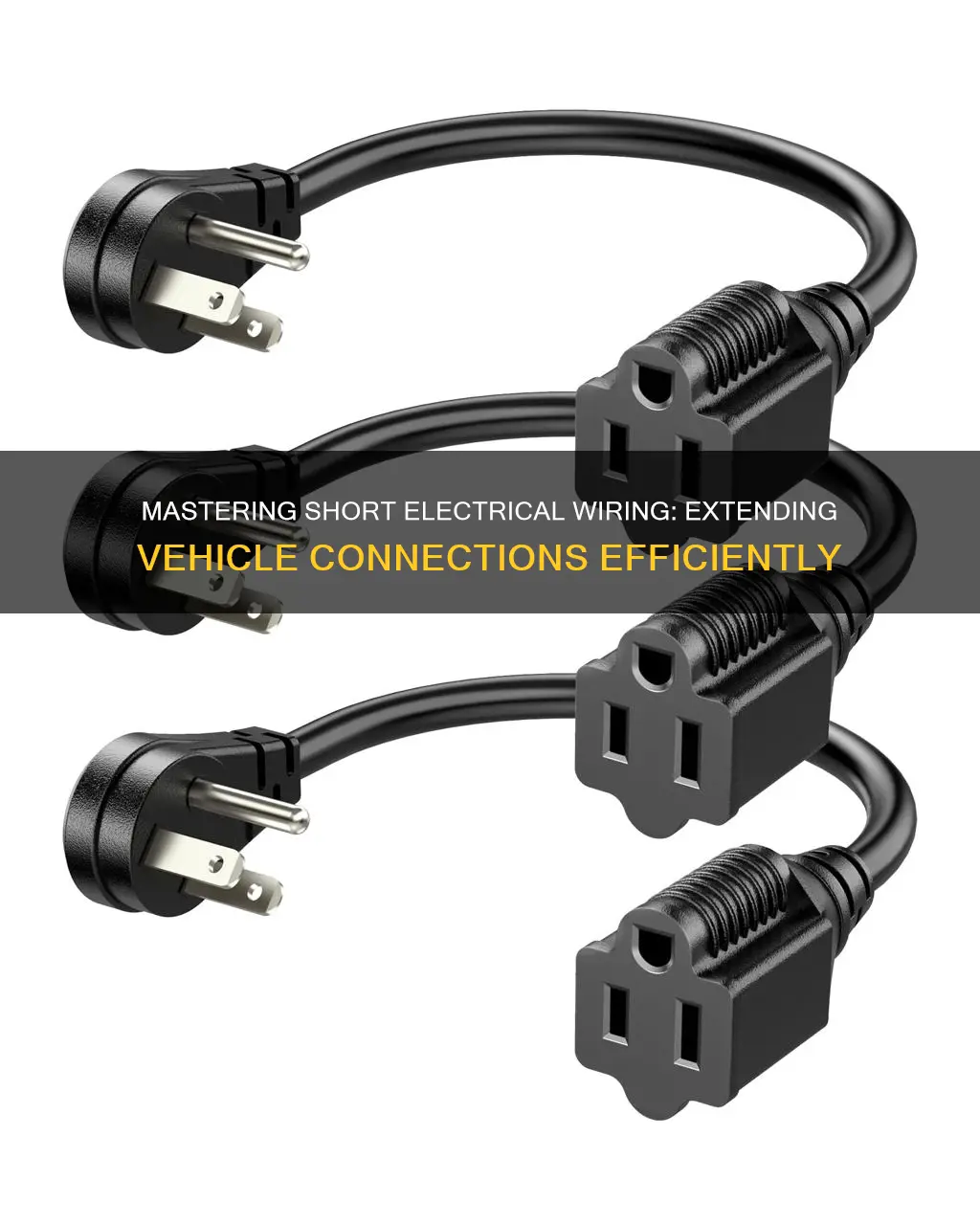
When it comes to extending the electrical wiring in a vehicle, it's important to follow a structured approach to ensure safety and functionality. This guide will provide a step-by-step process for extending short electrical wiring in a vehicle, covering essential aspects such as identifying the wiring diagram, selecting the appropriate gauge and type of wire, and ensuring proper grounding and insulation. By following these guidelines, you can effectively enhance the electrical system of your vehicle while maintaining its reliability and performance.
What You'll Learn
- Wire Selection: Choose appropriate gauge and type of wire for the application
- Terminal Connections: Ensure secure and reliable connections using crimping or soldering techniques
- Grounding: Establish a solid ground path to prevent electrical interference
- Insulation: Protect wires from damage with suitable insulation materials
- Safety Checks: Regularly inspect wiring for wear, damage, and proper functionality
Wire Selection: Choose appropriate gauge and type of wire for the application
When extending electrical wiring in a vehicle, selecting the right wire is crucial for ensuring a safe and reliable system. The first step is to understand the specific requirements of your application. Different electrical components in a vehicle have varying power needs and current-carrying capacities, so the wire gauge and type must be appropriate for each section. For instance, wires used for high-current applications, such as starting motors or alternators, should have a larger gauge to handle the increased load without overheating.
Wire gauge is measured in American Wire Gauge (AWG) and determines the wire's thickness. Thicker wires have a lower AWG number. For automotive wiring, common gauges range from 10 to 18 AWG. Thicker wires (lower AWG numbers) are generally used for power-intensive components, while thinner wires (higher AWG numbers) are suitable for lower-current applications. As a rule of thumb, the thicker the wire, the more current it can handle, but it's essential to consider the specific requirements of your vehicle's electrical system.
The type of wire is also critical. Solid wires are commonly used for general-purpose applications and are suitable for most vehicle wiring. However, for high-current or high-voltage circuits, stranded wires are preferred. Stranded wires consist of multiple smaller wires twisted together, offering better flexibility and reduced resistance compared to solid wires. This is particularly important when routing wires through tight spaces or making multiple connections.
Additionally, consider the environmental conditions your vehicle will operate in. If the wiring will be exposed to extreme temperatures or harsh environments, choose wires with appropriate insulation and shielding. For example, wires used in high-temperature areas should have insulation that can withstand such conditions. Always refer to the vehicle's electrical diagram or consult the manufacturer's specifications to determine the correct wire types and sizes for each circuit.
In summary, selecting the right wire involves considering the specific electrical demands of your vehicle's components, choosing the appropriate gauge to handle the current, and selecting the right type of wire (solid or stranded) for the application. Proper wire selection ensures the electrical system functions efficiently and safely, even when extended or modified.
Troubleshooting Electrical Issues: A Comprehensive Guide to Diagnosing Vehicle Problems
You may want to see also
Terminal Connections: Ensure secure and reliable connections using crimping or soldering techniques
When extending electrical wiring in a vehicle, ensuring secure and reliable terminal connections is crucial to prevent issues like loose connections, short circuits, or even fire hazards. There are two primary methods to achieve this: crimping and soldering. Each method has its advantages and is suitable for different scenarios.
Crimping:
Crimping is a popular and accessible technique for making terminal connections. It involves using a crimping tool to apply pressure to a terminal connector, which then securely locks onto the wire. Here's a step-by-step guide:
- Prepare the Wire: Ensure the wire is clean and free of any insulation that might interfere with the connection. Strip the insulation back to expose the required length of the wire's conductive core.
- Choose the Terminal: Select a terminal connector that matches the wire gauge. Terminals come in various sizes and configurations, so choose one suitable for your application.
- Crimping Process: Insert the wire into the terminal, ensuring it is centered. Use the crimping tool to apply firm pressure to the terminal, following the manufacturer's instructions for the specific tool and terminal type. The crimp should be tight and secure, creating a reliable bond.
- Insulation: After crimping, ensure the terminal is insulated to prevent short circuits. You can use heat-shrink tubing or insulated boots to cover the crimped connection.
Soldering:
Soldering is a more permanent and robust method, ideal for high-current applications or when a strong, long-lasting connection is required.
- Preparation: Similar to crimping, start by preparing the wire and terminal. Solder the wire to the terminal by melting a small amount of solder onto the terminal's surface, then placing the wire in contact with the solder. Ensure the wire is clean and free of oxidation.
- Soldering Technique: Use a soldering iron to heat the solder until it melts and flows onto the joint. Apply gentle pressure to ensure good contact between the wire and terminal. Allow the solder to cool and solidify, creating a strong bond.
- Insulation and Testing: Insulate the soldered connection with heat-shrink tubing or a suitable insulator. Test the connection by applying voltage to ensure it is secure and functional.
Both crimping and soldering techniques require practice and precision to master. It's essential to use the right tools and materials for each method to ensure the connections are reliable and safe. Always refer to vehicle wiring diagrams and manufacturer guidelines for specific instructions related to your vehicle's electrical system.
Transform Your Ride: A Comprehensive Guide to Electric Vehicle Conversion
You may want to see also
Grounding: Establish a solid ground path to prevent electrical interference
Grounding is a critical aspect of electrical systems, especially when dealing with vehicle wiring. Establishing a solid ground path is essential to prevent electrical interference and ensure the safe and efficient operation of your vehicle's electrical components. Here's a detailed guide on how to achieve this:
Understanding the Importance of Grounding:
Grounding serves as a reference point for electrical circuits, providing a low-resistance path to the earth. In vehicles, proper grounding is crucial to maintain electrical stability and minimize interference. It helps in reducing voltage fluctuations, preventing electrical noise, and ensuring that any faults or short circuits are safely directed to the ground, protecting the vehicle's electrical system.
Steps to Establish a Solid Ground Path:
- Identify the Existing Ground Point: Start by locating the existing ground point in your vehicle. This is typically a metal body component, often the engine block or a dedicated grounding strap. Understanding the vehicle's original grounding system is essential to avoid disrupting it.
- Use a Dedicated Grounding Wire: For extending the wiring, it's best to use a separate, heavy-duty grounding wire. Choose a wire gauge suitable for the vehicle's electrical system, ensuring it can handle the expected current. Strip the insulation from both ends of the wire and connect it to the designated ground point. Ensure a secure connection by using a suitable connector or crimping the wire to the ground terminal.
- Grounding Straps: In some cases, a grounding strap can be used to provide an additional ground path. This strap should be made of a conductive material and connected to the vehicle's body and the new wiring system. It offers a reliable path for electrical discharge.
- Ensure Proper Connection: Double-check all connections to guarantee a solid ground. Ensure that the grounding wire is securely attached to the ground point and that there are no loose connections that could cause interference.
Maintenance and Inspection:
Regular maintenance is key to maintaining a reliable grounding system. Inspect the grounding connections periodically to ensure they remain intact and free from corrosion. Clean any corrosion or oxidation that may build up over time. This proactive approach will help prevent electrical issues and ensure the longevity of your vehicle's wiring.
By following these steps, you can effectively establish a solid ground path, which is fundamental to managing electrical interference and ensuring the reliability of your vehicle's electrical wiring. Remember, proper grounding is a vital component in any electrical extension or repair project.
Unlocking Federal EV Tax Credit: A Step-by-Step Guide
You may want to see also
Insulation: Protect wires from damage with suitable insulation materials
Insulation is a critical aspect of any electrical wiring project, especially when dealing with vehicle electrical systems. It serves as a protective barrier, safeguarding the wires from various potential hazards and ensuring the overall safety and reliability of the wiring extension. When extending short electrical wiring in a vehicle, proper insulation is essential to prevent damage, short circuits, and potential fire hazards.
The primary purpose of insulation is to provide electrical protection. It acts as a barrier between the conductive core of the wire and the surrounding environment, preventing unintended contact and potential short circuits. Insulation materials are carefully chosen to withstand the specific conditions of the vehicle's electrical system, including temperature variations, vibrations, and exposure to various chemicals and moisture. For example, rubber insulation is commonly used for its flexibility and resistance to heat and chemicals, making it ideal for vehicle wiring.
There are various types of insulation materials available, each with its own advantages and applications. One common type is thermoplastic insulation, which offers excellent electrical resistance and can withstand high temperatures. It is often used for wires that are exposed to intense heat, such as those near the engine or in high-performance vehicles. Another popular choice is thermoset insulation, known for its superior insulation properties and ability to retain its shape under pressure. This type is commonly used in high-voltage applications and provides long-lasting protection.
When insulating wires, it is crucial to ensure a secure and tight fit. The insulation should be applied carefully, ensuring it covers the entire wire, including the connections. Overlapping the insulation on each side of the connection is essential to create a robust barrier. Additionally, the insulation should be securely attached to the wire, preventing it from coming loose during the vehicle's operation. This can be achieved by using specialized insulation sleeves or by carefully wrapping the insulation around the wire.
In summary, insulation plays a vital role in extending electrical wiring in vehicles. It provides electrical protection, prevents damage, and ensures the safety of the vehicle's electrical system. By choosing the right insulation materials and applying them correctly, you can create a reliable and long-lasting wiring extension, ensuring the vehicle's electrical components function optimally and safely. Proper insulation is a fundamental step in any wiring project, and it should not be overlooked.
Unlocking EV Tax Savings: A Guide to Maximizing Your Credit
You may want to see also
Safety Checks: Regularly inspect wiring for wear, damage, and proper functionality
Regular safety checks are essential to ensure the reliability and safety of your vehicle's electrical system, especially when dealing with extended wiring. Here's a detailed guide on how to inspect and maintain your vehicle's wiring for optimal performance:
Visual Inspection: Start by visually examining the wiring harness and all connected components. Look for any visible signs of damage, such as frayed or exposed wires, burn marks, or discolored insulation. Check for any loose connections where wires are attached to fuses, switches, or other terminals. Even small cracks or brittleness in the insulation can lead to potential issues. Pay close attention to areas where the wiring passes through the vehicle's frame or body, as these spots may be more susceptible to damage.
Flexibility and Movement: Electrical wiring should be flexible and capable of moving with the vehicle's components. Inspect the wiring harness for any signs of rigidity or stiffness, especially in areas where the wiring is routed around engine components or suspension parts. Worn-out wiring may become stiff over time, leading to potential disconnections or damage during normal vehicle operation.
Connection Integrity: Ensure that all electrical connections are secure and intact. Check for any signs of corrosion around terminals, as this can prevent proper contact and lead to intermittent or lost signals. Clean the terminals if necessary using a small amount of electrical contact cleaner. Tighten any loose connections and ensure that all wires are properly routed and not chafing against moving parts.
Testing Functionality: Regularly test the functionality of your vehicle's electrical system. This can be done using a multimeter or a similar testing device. Check for continuity in the wiring to ensure that the circuit is complete. Test each fuse and relay to confirm they are functioning correctly. Pay attention to warning lights or gauges that may indicate a problem with the electrical system. Address any issues promptly to prevent further damage.
Document and Maintain: Keep a record of your inspections and any issues found. Note the date, the components inspected, and the actions taken. Regular maintenance and timely repairs will help extend the life of your vehicle's electrical wiring. If you notice any recurring problems or are unsure about specific components, consult a professional mechanic who can provide expert advice and ensure your vehicle's electrical system remains safe and reliable.
Mastering EV Battery Care: Tips for Optimal Performance and Longevity
You may want to see also
Frequently asked questions
Extending your vehicle's electrical wiring is a common task for DIY enthusiasts and can be achieved with some basic tools and knowledge. Start by identifying the power source for the new accessory, which could be the battery, a fuse box, or another existing circuit. Then, locate the appropriate gauge wire that can handle the current draw of your accessory. Strip the insulation from the wire ends and connect them securely using crimp connectors or heat-shrink tubing. Ensure you follow safety guidelines and consult a wiring diagram specific to your vehicle for accurate connections.
Wire gauge is a critical factor in vehicle electrical systems. Thicker wires (lower gauge numbers) carry more current and are suitable for high-power accessories. For example, 12-gauge wire is commonly used for power windows and seats, while 14-gauge wire is often employed for interior lights and audio systems. Always refer to your vehicle's wiring diagram and the accessory's power requirements to select the appropriate gauge. Thinner wires (higher gauge numbers) are better for signal transmission, like wiring speakers or sensors.
Yes, having the right tools is essential for a successful wiring job. Basic tools include wire strippers to remove insulation, crimping tools for secure connections, and heat shrink tubing for insulation and protection. You might also need a voltage tester to ensure proper wiring connections and a soldering iron for more permanent installations. Always ensure you have the necessary safety gear, such as gloves and safety goggles, to protect yourself during the wiring process.
Safety is paramount when extending your vehicle's wiring. Always use high-quality, automotive-grade wiring and connectors to ensure reliability. Double-check your connections and ensure they are securely fastened to avoid loose contacts. Verify that the wiring path does not interfere with any moving parts or cause damage to the vehicle's interior. It's also crucial to ground the wiring properly to prevent electrical issues. Finally, consult your local regulations and your vehicle's manual to ensure compliance with any legal requirements for vehicle modifications.