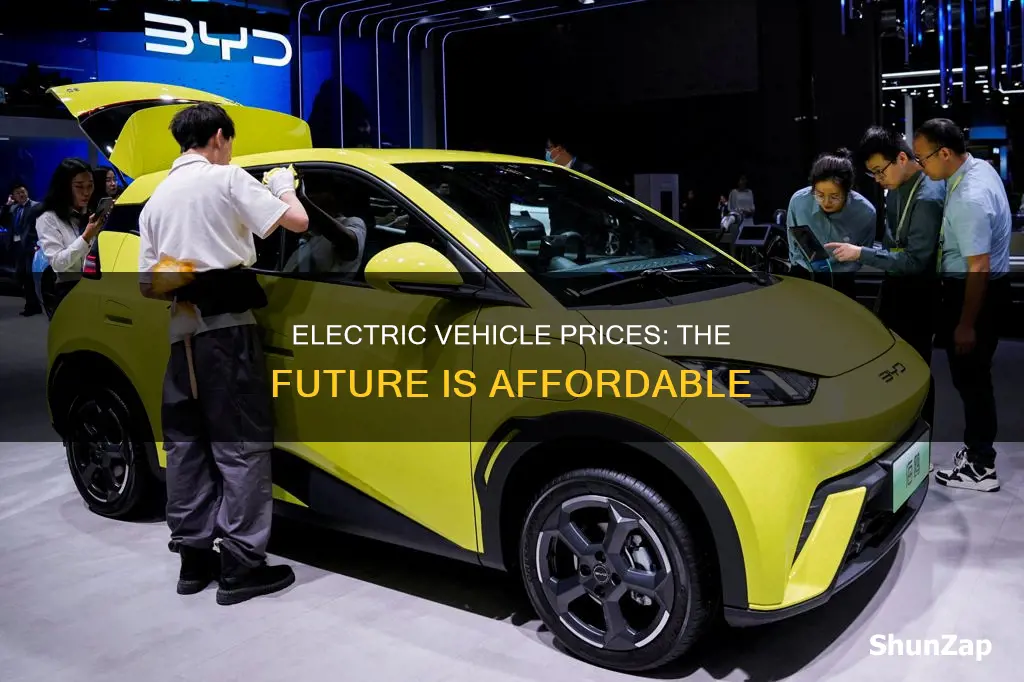
Electric vehicles (EVs) have gained significant popularity in recent years, but one of the main concerns for potential buyers is the cost. The initial perception of EVs being expensive has been a barrier to widespread adoption. However, with advancements in technology and increased market demand, there is a growing question: Are electric vehicle prices coming down? This paragraph aims to explore the factors influencing the cost of EVs and whether we can expect more affordable options in the future.
What You'll Learn
- Battery Technology: Advances in battery chemistry and design are driving down costs
- Manufacturing Efficiency: Optimizing production processes reduces EV manufacturing expenses
- Supply Chain: A stable supply of raw materials can lower prices
- Market Competition: Increased competition among EV manufacturers may lead to price drops
- Government Incentives: Tax credits and subsidies can make EVs more affordable
Battery Technology: Advances in battery chemistry and design are driving down costs
The rapid evolution of battery technology is a key factor in the ongoing trend of decreasing electric vehicle (EV) prices. Advances in battery chemistry and design have led to significant improvements in energy density, charging speed, and overall cost-effectiveness, making EVs more accessible and affordable to a wider range of consumers.
One of the primary drivers of cost reduction is the development of lithium-ion batteries, which have become the standard for electric vehicles. Researchers and engineers have been working on enhancing the cathode and anode materials, as well as the electrolyte solutions, to increase energy storage capacity and reduce manufacturing expenses. For instance, the use of nickel-rich cathodes, such as NMC (Nickel-Manganese-Cobalt) compositions, has shown promise in achieving higher energy densities while maintaining stability. Similarly, the exploration of silicon-based anodes offers the potential for significantly increased energy storage capacity, although challenges related to cycle life and volume expansion need to be addressed.
In addition to material innovations, battery design improvements play a crucial role in cost reduction. Engineers are developing more efficient and compact battery packs by optimizing the arrangement of cells, cooling systems, and packaging. This not only reduces the overall weight and volume of the battery but also minimizes the amount of expensive materials required. For example, the implementation of solid-state electrolytes, which replace the liquid or gel electrolytes in traditional lithium-ion batteries, has the potential to enable higher energy density and faster charging rates while also simplifying the battery manufacturing process.
Furthermore, the scaling up of battery production has led to economies of scale, driving down costs. As the demand for electric vehicles increases, manufacturers can produce batteries in larger quantities, allowing for more efficient processes and reduced per-unit costs. This trend is further accelerated by the establishment of gigafactories, dedicated manufacturing facilities for lithium-ion batteries, which have the capacity to produce millions of battery cells annually, thereby driving down production costs significantly.
The continuous advancements in battery technology are not only making electric vehicles more affordable but also improving their performance and range. As a result, the overall cost of ownership for EVs is becoming more competitive compared to traditional internal combustion engine vehicles, making the transition to electric mobility more attractive to consumers worldwide.
Mastering the EV Service Permit: A Step-by-Step Guide to Application Success
You may want to see also
Manufacturing Efficiency: Optimizing production processes reduces EV manufacturing expenses
The cost of electric vehicles (EVs) has been a significant barrier to their widespread adoption, but there is a growing trend of decreasing prices, which is largely attributed to improvements in manufacturing efficiency. As the demand for EVs increases, manufacturers are focusing on optimizing their production processes, leading to more cost-effective and competitive pricing. This shift in strategy is a response to the market's evolving needs and the increasing competition from traditional automakers entering the EV space.
One key aspect of manufacturing efficiency is the implementation of standardized production lines. By streamlining the assembly process, manufacturers can reduce the time and resources required to produce each vehicle. This involves the use of modular designs, where different components can be easily swapped, allowing for faster assembly and reduced labor costs. For instance, the adoption of robotic arms for repetitive tasks has proven to be highly efficient, ensuring consistent quality and minimizing human error. These automated systems can work tirelessly, improving overall productivity and reducing the time needed for vehicle assembly.
Another strategy to optimize manufacturing is the adoption of vertical integration. This approach enables companies to control various stages of production, from component sourcing to final assembly. By managing the supply chain, manufacturers can reduce costs associated with external suppliers and ensure a steady supply of raw materials. Vertical integration also allows for better quality control, as every step of the production process is closely monitored. This level of control can lead to significant cost savings and improved product reliability, which are essential factors in making EVs more affordable.
Furthermore, the use of advanced technologies and data analytics plays a crucial role in manufacturing efficiency. By implementing industrial Internet of Things (IIoT) devices, manufacturers can collect real-time data on production processes, enabling them to identify bottlenecks and inefficiencies. This data-driven approach allows for quick adjustments and improvements, ensuring that the production line operates at peak performance. Additionally, predictive analytics can forecast equipment failures, reducing downtime and further enhancing manufacturing efficiency.
In summary, the reduction in EV prices is closely tied to the optimization of manufacturing processes. Standardized production lines, vertical integration, and the utilization of advanced technologies all contribute to lower production costs. As manufacturers continue to refine their strategies, the accessibility and affordability of electric vehicles are expected to increase, making them a more viable and attractive option for consumers worldwide. This trend is a positive step towards a more sustainable and environmentally friendly transportation future.
Uncover States' EV Tax Credit Secrets: Your Green Car Guide
You may want to see also
Supply Chain: A stable supply of raw materials can lower prices
The cost of electric vehicles (EVs) has been a topic of much discussion and concern for potential buyers and industry analysts alike. One of the key factors influencing EV prices is the supply chain, particularly the availability and stability of raw materials. As the demand for EVs continues to rise, ensuring a consistent supply of essential materials becomes crucial to driving down costs.
The supply chain for electric vehicles involves a complex network of raw material extraction, processing, manufacturing, and assembly. Key raw materials include lithium, cobalt, nickel, and rare earth elements, which are essential for battery production and other vehicle components. Fluctuations in the supply of these materials can directly impact production costs and, consequently, the final price of EVs.
A stable supply of raw materials can significantly lower EV prices. When there is a consistent and reliable source of these materials, manufacturers can secure long-term supply contracts, ensuring a steady flow of resources. This stability allows for better cost management and planning, as companies can predict and control their expenses more effectively. With a stable supply, manufacturers can also optimize their production processes, reduce waste, and improve overall efficiency, further contributing to cost reduction.
One way to achieve a stable supply chain is by diversifying sourcing. This involves obtaining raw materials from multiple regions and suppliers, reducing the risk of supply disruptions. For example, companies might source lithium from various countries, ensuring that any regional issues or political tensions do not impact the overall supply. By diversifying, manufacturers can also negotiate better prices and terms with suppliers, as they become less dependent on any single source.
Additionally, investing in recycling and second-life battery technologies can help address the issue of raw material scarcity. Recycling used EV batteries can recover valuable materials, reducing the need for new extraction. Second-life applications, where batteries are repurposed for energy storage or other uses, can also extend the lifespan of these materials, ensuring a more sustainable and cost-effective supply chain. These strategies not only contribute to a more stable supply but also promote environmental sustainability and long-term cost reduction.
Powering Electric Vehicles: Exploring Battery Types and Technology
You may want to see also
Market Competition: Increased competition among EV manufacturers may lead to price drops
The electric vehicle (EV) market is experiencing rapid growth, and with it, an interesting dynamic is emerging: increased competition among manufacturers. This competition is a significant factor in the ongoing debate about whether EV prices are coming down, and it's an essential aspect to consider when evaluating the future of the EV industry.
As more companies enter the EV space, the market becomes more saturated, leading to a natural consequence: competition. This competition drives manufacturers to differentiate themselves and gain a competitive edge. One of the primary ways they do this is by offering more affordable options. With a growing number of players, the market becomes more price-sensitive, and companies are forced to lower their prices to attract customers. This is a classic supply and demand scenario, where increased supply (more manufacturers) leads to a more competitive environment, and ultimately, lower prices for consumers.
The strategy of reducing prices to gain market share is a common tactic in any industry, and the EV market is no exception. Companies like Tesla have already demonstrated the power of this approach, quickly gaining a significant market presence by offering high-quality EVs at competitive prices. As a result, traditional automakers are now investing heavily in EV development and are under pressure to match these prices or risk losing customers. This competitive environment is driving innovation and forcing companies to streamline production, reduce costs, and ultimately, lower the prices of their vehicles.
Additionally, the increased competition has led to a focus on efficiency and cost-effectiveness in production processes. Manufacturers are exploring new technologies and supply chain optimizations to reduce the overall cost of EV production. This includes advancements in battery technology, which is a significant contributor to the cost of EVs. As battery technology improves, it becomes more affordable, and this, in turn, can lead to price drops for consumers.
In summary, the growing competition among EV manufacturers is a powerful force driving down prices. As more companies enter the market, they strive to offer competitive pricing, innovative features, and improved efficiency. This competitive landscape is essential for the EV industry's growth, as it encourages manufacturers to continuously innovate and provide consumers with more affordable and accessible electric vehicles. With the market becoming more saturated, the focus on price reduction is likely to intensify, benefiting consumers in the long term.
Electric Vehicles: Sales Tax Exemption Explained
You may want to see also
Government Incentives: Tax credits and subsidies can make EVs more affordable
The rising popularity of electric vehicles (EVs) has sparked a crucial question: Are electric vehicle prices coming down? While the initial cost of EVs has been a significant barrier to widespread adoption, governments worldwide are implementing various incentives to make electric cars more accessible and affordable. One of the most effective strategies is the use of tax credits and subsidies, which directly impact the purchase price of electric vehicles.
Tax credits are a financial reward provided by governments to consumers who purchase EVs. These credits can be substantial, often covering a percentage of the vehicle's cost. For instance, many countries offer tax credits that can range from a few hundred to several thousand dollars, depending on the vehicle's price and the specific incentive program. These credits provide a significant financial boost to buyers, making EVs more competitive against traditional gasoline vehicles. For example, in the United States, the Inflation Reduction Act (IRA) introduced in 2022 provides a tax credit of up to $7,500 for new EVs, which has already led to a surge in EV sales and a more affordable market for consumers.
Subsidies, on the other hand, are financial assistance provided to manufacturers or consumers to encourage the production and sale of electric vehicles. Governments may offer subsidies in the form of grants, low-interest loans, or direct payments to reduce the overall cost of EV production and, consequently, the final price for consumers. These subsidies can be particularly beneficial for small and medium-sized EV manufacturers, helping them to establish a presence in the market and offering more affordable options to buyers. For instance, the European Union's REPowerEU plan includes a €2.5 billion subsidy program to support the production of EVs and related technologies, aiming to make European EVs more competitive and affordable.
The combination of tax credits and subsidies creates a powerful incentive structure. Tax credits directly benefit individual consumers, making EVs more affordable at the point of sale. Subsidies, on the other hand, can drive down production costs, leading to lower prices for consumers in the long term. This two-pronged approach has already shown positive results, with many countries witnessing a significant decline in EV prices, making them more accessible to a broader market segment.
In summary, government incentives, particularly tax credits and subsidies, play a pivotal role in making electric vehicles more affordable. These incentives not only encourage consumer adoption but also support the growth of the EV market by reducing production costs. As a result, the dream of owning an electric car is becoming more attainable, contributing to a greener and more sustainable future.
Uncover the Mystery: Signs Your Car Has Electric Start
You may want to see also
Frequently asked questions
Yes, the cost of electric vehicles has been on a downward trend and is projected to continue doing so. This is primarily due to technological advancements, increased production volumes, and economies of scale. As more manufacturers invest in EV technology and production, the overall cost of batteries and other components is expected to reduce, making EVs more affordable for consumers.
Several factors are driving the price reduction in the EV market. Firstly, battery technology has improved significantly, allowing for higher energy density and lower production costs. Secondly, the growing demand for EVs has led to increased investment and competition among manufacturers, pushing them to offer more competitive pricing. Additionally, government incentives and subsidies for EV buyers further stimulate market growth and price drops.
While the overall trend suggests a decline in prices, the extent of the decrease may vary across different EV models and brands. Entry-level, mass-market EVs are likely to experience more significant price drops due to higher production volumes and lower development costs. However, luxury or high-performance EVs might see more modest price reductions as they often have unique features and higher production costs.
Industry experts predict that electric vehicle prices will continue to fall, potentially reaching price parity with traditional internal combustion engine (ICE) vehicles within the next few years. By 2030, it is estimated that the cost of EVs could be significantly lower, making them more accessible to a broader consumer base. This projection is supported by ongoing research and development efforts aimed at improving battery efficiency and reducing manufacturing expenses.