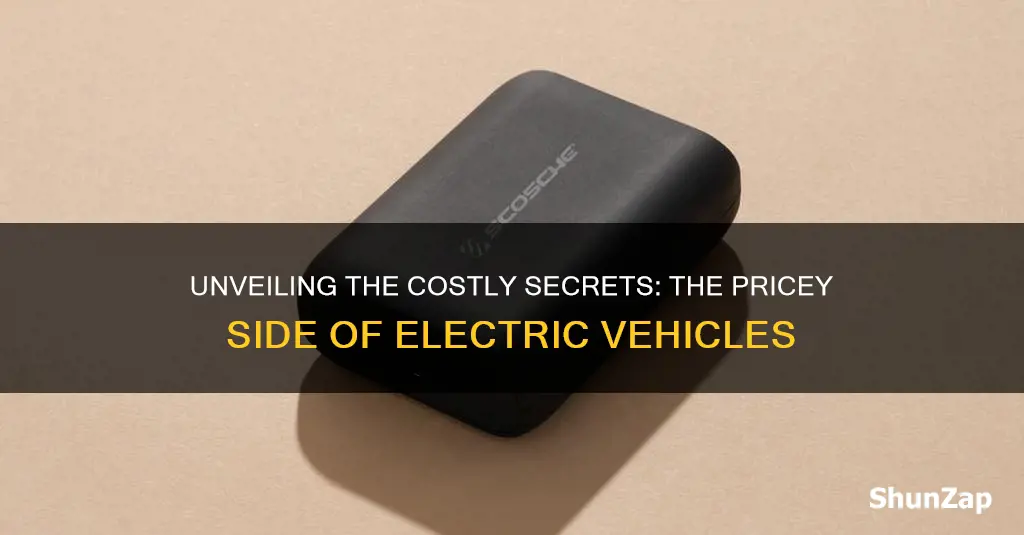
The cost of electric vehicles (EVs) is a multifaceted topic, and while the initial purchase price is a significant factor, it's not the only consideration. The most expensive aspect of an electric vehicle often lies in its long-term ownership and maintenance costs. These include the price of electricity to power the vehicle, which can vary widely depending on regional energy prices and the vehicle's efficiency. Additionally, the depreciation of EVs can be rapid, especially for older models, which may lead to significant financial losses over time. Maintenance and repair costs can also be higher due to the specialized nature of EV technology, and the limited availability of certain parts. Understanding these factors is crucial for anyone considering the financial implications of owning an electric vehicle.
What You'll Learn
- Battery Technology: High-capacity batteries are costly, impacting overall EV price
- Rare Earth Metals: These metals, used in motors, are expensive and environmentally challenging to source
- Charging Infrastructure: Expensive and complex charging systems are a significant cost factor
- Research and Development: Extensive R&D drives up the price of electric vehicles
- Production Costs: Manufacturing EVs is expensive due to specialized equipment and labor
Battery Technology: High-capacity batteries are costly, impacting overall EV price
The battery is often cited as the most expensive component of an electric vehicle (EV), and this is especially true for high-capacity batteries used in premium models. The cost of these batteries is a significant factor in the overall price of EVs, which can be a barrier to entry for many potential buyers.
Battery technology has advanced rapidly in recent years, with manufacturers striving to increase energy density and reduce costs. However, the current state of battery technology still presents challenges. High-capacity batteries, which are essential for longer-range EVs, are expensive to produce. The cost of raw materials, such as lithium, cobalt, and nickel, has been on the rise, and these materials are crucial for battery manufacturing. As a result, the price of batteries has increased, and this cost is often passed on to consumers.
The impact of battery cost on the overall EV price is substantial. A high-capacity battery pack can account for a significant portion of the vehicle's total cost. For example, a premium EV with a large battery pack might have a battery cost that is 2-3 times higher than the cost of the engine and other mechanical components combined. This means that even a small increase in battery price can lead to a substantial increase in the overall vehicle price.
Manufacturers are working on various strategies to reduce battery costs. These include developing more efficient battery designs, improving recycling processes, and exploring alternative materials. For instance, solid-state batteries, which use a solid electrolyte instead of a liquid one, have the potential to offer higher energy density and lower costs. However, these technologies are still in the early stages of development and may take some time to become commercially viable.
In summary, the high cost of high-capacity batteries is a critical factor in the overall price of EVs. While battery technology continues to advance, the current cost structure presents a challenge for the widespread adoption of electric vehicles. As the demand for EVs grows, it is essential to address the cost of batteries to make EVs more affordable and accessible to a broader market.
Electric Vehicle Recharge Costs: A Comprehensive Guide to Charging Expenses
You may want to see also
Rare Earth Metals: These metals, used in motors, are expensive and environmentally challenging to source
The cost of rare earth metals is a significant factor in the expense of electric vehicles (EVs). These metals, including neodymium, praseodymium, and dysprosium, are essential components in the powerful permanent magnets used in electric motors. The demand for these metals has skyrocketed due to their crucial role in the EV industry, and their prices have followed suit. For instance, neodymium prices have increased by over 500% since 2010, making it one of the most expensive commodities in the EV supply chain.
The environmental challenges associated with mining and processing rare earth metals are another critical aspect of their cost. The extraction process often involves destructive mining techniques, such as open-pit mining, which can lead to habitat destruction and soil erosion. Additionally, the chemical processes used to separate and refine these metals can result in water pollution and the release of toxic substances into the environment. These environmental impacts not only contribute to the high cost of rare earth metals but also raise ethical concerns about the sustainability of their extraction.
The limited availability of these metals further exacerbates the cost issue. Rare earth metals are not abundant, and their reserves are concentrated in a few regions, primarily China, the United States, and Australia. This geographical concentration makes the supply vulnerable to geopolitical tensions and economic disruptions. As a result, the supply chain for these metals is often subject to price volatility, which can significantly impact the overall cost of EVs.
To address these challenges, researchers and engineers are exploring alternative materials and technologies. One approach is to develop more efficient motors that require fewer rare earth magnets. Another strategy involves recycling and reusing rare earth metals from end-of-life vehicles, which can help reduce the demand for new mining operations. Additionally, some companies are investing in the development of new mining techniques that are less environmentally damaging, aiming to minimize the ecological footprint of rare earth metal extraction.
In summary, the high cost of rare earth metals in electric vehicles is primarily due to their essential role in powerful motors and the environmental challenges associated with their extraction. The limited availability of these metals and the resulting supply chain vulnerabilities further contribute to the expense. However, ongoing research and development efforts offer potential solutions, including alternative materials and recycling technologies, which could help mitigate the cost and environmental impact of rare earth metals in the EV industry.
Electric Vehicle Owners: Taxed for a Greener Future?
You may want to see also
Charging Infrastructure: Expensive and complex charging systems are a significant cost factor
The charging infrastructure for electric vehicles (EVs) is a critical component that often comes with a hefty price tag, making it one of the most expensive aspects of owning an EV. The complexity and cost of charging systems are significant factors that contribute to the overall expense of EV ownership.
Charging an electric vehicle requires specialized equipment and infrastructure that is different from traditional gasoline refueling. The charging process involves converting electrical energy into a form that can be stored in the vehicle's battery, which demands a robust and often expensive power supply and distribution system. The complexity arises from the need to handle high-voltage electricity and ensure efficient and safe charging, especially for fast-charging stations that can rapidly replenish a vehicle's battery.
The cost of installing and maintaining charging infrastructure is substantial. For home charging, EV owners typically need to install a dedicated charging station, which can range from a few hundred to several thousand dollars, depending on the type of charger and the electrical upgrades required. Fast-charging stations, which are essential for long-distance travel, are even more expensive, with costs reaching into the tens of thousands of dollars for each station. These stations require powerful transformers, specialized cables, and advanced control systems to manage the high-power charging process.
Furthermore, the complexity of charging systems is evident in the technology and engineering involved. Fast-charging stations, for instance, employ advanced cooling systems to dissipate the heat generated during rapid charging, which is crucial for battery longevity. The charging process also requires sophisticated software to manage power distribution, ensure safety, and optimize charging rates, all of which contribute to the overall cost.
In summary, the charging infrastructure is a significant expense for EV owners, with costs stemming from the installation and maintenance of charging stations, the need for specialized equipment, and the complexity of managing high-power electrical systems. As the demand for electric vehicles grows, investing in robust and efficient charging infrastructure becomes essential to support widespread EV adoption and ensure a seamless charging experience for vehicle owners.
Unlocking EV Savings: A Guide to Claiming Your Subsidy
You may want to see also
Research and Development: Extensive R&D drives up the price of electric vehicles
The development of electric vehicles (EVs) is a complex and resource-intensive process, and research and development (R&D) is often cited as one of the most significant factors contributing to their high cost. The extensive R&D required to create these vehicles is a critical aspect of the EV industry, and it plays a pivotal role in determining the overall price.
One of the primary reasons for the high R&D costs is the cutting-edge technology involved in electric powertrains. Electric motors, advanced battery systems, and sophisticated power electronics are just a few examples of the innovative components that need to be designed and engineered. These technologies are at the forefront of automotive innovation, requiring a significant investment in research to understand and optimize their performance, efficiency, and reliability. The development of these systems involves extensive testing, prototyping, and refinement, which are costly endeavors.
Furthermore, the R&D process for EVs is not limited to the powertrain alone. The entire vehicle architecture, including the chassis, body, and electronics, undergoes rigorous development. This comprehensive approach ensures that all aspects of the vehicle are integrated seamlessly and function optimally. Each component must be meticulously designed and tested to meet the specific requirements of an electric vehicle, which often involves unique challenges compared to traditional internal combustion engine (ICE) cars.
Another critical aspect of R&D in EVs is the focus on battery technology. Developing advanced battery systems is a complex task, as it involves creating energy-dense, lightweight, and safe cells. Researchers and engineers work tirelessly to improve battery performance, extend range, and reduce charging times. This includes exploring new materials, optimizing cell chemistry, and enhancing manufacturing processes, all of which contribute to the overall cost of R&D.
Additionally, the regulatory and safety standards for EVs are stringent, requiring extensive R&D to ensure compliance. These vehicles must meet or exceed the same safety and environmental regulations as traditional cars, often with more stringent requirements due to the unique characteristics of electric powertrains. Meeting these standards involves rigorous testing, validation, and certification processes, which add to the overall R&D expenditure.
In summary, the high cost of electric vehicles is significantly influenced by the extensive research and development efforts required to bring these innovative vehicles to market. The cutting-edge technology, comprehensive vehicle architecture, advanced battery systems, and stringent safety standards all contribute to the substantial R&D investment. While these factors drive up the initial price of EVs, they also contribute to the long-term sustainability and performance of these vehicles, making them a desirable and increasingly accessible option for environmentally conscious consumers.
Fund Your Electric Dream: Strategies for EV Funding
You may want to see also
Production Costs: Manufacturing EVs is expensive due to specialized equipment and labor
The production of electric vehicles (EVs) is a complex and costly process, with several factors contributing to the high expenses associated with their manufacturing. One of the most significant aspects is the specialized equipment required to build these vehicles. Electric powertrains, advanced batteries, and sophisticated electronics demand cutting-edge machinery and tools. For instance, the production of lithium-ion batteries, a critical component in EVs, involves intricate processes like cell manufacturing, assembly, and testing, all of which require precision and specialized equipment. This specialized machinery is often custom-built and can be extremely expensive, with costs passed on to the final product.
Labor costs also play a substantial role in the high production expenses of EVs. Manufacturing these vehicles requires a highly skilled workforce with expertise in electronics, software, and mechanical engineering. The assembly process is intricate, involving the precise installation of numerous components, including motors, batteries, and control systems. Skilled workers are needed to ensure the quality and accuracy of these installations, which can be time-consuming and labor-intensive. Moreover, the increasing demand for EVs has led to a surge in labor costs as companies invest in training and hiring specialized personnel to meet the growing production requirements.
The specialized nature of EV manufacturing extends to the materials used. Traditional automotive materials like steel and aluminum are still utilized, but EVs require additional materials such as lithium, cobalt, and rare earth elements for batteries and motors. Sourcing and processing these materials can be expensive, and their availability may be limited, especially for rare earth elements, which are crucial for the permanent magnets used in electric motors. The extraction and refining processes for these materials often involve specialized techniques, further contributing to the overall production costs.
In addition to the initial production costs, the maintenance and repair of specialized equipment also contribute to the financial burden. Electric vehicles have complex systems that require specialized tools and knowledge for maintenance and repairs, which can be costly for both manufacturers and consumers. This aspect becomes even more critical as the automotive industry moves towards more advanced and integrated systems in future EV models.
Despite the challenges, the production costs of EVs are an essential consideration for the industry's growth. As technology advances and production processes become more streamlined, manufacturers aim to reduce these costs while maintaining the high quality and performance expected from electric vehicles. This balance is crucial to making EVs more accessible and competitive in the market, ultimately driving the widespread adoption of sustainable transportation.
South Carolina's EV Tax Exemption: A Green Car Owner's Guide
You may want to see also
Frequently asked questions
The most costly part of an EV is typically the battery pack. These packs are made up of numerous lithium-ion cells and are a significant factor in determining the overall price of the vehicle. The battery's capacity, energy density, and quality directly impact the range, performance, and longevity of the EV, making it a critical and expensive component.
The battery pack in an EV can be several times more expensive than the engine and transmission system in a conventional internal combustion engine (ICE) vehicle. For example, the battery pack in some high-end EVs can cost upwards of $10,000, while a similar-sized ICE vehicle's engine and transmission might only cost a few thousand dollars. However, it's important to note that the total cost of ownership for EVs is often lower due to reduced maintenance and fuel expenses.
Yes, several strategies can help mitigate the high cost of batteries in EVs. These include optimizing the battery chemistry to increase energy density and reduce material costs, implementing advanced manufacturing techniques to improve efficiency and reduce production expenses, and extending the battery's lifespan through smart charging and maintenance practices. Additionally, some EV manufacturers are exploring solid-state battery technology, which could potentially offer higher energy density and lower costs in the future.