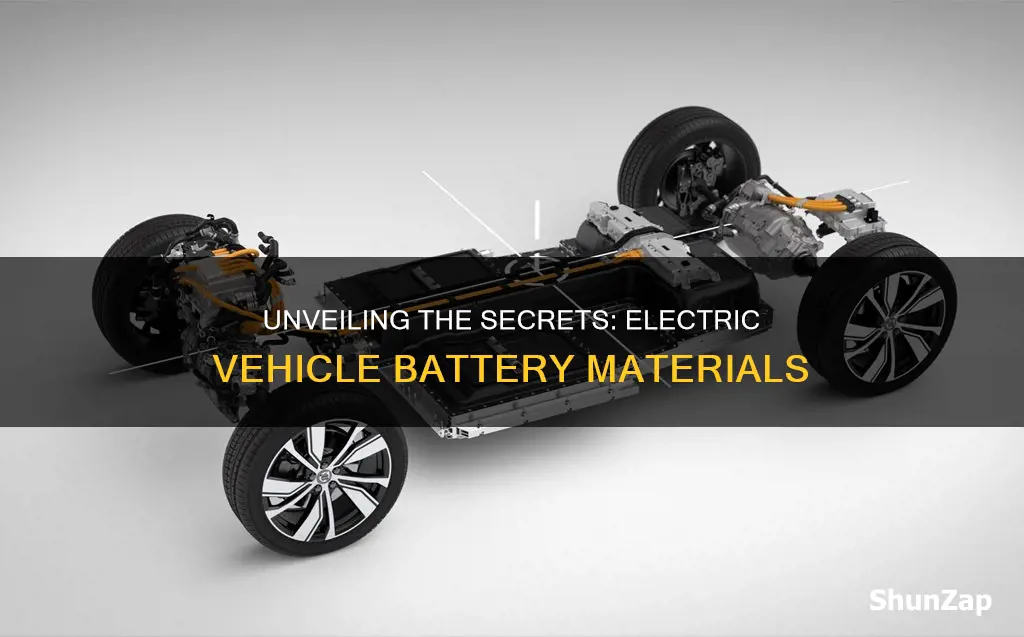
Electric vehicle batteries, the heart of these sustainable vehicles, are complex systems that power the modern world. These batteries are not just any ordinary power source; they are carefully crafted to meet the demands of electric mobility. The composition of these batteries is a fascinating blend of science and engineering, where various materials work in harmony to store and release energy efficiently. Understanding the materials used in electric vehicle batteries is crucial as it directly impacts performance, safety, and sustainability. From the anode to the cathode, each component plays a vital role, and the choice of materials can significantly influence the battery's overall efficiency and longevity.
What You'll Learn
- Battery Chemistry: Key materials include lithium, cobalt, nickel, and manganese
- Electrolytes: These are ionic conductors that facilitate charge transfer
- Anodes: Typically made of graphite, they store lithium ions
- Cathodes: Often contain lithium-metal oxides, like lithium cobalt oxide
- Electrolyte Solvent: Organic solvents like ethylene carbonate are used to dissolve electrolytes
Battery Chemistry: Key materials include lithium, cobalt, nickel, and manganese
The chemistry of electric vehicle (EV) batteries is a complex interplay of various materials, each contributing to the overall performance, energy density, and longevity of the battery. Among the key components, lithium, cobalt, nickel, and manganese stand out as essential elements in the battery's composition.
Lithium, a highly reactive metal, is a cornerstone of EV batteries. It serves as the anode material in many lithium-ion batteries, allowing for the storage of a significant amount of energy in a relatively small space. The unique properties of lithium, including its high electrochemical potential, enable the battery to deliver high power output, making it ideal for powering electric vehicles that require rapid acceleration and responsive performance.
Cobalt, another critical element, is primarily used in the cathode material of lithium-ion batteries. It is known for its high specific heat capacity and excellent thermal stability, which are crucial for maintaining the battery's performance and safety under various operating conditions. Cobalt-based cathodes, such as lithium cobalt oxide (LiCoO2), have been widely adopted in EV batteries due to their high energy density and ability to operate at a wide range of temperatures.
Nickel, often in the form of nickel-manganese-cobalt (NMC) or nickel-cobalt-aluminum (NCA) compounds, is a key component in the cathode material. NMC and NCA cathodes offer improved performance over traditional cobalt-based cathodes, including higher energy density, lower cost, and reduced reliance on cobalt. These materials have gained popularity in EV batteries as manufacturers strive to optimize energy efficiency and reduce the environmental impact of battery production.
Manganese, while not as abundant as lithium, plays a vital role in enhancing the performance and stability of EV batteries. It is commonly used in combination with nickel and cobalt to form spinel-structured cathodes, such as lithium manganese oxide (LiMn2O4). These spinel-structured materials offer advantages like high thermal stability, improved safety, and reduced cost, making them attractive for EV battery applications.
The combination of these key materials—lithium, cobalt, nickel, and manganese—in various forms and compositions is what enables the high energy density, long cycle life, and reliable performance required for electric vehicles. Ongoing research and development efforts focus on optimizing these materials, exploring new chemistries, and improving manufacturing processes to further enhance the efficiency and sustainability of EV batteries.
Emergency Disconnect: Guide to Safely Powering Down Electric and Hybrid Vehicles
You may want to see also
Electrolytes: These are ionic conductors that facilitate charge transfer
Electrolytes are a crucial component of lithium-ion batteries, which are commonly used in electric vehicles (EVs). These ionic conductors play a vital role in facilitating the transfer of charge between the battery's electrodes and the electrolyte itself. The primary function of electrolytes is to provide a medium for the movement of ions, enabling the flow of electricity within the battery.
In the context of EV batteries, the electrolyte is typically a lithium salt dissolved in a solvent, such as ethylene carbonate or diethyl carbonate. When a lithium-ion battery is charged, lithium ions move from the positive electrode (cathode) to the negative electrode (anode) through the electrolyte. This movement of ions is driven by the application of an external voltage, creating an electrochemical reaction. The electrolyte's role is to ensure that these ions can freely move, allowing for efficient charge transfer and subsequent discharge when the vehicle is in use.
The choice of electrolyte is essential for battery performance and safety. Different electrolytes have varying properties, such as ionic conductivity, thermal stability, and compatibility with the battery's electrodes. For instance, lithium-ion batteries often use electrolytes with a high ionic conductivity to enhance charge transfer rates, ensuring faster charging and improved overall efficiency. Additionally, the electrolyte's chemical stability is critical to prevent side reactions and maintain the battery's longevity.
Modern EV batteries often employ electrolytes with added additives to enhance their performance. These additives can improve ionic conductivity, suppress side reactions, and even contribute to the battery's overall energy density. For example, some electrolytes contain fluorinated solvents or ionic liquids, which offer advantages in terms of thermal stability and safety. These advancements in electrolyte technology are driving the development of more efficient and reliable EV batteries.
In summary, electrolytes are the ionic conductors that enable the flow of charge in electric vehicle batteries. Their role is to facilitate the movement of lithium ions between the electrodes, ensuring efficient energy storage and release. With ongoing research and development, the composition and properties of electrolytes are being optimized to enhance battery performance, safety, and sustainability, ultimately contributing to the widespread adoption of electric vehicles.
Unveiling PEVs and BEVs: The Electric Vehicle Revolution
You may want to see also
Anodes: Typically made of graphite, they store lithium ions
The anodes in electric vehicle batteries are a crucial component, responsible for storing and releasing lithium ions during the battery's operation. These anodes are typically constructed from a material known as graphite, which is a form of carbon. Graphite is an ideal choice for this application due to its unique properties. Firstly, it has a high specific surface area, allowing for a large number of lithium ions to be stored within its structure. This is a result of graphite's layered crystalline structure, where each layer can accommodate lithium ions, forming a stable and reversible reaction.
Graphite anodes offer several advantages. They have a relatively low reactivity, which means they do not readily react with other substances, ensuring the stability of the battery. Additionally, graphite can undergo a controlled intercalation reaction with lithium ions, allowing for efficient charge and discharge cycles. This process involves the insertion and removal of lithium ions between the layers of the graphite lattice, enabling the anode to store and release energy as needed.
The manufacturing process of graphite anodes involves several steps. Firstly, high-purity graphite is sourced and processed to create a fine powder. This powder is then mixed with a binder, typically a polymer, to provide structural integrity to the anode. The mixture is then shaped into the desired form, often a thin film or a porous structure, which is crucial for maximizing the surface area and enhancing ion mobility. After shaping, the anode material is coated onto a current collector, usually made of copper, to facilitate electron transfer during the battery operation.
During the charging process, lithium ions from the electrolyte migrate to the anode and intercalate into the graphite layers, causing the anode to swell slightly. This intercalation reaction is reversible, allowing the anode to release the stored lithium ions during discharge. The graphite's layered structure accommodates this expansion and contraction, ensuring the anode's longevity and stability.
In summary, the use of graphite as the anode material in electric vehicle batteries is a strategic choice. Its ability to store and release lithium ions efficiently, combined with its stability and low reactivity, makes it an ideal candidate for powering electric vehicles. The manufacturing process ensures a controlled and precise creation of these anodes, contributing to the overall performance and reliability of electric vehicle batteries.
Electric Vehicle Efficiency: Unlocking the Power of Clean Energy
You may want to see also
Cathodes: Often contain lithium-metal oxides, like lithium cobalt oxide
The cathodes, or positive electrodes, in electric vehicle (EV) batteries are a crucial component, and their composition significantly influences the battery's performance and characteristics. One of the most common materials used in cathodes is lithium-metal oxides, which have revolutionized the field of energy storage. These oxides are carefully engineered to provide high energy density, allowing EVs to travel longer distances on a single charge.
Lithium cobalt oxide (LiCoO2) is a prominent example of a lithium-metal oxide cathode material. It has been widely adopted in the EV industry due to its excellent properties. This material offers a high specific energy, which means it can store a significant amount of energy in a relatively small volume. LiCoO2 also exhibits good thermal stability, ensuring that the battery operates reliably even under various environmental conditions. The structure of lithium cobalt oxide is well-understood, with a layered crystal structure that facilitates the movement of lithium ions during charging and discharging.
The synthesis of lithium cobalt oxide involves a precise process. It is typically produced through a sol-gel method or a co-precipitation technique, followed by heat treatment to achieve the desired crystal structure. The manufacturing process ensures that the material has a controlled particle size and morphology, which is essential for optimizing its electrochemical performance. During the production, the purity of the starting materials is critical to avoid impurities that could hinder the battery's efficiency.
Other lithium-metal oxides, such as lithium nickel manganese cobalt oxide (NMC) and lithium iron phosphate (LFP), are also gaining popularity in EV batteries. NMC offers improved safety characteristics compared to LiCoO2, making it an attractive option for mass-market EVs. LFP, on the other hand, provides high energy density and excellent low-temperature performance, making it suitable for regions with colder climates. These variations in cathode materials allow battery manufacturers to tailor the performance to specific EV applications.
In summary, cathodes in electric vehicle batteries are often composed of lithium-metal oxides, with lithium cobalt oxide being a prominent example. These materials offer high energy density, thermal stability, and controlled electrochemical properties, making them ideal for powering modern EVs. The synthesis and manufacturing processes are carefully optimized to ensure the cathodes meet the demanding requirements of the automotive industry.
The Ultimate Guide to the Most Reliable Electric Vehicles
You may want to see also
Electrolyte Solvent: Organic solvents like ethylene carbonate are used to dissolve electrolytes
The electrolyte solvent plays a crucial role in the composition of electric vehicle batteries, particularly in lithium-ion batteries, which are widely used in the automotive industry. One of the key organic solvents utilized in this context is ethylene carbonate (EC). This solvent is a critical component in the electrolyte mixture, which is responsible for facilitating the movement of ions between the battery's electrodes during charging and discharging processes.
Ethylene carbonate is a highly stable and non-flammable compound, making it an attractive choice for battery manufacturers. Its chemical structure allows it to effectively dissolve and transport electrolytes, ensuring efficient ion conduction. This property is essential for the overall performance and longevity of the battery. When combined with other organic solvents, ethylene carbonate forms a homogeneous solution, creating a stable and reliable electrolyte system.
In the context of electric vehicle batteries, the electrolyte solvent is designed to withstand the demanding conditions of high-performance driving. It must be able to operate efficiently across a wide temperature range, from sub-zero temperatures to high-heat environments. Ethylene carbonate's thermal stability and ability to maintain its solvent properties under these varying conditions make it an ideal choice. This ensures that the battery can deliver consistent performance regardless of the external temperature.
Furthermore, the use of organic solvents like ethylene carbonate offers advantages in terms of safety. Unlike some other solvents, ethylene carbonate is non-flammable, reducing the risk of thermal runaway, a potential hazard in lithium-ion batteries. This safety feature is crucial for the widespread adoption of electric vehicles, as it addresses concerns related to battery safety and reliability.
In summary, the electrolyte solvent, particularly organic solvents such as ethylene carbonate, is a critical component in the construction of electric vehicle batteries. Its role in dissolving electrolytes, ensuring efficient ion movement, and providing thermal stability makes it an essential element in the overall performance and safety of these batteries. The choice of solvent is a strategic decision in battery design, contributing to the advancement of electric vehicle technology.
Ford's Electric Future: Rumors of EV Production Halt
You may want to see also
Frequently asked questions
Electric vehicle batteries, typically lithium-ion batteries, are composed of several key components. The positive electrode (cathode) is often made of a lithium-based material, such as lithium cobalt oxide (LiCoO2), lithium nickel manganese cobalt oxide (LiNiMnCoO2), or lithium iron phosphate (LiFePO4). The negative electrode (anode) can be made of graphite, lithium metal, or silicon-based compounds. Other essential parts include the electrolyte, which facilitates the movement of lithium ions, and the separator, which prevents the electrodes from coming into direct contact.
Yes, several metals and minerals are crucial in the manufacturing process. For instance, lithium, cobalt, nickel, and manganese are essential for the cathode materials mentioned above. Graphite, a form of carbon, is used for the anode. Additionally, metals like aluminum and copper are used in the battery's casing and for electrical connections. The production of these materials involves mining and refining processes, which can have environmental impacts, hence the focus on sustainable sourcing and recycling.
The choice of materials significantly influences the battery's performance, energy density, and longevity. For example, lithium-ion batteries offer high energy density, allowing for compact designs and longer driving ranges. The specific cathode and anode materials determine the battery's voltage, capacity, and stability. Furthermore, the use of recyclable materials and the implementation of efficient recycling processes are vital for sustainability, as they reduce the environmental footprint and ensure a more circular economy for battery production and end-of-life management.