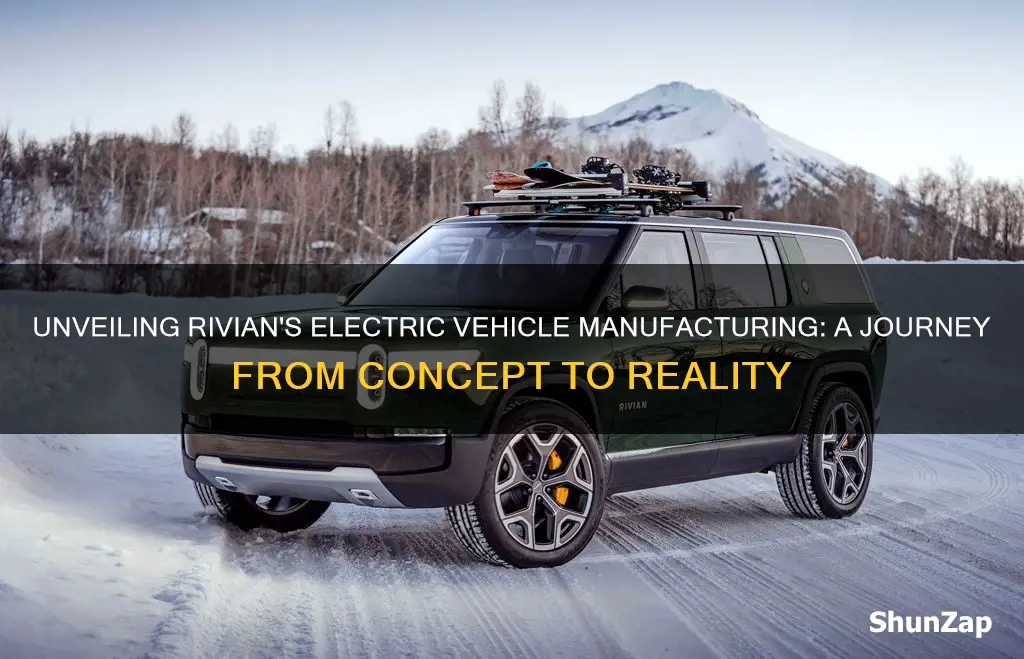
Rivian, an American electric vehicle manufacturer, has made significant strides in the automotive industry with its innovative and sustainable vehicles. The company's headquarters and primary manufacturing facility are located in Normal, Illinois, where it has established a state-of-the-art production plant. Rivian's commitment to local manufacturing has been a key aspect of its business strategy, allowing it to control the quality and efficiency of its production processes. The facility in Normal is designed to produce a range of electric vehicles, including the R1T pickup truck and the R1S SUV, catering to the growing demand for sustainable transportation solutions.
Characteristics | Values |
---|---|
Manufacturing Location | Rivian's electric vehicles are primarily manufactured in Normal, Illinois, USA. |
Assembly Facilities | The company operates two assembly plants: one for its R1T pickup truck and another for the R1S SUV. |
Production Capacity | Rivian aims to produce up to 15,000 vehicles annually at its Illinois plant. |
Supply Chain | The company sources components and materials from various suppliers across North America. |
Employment | The manufacturing facility employs a significant workforce, creating jobs in the local community. |
Expansion Plans | Rivian has announced plans to expand its production capabilities, potentially adding more assembly lines. |
Environmental Impact | The company emphasizes sustainable practices and aims to minimize the environmental footprint of its manufacturing process. |
What You'll Learn
- Manufacturing Facilities: Rivian's electric vehicles are produced at its state-of-the-art factories in Normal, Illinois, and Wilson, South Carolina
- Assembly Process: The assembly line involves robotic automation and human oversight for precision engineering
- Supply Chain: Rivian sources materials and components from various suppliers across the United States and globally
- Battery Production: In-house battery cells are manufactured using advanced lithium-ion technology for optimal performance and sustainability
- Quality Control: Rigorous testing and inspection protocols ensure every vehicle meets Rivian's high standards for quality and safety
Manufacturing Facilities: Rivian's electric vehicles are produced at its state-of-the-art factories in Normal, Illinois, and Wilson, South Carolina
Rivian, the American electric vehicle manufacturer, has established a strong presence in the automotive industry by focusing on sustainable and innovative transportation solutions. The company's commitment to environmental responsibility is evident in its manufacturing facilities, which are designed to produce high-quality electric vehicles while minimizing its environmental footprint.
The manufacturing process begins at Rivian's state-of-the-art factories located in Normal, Illinois, and Wilson, South Carolina. These facilities are strategically chosen to leverage the local resources and skilled workforce, ensuring efficient production and timely delivery of vehicles to customers. The Normal, Illinois, plant serves as the primary production hub, where the R1T pickup truck and R1S SUV are assembled with precision and care. This facility boasts advanced robotics and automation, allowing for a seamless assembly process and ensuring the highest quality standards.
In Wilson, South Carolina, Rivian has established a second manufacturing site, further expanding its production capabilities. This facility plays a crucial role in the company's mission to meet the growing demand for electric vehicles. The Wilson plant is equipped with cutting-edge technology, including advanced assembly lines and robotic systems, enabling the efficient production of Rivian's electric vehicles. The strategic location of these factories also ensures easy access to transportation networks, facilitating the distribution of vehicles across the country.
Rivian's manufacturing facilities are designed with sustainability in mind. The company has implemented various eco-friendly practices, such as using renewable energy sources and minimizing waste. The factories are also designed to be energy-efficient, incorporating advanced insulation and lighting systems to reduce energy consumption. Additionally, Rivian prioritizes the well-being of its employees by providing a safe and comfortable working environment, ensuring that the manufacturing process is not only efficient but also environmentally and socially responsible.
The production process at Rivian's factories involves a meticulous assembly of various components, including the electric drivetrain, battery packs, and advanced driver-assistance systems. Skilled technicians and engineers work together to ensure that each vehicle meets the highest standards of quality and performance. The final assembly process is a testament to Rivian's commitment to delivering exceptional electric vehicles, ready to embark on their journey to provide sustainable transportation solutions.
Unveiling the Electric Vehicle's MPGe Mystery: A Common Number Revealed
You may want to see also
Assembly Process: The assembly line involves robotic automation and human oversight for precision engineering
The assembly of Rivian electric vehicles is a meticulous process, combining advanced robotic automation with human expertise to ensure the highest level of precision engineering. This approach is crucial in the production of these vehicles, which are designed with a focus on performance, sustainability, and cutting-edge technology.
The assembly line begins with the arrival of individual vehicle components, each carefully inspected and verified. Robotic arms, programmed with precision, then take over the task of assembling these parts. These robots are designed to handle a variety of materials, from lightweight composites to heavy-duty steel, ensuring that each component is fitted with utmost accuracy. The robotic arms are equipped with advanced sensors that detect the slightest deviation from the desired specifications, allowing for immediate adjustments to maintain quality.
Human workers play a critical role in this process, overseeing the robotic automation and providing additional expertise. They ensure that the assembly line runs smoothly and efficiently, making real-time decisions to address any issues that may arise. Human engineers are responsible for fine-tuning the robotic systems, optimizing their performance, and ensuring that the vehicles meet the exacting standards set by Rivian. This collaboration between humans and robots is a key feature of Rivian's manufacturing process, allowing for a high level of customization and adaptability.
One of the key advantages of this assembly process is the ability to produce vehicles with a high degree of customization. Each vehicle can be tailored to the customer's specific requirements, whether it's the choice of battery pack, motor configuration, or interior design. The robotic automation ensures that these customizations are accurately implemented, while human oversight guarantees that the final product meets the highest standards of quality and performance.
In addition to precision engineering, this assembly process also emphasizes efficiency and sustainability. The robotic systems are designed to minimize waste and optimize material usage, contributing to Rivian's commitment to environmental sustainability. Furthermore, the assembly line is designed to be flexible, allowing for quick adjustments to meet changing production demands and market trends. This adaptability is a significant advantage in the rapidly evolving electric vehicle market.
Unveiling the Power of Electric Conveyance: A Comprehensive Guide
You may want to see also
Supply Chain: Rivian sources materials and components from various suppliers across the United States and globally
Rivian, an American electric vehicle manufacturer, has built a robust supply chain network to support its production goals. The company's supply chain strategy involves a global approach, sourcing materials and components from various suppliers across the United States and internationally. This approach ensures a steady supply of high-quality raw materials and parts, enabling Rivian to meet its production targets and maintain a competitive edge in the electric vehicle market.
The sourcing process begins with identifying reliable suppliers who can provide the necessary materials and components. Rivian has established partnerships with suppliers in the US, Europe, and Asia, ensuring a diverse and robust supply chain. For instance, the company sources lithium-ion batteries from suppliers in Asia, taking advantage of the region's expertise in battery technology. These batteries are then used in the production of Rivian's electric vehicles, ensuring a consistent supply of power for its vehicles.
In addition to batteries, Rivian sources a range of other components globally. The company procures advanced electronics, such as processors and sensors, from suppliers in the US and Europe, ensuring the vehicles are equipped with cutting-edge technology. The global sourcing strategy also extends to the procurement of raw materials like aluminum, steel, and plastics, which are essential for the vehicle's structure and body. By diversifying its supplier base, Rivian can secure the necessary materials while also reducing the risk of supply chain disruptions.
The supply chain management at Rivian involves a meticulous process of selecting and managing suppliers. The company has a dedicated team responsible for evaluating and approving suppliers, ensuring they meet strict quality and sustainability standards. This includes assessing suppliers' environmental impact, ethical practices, and ability to deliver consistent quality products. By maintaining high standards, Rivian aims to build a sustainable supply chain that supports its long-term goals.
Furthermore, Rivian's supply chain strategy includes a focus on local sourcing and manufacturing. The company has established partnerships with domestic suppliers and manufacturers, particularly in the US, to reduce transportation costs and carbon emissions. This approach also allows for better control over the production process and enables Rivian to adapt quickly to market demands. As a result, the company can efficiently manage its supply chain, ensuring a steady flow of materials and components to its production facilities.
Unveiling the Power of Full Hybrid Electric Vehicles: A Comprehensive Guide
You may want to see also
Battery Production: In-house battery cells are manufactured using advanced lithium-ion technology for optimal performance and sustainability
Rivian, an American electric vehicle manufacturer, has made significant strides in the automotive industry by focusing on sustainable and high-performance electric vehicles. One of the key aspects that sets Rivian apart is its in-house battery production, which is a crucial component of its electric vehicle ecosystem.
The company's battery production process is a testament to its commitment to innovation and sustainability. Rivian has developed an advanced lithium-ion battery technology that powers its electric vehicles. This technology is designed to provide optimal performance and efficiency, ensuring that Rivian's vehicles can go the distance on a single charge. The lithium-ion cells are manufactured in-house, allowing Rivian to maintain control over the quality and performance of its batteries. This in-house production also enables the company to adapt and improve its battery technology over time, keeping up with the evolving demands of the electric vehicle market.
The manufacturing process involves a series of intricate steps. It begins with the selection of high-quality raw materials, ensuring the purity and consistency of lithium, cobalt, and other essential elements. These materials are then carefully processed to create the lithium-ion cells, which are the heart of the battery. Rivian's engineers and scientists employ advanced techniques to assemble and test these cells, ensuring they meet the highest standards of performance and safety. The in-house production facility is designed to be energy-efficient and environmentally friendly, minimizing waste and reducing the carbon footprint associated with battery manufacturing.
By producing its own battery cells, Rivian gains several advantages. Firstly, it allows for customization and optimization of the battery pack to suit the specific requirements of its electric vehicles. This includes tailoring the energy capacity, power output, and charging capabilities to match the vehicle's performance and range goals. Secondly, in-house production ensures a consistent supply of batteries, reducing reliance on external suppliers and providing Rivian with greater control over production timelines and quality.
Furthermore, Rivian's focus on battery production contributes to the overall sustainability of its electric vehicles. The use of advanced lithium-ion technology allows for higher energy density, enabling longer driving ranges and reduced charging times. Additionally, the in-house production process minimizes transportation-related emissions and supports the company's goal of creating a more environmentally friendly transportation ecosystem. With its in-house battery cells, Rivian can offer electric vehicles that not only perform exceptionally but also contribute to a greener future.
Unveiling the Ultimate: World's Fastest Electric Car
You may want to see also
Quality Control: Rigorous testing and inspection protocols ensure every vehicle meets Rivian's high standards for quality and safety
Rivian's commitment to quality and safety is evident in their stringent quality control processes, which are an integral part of their manufacturing operations. Every vehicle that rolls off the assembly line undergoes a series of rigorous tests and inspections to ensure it meets the highest standards set by the company. This meticulous approach is a cornerstone of Rivian's reputation for delivering exceptional electric vehicles.
The quality control journey begins with incoming material inspections, where each component is carefully examined to ensure it adheres to the specified standards. This includes checking for defects, verifying dimensions, and assessing the overall quality of the materials used in the vehicle's construction. Only the finest materials and components make it onto the production line, setting a foundation for superior quality.
Once the vehicle is assembled, a series of dynamic and static tests are conducted. These tests simulate real-world driving conditions, evaluating the vehicle's performance, handling, and overall drivability. Rivian's engineers push the vehicles to their limits, subjecting them to various road conditions and speeds to identify any potential issues. This comprehensive testing ensures that the vehicles are not only efficient but also safe and reliable.
Static inspections involve a thorough examination of the vehicle's interior and exterior, checking for any deviations from the design specifications. This includes assessing the fit and finish of panels, the alignment of windows and doors, and the overall aesthetics of the vehicle. Every detail is scrutinized to ensure a seamless and premium customer experience.
Finally, a comprehensive final inspection is performed before the vehicle is deemed ready for delivery. This inspection covers all critical areas, including the electrical systems, safety features, and overall functionality. Any identified issues are promptly addressed, ensuring that the final product meets Rivian's exacting standards. This multi-layered quality control process is a testament to the company's dedication to delivering a superior product to its customers.
Electric Vehicles: The Cost Revolution
You may want to see also
Frequently asked questions
Rivian's electric vehicles are primarily produced at its manufacturing facility in Normal, Illinois, USA. This state-of-the-art plant covers over 1,300 acres and is designed to be a hub for electric vehicle production, featuring advanced assembly lines and a focus on sustainability.
Yes, Rivian has plans to expand its manufacturing footprint. The company has announced a second production site in Texas, which will serve as a secondary assembly and battery pack manufacturing facility. This expansion aims to increase production capacity and ensure a more efficient supply chain.
Rivian's approach to manufacturing includes several innovative techniques. They utilize a modular assembly system, allowing for flexible production and customization. The company also employs advanced robotics and automation to ensure precision and efficiency in the manufacturing process.
Rivian has not publicly announced any plans to outsource production to other countries. The company aims to maintain control over the entire supply chain, from design to manufacturing, to ensure the highest quality and performance standards for its electric vehicles.