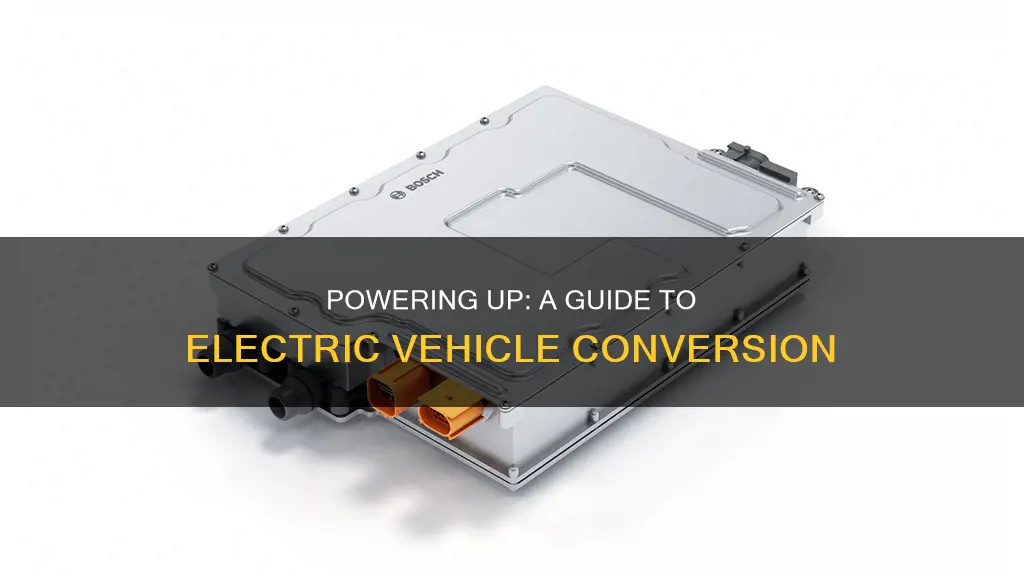
Converting a vehicle to electric power is an exciting and sustainable project that can significantly reduce environmental impact. This process involves replacing the traditional internal combustion engine with an electric motor, along with a sophisticated battery system and associated components. It requires careful planning, technical expertise, and a deep understanding of electrical systems. The conversion process can be complex, involving the installation of a powerful electric motor, advanced battery management systems, and the integration of various sensors and controls. This guide will explore the key steps, considerations, and benefits of making the switch to electric power, offering a comprehensive overview for those interested in this innovative and eco-friendly transformation.
What You'll Learn
- Battery Selection: Choose the right battery for your vehicle's needs and size
- Motor Installation: Install an electric motor compatible with your vehicle's drivetrain
- Charging System: Design and integrate a charging system for efficient power supply
- Power Electronics: Utilize inverters and converters to manage power flow
- Safety Measures: Implement safety protocols to prevent hazards during conversion
Battery Selection: Choose the right battery for your vehicle's needs and size
Battery selection is a critical aspect of converting a vehicle to electric power, as it directly impacts the vehicle's performance, range, and overall driving experience. When choosing the right battery for your electric vehicle (EV), several factors need to be considered to ensure optimal efficiency and longevity.
The first step is to determine the battery capacity required for your specific vehicle. This involves understanding the power demands of your car, including the desired range and the expected load during everyday use. For instance, a smaller city car might require a battery with a lower voltage and amp-hour rating, while a larger SUV or truck will need a more substantial battery pack to accommodate the increased energy requirements. Consider the vehicle's intended use and the range you want to achieve with a single charge. This will help you narrow down the suitable battery options.
Next, you should evaluate the battery chemistry and technology. Common choices for EV batteries include lithium-ion (Li-ion), nickel-metal hydride (NiMH), and lead-acid batteries. Li-ion batteries are the most prevalent in the EV market due to their high energy density, lightweight, and long cycle life. They offer a good balance between power, range, and cost. NiMH batteries are an older technology but can be a more affordable option, while lead-acid batteries are heavy and less efficient but may be suitable for low-performance vehicles. Research the specific battery chemistry and its advantages and disadvantages to make an informed decision.
Another important consideration is the battery's physical dimensions and weight. The battery pack must fit within the vehicle's frame and not compromise the overall structure or performance. Ensure that the chosen battery dimensions align with the available space in your car. Additionally, battery weight is a critical factor, as it affects the vehicle's center of gravity and overall handling. Heavier batteries might require additional structural support to maintain stability.
Lastly, consider the battery's warranty and after-sales support. Reputable battery manufacturers often provide comprehensive warranties that cover defects and performance issues. Review the warranty terms and conditions to understand the coverage and any potential limitations. After-sales support is also essential, as it ensures you have access to technical assistance and potential replacements if needed.
In summary, battery selection for an electric vehicle conversion involves a careful evaluation of capacity, chemistry, physical attributes, and warranty. By considering these factors, you can choose a battery that meets your vehicle's specific requirements, ensuring an efficient, reliable, and enjoyable electric driving experience.
Electric Vehicle Licensing: Navigating the Rules and Requirements
You may want to see also
Motor Installation: Install an electric motor compatible with your vehicle's drivetrain
The installation of an electric motor is a crucial step in converting a vehicle to an electric-powered one. This process requires careful planning and technical expertise to ensure compatibility and optimal performance. Here's a detailed guide on how to install an electric motor compatible with your vehicle's drivetrain:
Motor Selection: Begin by choosing an electric motor that suits your vehicle's requirements. Consider factors such as power output, torque, and size. The motor should match or exceed the performance of the original internal combustion engine. Research and select a motor with a suitable voltage and current rating to match your vehicle's battery system.
Drivetrain Compatibility: Understanding your vehicle's drivetrain is essential. Identify the type of transmission (manual or automatic) and the specific components involved, such as the driveshaft, differential, and axles. Ensure that the electric motor you choose is compatible with these components. Some electric motors are designed to replace specific internal combustion engine configurations, so select one that aligns with your vehicle's drivetrain layout.
Motor Mounting: Install the electric motor in the vehicle's engine bay or designated space, ensuring it is securely mounted. The motor should be positioned to allow for the necessary connections to the drivetrain and battery system. Use appropriate mounting brackets and fasteners to secure the motor in place, ensuring it can withstand the mechanical stresses during operation.
Driveshaft and Transmission Connection: Connect the electric motor to the vehicle's drivetrain. This involves attaching the motor's output shaft to the driveshaft or transmission input shaft. Use high-torque fasteners and ensure proper alignment to transmit power efficiently. If your vehicle has an automatic transmission, you might need to adapt the motor's output to match the transmission's requirements.
Battery and Electrical System Integration: Connect the electric motor to the vehicle's battery system. This includes running high-voltage cables from the battery to the motor and ensuring proper grounding. Install a suitable inverter to convert the direct current (DC) from the battery to alternating current (AC) for the motor. Test the electrical connections thoroughly to identify and rectify any issues.
Testing and Calibration: After the motor installation, conduct thorough testing. Start the vehicle and check for proper motor operation, including speed and torque. Calibrate the motor control system to optimize performance and ensure smooth acceleration and deceleration. Test the vehicle's range and charging capabilities to verify the efficiency of the conversion.
Remember, converting a vehicle to electric power is a complex process, and seeking professional assistance or joining conversion communities can provide valuable guidance and support throughout the installation process.
Understanding DCV: Powering Electric Vehicles with Direct Current
You may want to see also
Charging System: Design and integrate a charging system for efficient power supply
The charging system is a critical component of an electric vehicle (EV) conversion, ensuring efficient power supply and optimal performance. Here's a detailed guide on designing and integrating an efficient charging system:
Charging System Design:
- Charging Port and Connector: Choose a suitable charging port and connector that aligns with industry standards (e.g., CHAdeMO, CCS, or Tesla's proprietary connector). Ensure it's easily accessible and weatherproof to withstand outdoor conditions.
- Charging Rate: Determine the desired charging rate based on your EV's battery capacity and driving needs. Higher charging rates (e.g., DC fast charging) are ideal for quick top-ups during long journeys, while slower rates (AC charging) are suitable for overnight charging at home.
- Power Electronics: Select high-quality power electronics components like inverters and converters to efficiently manage the power flow between the charging source and the battery. These components regulate voltage, frequency, and current to ensure safe and efficient charging.
System Integration:
- Battery Management System (BMS): Integrate a BMS to monitor and control the battery's performance. The BMS tracks battery voltage, temperature, state of charge, and health, ensuring safe and optimized charging. It also prevents overcharging, over-discharging, and overheating.
- Charging Controller: Install a charging controller that acts as the brain of the charging system. It regulates the charging current and voltage, ensuring the battery is charged at the appropriate rate. The controller also protects the battery from damage by monitoring for faults and disconnecting the charging source if necessary.
- Wiring and Connections: Design a robust wiring harness to connect all components safely and efficiently. Use high-quality wires and terminals to handle the charging currents and ensure reliable connections. Consider using a CAN bus system for communication between the charging controller, BMS, and other vehicle systems.
Efficient Power Supply:
- Regenerative Braking: Integrate a regenerative braking system to capture energy during braking and recharge the battery. This not only extends the driving range but also reduces wear on traditional braking components.
- Energy Recovery: Explore opportunities to recover energy from other vehicle systems, such as waste heat from the engine (if applicable) or even the exhaust system. This additional energy can be fed back into the battery, further improving efficiency.
- Smart Charging: Implement smart charging strategies that adapt to the vehicle's usage patterns and external factors like weather. This can involve scheduling charging during off-peak electricity hours or using solar power if available.
Remember, a well-designed charging system is crucial for the overall performance and longevity of your electric vehicle conversion. It's essential to consult with experienced professionals and follow manufacturer guidelines for safe and efficient integration.
Understanding the Electrical Nature of Vehicle Modules
You may want to see also
Power Electronics: Utilize inverters and converters to manage power flow
Power electronics play a crucial role in the conversion of traditional internal combustion engine vehicles to electric powertrains. Inverters and converters are essential components that enable efficient power flow management, ensuring the smooth operation of an electric vehicle (EV). Here's an overview of their significance:
Inverters: In the context of EV conversion, inverters are responsible for converting direct current (DC) from the battery into alternating current (AC) required by the electric motor. This process is vital as it allows the vehicle to utilize the stored energy in the battery effectively. When designing an inverter system, engineers must consider factors such as voltage regulation, frequency control, and power handling capacity. Modern inverters often incorporate advanced features like pulse-width modulation (PWM) to achieve precise control over the motor's speed and torque. By adjusting the inverter's output, the vehicle's performance can be tailored to various driving conditions, ensuring a smooth and responsive driving experience.
Converters: Converters, on the other hand, are used to manage power flow between different parts of the electrical system. In an EV, converters facilitate the transfer of energy between the battery, motor, and other accessories. For instance, a DC-DC converter can step down the high-voltage battery output to supply power to lower-voltage components like the vehicle's electronics and lighting. This ensures that the sensitive electronics receive the appropriate voltage levels while also protecting the battery from potential over-voltage conditions. Converters are designed to handle specific power ranges and are crucial for maintaining the overall efficiency and safety of the EV's electrical architecture.
The design and implementation of these power electronics systems require careful consideration of various factors. Engineers must select components that can handle the expected power levels and ensure compatibility with the vehicle's existing architecture. Additionally, thermal management becomes critical as inverters and converters generate heat during operation. Effective cooling solutions, such as heat sinks and fans, are employed to maintain optimal temperatures and prevent component failure.
In summary, inverters and converters are integral to the successful conversion of vehicles to electric powertrains. They enable efficient power management, ensuring the motor operates optimally while protecting the battery and other vehicle systems. As technology advances, these power electronics components continue to evolve, offering improved performance, efficiency, and reliability for electric vehicles.
The Future of Electric Vehicles: A Timeline
You may want to see also
Safety Measures: Implement safety protocols to prevent hazards during conversion
When converting a vehicle to electric, prioritizing safety is paramount to ensure a successful and hazard-free process. Here are some critical safety measures to consider:
- Electrical System Expertise: Converting a vehicle to electric requires a deep understanding of electrical systems. It is highly recommended to engage the services of experienced professionals who specialize in electric vehicle conversions. These experts possess the knowledge to handle high-voltage systems, ensure proper wiring, and integrate components safely. Attempting the conversion without proper expertise can lead to electrical hazards, including short circuits, fires, or explosions.
- Battery Safety: The electric vehicle's battery is a powerful and potentially hazardous component. It is crucial to source high-quality, compatible batteries from reputable manufacturers. Ensure that the battery installation area is well-ventilated and free from flammable materials. Implement safety measures such as overcharge/over-discharge protection circuits, temperature monitoring, and proper grounding to prevent battery-related accidents. Regularly inspect the battery for any signs of damage or corrosion.
- Wiring and Grounding: Proper wiring is essential to prevent electrical hazards. Use only high-temperature, high-voltage-rated wires and ensure all connections are secure and insulated. Double-check the wiring diagram and follow it meticulously to avoid incorrect connections. Grounding is critical to dissipate electrical faults safely. Ensure all grounding points are properly connected and regularly inspect the grounding system for integrity.
- Fire Prevention: Electric vehicle conversions involve high-voltage systems that can generate heat. Implement fire safety measures by using fire-resistant materials for insulation and wiring. Install a fire suppression system, such as a sprinkler or fire extinguisher, in the conversion area. Regularly inspect the vehicle for any signs of overheating or fire hazards, especially around the battery and wiring harnesses.
- Testing and Validation: Thoroughly test the converted vehicle's electrical system to identify and rectify any potential issues. This includes load testing, insulation resistance testing, and high-voltage insulation resistance testing. Validate the vehicle's performance, range, and charging capabilities under various conditions. Ensure that all safety protocols and regulations are met before the vehicle is operated on public roads.
- Regular Maintenance: Even after the conversion, regular maintenance is crucial to identify and address potential safety issues. Inspect the vehicle's electrical system periodically, checking for loose connections, corrosion, or damage. Keep the battery and wiring clean and well-maintained to prevent short circuits. Stay updated with the latest safety guidelines and best practices in electric vehicle conversion to ensure ongoing safety.
Electric Vehicles: Navigating the Product Lifecycle from Birth to End
You may want to see also
Frequently asked questions
The key components include an electric motor, a high-voltage battery pack, an inverter, a charger, and a power electronics controller. These components work together to replace the internal combustion engine and provide the necessary power and control for the vehicle's operation.
Selecting the appropriate motor depends on various factors such as the vehicle's weight, desired performance, and range requirements. You'll need to consider the motor's power output, torque, and efficiency, ensuring it matches the specifications of your original vehicle or the desired performance level. Consulting with experts or referring to conversion guides can help make an informed decision.
Yes, there are several important aspects to consider. You must ensure that the conversion complies with local regulations and safety standards. This includes proper wiring, grounding, and insulation to prevent electrical hazards. Additionally, you may need to obtain permits and meet emissions requirements. It is advisable to consult with professionals who can guide you through the legal process and ensure your conversion is safe and compliant.