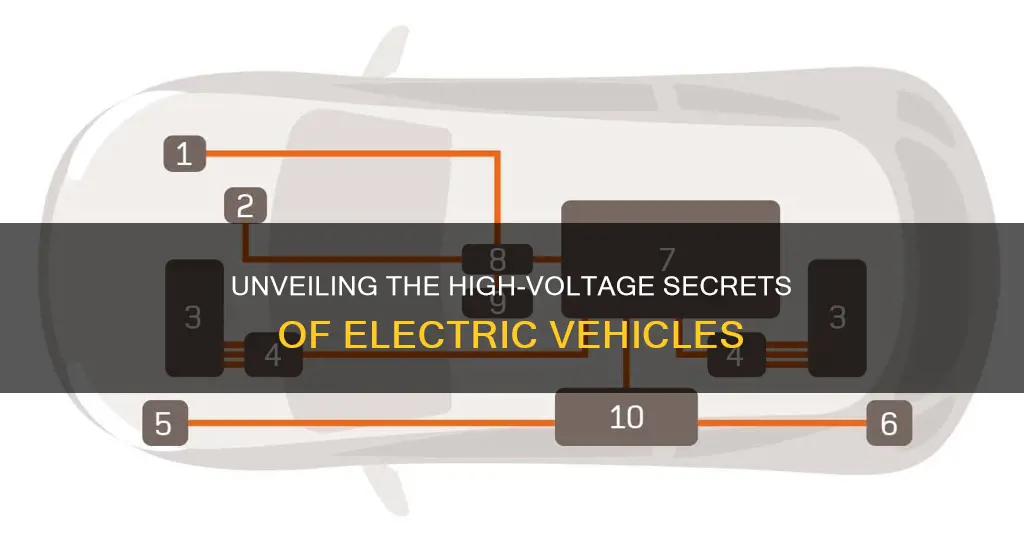
Electric vehicles (EVs) rely on a complex network of high-voltage components to function efficiently and safely. These components are designed to handle the high electrical currents and voltages required to power the vehicle's electric motor and other systems. The high-voltage components typically include the battery pack, inverter, and power electronics. The battery pack stores the electrical energy, and its high-voltage output is regulated and converted by the inverter to provide the appropriate voltage and current to the electric motor. Power electronics, such as DC-DC converters and DC-AC inverters, further manage the electrical flow, ensuring optimal performance and safety. Understanding these high-voltage components is crucial for EV maintenance, troubleshooting, and ensuring the overall reliability of electric vehicle technology.
Characteristics | Values |
---|---|
Battery Pack | Typically 300-800 volts, depending on the vehicle model and manufacturer. |
Power Electronics | High-voltage inverters and converters to manage power flow and convert DC to AC. |
Motor(s) | Often operates at 400-600 volts, especially in high-performance EVs. |
Charger | Can range from 200-400 volts for onboard chargers to higher values for fast charging stations. |
High-Voltage Cables and Connectors | Specially designed to handle the high voltage, ensuring safety and efficiency. |
Power Distribution Unit | Manages the high-voltage power distribution within the vehicle. |
Protection Systems | Advanced safety features like high-voltage fuses, circuit breakers, and grounding systems. |
Onboard Charger | Converts AC charging power to high-voltage DC for battery charging. |
DC-DC Converter | Used in some systems to regulate voltage and power between the battery and other components. |
High-Voltage Grounding | Essential for electrical safety and to prevent electrical shock. |
What You'll Learn
- Battery Pack: High-voltage storage units power the vehicle
- Power Electronics: Converters and inverters manage electrical flow
- Charging Systems: High-voltage interfaces for efficient charging
- Motor Drive: Power electronics control the electric motor
- Power Distribution: High-voltage wiring and connectors throughout the vehicle
Battery Pack: High-voltage storage units power the vehicle
The battery pack is undoubtedly the heart of an electric vehicle (EV), and it is a high-voltage system that powers the entire vehicle. These packs are designed to store and supply the electrical energy required to run the car, and they are a critical component of the EV's performance and efficiency.
In an EV, the battery pack is a collection of multiple individual cells, often arranged in a series-parallel configuration. Each cell is a small, compact unit that stores electrical energy through electrochemical reactions. These cells are carefully arranged to form a high-voltage battery pack, typically with a voltage output ranging from 200 to 400 volts, depending on the vehicle's specifications. The high voltage is necessary to provide the power required for the vehicle's operation, especially during acceleration and when driving at higher speeds.
These packs are designed to be compact and lightweight while offering a high energy density, allowing for efficient storage and distribution of power. The cells are often made of lithium-ion technology, which is known for its ability to store a large amount of energy in a relatively small space. This high-voltage storage system is a key factor in the overall performance and range of electric vehicles, as it directly impacts the vehicle's ability to travel on a single charge.
One of the critical aspects of the battery pack is its ability to manage voltage and current levels. High-voltage systems require sophisticated control and monitoring systems to ensure safe and efficient operation. These systems include voltage regulators, temperature sensors, and advanced battery management software that optimizes performance and extends the battery's lifespan. The management system also helps prevent overcharging, over-discharging, and overheating, which are potential risks associated with high-voltage batteries.
In summary, the battery pack is a high-voltage, high-capacity storage unit that powers the entire electric vehicle. Its design, composition, and management systems are crucial to the vehicle's performance, efficiency, and safety. As technology advances, these battery packs continue to evolve, offering improved energy storage and distribution, making electric vehicles an increasingly viable and sustainable transportation option.
Unraveling the Mystery: Common Causes of Electric Fires in Vehicles
You may want to see also
Power Electronics: Converters and inverters manage electrical flow
Power electronics play a crucial role in electric vehicles (EVs) by managing the high-voltage electrical flow that powers the vehicle's components. This technology enables efficient energy conversion and control, ensuring the vehicle's performance, safety, and longevity. Here's an overview of how converters and inverters function in this context:
In electric vehicles, high-voltage power electronics are essential to handle the large amounts of electrical energy required to propel the car. These systems are designed to convert and manage the flow of electricity, ensuring it is suitable for various vehicle functions. The primary components involved are converters and inverters, which are responsible for adjusting voltage levels and converting direct current (DC) to alternating current (AC) or vice versa.
Converters are power electronic devices that regulate the voltage and current in an electric circuit. In EVs, converters are used to step down the high voltage from the battery pack to a lower level suitable for charging the auxiliary batteries and powering accessories. These converters ensure that the vehicle's electrical system operates efficiently and safely, preventing overvoltage that could damage components. For instance, a DC-DC converter is commonly used to regulate the voltage for the vehicle's onboard charger and other low-voltage systems.
Inverters, on the other hand, are crucial for converting DC power from the vehicle's battery to AC power, which is essential for driving the electric motor. This process is vital for hybrid and fully electric vehicles. The inverter's role is to adjust the voltage and frequency to match the motor's requirements, ensuring smooth and efficient operation. By controlling the flow of electricity, inverters enable precise speed and torque control, allowing the vehicle to accelerate, decelerate, and maintain stability.
The efficiency and performance of these power electronics are critical for EV technology. Modern EVs use sophisticated inverter designs to optimize power distribution and minimize energy losses. This includes advanced switching techniques and cooling systems to handle the high-power density of these components. Additionally, the use of insulated gate bipolar transistors (IGBTs) and other power semiconductors has improved the reliability and efficiency of converters and inverters in electric vehicles.
In summary, power electronics, specifically converters and inverters, are vital for managing the high-voltage electrical flow in electric vehicles. They enable efficient energy conversion, ensuring the vehicle's motor, accessories, and charging systems operate optimally. The continuous development of these power electronics contributes to the advancement of EV technology, making it more efficient, reliable, and environmentally friendly.
Brazil's Electric Vehicle Revolution: Mandates and Future
You may want to see also
Charging Systems: High-voltage interfaces for efficient charging
The charging systems of electric vehicles (EVs) are a critical component that enables efficient power transfer, and they often involve high-voltage interfaces to ensure optimal performance and safety. These interfaces are designed to handle the high electrical potential of EV batteries, typically ranging from 300 to 800 volts, depending on the vehicle model. The primary goal is to facilitate rapid and safe charging while minimizing energy losses.
At the heart of these high-voltage interfaces are specialized connectors and cables that can withstand the extreme conditions of EV charging. These connectors are engineered to provide a robust and reliable connection between the charging station and the vehicle's charging port. One of the key challenges in designing these interfaces is managing the high electrical current and ensuring it flows efficiently without causing damage to the vehicle's electrical system or the charging infrastructure.
To achieve efficient charging, high-voltage interfaces often incorporate advanced technologies such as pulse-width modulation (PWM) and direct current (DC) converters. PWM is a technique used to regulate the voltage and current, ensuring that the charging process is controlled and optimized. DC converters play a crucial role in converting the high-voltage DC power from the charging station to the lower-voltage DC power required by the EV's battery. This conversion process is essential to prevent overcharging and potential damage to the battery.
Additionally, these interfaces are designed with safety mechanisms to protect both the vehicle and the charging system. This includes features like ground fault circuit interrupters (GFCIs) that detect any leakage of electricity to the ground and automatically shut down the charging process to prevent electrical shocks or fires. Another critical safety aspect is the use of insulated connectors and cables to minimize the risk of electrical accidents.
In summary, the charging systems of electric vehicles rely on high-voltage interfaces to efficiently transfer power from charging stations to the vehicle's battery. These interfaces are engineered to handle high electrical potentials, utilize advanced conversion technologies, and incorporate safety features to ensure rapid and secure charging. As EV technology advances, the development of more efficient and reliable high-voltage interfaces will continue to play a vital role in the widespread adoption of electric mobility.
Powering the Future: Essential Resources for Electric Vehicles
You may want to see also
Motor Drive: Power electronics control the electric motor
The electric motor is a critical component of an electric vehicle (EV), and its operation is heavily reliant on power electronics. These power electronics are responsible for controlling the flow of electrical energy to the motor, ensuring efficient and precise performance. In the context of EVs, the term "high voltage" refers to the electrical systems and components that operate at voltages typically above 100 volts, often reaching several hundred volts. This high voltage is necessary to achieve the performance and efficiency required by electric motors.
Power electronics, in the context of motor drive, include devices such as inverters, converters, and switches. Inverters are a key player in this system, as they convert the direct current (DC) from the vehicle's battery into alternating current (AC) that the electric motor needs to operate. This process is crucial because most electric motors are designed to run on AC power. The inverter's role is to control the voltage and frequency of the AC output, ensuring the motor receives the right amount of power at the correct frequency.
The efficiency of power electronics is a significant factor in EV performance. High-efficiency power electronics minimize energy losses during the conversion process, ensuring that more of the electrical energy from the battery is utilized by the motor. This efficiency is vital for extending the vehicle's range and reducing energy consumption. Modern power electronics are designed to operate at high frequencies, allowing for smaller and more compact designs, which is essential for the space-constrained environment of an EV.
Additionally, these power electronics provide control over the motor's speed and torque. By adjusting the voltage and frequency, the inverter can modify the motor's output, enabling the vehicle to accelerate, decelerate, and maintain speed efficiently. This level of control is achieved through sophisticated algorithms and feedback systems, ensuring the motor's performance aligns with the driver's commands. The precision of these controls is a hallmark of advanced EV technology.
In summary, power electronics play a pivotal role in the motor drive system of an electric vehicle. They enable the conversion of DC to AC, control voltage and frequency, and provide the necessary precision for motor operation. The high voltage nature of these systems is essential to meet the performance demands of electric motors, making power electronics a critical component in the overall functionality and efficiency of electric vehicles.
Unlocking EV Potential: Overcoming Range Anxiety and Charging Infrastructure Challenges
You may want to see also
Power Distribution: High-voltage wiring and connectors throughout the vehicle
The power distribution system in an electric vehicle (EV) is a critical component that ensures efficient and safe operation of the high-voltage electrical architecture. This system is responsible for managing the flow of electricity from the battery to various components, such as the electric motor, inverter, and accessories. One of the key aspects of this distribution is the use of high-voltage wiring and connectors, which are designed to handle the increased power levels and provide reliable performance.
High-voltage wiring in EVs is typically made of specialized materials to withstand the harsh operating conditions and electrical demands. These wires are often thicker and more robust compared to conventional automotive wiring, as they need to carry a significant amount of power over relatively long distances. The insulation used is also crucial; it must be able to resist high temperatures, chemical degradation, and mechanical stress to ensure the safety and longevity of the wiring harness. Common materials used for insulation include cross-linked polyethylene (XLPE) and polyimide, which offer excellent electrical properties and thermal stability.
Connectors play a vital role in the high-voltage power distribution system, acting as interfaces between different components and ensuring a secure and reliable electrical connection. These connectors are designed to handle high-voltage and high-current requirements, often featuring robust construction and specialized sealing to prevent electrical leakage and short circuits. The design of these connectors also considers ease of assembly and disassembly, allowing for efficient maintenance and repair. For instance, some connectors use spring-loaded contacts or pressure-fit terminals to ensure a firm connection, even in the presence of vibration and temperature fluctuations.
The high-voltage wiring and connectors are strategically routed throughout the vehicle to minimize the risk of damage and ensure optimal performance. This routing often involves careful planning to avoid sharp bends, sharp edges, and potential sources of mechanical stress, such as suspension components or body panels. The wiring harness may be protected by insulation sleeves, heat shields, or even integrated into the vehicle's structure to provide additional protection.
In summary, the power distribution system in an electric vehicle, particularly the high-voltage wiring and connectors, is a complex yet essential part of the vehicle's electrical architecture. It requires careful design and selection of materials to handle the increased power levels and ensure the safety and reliability of the EV's operation. Proper routing and protection of these components are also critical to maintaining the vehicle's performance and longevity.
Honda's Electric Revolution: Unveiling the Quiet Power
You may want to see also
Frequently asked questions
In an EV, high voltage typically refers to the electrical systems and components that operate at a voltage level above 60 volts. This is a standard threshold used in the automotive industry to differentiate between low and high-voltage systems.
The high-voltage components in an electric vehicle include the battery pack, inverter, DC-DC converter, high-voltage cables, and the power electronics control unit (PECU). These parts are responsible for managing the high-voltage electrical flow and power distribution within the vehicle.
These components handle the high-voltage electricity required to power the EV's electric motor and other electrical systems. The battery pack stores the electrical energy, the inverter converts direct current (DC) to alternating current (AC) for motor use, and the DC-DC converter regulates voltage levels. High-voltage cables and the PECU ensure efficient and safe power distribution.
Absolutely. High-voltage systems in EVs require careful design and implementation to ensure safety. These components are often enclosed in protective casings to prevent accidental contact. Proper insulation and grounding techniques are employed to minimize the risk of electrical shocks. Additionally, advanced safety mechanisms, such as high-voltage shut-off switches and protective circuits, are in place to safeguard against potential hazards.
Low-voltage systems in an EV typically operate at 12 volts, which is the standard voltage for vehicle accessories and lighting. These systems include the alternator, battery charging circuits, and low-voltage sensors. High-voltage components, on the other hand, deal with much higher voltage levels, enabling the EV to achieve efficient propulsion and power management.