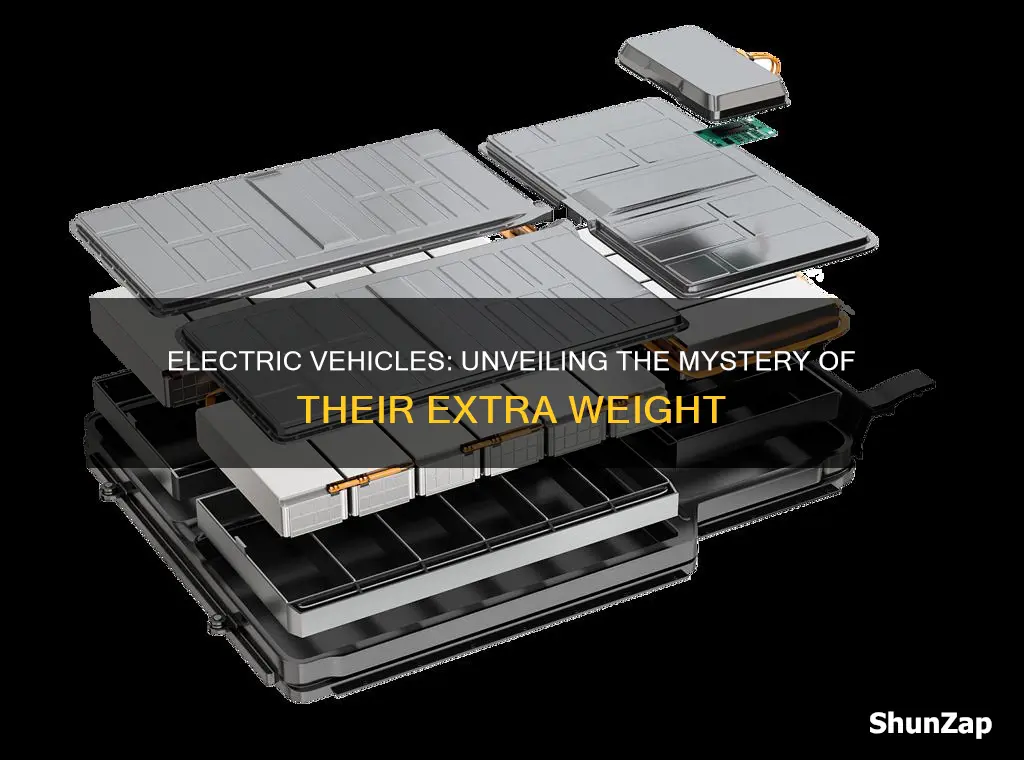
Electric vehicles (EVs) often have a reputation for being heavier than their traditional gasoline counterparts, which can be surprising given their eco-friendly credentials. This phenomenon is primarily due to the advanced technology and materials used in their construction. EVs are equipped with heavy batteries, powerful electric motors, and sophisticated electronic systems, all of which contribute to their increased weight. Despite the initial perception of being heavier, the benefits of electric vehicles, such as improved performance, reduced emissions, and lower maintenance costs, often outweigh the weight difference, making them an attractive choice for environmentally conscious consumers.
What You'll Learn
- Battery Weight: Large battery packs contribute significantly to EV weight
- Safety Features: Advanced safety systems add mass to vehicle design
- Structural Reinforcement: Stronger frames and body panels for crash protection
- Cooling Systems: Efficient cooling mechanisms are heavier than traditional engines
- Advanced Materials: Use of lightweight composites and alloys in EV construction
Battery Weight: Large battery packs contribute significantly to EV weight
The weight of electric vehicles (EVs) is a topic of interest for both manufacturers and consumers, as it directly impacts performance, efficiency, and driving experience. One of the primary factors contributing to the heavier nature of EVs is the large battery packs they carry. These battery packs are essential for storing the energy required to power the vehicle's electric motor, and their weight can be substantial.
EV battery technology has advanced significantly, allowing for higher energy densities and more compact designs. However, the sheer size and number of batteries needed to provide sufficient range still result in a considerable weight increase. Modern EVs often feature large battery packs with thousands of lithium-ion cells, each contributing to the overall mass. The weight of these batteries is a critical consideration in vehicle design, as it affects the vehicle's center of gravity and overall structural integrity.
The large battery packs are typically located at the base of the vehicle, near the wheels, to maintain a low center of gravity, which is crucial for handling and stability. This placement helps counterbalance the weight of the batteries, ensuring the EV remains balanced and responsive during acceleration and cornering. As a result, the weight distribution is optimized, providing a smooth and controlled driving experience.
Despite the challenges, engineers are continually working on innovative solutions to reduce the weight of battery packs. This includes developing more efficient battery chemistries, improving cooling systems, and exploring lightweight materials. For instance, some manufacturers are using advanced composites and alloys to construct battery enclosures, reducing the overall weight while maintaining structural integrity. These efforts aim to strike a balance between battery capacity and vehicle weight, ensuring EVs remain competitive with traditional internal combustion engine vehicles in terms of performance and efficiency.
In summary, the large battery packs in electric vehicles significantly contribute to their weight, but ongoing advancements in battery technology and design are addressing this issue. By optimizing weight distribution and exploring lightweight materials, manufacturers are working towards creating more efficient and lighter EVs, making them more appealing to a wider range of consumers. This continuous innovation will play a vital role in the widespread adoption of electric vehicles.
California's 2030 EV Law: A Green Revolution or a Costly Burden?
You may want to see also
Safety Features: Advanced safety systems add mass to vehicle design
The weight of electric vehicles (EVs) is a topic of interest for both manufacturers and consumers, as it directly impacts performance, efficiency, and overall driving experience. One significant factor contributing to the heavier nature of EVs is the integration of advanced safety systems, which are essential for enhancing road safety and protecting occupants. These safety features often come at a cost of additional mass, which is a trade-off that engineers carefully consider in the design process.
Advanced safety systems in modern vehicles include a range of technologies aimed at preventing accidents, mitigating their impact, and assisting drivers in various driving scenarios. For instance, autonomous emergency braking (AEB) systems use sensors and cameras to detect potential collisions and automatically apply the brakes to avoid or reduce the severity of crashes. These systems often require powerful processors and a network of sensors, which contribute to the overall weight of the vehicle. Similarly, lane-keeping assist, adaptive cruise control, and automatic parking systems also rely on sophisticated electronics and sensors, adding to the vehicle's mass.
Another critical safety feature that adds weight is the implementation of advanced driver-assistance systems (ADAS). These systems encompass a wide range of technologies, such as blind-spot monitoring, rear cross-traffic alert, and automatic high-beam control. Each of these features requires specialized sensors and software, which are integrated into the vehicle's electronics architecture. The complexity and number of components in ADAS contribute significantly to the overall weight, as they need to be strategically placed within the vehicle's structure to ensure optimal performance.
Furthermore, the use of advanced materials in vehicle construction also plays a role in the weight increase. Modern safety systems often utilize lightweight yet robust materials like high-strength steel, carbon fiber composites, and advanced alloys. While these materials offer improved strength and durability, they may also introduce additional mass due to their specialized properties. The careful selection and placement of these materials during the manufacturing process are crucial to achieving the desired balance between safety and weight.
In summary, the integration of advanced safety systems in electric vehicles is essential for enhancing road safety and protecting occupants. However, these safety features contribute to the overall weight of the vehicle due to the presence of powerful processors, sensors, and specialized materials. Engineers must carefully consider the design and placement of these components to ensure optimal performance while managing the impact on vehicle weight. This balance is crucial in the development of electric vehicles, as it directly influences their efficiency, driving experience, and overall appeal to consumers.
EU Subsidies: A Boost for Electric Vehicle Adoption?
You may want to see also
Structural Reinforcement: Stronger frames and body panels for crash protection
The structural integrity of electric vehicles (EVs) is a critical aspect that contributes to their heavier weight, especially when compared to traditional internal combustion engine (ICE) vehicles. One of the primary reasons EVs are heavier is the need to accommodate heavy batteries and the additional safety features required for these vehicles. To address this, manufacturers have focused on structural reinforcement, which involves designing and engineering stronger frames and body panels to enhance crash protection and overall vehicle safety.
In the pursuit of structural reinforcement, EV manufacturers have adopted advanced materials and construction techniques. High-strength steel alloys, for instance, are now commonly used in the chassis and body structure. These materials offer superior strength and durability, enabling the creation of robust frames that can withstand the forces generated during a collision. By utilizing these advanced materials, engineers can design a vehicle's structure to absorb and redistribute crash energy more effectively, reducing the risk of structural failure and improving passenger safety.
Body panels also play a significant role in structural reinforcement. These panels, including the hood, doors, and trunk lid, are engineered to be stiffer and stronger. By employing advanced manufacturing processes such as laser welding and automated assembly, manufacturers can create seamless joints and reinforce critical areas. This ensures that the body structure remains intact during a crash, providing a rigid barrier to protect occupants and maintain the vehicle's overall integrity.
Furthermore, the integration of advanced safety features in EVs contributes to their weight. These features include advanced driver-assistance systems (ADAS), such as autonomous emergency braking, lane-keeping assist, and adaptive cruise control. These systems require sensors, cameras, and processing units, which add to the overall weight of the vehicle. However, the benefits of improved safety and reduced accident severity far outweigh the additional weight, making it a necessary trade-off in the design of modern EVs.
In summary, structural reinforcement is a key factor in the heavier weight of electric vehicles. By employing stronger frames and body panels, manufacturers enhance crash protection and overall vehicle safety. The use of advanced materials and construction techniques, along with the integration of advanced safety features, ensures that EVs meet and often exceed the safety standards required for the automotive industry. This attention to structural integrity is a testament to the commitment of EV manufacturers to provide a safer and more reliable driving experience.
Uncover States' EV Tax Credit Secrets: Your Green Car Guide
You may want to see also
Cooling Systems: Efficient cooling mechanisms are heavier than traditional engines
Electric vehicles (EVs) have gained significant popularity due to their environmental benefits and performance, but one aspect that often raises curiosity is their weight. While EVs are known for their lightweight designs, the cooling systems required to manage the increased heat generation from electric motors and batteries contribute to their overall heavier nature. This is a crucial consideration for engineers and manufacturers, as it directly impacts the vehicle's performance, efficiency, and range.
The cooling systems in electric vehicles are designed to handle the unique challenges posed by electric powertrains. Unlike traditional internal combustion engines, electric motors produce a significant amount of heat during operation, especially when accelerating or under high load conditions. This heat needs to be dissipated efficiently to prevent overheating, which could lead to reduced performance, increased energy consumption, and potential damage to the vehicle's components. As a result, EVs often employ more complex and heavier cooling mechanisms.
One of the primary cooling systems in electric vehicles is the liquid cooling system. This system uses a coolant, typically a mixture of water and ethylene glycol, to absorb heat from the electric motor and transfer it to the radiator. The coolant circulates through the motor, absorbing heat, and then passes through a radiator, where it dissipates the heat into the surrounding air. This process is crucial for maintaining optimal operating temperatures, especially during high-performance driving. The radiator, being a larger and more intricate component, adds to the vehicle's weight.
Additionally, the battery pack in an EV also requires efficient cooling to ensure optimal performance and longevity. Lithium-ion batteries generate heat during charging and discharging, and this heat needs to be managed to prevent thermal runaway and maintain the battery's health. EVs often incorporate liquid or air cooling systems specifically designed for the battery pack. These cooling mechanisms are carefully integrated into the battery design, ensuring efficient heat transfer and distribution. The additional weight of these cooling systems is a trade-off for the improved performance and extended lifespan of the battery.
The heavier cooling systems in electric vehicles are a result of the need for enhanced thermal management. While traditional engines rely on natural convection and smaller cooling systems, electric powertrains demand more robust solutions. The increased weight may seem counterintuitive, especially when aiming for lightweight designs, but it is a necessary compromise to ensure the reliability and efficiency of electric vehicles. Engineers are continually working on optimizing cooling technologies to minimize weight while maintaining the required cooling capacity.
The Birth of the First Fully Electric Car: A Revolutionary Journey
You may want to see also
Advanced Materials: Use of lightweight composites and alloys in EV construction
The quest for improved performance and efficiency in electric vehicles (EVs) has led to a critical focus on reducing weight, as it directly impacts acceleration, range, and overall energy consumption. One of the primary strategies to achieve this is through the innovative use of advanced materials, particularly lightweight composites and alloys. These materials are designed to offer exceptional strength-to-weight ratios, allowing EV manufacturers to create vehicles that are both robust and significantly lighter than their traditional counterparts.
Lightweight composites, such as carbon fiber-reinforced polymers (CFRP), have revolutionized the automotive industry. Carbon fiber, known for its exceptional strength and stiffness, is woven into a polymer matrix to create a composite material that is remarkably light yet incredibly strong. This composite is increasingly used in the construction of EV body panels, chassis, and even battery enclosures. By incorporating carbon fiber, manufacturers can reduce the overall weight of the vehicle while maintaining or even enhancing structural integrity. For instance, the use of CFRP in the chassis can provide better rigidity, leading to improved handling and a more responsive driving experience.
Alloys, on the other hand, play a crucial role in minimizing weight without compromising on safety and performance. Magnesium alloys, for example, are being explored as a potential replacement for traditional steel in certain EV components. Magnesium is the lightest structural metal, and its alloys offer a significant weight reduction compared to steel while maintaining adequate strength. These alloys are particularly useful in applications where weight reduction is essential, such as in the engine bay and underbody of EVs. By utilizing magnesium alloys, manufacturers can achieve a more efficient power-to-weight ratio, resulting in improved acceleration and extended driving range.
The benefits of employing lightweight composites and alloys in EV construction are twofold. Firstly, the reduced weight directly translates to lower energy consumption, as less power is required to accelerate and maintain speed. This not only extends the vehicle's range but also contributes to a more environmentally friendly mode of transportation. Secondly, the use of advanced materials enhances the overall driving experience. Lighter EVs offer quicker acceleration, better handling, and improved responsiveness, making them more enjoyable to drive.
In summary, the integration of lightweight composites and alloys in EV construction is a strategic move towards a more sustainable and efficient future. These advanced materials enable manufacturers to create vehicles that are not only environmentally conscious but also deliver an enhanced driving experience. As the automotive industry continues to evolve, the use of such innovative materials will likely become even more prevalent, shaping the future of electric mobility.
Electric Vehicles: Cost-Effective Transportation for Businesses?
You may want to see also
Frequently asked questions
Electric vehicles often incorporate additional components such as batteries, electric motors, and advanced electronics, which contribute to their overall weight. These components are essential for the vehicle's performance and efficiency but can make the EV heavier.
Yes, batteries play a crucial role in the weight of electric cars. High-capacity lithium-ion batteries are commonly used, and their weight can vary depending on the vehicle's range and specifications. While advancements have been made to reduce battery weight, it remains a significant factor in the overall mass of EVs.
The design choices and architecture of electric vehicles can influence their weight. For instance, some EVs use a unibody construction, which integrates the body and chassis, providing structural rigidity. This design can add weight but also contributes to the vehicle's overall safety and performance. Additionally, the placement of heavy components, such as the battery pack, may impact the vehicle's center of gravity.
Heavier EVs often offer improved handling and a lower center of gravity, which can enhance stability and performance. The additional weight can also contribute to better braking performance and overall safety. However, the trade-off is that heavier vehicles may have slightly reduced efficiency compared to lighter gasoline-powered cars.