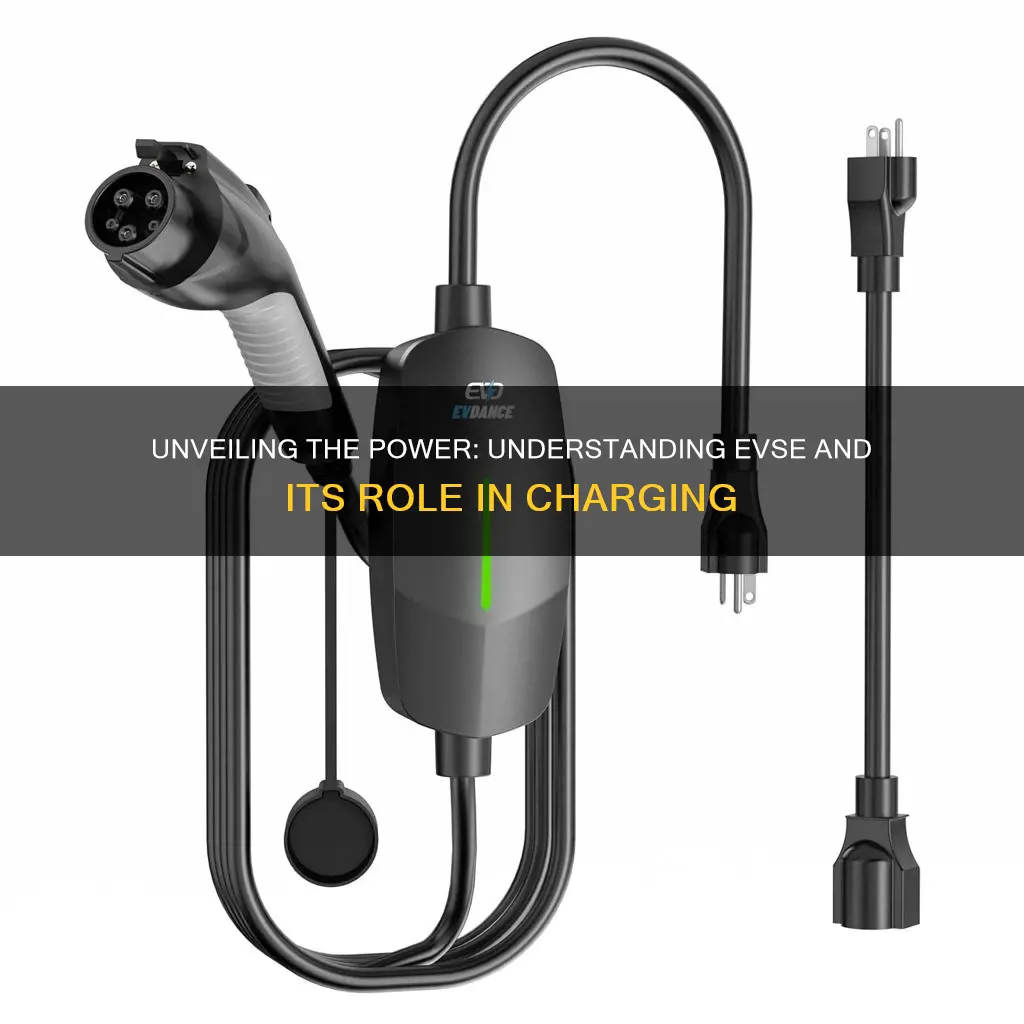
Electric Vehicle Supply Equipment (EVSE) is a crucial component in the infrastructure supporting the growing electric vehicle (EV) market. It refers to the hardware and software systems designed to supply electricity to charge electric vehicles, ensuring they are ready for use. This equipment includes charging stations, which can be installed in various locations such as homes, workplaces, public areas, and parking lots, enabling EV owners to conveniently recharge their vehicles. The technology behind EVSE varies, ranging from simple AC (alternating current) chargers to more advanced DC (direct current) fast chargers, each catering to different charging needs and vehicle types. Understanding EVSE is essential for optimizing the efficiency and accessibility of electric transportation, as it plays a pivotal role in the widespread adoption of sustainable mobility solutions.
What You'll Learn
- Power Inverters: Convert direct current (DC) from batteries to alternating current (AC) for vehicle electronics and accessories
- Charging Systems: Manage the charging process, ensuring safe and efficient power delivery to the vehicle's battery
- DC-DC Converters: Step down high-voltage DC to lower voltages for various vehicle systems and accessories
- Battery Management Systems (BMS): Monitor and control battery performance, temperature, and state of charge
- Communication Protocols: Define standards for data exchange between EVSE and vehicle, ensuring compatibility and safety
Power Inverters: Convert direct current (DC) from batteries to alternating current (AC) for vehicle electronics and accessories
Power inverters are essential components in electric vehicles (EVs) that play a crucial role in converting the direct current (DC) power stored in the vehicle's batteries into alternating current (AC) that can be used to power various vehicle electronics and accessories. This process is vital as it enables the operation of devices and systems that are designed to run on AC power, ensuring the functionality and comfort of the EV during everyday use.
In an EV, the battery pack typically provides DC power, which is a constant voltage and current level. However, many vehicle components and systems, such as lights, fans, entertainment systems, and charging ports, require AC power to function optimally. This is where power inverters come into play. These devices act as intermediaries, taking the DC power and transforming it into the alternating current required by these vehicle systems.
The process of inversion involves rapidly switching the direction of current flow in the DC power source, creating a back-and-forth pattern that mimics the waveform of AC power. This conversion is necessary because AC power is more efficient for long-distance transmission and is the standard for household electrical outlets. By using power inverters, EVs can utilize their battery power effectively, ensuring that all essential vehicle functions are operational.
There are different types of power inverters available for EVs, including modified sine wave (MSW) and pure sine wave (PSW) inverters. MSW inverters are more affordable but may produce less efficient and less stable AC power, which can impact the performance of sensitive electronics. On the other hand, PSW inverters provide a more accurate AC waveform, ensuring that all vehicle systems operate optimally and efficiently.
In summary, power inverters are critical in the EV supply system, enabling the conversion of DC battery power to AC power for various vehicle applications. This technology ensures that electric vehicles can power their electronics and accessories, providing a seamless and comfortable driving experience. Understanding the role of power inverters is essential for EV owners and enthusiasts to optimize their vehicle's performance and functionality.
Unveiling the Electric Vehicle's MPGe Mystery: A Common Number Revealed
You may want to see also
Charging Systems: Manage the charging process, ensuring safe and efficient power delivery to the vehicle's battery
Electric Vehicle Supply Equipment (EVSE) plays a crucial role in the charging infrastructure for electric vehicles (EVs), ensuring a safe and efficient power supply to the vehicle's battery. The charging system is a critical component of EVSE, as it manages the entire charging process, from initiating the charge to monitoring and controlling the power flow.
The primary function of a charging system is to deliver electrical energy to the EV's battery pack while adhering to specific safety standards and regulations. This process involves several key steps. Firstly, the charging system must identify the vehicle's charging capabilities and communicate with the EV to determine the appropriate charging parameters, such as voltage, current, and power levels. This communication is essential to ensure that the charging process is tailored to the vehicle's specific requirements, optimizing charging efficiency.
During the charging process, the system regulates the power flow to the battery, preventing overcharging and potential damage to the vehicle. It monitors the battery's state of charge and adjusts the charging rate accordingly. For instance, if the battery is nearly full, the system may reduce the charging current to maintain a steady and safe power delivery. This dynamic control is vital for extending the battery's lifespan and ensuring user convenience.
Safety is a paramount consideration in EVSE. Charging systems incorporate various safety mechanisms to protect both the vehicle and the user. These include ground fault circuit interrupters (GFCIs) to detect electrical faults, temperature sensors to monitor battery heat, and overcurrent protection to prevent excessive current flow. In the event of a fault or abnormal condition, the system can automatically shut down the charging process, mitigating potential risks.
Efficient power delivery is another critical aspect of charging systems. They are designed to optimize energy transfer, minimizing energy losses during the charging process. This efficiency is crucial for reducing the overall charging time and ensuring that the vehicle's battery is replenished quickly and effectively. Additionally, some advanced charging systems support fast-charging technologies, enabling rapid charging for long-distance travel or when time is limited.
In summary, the charging system within EVSE is responsible for managing the entire charging process, ensuring the safe and efficient delivery of power to the vehicle's battery. It communicates with the EV, regulates power flow, incorporates safety measures, and optimizes energy transfer, all of which contribute to a seamless and reliable charging experience for electric vehicle owners.
Arizona's Electric Revolution: Unveiling the EV Leaders
You may want to see also
DC-DC Converters: Step down high-voltage DC to lower voltages for various vehicle systems and accessories
Electric Vehicle Supply Equipment (EVSE) is a crucial component in the infrastructure and technology that powers electric vehicles (EVs). It encompasses various devices and systems that enable the charging, power management, and overall supply of electricity to electric cars, buses, and other vehicles. One essential type of component within EVSE is the DC-DC converter, which plays a vital role in managing the high-voltage direct current (DC) found in electric vehicles and converting it to lower voltages required by different vehicle systems and accessories.
DC-DC converters are specialized electronic devices designed to step down the high voltage present in an EV's battery pack to the lower voltages needed by various vehicle components. Electric vehicles typically operate on high-voltage DC power, which is stored in large batteries. This high voltage is necessary to achieve efficient energy transfer and propulsion. However, not all vehicle systems and accessories require such high voltage. For instance, lighting, infotainment systems, and climate control units often need lower voltages to function optimally.
The primary function of a DC-DC converter is to regulate and adjust the voltage levels. It does this by converting the high-voltage DC input to a lower DC output voltage. This process is essential because it allows the vehicle's electrical system to power different components without the risk of damage or malfunction due to excessive voltage. For example, a DC-DC converter can step down the voltage from 400V (a common high-voltage in EVs) to 12V, which is the standard voltage used for vehicle accessories like lights, radio, and power windows.
These converters are designed to be compact and efficient, ensuring minimal energy loss during the conversion process. They are typically integrated into the vehicle's power electronics system, where they work in conjunction with other components like inverters and batteries to manage power distribution. The efficiency and reliability of DC-DC converters are critical, as they directly impact the overall performance and longevity of the electric vehicle.
In summary, DC-DC converters are essential components of EVSE, responsible for stepping down high-voltage DC to power various vehicle systems and accessories. Their role is to ensure that electric vehicles can operate safely and efficiently by providing the appropriate voltage levels for different components. As the demand for electric mobility continues to grow, the development and optimization of such power management systems will be key to supporting the widespread adoption of electric vehicles.
Warren Buffett's Electric Vehicle Stake: Selling or Holding?
You may want to see also
Battery Management Systems (BMS): Monitor and control battery performance, temperature, and state of charge
Battery Management Systems (BMS) are critical components of Electric Vehicle Supply Equipment (EVSE), playing a vital role in ensuring the safe and efficient operation of electric vehicles (EVs). These systems are designed to monitor and control various aspects of the battery, including performance, temperature, and state of charge, which are essential parameters for optimizing battery life and enhancing overall vehicle performance.
The primary function of a BMS is to safeguard the battery pack from potential damage caused by over-charging, over-discharging, or excessive temperature variations. It achieves this by implementing a set of sophisticated algorithms and sensors. These algorithms continuously calculate and monitor the battery's state of charge (SoC), which represents the current level of energy stored in the battery. By accurately tracking the SoC, the BMS can ensure that the battery is neither overcharged, leading to potential safety hazards, nor discharged beyond its safe limits, which could result in permanent damage.
Temperature monitoring is another critical aspect of BMS. Electric vehicle batteries are sensitive to temperature changes, and extreme conditions can significantly impact their performance and longevity. The BMS employs temperature sensors to monitor the battery pack's temperature, ensuring it operates within an optimal range. If the temperature deviates significantly from the ideal range, the BMS can activate cooling or heating mechanisms to maintain the desired temperature, thus optimizing battery performance and safety.
In addition to monitoring, the BMS also plays a crucial role in controlling the battery's performance. It manages the charging and discharging processes, ensuring they occur at safe and efficient rates. By regulating the current and voltage during charging and discharging, the BMS prevents overloading, which could lead to battery damage or reduced lifespan. It also optimizes the battery's performance by adjusting the charging and discharging rates based on the vehicle's needs and the battery's current state.
Furthermore, BMS provides valuable data and diagnostics to both the vehicle's onboard systems and the user. It can offer real-time information on battery health, including voltage, current, and temperature readings. This data is essential for the vehicle's control unit to make informed decisions about energy management and for the driver to understand the battery's status. The BMS also contributes to the overall safety of the vehicle by implementing protective measures, such as disconnecting the battery in case of severe issues.
In summary, Battery Management Systems are integral to EVSE, ensuring the safe and efficient operation of electric vehicle batteries. Through continuous monitoring and control of performance, temperature, and state of charge, BMS optimizes battery life, enhances vehicle performance, and contributes to the overall safety of electric vehicles.
Chrysler's Electric Evolution: A New Era of Sustainable Mobility
You may want to see also
Communication Protocols: Define standards for data exchange between EVSE and vehicle, ensuring compatibility and safety
Communication protocols are a critical aspect of Electric Vehicle Supply Equipment (EVSE) as they ensure seamless and safe data exchange between the EVSE and the electric vehicle (EV). These protocols define the rules and formats for transmitting information, such as charging status, power levels, and vehicle data, between the two systems. The primary goal is to establish a standardized method of communication that is widely accepted and understood by both the EVSE and the EV, ensuring compatibility and reliability.
One of the key standards in this domain is the ISO/IEC 15444, which specifies the communication interface and protocol for EV charging systems. This standard defines the physical and logical interfaces, including the data formats and protocols, that enable the EVSE to communicate with the EV during the charging process. By adhering to this standard, manufacturers can ensure that their EVSE systems are compatible with a wide range of EVs on the market.
The protocol also includes security measures to protect the data exchange process. It defines authentication and encryption methods to prevent unauthorized access and ensure the integrity of the transmitted data. This is crucial for maintaining the security of the charging process and safeguarding sensitive information, such as vehicle identification and charging preferences.
Additionally, communication protocols must consider various charging scenarios and modes. For instance, the protocol should accommodate different charging rates, such as slow, fast, and rapid charging, and ensure that the EVSE can adjust the power supply accordingly. It should also support various charging modes, including battery-to-grid (V2G) and vehicle-to-grid (V2G) technologies, which enable bidirectional power flow between the EV and the grid.
To ensure widespread adoption and interoperability, industry organizations and standards bodies play a vital role in developing and maintaining these communication protocols. They collaborate with manufacturers, researchers, and stakeholders to establish and update standards, ensuring that EVSE systems are designed with universal compatibility in mind. This collaborative effort is essential for the seamless integration of EVs into the existing energy infrastructure.
India's Electric Revolution: Are We Ready for the Change?
You may want to see also
Frequently asked questions
Electric Vehicle Supply Equipment, commonly known as EVSE, is the hardware and infrastructure used to supply electrical power to electric vehicles (EVs). It includes charging stations, connectors, and associated controls, enabling EV owners to recharge their vehicles at home, in public areas, or at work.
EVSE operates by connecting an EV to a power source, typically the electrical grid or a dedicated generator. It regulates the voltage and current to ensure safe and efficient charging. The equipment can be installed as a wall-mounted unit, a free-standing kiosk, or integrated into existing power outlets, providing various charging options for EV owners.
There are several types of EVSE, including:
- AC (Alternating Current) Chargers: These are the most common and provide charging through standard household outlets or dedicated wall-mounted units.
- DC (Direct Current) Fast Chargers: These chargers use direct current to rapidly charge EVs, often found in public charging stations and offering much faster charging times.
- Wireless Chargers: These chargers use electromagnetic fields to transfer power to the vehicle without physical connections, providing a convenient and cable-free charging experience.
EVSE offers numerous advantages, such as:
- Convenience: EV owners can charge their vehicles at home, eliminating the need for frequent visits to public charging stations.
- Cost-Effectiveness: Charging at home or using workplace EVSE can be more affordable than public charging, especially during off-peak hours.
- Environmental Impact: By promoting the use of electric vehicles, EVSE contributes to reducing greenhouse gas emissions and improving air quality.
- Safety: Modern EVSE systems include safety features like overcharge protection, temperature monitoring, and fault detection to ensure secure charging.