevity. Some cell chemistries, like lithium-ion with graphite anodes, exhibit better temperature stability, making them suitable for extreme weather conditions. Additionally, cells with temperature management systems, such as cooling channels or phase-change materials, can further enhance temperature stability and overall battery efficiency.
In summary, selecting cells with high energy density, safety features, and temperature stability is essential for designing a reliable and efficient battery module for electric vehicles. By considering these factors, engineers can ensure that the battery pack meets the performance requirements of the vehicle while also prioritizing safety and longevity. This careful cell selection process is a fundamental step in the overall design and development of advanced battery systems for the automotive industry.
Unlocking EV Savings: A Guide to Claiming Your Subsidy
You may want to see also
Packaging and Protection: Design robust, lightweight enclosures to shield cells from mechanical damage and environmental factors
When designing the packaging and protection for a battery module in an electric vehicle, the primary goal is to ensure the safety, reliability, and longevity of the battery pack while also considering weight and space efficiency. This involves creating a robust yet lightweight enclosure that can effectively shield the battery cells from various mechanical and environmental hazards.
The enclosure should be designed to withstand potential impacts and vibrations during the vehicle's operation. This includes protecting against accidental drops, collisions, and the structural stresses that the vehicle may experience on the road. To achieve this, engineers often use impact-resistant materials such as advanced composites, high-density plastics, or even metal alloys, depending on the specific requirements and cost considerations. These materials should be carefully selected to ensure they do not add excessive weight to the battery module.
In addition to mechanical protection, the enclosure must also safeguard the battery cells from environmental factors. This includes shielding against extreme temperatures, moisture, and corrosion. For temperature management, the enclosure might incorporate cooling or heating systems, or it could be designed to promote natural convection, allowing the battery to maintain an optimal operating temperature. Moisture protection can be achieved through the use of breathable membranes or desiccant-based systems to absorb any humidity that may enter the enclosure.
Corrosion protection is another critical aspect, especially for batteries that will be exposed to varying weather conditions. This can be addressed by using corrosion-resistant materials for the enclosure and implementing measures to prevent the accumulation of electrolytes or other corrosive substances. For instance, the enclosure might feature a sealed design with gaskets or seals to prevent moisture ingress, or it could be treated with anti-corrosion coatings.
Furthermore, the design should consider the ease of manufacturing and assembly to ensure cost-effectiveness. This includes optimizing the enclosure's geometry to facilitate automated processes and minimizing the number of components required. Lightweight materials also contribute to cost savings, as they reduce the overall weight of the vehicle, potentially leading to improved fuel efficiency or increased payload capacity.
In summary, the packaging and protection design for a battery module in an electric vehicle require a careful balance between robust protection, lightweight construction, and environmental considerations. By selecting appropriate materials, implementing protective measures, and optimizing the design for manufacturing, engineers can create a reliable and efficient battery pack that contributes to the overall performance and safety of the electric vehicle.
Transform Your Ride: A Guide to Electric Brakes Conversion
You may want to see also
Thermal Management: Implement efficient cooling systems to maintain optimal operating temperatures and prevent overheating
Thermal management is a critical aspect of designing battery modules for electric vehicles (EVs) as it directly impacts the performance, safety, and longevity of the battery pack. Efficient cooling systems are essential to maintain optimal operating temperatures and prevent overheating, which can lead to reduced efficiency, performance degradation, and potential safety hazards. Here's a detailed guide on implementing effective thermal management:
- Identify Heat Generation Sources: Begin by understanding the heat generation sources within the battery module. Lithium-ion batteries produce heat during charging and discharging due to internal resistance and exothermic reactions. Identify the hottest spots, such as the cells, modules, and any additional electronic components, to determine the most effective cooling strategies.
- Choose Appropriate Cooling Technologies: Select cooling systems based on the specific requirements of your EV battery module. Common cooling methods include:
- Air Cooling: This is a simple and cost-effective approach where air is circulated around the battery pack using fans or natural convection. It is suitable for moderate-temperature environments and can be enhanced with heat sinks or fins to increase surface area.
- Liquid Cooling: Employing a liquid coolant, such as a thermally conductive fluid, can efficiently absorb and transfer heat away from the battery cells. This method is often used in high-performance EVs and can maintain lower temperatures, especially in demanding conditions.
- Phase Change Cooling: This innovative technique utilizes phase change materials (PCMs) that absorb and release heat during phase transitions. PCMs can store and release thermal energy, providing stable temperature regulation.
- Design Efficient Cooling Channels: The layout and design of cooling channels are crucial for effective heat dissipation. Ensure that the cooling fluid or air flows directly over the hottest components, such as the battery cells or modules. Design channels with optimal dimensions and surface roughness to enhance heat transfer. Consider using microchannel heat exchangers for high-performance applications.
- Implement Thermal Insulation: Proper insulation is essential to prevent heat transfer between different parts of the battery module. Use thermal insulation materials with low thermal conductivity to separate heat-generating components from areas that need cooling. Insulation helps maintain temperature differentials, ensuring efficient cooling where needed.
- Monitor and Control Temperature: Integrate temperature sensors throughout the battery module to monitor individual cell or module temperatures. This data can be used to control the cooling system's operation. Implement feedback control systems that adjust fan speeds, coolant flow rates, or other parameters to maintain optimal temperatures. Real-time monitoring ensures quick response to temperature changes.
- Consider Environmental Factors: Take into account the operating environment of the EV, including climate conditions and potential extreme temperatures. Design the thermal management system to handle these variations. For instance, in cold climates, pre-heating or additional insulation might be required, while in hot regions, more aggressive cooling methods may be necessary.
- Optimize System Integration: Ensure that the cooling system integrates seamlessly with the battery module's design. Consider factors like space constraints, weight, and manufacturing processes. Optimize the layout to minimize thermal resistance and maximize heat transfer efficiency. Proper integration ensures that the cooling system enhances performance without adding unnecessary complexity.
By implementing these thermal management strategies, you can create a robust and efficient battery module for electric vehicles, ensuring reliable performance, extended battery life, and enhanced safety.
Unlocking EV Benefits: A Guide to Claiming Your MA Electric Vehicle Credit
You may want to see also
Safety Mechanisms: Integrate overcurrent, overvoltage, and short-circuit protection to ensure safe operation and prevent hazards
When designing a battery module for electric vehicles, safety mechanisms are paramount to ensure the reliable and secure operation of the system. One critical aspect is the integration of overcurrent, overvoltage, and short-circuit protection. These protective measures are essential to safeguard the battery module from potential hazards and ensure its longevity.
Overcurrent protection is a fundamental safety feature. It involves implementing devices such as fuses or circuit breakers that can detect and interrupt excessive current flow. In the context of a battery module, overcurrent protection is crucial to prevent overheating, potential fires, and damage to the battery cells. By monitoring the current levels, these protective devices can quickly respond to any abnormal current surges, ensuring that the battery module operates within safe limits.
Overvoltage protection is equally vital. It requires the use of voltage regulators or diodes that can limit the voltage output of the battery module. Electric vehicles rely on stable voltage levels to function optimally. If the voltage exceeds safe limits, it can lead to performance degradation, cell damage, or even system failure. By integrating overvoltage protection, designers can maintain the voltage within the specified range, ensuring the battery module operates efficiently and safely.
Short-circuit protection is another critical safety mechanism. Short circuits can occur due to various factors, such as manufacturing defects, external damage, or internal cell failures. These events can result in excessive current flow, causing rapid heating, potential explosions, and severe damage to the battery module. To mitigate these risks, designers should incorporate protective devices like varistors or specialized fuses that can detect and interrupt short circuits promptly. This ensures that any potential hazards are minimized, and the battery module remains safe during operation.
Incorporating these safety mechanisms requires careful consideration of the battery module's design and component selection. It involves choosing appropriate protective devices, sizing them according to the expected current and voltage levels, and strategically placing them within the module. Additionally, thorough testing and validation processes should be conducted to ensure the effectiveness of these safety measures. By implementing overcurrent, overvoltage, and short-circuit protection, designers can create a robust and secure battery module for electric vehicles, contributing to the overall safety and reliability of the vehicle's power system.
Unleash Savings: Your Guide to Federal EV Credit Claims
You may want to see also
System Integration: Optimize module layout, wiring, and connections for efficient power distribution and vehicle compatibility
When designing a battery module for electric vehicles, system integration is a critical aspect that ensures efficient power distribution and vehicle compatibility. The layout, wiring, and connections within the module play a significant role in optimizing performance and safety. Here's a detailed guide on how to approach this:
Module Layout Optimization:
Start by visualizing the physical arrangement of the battery cells within the module. Aim for a compact and organized layout to minimize space usage in the vehicle. Consider the following:
- Cell Orientation: Decide whether to stack cells vertically or horizontally, or even explore innovative 3D arrangements to maximize space efficiency.
- Cell Placement: Strategically place cells to ensure even weight distribution and balance the module's center of gravity. This is crucial for vehicle stability and handling.
- Cooling Channels: Design cooling channels or pathways to facilitate efficient heat dissipation from the cells. Proper cooling is essential to maintain optimal operating temperatures.
Wiring and Connections:
Efficient wiring is key to minimizing power losses and ensuring reliable power distribution. Here's a breakdown:
- Busbar System: Implement a busbar system to collect power from individual cells and distribute it to the vehicle's electrical system. Busbars should be strategically placed to avoid unnecessary wiring complexity.
- Internal Wiring: Use high-quality, low-resistance wires to connect cells in series or parallel configurations. Ensure proper insulation to prevent short circuits and maintain safety.
- Terminal Connections: Design easily accessible terminals for efficient charging and maintenance. Consider using quick-disconnect mechanisms for faster charging processes.
Connection Optimization:
- Cell Connections: When connecting cells in series or parallel, ensure precise alignment and secure fastening methods to maintain structural integrity.
- Interconnects: Utilize high-performance interconnects like flexible printed circuits or thin-film technology for reliable and compact connections.
- Grounding: Implement an effective grounding system to minimize electromagnetic interference and ensure electrical safety.
Vehicle Compatibility:
The battery module should seamlessly integrate into the vehicle's architecture:
- Mounting: Design the module with compatible mounting points to match the vehicle's frame and ensure easy installation.
- Thermal Management: Consider the vehicle's existing cooling systems and integrate the battery module accordingly to manage temperature effectively.
- Electrical Interface: Ensure the module's electrical connections align with the vehicle's power management system for efficient charging and discharging.
By carefully considering the module layout, wiring, and connections, you can achieve an optimized system that delivers efficient power distribution, enhances vehicle compatibility, and contributes to the overall performance and safety of the electric vehicle. This approach is essential in the development of high-performance and reliable battery modules for the automotive industry.
Transform Your Ride: A Comprehensive Guide to Electric Vehicle Conversion
You may want to see also
Frequently asked questions
Designing a battery module for electric vehicles involves several critical factors. Firstly, energy density is essential to maximize the vehicle's range. This requires careful selection of high-performance cells and efficient packaging. Secondly, thermal management is crucial to maintain optimal operating temperatures, especially in high-power applications. Effective cooling systems and heat dissipation methods should be employed. Additionally, safety is paramount; the design must include protective measures against overcharging, overheating, and short circuits. Finally, consider the overall system integration, ensuring the module fits the vehicle's dimensions and provides easy access for maintenance.
Selecting appropriate battery cells is a critical decision. Consider the cell chemistry, such as lithium-ion, and evaluate its specific energy, power capabilities, and temperature performance. Match the cell voltage and current ratings to the module's requirements. It's essential to choose cells with similar characteristics to ensure balanced performance and longevity. Additionally, consider the cell size and form factor to ensure they fit the module's design and provide the desired energy density.
Thermal management in battery modules can be complex. One challenge is ensuring uniform temperature distribution across the module, especially in high-power applications. This can be achieved through advanced cooling techniques like liquid cooling or phase-change materials. Another issue is managing the heat generated during charging and discharging, which requires efficient heat dissipation methods. Proper ventilation and insulation are also crucial to prevent overheating and ensure the battery's longevity.
Safety is a top priority in battery module design. Implement protective circuits and sensors to monitor voltage, current, and temperature. Overcurrent and overvoltage protection circuits should be in place to prevent damage. Consider adding safety mechanisms like venting systems to release built-up pressure and prevent explosions. Regularly test and validate the module's performance under various conditions to ensure it meets safety standards.
A modular design approach offers several benefits. It allows for easy customization and scalability, enabling manufacturers to adapt to varying vehicle requirements. Modular packs can be designed with interchangeable modules, simplifying maintenance and repair. This design also facilitates parallel or series connections, optimizing voltage and current output. Additionally, modularity enhances flexibility in manufacturing processes, reducing production costs and time.